- お役立ち記事
- A must-see for equipment engineers in the semiconductor industry! Clean room filter replacement frequency and efficiency techniques
A must-see for equipment engineers in the semiconductor industry! Clean room filter replacement frequency and efficiency techniques
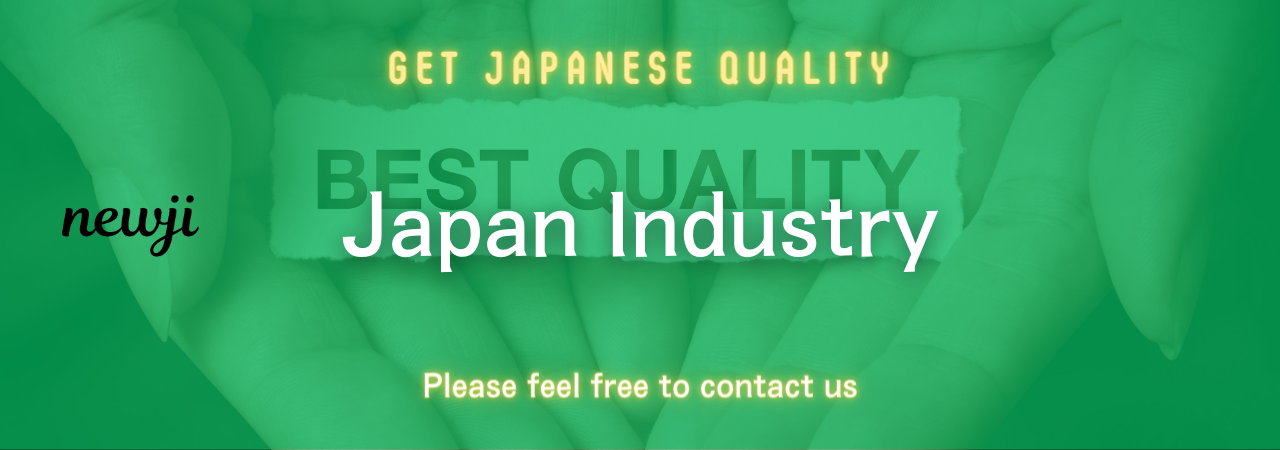
目次
Understanding Clean Room Filters
In the semiconductor industry, maintaining a contaminant-free environment is crucial for the production process.
This is achieved through the use of clean rooms, highly controlled environments designed to limit the presence of particles, pollutants, and other impurities.
A key component of these clean rooms is the filtration system, which plays an essential role in ensuring air quality standards are met.
Clean room filters are specialized devices that capture and remove microscopic particles from the air.
These filters are vital for protecting sensitive semiconductor manufacturing processes from contamination, which can cause defects and yield losses.
The effectiveness of a clean room largely depends on the proper maintenance and timely replacement of these filters.
Importance of Filter Replacement
The frequency of filter replacement in clean rooms is a critical consideration for equipment engineers.
Over time, filters accumulate particles, leading to reduced airflow and increased pressure drop across the filter.
This can compromise the clean room’s ability to maintain the desired air quality, potentially impacting product quality and process yield.
Regular filter replacement is necessary to preserve the integrity and performance of the clean room.
Neglecting to change filters at the appropriate intervals can result in higher operating costs, equipment malfunction, and increased risk of contamination.
Thus, determining the optimal replacement schedule is crucial for maximizing the efficiency and lifespan of clean room filters.
Factors Influencing Replacement Frequency
Various factors influence how often clean room filters should be replaced.
Understanding these factors can help equipment engineers establish an effective maintenance schedule.
Type of Filter
The type of filter used in a clean room significantly affects its replacement frequency.
High-Efficiency Particulate Air (HEPA) filters are commonly used in semiconductor clean rooms due to their ability to capture particles as small as 0.3 microns with an efficiency of 99.97%.
However, other filter types, such as Ultra Low Penetration Air (ULPA) filters, offer even higher efficiency but may require more frequent replacements due to their finer filtration capabilities.
Clean Room Class
Clean rooms are classified based on the level of cleanliness required for specific manufacturing processes.
The International Organization for Standardization (ISO) classifies clean rooms from ISO 1, the cleanest, to ISO 9, the least clean.
Higher-class clean rooms demand more frequent filter replacements as they require stricter air quality standards to be maintained.
Production and Process Load
The production volume and type of processes conducted within the clean room also impact filter replacement frequency.
High production loads increase the number of particles generated inside the clean room, necessitating more regular filter changes.
Processes involving chemicals or open fluid systems may also contribute to the need for more frequent replacements.
Ambient Environmental Conditions
The quality of the external environment where the facility is located can influence the rate of filter degradation.
Facilities in areas with high levels of pollution or dust might require more frequent filter changes compared to those in cleaner environments.
Seasonal changes, such as pollen bursts or increased industrial activity, could also affect filter performance.
Efficient Techniques for Filter Replacement
Implementing efficient techniques for filter replacement can optimize clean room operations and reduce unplanned downtime.
Regular Monitoring and Testing
Establishing a routine monitoring and testing schedule for clean room filters is essential.
This can involve using instruments to measure pressure drop, airflow rates, and particle counts.
Such data allows engineers to evaluate filter performance accurately and determine when replacements are necessary.
Predictive Maintenance
Instead of adhering strictly to a time-based replacement schedule, predictive maintenance relies on real-time data to forecast when a filter is likely to fail.
By analyzing trends and establishing predictive algorithms, facilities can anticipate filter degradation and change filters just before they impact operations.
This approach maximizes filter life and ensures cost-effectiveness.
Inventory Management
Keeping a well-organized inventory of filter types and sizes is critical for timely replacements.
Ensure that all necessary filters are stocked in advance to avoid potential delays during replacement schedules.
An efficient inventory management system can aid in streamlined operations and prevent unexpected down periods.
Training and Automation
Investing in training sessions for maintenance staff can increase their competence in performing efficient filter replacements.
Automation technologies, like robotic systems, can also be employed to handle repetitive replacement tasks, ensuring consistency and precision.
Conclusion
In the semiconductor industry, clean room filters are indispensable for maintaining a contaminant-free environment.
Properly managing the replacement frequency of these filters involves taking into account the type of filter, clean room class, production load, and external conditions.
Implementing effective techniques for filter replacement, such as regular monitoring, predictive maintenance, inventory management, and staff training, can ensure that clean rooms operate efficiently and that production yields remain optimal.
By doing so, equipment engineers can uphold the high standards required in semiconductor manufacturing, ultimately safeguarding product quality and enhancing operational performance.
資料ダウンロード
QCD調達購買管理クラウド「newji」は、調達購買部門で必要なQCD管理全てを備えた、現場特化型兼クラウド型の今世紀最高の購買管理システムとなります。
ユーザー登録
調達購買業務の効率化だけでなく、システムを導入することで、コスト削減や製品・資材のステータス可視化のほか、属人化していた購買情報の共有化による内部不正防止や統制にも役立ちます。
NEWJI DX
製造業に特化したデジタルトランスフォーメーション(DX)の実現を目指す請負開発型のコンサルティングサービスです。AI、iPaaS、および先端の技術を駆使して、製造プロセスの効率化、業務効率化、チームワーク強化、コスト削減、品質向上を実現します。このサービスは、製造業の課題を深く理解し、それに対する最適なデジタルソリューションを提供することで、企業が持続的な成長とイノベーションを達成できるようサポートします。
オンライン講座
製造業、主に購買・調達部門にお勤めの方々に向けた情報を配信しております。
新任の方やベテランの方、管理職を対象とした幅広いコンテンツをご用意しております。
お問い合わせ
コストダウンが利益に直結する術だと理解していても、なかなか前に進めることができない状況。そんな時は、newjiのコストダウン自動化機能で大きく利益貢献しよう!
(Β版非公開)