- お役立ち記事
- A must-see for equipment engineers in the steel industry! Sophistication of surface hardening process using high frequency heating
A must-see for equipment engineers in the steel industry! Sophistication of surface hardening process using high frequency heating
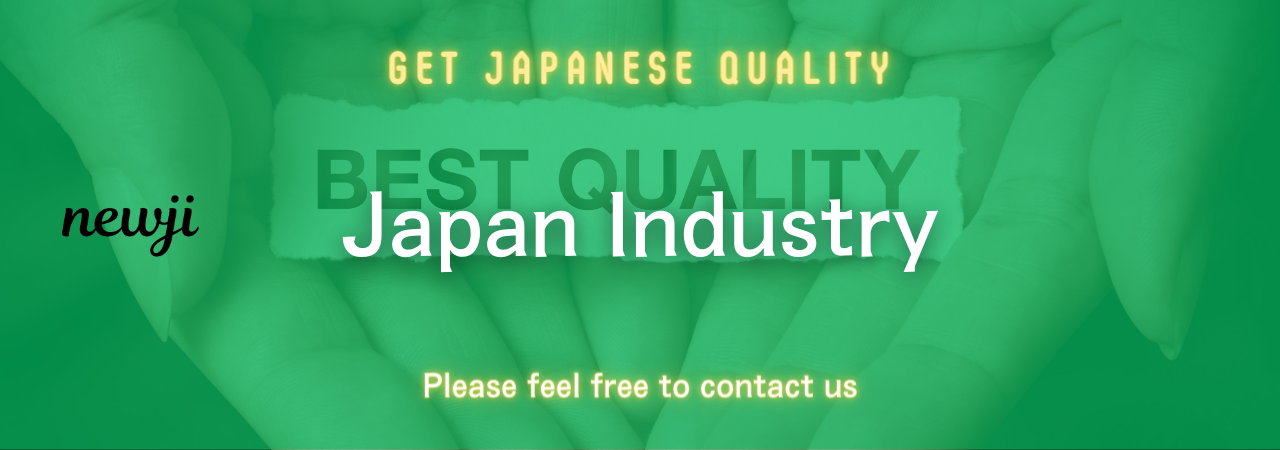
目次
Understanding the Basics of Surface Hardening
Surface hardening is a crucial process in the steel industry, primarily aimed at enhancing the wear resistance and durability of metal surfaces.
It involves altering the surface layer of the steel without affecting the inner core.
This ensures that the metal surface can withstand wear and tear while retaining its toughness and impact resistance.
In the steel industry, various methods are used for surface hardening, such as carburizing, nitriding, and induction hardening.
Each method serves different purposes and has its own set of benefits and applications.
Among these, high-frequency heating, often utilized in induction hardening, stands out for its efficiency and effectiveness in quickly achieving the desired hardness on steel surfaces.
What is High-Frequency Heating?
High-frequency heating is a process where high-frequency alternating current (AC) is passed through a coil, generating an electromagnetic field.
When a steel component is placed within this field, eddy currents are induced on its surface.
These currents rapidly raise the temperature of the surface, leading to its hardening.
The high-frequency heating process is prized for its speed and precision.
It can focus heat on specific areas without affecting the entire part, making it ideal for parts requiring localized hardening.
This process ensures minimal distortion and preserves the mechanical properties of the steel.
Advantages of Using High-Frequency Heating for Surface Hardening
High-frequency heating has several advantages over traditional surface hardening methods.
Speed and Efficiency
One key advantage is the speed at which the process can be completed.
High-frequency heating quickly raises the surface temperature, allowing the process to be completed in a fraction of the time compared to other methods.
This efficiency not only increases productivity but also reduces energy consumption.
Precision and Control
Another significant benefit is the level of precision that can be achieved.
High-frequency heating allows for precise control over the area being hardened, which is particularly useful for complex parts or parts requiring only specific surface areas to be hardened.
This precision helps in achieving consistent results, ensuring each part meets the required specifications.
Minimal Distortion
Traditional surface hardening methods often lead to distortion of the part, requiring additional machining.
However, high-frequency heating minimizes this risk, preserving the original shape and dimensions of the components.
Flexibility in Application
This method is also highly flexible, as it can be applied to a wide range of steel grades and part sizes.
Whether it’s a small gear or a large axle, high-frequency heating can be tailored to meet the specific needs of varying applications.
Applications of High-Frequency Heating in the Steel Industry
High-frequency heating is widely used across the steel industry, spanning a variety of applications.
Automotive Industry
In the automotive industry, components such as gears, crankshafts, and camshafts are often surface-hardened using high-frequency heating.
This enhances their durability and resistance to wear, essential qualities for parts subjected to continuous friction.
Tool Manufacturing
Tool manufacturers also employ this method to harden cutting tools, drill bits, and other high-wear tools.
The surface hardening extends the life of the tools, ensuring they can maintain their cutting edge for longer periods.
Shipbuilding and Aerospace
In more demanding environments like shipbuilding and aerospace, high-frequency heating is used to harden critical components that must endure extreme conditions.
The process ensures these components perform reliably, maintaining safety and efficiency.
The Process of High-Frequency Surface Hardening
The high-frequency surface hardening process is a technically sophisticated procedure involving several key steps.
Preparation
First, the steel component is thoroughly cleaned to remove any contaminants that might interfere with the heating process.
Accurate measurement of the component is undertaken to ensure the correct coil design and fit.
Heating
Next, the steel part is placed within the induction coil.
The high-frequency current passes through the coil, creating an electromagnetic field that induces heat in the surface layer of the part.
Quenching
Once the desired temperature is reached, the part is rapidly quenched.
This cooling can be done with water, oil, or a polymer solution, depending on the steel alloy and the required properties.
The rapid cooling hardens the surface, creating a hard wear-resistant layer.
Tempering
After quenching, the component often undergoes tempering to reduce any brittleness and improve toughness while retaining the surface hardness.
Challenges and Considerations
Despite its numerous benefits, high-frequency heating does pose some challenges.
Equipment Costs
One of the main considerations is the cost of equipment.
Induction heating systems can require significant initial investment.
However, the long-term savings in energy efficiency and reduced processing time can offset these initial costs.
Technical Expertise
The process also requires skilled operators to ensure optimal results.
Proper training and expertise are crucial to managing the intricacies of heating parameters, coil design, and quenching techniques.
Conclusion
High-frequency heating for surface hardening is a transformative process within the steel industry.
Its ability to deliver fast, efficient, and precise hardening makes it a cornerstone technology for equipment engineers looking to innovate and improve operational efficiency.
By understanding and leveraging its advantages, challenges, and applications, engineers can help push boundaries in product durability and performance, setting new standards in the industry.
資料ダウンロード
QCD調達購買管理クラウド「newji」は、調達購買部門で必要なQCD管理全てを備えた、現場特化型兼クラウド型の今世紀最高の購買管理システムとなります。
ユーザー登録
調達購買業務の効率化だけでなく、システムを導入することで、コスト削減や製品・資材のステータス可視化のほか、属人化していた購買情報の共有化による内部不正防止や統制にも役立ちます。
NEWJI DX
製造業に特化したデジタルトランスフォーメーション(DX)の実現を目指す請負開発型のコンサルティングサービスです。AI、iPaaS、および先端の技術を駆使して、製造プロセスの効率化、業務効率化、チームワーク強化、コスト削減、品質向上を実現します。このサービスは、製造業の課題を深く理解し、それに対する最適なデジタルソリューションを提供することで、企業が持続的な成長とイノベーションを達成できるようサポートします。
オンライン講座
製造業、主に購買・調達部門にお勤めの方々に向けた情報を配信しております。
新任の方やベテランの方、管理職を対象とした幅広いコンテンツをご用意しております。
お問い合わせ
コストダウンが利益に直結する術だと理解していても、なかなか前に進めることができない状況。そんな時は、newjiのコストダウン自動化機能で大きく利益貢献しよう!
(Β版非公開)