- お役立ち記事
- A must-see for engineers in the welding industry! Optimal conditions for MIG welding to minimize slag inclusions
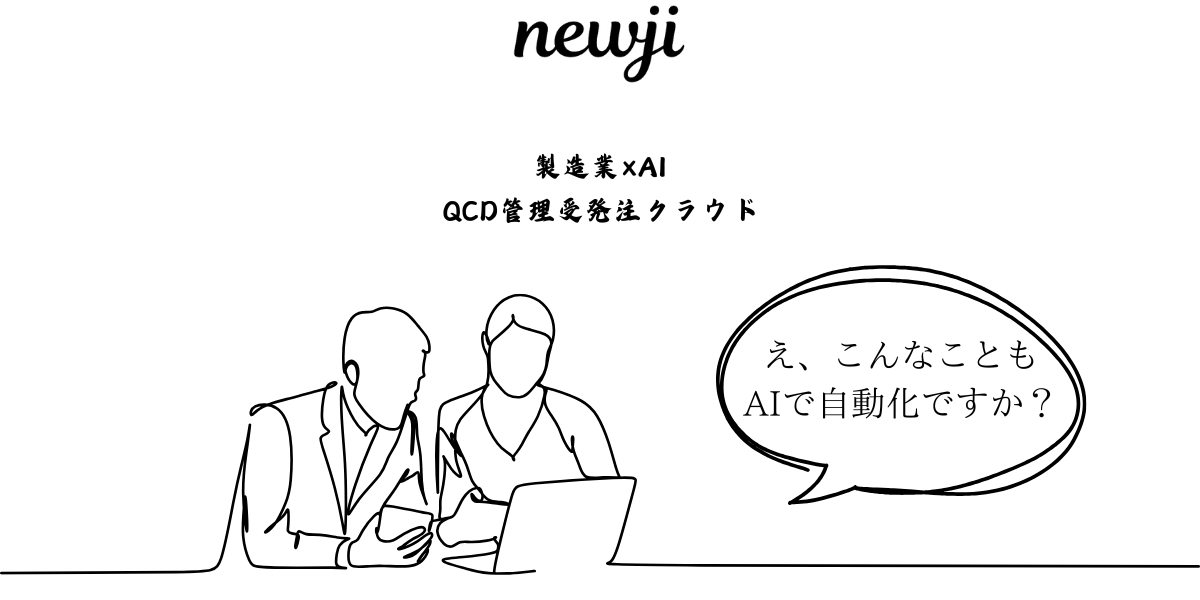
A must-see for engineers in the welding industry! Optimal conditions for MIG welding to minimize slag inclusions
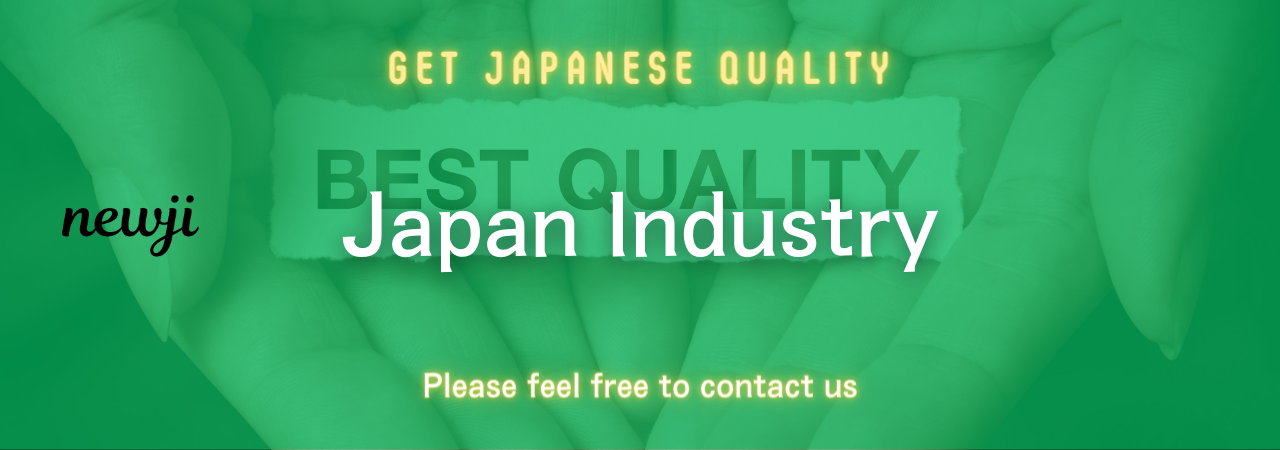
目次
Understanding MIG Welding and Slag Inclusions
MIG welding, or Metal Inert Gas welding, is a popular technique used in the welding industry due to its efficiency and capability to weld a variety of metals.
Understanding how to optimize MIG welding conditions can help reduce defects like slag inclusions, which are solid particles trapped in the weld.
Slag inclusions can significantly affect the weld quality and strength.
This article will explore optimal conditions and practices to minimize slag inclusions when using MIG welding.
Basics of MIG Welding
MIG welding is an arc welding process that uses a consumable electrode and a shielding gas to protect the weld from atmospheric contamination.
The process is commonly used due to its versatility, speed, and ease of use.
In MIG welding, the welding machine provides a constant voltage power supply, which ensures a consistent arc during the welding process.
The electrode wire, fed continuously through a welding gun, melts to join the base materials.
Shielding Gas
The choice of shielding gas is crucial in MIG welding.
It protects the weld from the surrounding atmosphere and affects the weld quality and penetration.
Common gases used in MIG welding include argon, carbon dioxide, or a mix of the two.
Argon provides a stable arc, while carbon dioxide offers deeper penetration.
Combining these gases can optimize weld quality by balancing stability and penetration.
Understanding Slag Inclusions
Slag inclusions occur when solid materials become trapped in the weld metal, which can create weak points and reduce the overall strength of the weld.
These inclusions can result from several factors, including improper cleaning, poor welding techniques, incorrect parameters, and unsuitable materials.
Common Causes of Slag Inclusions
1. **Contaminated Surfaces**: Oils, rust, and other impurities on the metal surface can lead to slag being trapped in the weld.
2. **Incorrect Welding Parameters**: Parameters like voltage, amperage, and travel speed, if not set correctly, can result in poor fusion and encourage slag entrapment.
3. **Improper Electrode Angling**: If the electrode is positioned incorrectly, it can affect the flow of weld and trap slag.
4. **Inadequate Cleaning Between Passes**: Not cleaning between weld passes can leave slag from previous layers, leading to inclusions as new layers are applied.
Optimal Conditions for MIG Welding
To minimize the risk of slag inclusions, achieving optimal welding conditions is essential.
These include proper preparation, parameter settings, and techniques.
Surface Preparation
Ensure that the surfaces to be welded are clean and free from contaminants.
Use a wire brush or grinder to remove rust, oil, paint, and dirt from the metal surface.
Proper preparation significantly reduces the risk of impurities being trapped in the weld.
Setting Correct Parameters
Adjust the welding machine settings to match the materials and thickness of the pieces being welded.
This includes setting the appropriate voltage, amperage, and travel speed.
For instance, thicker materials require higher voltage and amperage settings.
A consistent and appropriate travel speed helps in maintaining a solid weld bead and reducing spatters.
Too fast a speed can lead to lack of fusion and potential slag formation, whereas too slow can cause excessive heat input and result in slag inclusions.
Choosing the Right Electrode and Gas
Selection of the correct electrode size and composition plays a crucial role in achieving a quality weld.
The choice should align with the base materials and project requirements.
Similarly, choosing the right shielding gas mixture optimizes the weld pool fluidity and reduces porosity.
Proper Welding Technique
Technique is key in reducing slag inclusions.
Maintain a stable and consistent arc during welding.
A short arc length can help achieve a smoother bead and avoid trapping of slag in the weld.
Another critical aspect is the angle of the welding gun.
Ensure an angle between 15 to 30 degrees to help keep spatter and slag away from the weld pool.
Cleaning Between Passes
When welding several layers, clean the bead between each pass to remove any slag formed.
Use a chipping hammer or wire brush for manual cleaning.
Removing slag from previous passes ensures it does not get trapped as more layers are built up.
Conclusion
MIG welding is a highly efficient and versatile method used in various industries.
However, to achieve high-quality welds free from defects such as slag inclusions, it’s essential to adhere to optimal welding conditions and best practices.
By ensuring thorough surface preparation, setting correct welding parameters, choosing suitable electrodes and shielding gases, and using proper techniques, engineers and welders can minimize slag inclusions effectively.
Attention to these details ensures stronger, more reliable welds and extends the longevity of the weld structures.
With these guidelines, professionals in the welding industry can master their MIG welding processes and produce optimal results consistently.
資料ダウンロード
QCD調達購買管理クラウド「newji」は、調達購買部門で必要なQCD管理全てを備えた、現場特化型兼クラウド型の今世紀最高の購買管理システムとなります。
ユーザー登録
調達購買業務の効率化だけでなく、システムを導入することで、コスト削減や製品・資材のステータス可視化のほか、属人化していた購買情報の共有化による内部不正防止や統制にも役立ちます。
NEWJI DX
製造業に特化したデジタルトランスフォーメーション(DX)の実現を目指す請負開発型のコンサルティングサービスです。AI、iPaaS、および先端の技術を駆使して、製造プロセスの効率化、業務効率化、チームワーク強化、コスト削減、品質向上を実現します。このサービスは、製造業の課題を深く理解し、それに対する最適なデジタルソリューションを提供することで、企業が持続的な成長とイノベーションを達成できるようサポートします。
オンライン講座
製造業、主に購買・調達部門にお勤めの方々に向けた情報を配信しております。
新任の方やベテランの方、管理職を対象とした幅広いコンテンツをご用意しております。
お問い合わせ
コストダウンが利益に直結する術だと理解していても、なかなか前に進めることができない状況。そんな時は、newjiのコストダウン自動化機能で大きく利益貢献しよう!
(Β版非公開)