- お役立ち記事
- A must-see for equipment engineers in the food processing industry! A thorough guide to maintenance and maintenance of vacuum packaging machines
月間76,176名の
製造業ご担当者様が閲覧しています*
*2025年3月31日現在のGoogle Analyticsのデータより
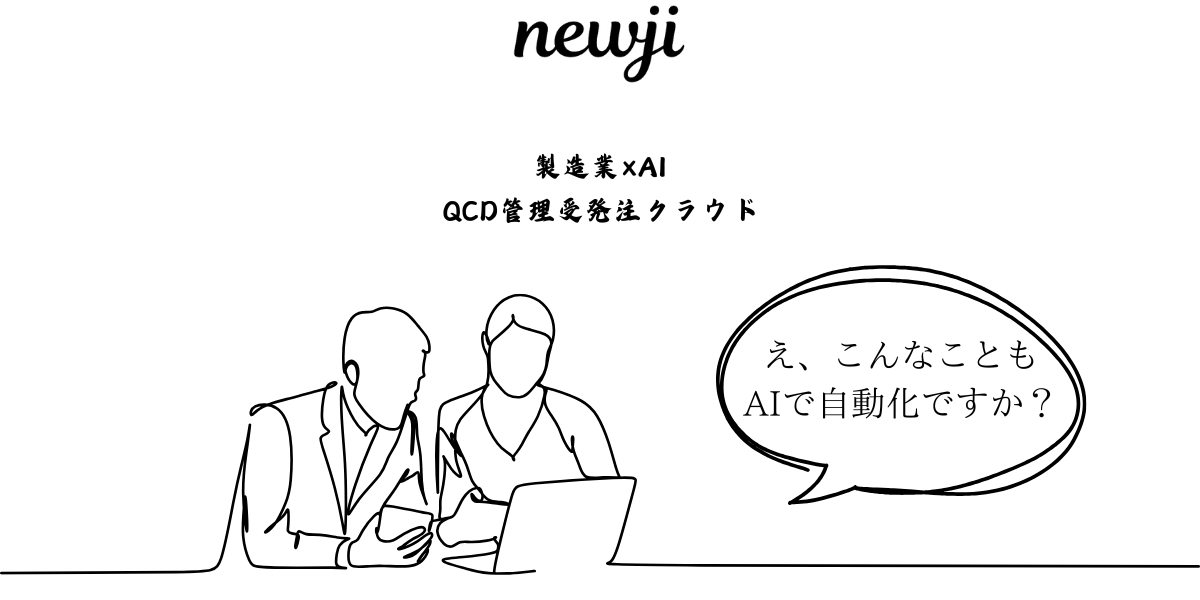
A must-see for equipment engineers in the food processing industry! A thorough guide to maintenance and maintenance of vacuum packaging machines
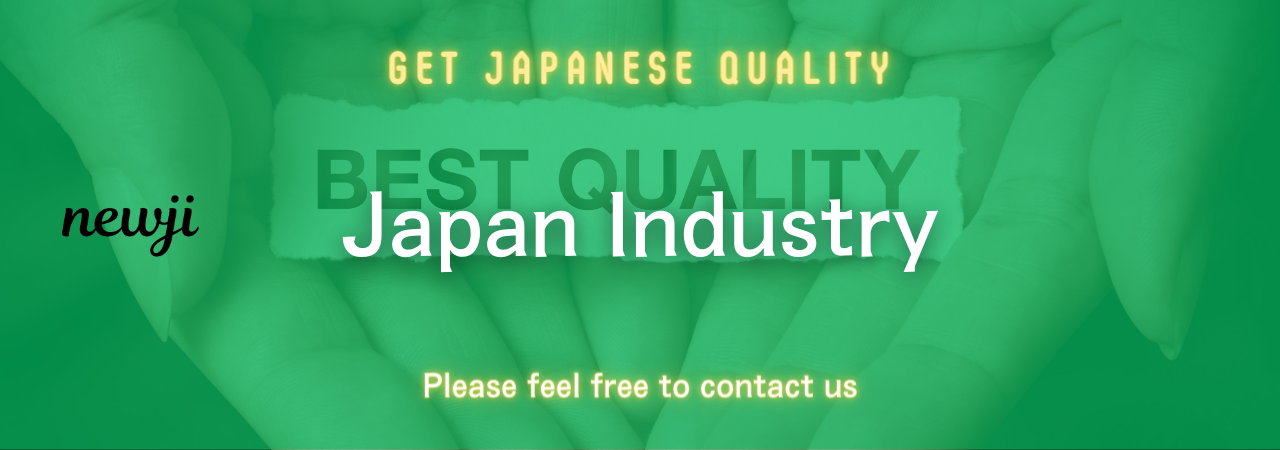
目次
Understanding Vacuum Packaging Machines
Vacuum packaging machines are essential tools in the food processing industry.
They are used to extend the shelf life of food products by removing air from the packaging before sealing it.
This process helps in reducing oxygen levels and inhibiting the growth of bacteria and mold.
These machines are utilized in various settings, from large-scale industrial food processing plants to smaller retail and restaurant establishments.
Understanding how these machines work and their maintenance requirements is crucial for equipment engineers who want to ensure optimal performance.
Components of Vacuum Packaging Machines
To maintain vacuum packaging machines effectively, it’s important to understand their key components.
Typically, these machines consist of a vacuum pump, sealing bar, chamber (for chamber machines), and control panel.
The vacuum pump is the heart of the machine, responsible for removing air from the packaging.
The sealing bar plays a critical role in ensuring the packaging is sealed tightly after the air is removed.
On the control panel, operators can set parameters like vacuum time, sealing time, and vacuum pressure.
Why Regular Maintenance is Important
Regular maintenance of vacuum packaging machines offers a multitude of benefits.
First and foremost, it ensures the machine operates efficiently, which in turn improves productivity and reduces downtime.
Consistent maintenance can also help in identifying potential issues before they become major problems, thus saving on costly repairs.
Additionally, well-maintained machines help in maintaining the quality of vacuum-sealed products, preventing contamination and spoilage.
Creating a Maintenance Schedule
Creating a comprehensive maintenance schedule is crucial for the longevity of vacuum packaging machines.
A good maintenance schedule should include daily, weekly, monthly, and annual tasks.
– **Daily Checks**: Operators should inspect the machine for any visible damage and ensure that the sealing bars are clean. Any debris or leftover packaging material can affect sealing quality.
– **Weekly Tasks**: Perform checks on the vacuum pump oil levels. If the machine uses an oil-lubricated pump, ensuring adequate oil levels is vital. Clean the internal chamber and remove any residues from the sealing area.
– **Monthly Examination**: Inspect the sealing elements and replace them if necessary. Test the machine for any inefficiencies in vacuum pressure and rectify any inconsistencies.
– **Annual Review**: Conduct a comprehensive check on the vacuum pump and consider servicing by a certified technician if required. Assess the control system for updates and recalibrate the machine settings for optimal performance.
Troubleshooting Common Issues
Despite following a rigorous maintenance routine, vacuum packaging machines may occasionally encounter issues. Understanding how to troubleshoot common problems can minimize downtime and maintain operational efficiency.
Problem: Poor Seal Quality
This issue is often caused by debris on the sealing bar or worn-out sealing elements.
Solution: Clean the sealing bar regularly and replace the seal elements if they show signs of wear or damage.
Problem: Incomplete Vacuum
An incomplete vacuum cycle can affect the shelf life of packaged products.
Solution: Check for leaks in the packaging or any obstruction in the vacuum chamber. Ensure the vacuum pump is functioning correctly and the settings are well-calibrated.
Problem: Machine Won’t Start
This can be due to electrical issues or a faulty starting mechanism.
Solution: Inspect the power supply and wiring for any faults. Consult a technician to examine the control panel for any internal issues.
Upgrading and Modernizing Your Machine
As technology advances, so do the capabilities of vacuum packaging machines. Modern machines come with improved energy efficiency, advanced control systems, and greater automation features.
Benefits of Upgrading
– **Energy Efficiency**: Newer models consume less power, leading to cost savings in the long run.
– **Automation**: Enhanced automation reduces the need for manual intervention, increasing throughput and consistency.
– **Improved Quality Control**: Modern machines often include integrated quality control features that monitor and maintain optimal conditions for packaging.
Consultation and Investment
For equipment engineers considering an upgrade, consulting with industry experts to understand the latest advancements can be beneficial. Investment in new technology should be aligned with the company’s operational goals and the specific needs of the production line.
Conclusion
Maintaining vacuum packaging machines is a critical task for equipment engineers in the food processing industry.
Regular maintenance not only extends the lifespan of the machine but also ensures product quality and operational efficiency.
By understanding the components, implementing a robust maintenance schedule, and staying abreast of technological advancements, engineers can significantly contribute to the success of their facilities.
Investing time and resources into proper maintenance and potential upgrades will pay dividends in terms of productivity and product quality.
資料ダウンロード
QCD管理受発注クラウド「newji」は、受発注部門で必要なQCD管理全てを備えた、現場特化型兼クラウド型の今世紀最高の受発注管理システムとなります。
ユーザー登録
受発注業務の効率化だけでなく、システムを導入することで、コスト削減や製品・資材のステータス可視化のほか、属人化していた受発注情報の共有化による内部不正防止や統制にも役立ちます。
NEWJI DX
製造業に特化したデジタルトランスフォーメーション(DX)の実現を目指す請負開発型のコンサルティングサービスです。AI、iPaaS、および先端の技術を駆使して、製造プロセスの効率化、業務効率化、チームワーク強化、コスト削減、品質向上を実現します。このサービスは、製造業の課題を深く理解し、それに対する最適なデジタルソリューションを提供することで、企業が持続的な成長とイノベーションを達成できるようサポートします。
製造業ニュース解説
製造業、主に購買・調達部門にお勤めの方々に向けた情報を配信しております。
新任の方やベテランの方、管理職を対象とした幅広いコンテンツをご用意しております。
お問い合わせ
コストダウンが利益に直結する術だと理解していても、なかなか前に進めることができない状況。そんな時は、newjiのコストダウン自動化機能で大きく利益貢献しよう!
(β版非公開)