- お役立ち記事
- A must-see for design department managers! Techniques for leveraging quality function deployment (QFD) to meet customer needs
A must-see for design department managers! Techniques for leveraging quality function deployment (QFD) to meet customer needs
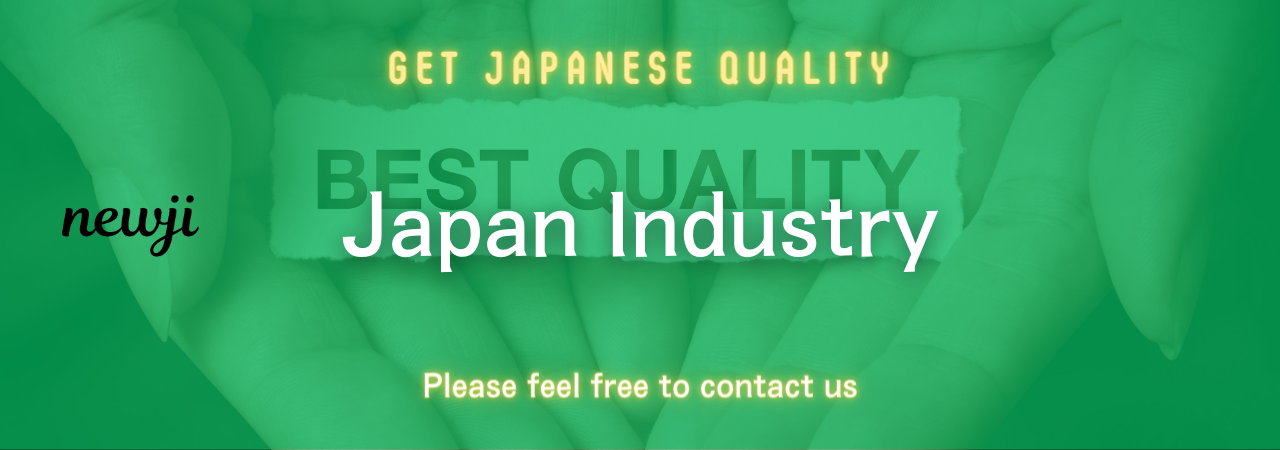
目次
Understanding Quality Function Deployment (QFD)
Quality Function Deployment (QFD) is a structured approach used in engineering and manufacturing that focuses on transforming customer needs into detailed product specifications.
Developed in Japan in the late 1960s, QFD helps organizations systematically identify and prioritize customer needs and then align these with specific engineering characteristics for development.
At its core, QFD aims to optimize product design and engineering processes by ensuring that every decision made during these stages directly corresponds to satisfying a specific customer need.
This not only leads to higher customer satisfaction but also reduces risk associated with product launches, as the end product is more likely to meet the target market’s expectations.
The Basic Structure of QFD
The process of implementing QFD involves creating a series of matrices that gradually break down customer requirements and translate them into actionable product features.
The starting point is usually the “House of Quality,” which is the most well-known tool of QFD.
This matrix serves as a visual representation of the relationship between customer desires and the company’s ability to fulfill them through various product attributes.
The “House of Quality” is divided into several sections.
It includes customer requirements (what the customers want), technical requirements (how you are going to achieve what they want), a relationship matrix (to show the strength of the relationships), and a competitive benchmark (to see how well competitors satisfy these needs).
Understanding and filling out each section allows design managers to address actual customer demands directly in the design phase.
Implementing QFD in Design Departments
Implementing QFD within a design department involves collaboration across different teams, including marketing, engineering, and production.
The primary role of the design manager is to facilitate this collaboration and ensure that customer requirements remain central throughout the design process.
Start by gathering customer data through surveys, focus groups, and market analysis.
This information forms the foundation of the QFD process as it highlights what the target market considers valuable.
The next step is the construction of the “House of Quality,” which will require input from various departments.
Design managers should organize workshops or meetings where team members can discuss and agree upon the critical aspects of the design that must meet customer needs.
Once the “House of Quality” matrix is completed, it is essential to continue with further matrices that break down the technical components into production phases.
This progressive focus ensures that customer requirements guide every step of the product’s development life cycle.
Benefits of Using QFD
The structured nature of QFD brings several benefits to design departments aiming to meet customer needs effectively:
– **Enhanced Communication:** By creating a common platform for dialogue between different departments, QFD ensures that everyone involved in product development understands the customer perspective.
– **Improved Product Quality:** Aligning product features with customer expectations naturally leads to improved quality and higher satisfaction rates.
– **Efficient Use of Resources:** By clarifying the relationships between customer demands and engineering responses, resources can be allocated more efficiently to achieve maximum impact.
– **Reduced Time to Market:** With clear guidelines on what needs to be developed and a priority on fulfilling customer desires, design departments can streamline their processes, reducing the time needed to bring a product to market.
Challenges and Solutions in QFD Implementation
Despite its benefits, implementing QFD can present several challenges.
One of the main difficulties is accurately capturing customer requirements, which requires comprehensive research and strategic data collection methods.
Design departments may overcome this challenge by employing experienced market researchers and leveraging technologies such as data analytics tools.
Another challenge is the need for cross-departmental collaboration.
Differing terminologies and objectives can sometimes hinder productive communication.
To address this, managers should focus on building a culture of collaboration through team-building activities and regular inter-departmental meetings.
There’s also the complexity of the QFD process itself, as creating detailed matrices may seem daunting.
Design managers should consider training sessions for team members to familiarize them with QFD principles and practical applications.
Real-Life Applications of QFD
Many companies across different industries have successfully implemented QFD to optimize their products and gain competitive advantage.
For instance, automobile manufacturers use QFD to ensure their vehicles meet safety standards and customer preferences in functionality and aesthetics.
Similarly, the electronic goods industry applies QFD to keep up with rapidly changing consumer tastes.
By continuously updating their QFD matrices, companies innovate faster and more effectively, ensuring that new product launches align with evolving customer needs.
Conclusion
For design department managers, leveraging Quality Function Deployment presents a powerful opportunity to align product development processes with customer needs effectively.
By understanding the structure of QFD, gathering comprehensive customer data, and promoting collaboration across departments, design managers can drastically enhance the quality and relevance of their products.
Though implementing QFD can present challenges, the benefits far outweigh the difficulties.
As customer satisfaction becomes increasingly critical for business success, tools like QFD offer a systematic way to ensure products consistently exceed customer expectations, helping companies maintain a competitive edge in their respective industries.
資料ダウンロード
QCD調達購買管理クラウド「newji」は、調達購買部門で必要なQCD管理全てを備えた、現場特化型兼クラウド型の今世紀最高の購買管理システムとなります。
ユーザー登録
調達購買業務の効率化だけでなく、システムを導入することで、コスト削減や製品・資材のステータス可視化のほか、属人化していた購買情報の共有化による内部不正防止や統制にも役立ちます。
NEWJI DX
製造業に特化したデジタルトランスフォーメーション(DX)の実現を目指す請負開発型のコンサルティングサービスです。AI、iPaaS、および先端の技術を駆使して、製造プロセスの効率化、業務効率化、チームワーク強化、コスト削減、品質向上を実現します。このサービスは、製造業の課題を深く理解し、それに対する最適なデジタルソリューションを提供することで、企業が持続的な成長とイノベーションを達成できるようサポートします。
オンライン講座
製造業、主に購買・調達部門にお勤めの方々に向けた情報を配信しております。
新任の方やベテランの方、管理職を対象とした幅広いコンテンツをご用意しております。
お問い合わせ
コストダウンが利益に直結する術だと理解していても、なかなか前に進めることができない状況。そんな時は、newjiのコストダウン自動化機能で大きく利益貢献しよう!
(Β版非公開)