- お役立ち記事
- A must-see for equipment maintenance department managers! How to maximize the life of your equipment with reliability testing
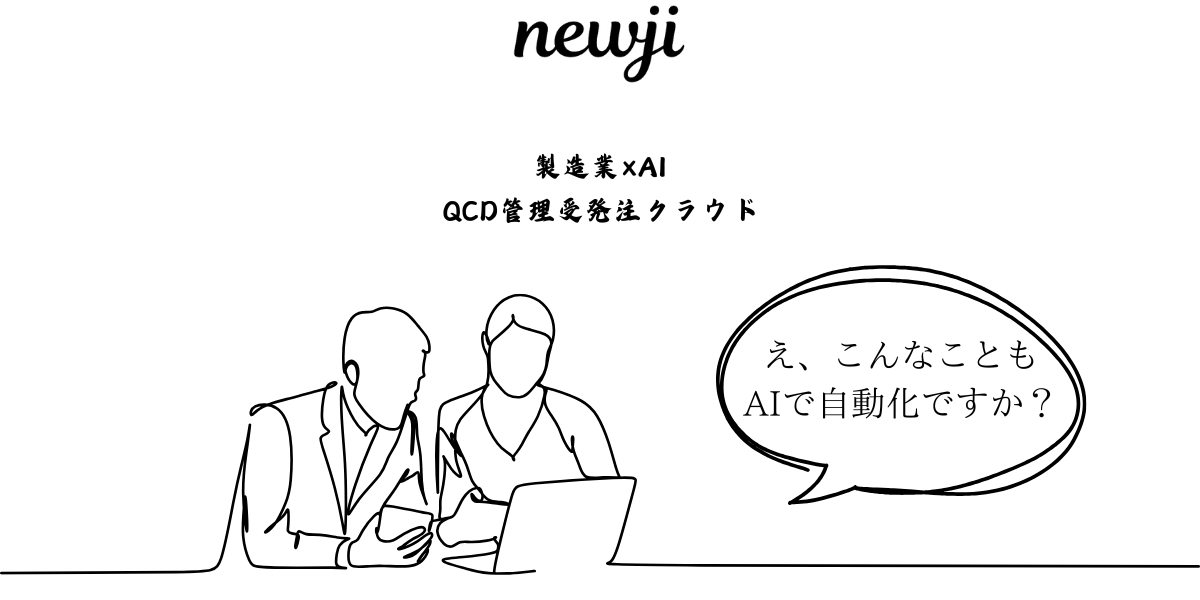
A must-see for equipment maintenance department managers! How to maximize the life of your equipment with reliability testing
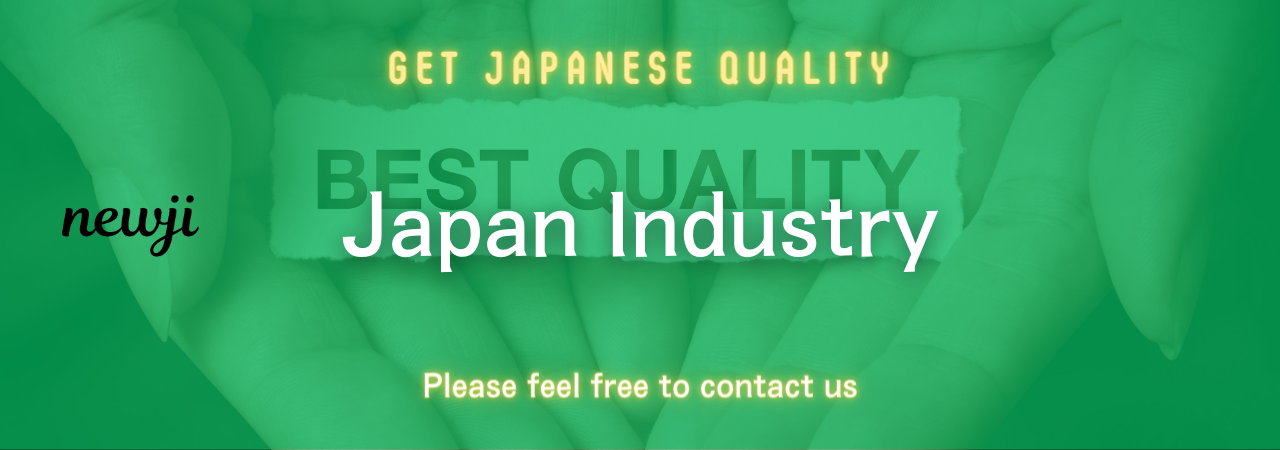
目次
Understanding Reliability Testing
Reliability testing is a critical process that helps equipment maintenance department managers understand the durability and performance of their machinery.
By subjecting equipment to various stress factors and operating conditions, reliability testing provides valuable insights into how long the equipment will last and how it will perform over time.
This process is essential for identifying potential issues before they become significant problems, ensuring that equipment operates smoothly and with minimal downtime.
Reliability testing is not just about identifying problems; it’s about understanding how equipment performs under different scenarios.
This knowledge allows maintenance managers to plan effectively, ensuring that equipment is only used within its designed parameters, which maximizes its lifespan.
The Importance of Reliability Testing in Equipment Maintenance
Reliability testing is pivotal in maintenance management as it contributes significantly to decision-making processes.
By understanding how equipment behaves under various conditions, maintenance managers can schedule repairs and maintenance work proactively rather than reactively.
This proactive approach reduces the risk of unexpected failures, which can be costly and disrupt production schedules.
Moreover, reliability testing provides hard data that can be used to justify investments in new technology or equipment upgrades.
By showing how existing equipment performs under stress, managers can make informed decisions about purchasing new machinery or continuing to invest in maintaining current assets.
Types of Reliability Testing
There are several types of reliability testing that maintenance managers can implement to maximize the life and performance of their equipment.
Each testing type serves a different purpose and provides unique insights into equipment behavior.
Environmental Testing
Environmental testing involves exposing equipment to different environmental conditions such as temperature, humidity, and altitude.
This type of testing helps managers understand how equipment will perform in varying environments, allowing them to make informed decisions about its installation and maintenance.
Life Testing
Life testing is a process that determines the lifespan of a piece of equipment by running it until it fails.
This testing helps managers understand the minimum, median, and maximum life expectancy of the equipment, providing valuable data that can be used to plan maintenance schedules effectively.
Stress Testing
Stress testing subjects equipment to extreme conditions to determine its breaking point or weaknesses.
It helps identify components that are likely to fail under high-stress situations, allowing maintenance teams to replace or reinforce these components before they cause major disruptions.
Implementing a Reliability Testing Program
For equipment maintenance department managers looking to implement a reliability testing program, the following steps can guide you through the process.
Define Requirements
The first step in implementing a reliability testing program is to define the specific requirements and objectives you want to achieve.
This could include reducing downtime, extending equipment life, or improving performance under certain conditions.
Having clear objectives will guide the testing process and ensure that resources are used effectively.
Select the Right Testing Methods
Once you have defined your objectives, the next step is to select the appropriate testing methods.
Consider the types of equipment you are working with and the environments in which they operate.
Choose the testing methods that will provide the most relevant information for your needs.
Conduct Pilot Tests
Before rolling out a full reliability testing program, it is advisable to conduct pilot tests on a small scale.
This allows you to refine your testing procedures, identify any issues, and make necessary adjustments before implementing the program on a larger scale.
Analyze Data and Make Decisions
After conducting reliability tests, analyze the data collected to identify trends and patterns.
Use this information to make informed decisions about maintenance schedules, replacement parts, and possible equipment upgrades.
This data-driven approach ensures that decisions are based on hard evidence rather than assumptions.
Benefits of Reliability Testing
Reliability testing offers numerous benefits for equipment maintenance department managers striving to maximize the lifespan of their equipment.
Reduced Downtime
By identifying potential issues before they lead to failures, reliability testing significantly reduces equipment downtime.
This ensures smoother operations and can lead to significant cost savings by minimizing production interruptions.
Cost Savings
Investing in reliability testing can lead to substantial cost savings over time.
The insights gained from testing allow for more efficient use of resources, reduced maintenance costs, and informed decision-making regarding equipment purchases and upgrades.
Improved Equipment Performance
Reliability testing helps enhance equipment performance by ensuring that machines are operating within optimal conditions.
This not only extends equipment life but also improves overall productivity and efficiency within the manufacturing process.
Conclusion
Reliability testing stands as an indispensable tool for equipment maintenance department managers looking to maximize the life and performance of their machinery.
By understanding equipment behavior under various conditions, maintenance managers can make informed decisions that lead to reduced downtime, cost savings, and improved performance.
Implementing a solid reliability testing program requires careful planning and analysis, but the benefits far outweigh the efforts involved.
For managers striving to enhance their equipment’s longevity and efficiency, reliability testing is not just an option—it’s a necessity.
資料ダウンロード
QCD調達購買管理クラウド「newji」は、調達購買部門で必要なQCD管理全てを備えた、現場特化型兼クラウド型の今世紀最高の購買管理システムとなります。
ユーザー登録
調達購買業務の効率化だけでなく、システムを導入することで、コスト削減や製品・資材のステータス可視化のほか、属人化していた購買情報の共有化による内部不正防止や統制にも役立ちます。
NEWJI DX
製造業に特化したデジタルトランスフォーメーション(DX)の実現を目指す請負開発型のコンサルティングサービスです。AI、iPaaS、および先端の技術を駆使して、製造プロセスの効率化、業務効率化、チームワーク強化、コスト削減、品質向上を実現します。このサービスは、製造業の課題を深く理解し、それに対する最適なデジタルソリューションを提供することで、企業が持続的な成長とイノベーションを達成できるようサポートします。
オンライン講座
製造業、主に購買・調達部門にお勤めの方々に向けた情報を配信しております。
新任の方やベテランの方、管理職を対象とした幅広いコンテンツをご用意しております。
お問い合わせ
コストダウンが利益に直結する術だと理解していても、なかなか前に進めることができない状況。そんな時は、newjiのコストダウン自動化機能で大きく利益貢献しよう!
(Β版非公開)