- お役立ち記事
- A must-see for IT department managers! How to digitalize your production site using IoT and big data
A must-see for IT department managers! How to digitalize your production site using IoT and big data
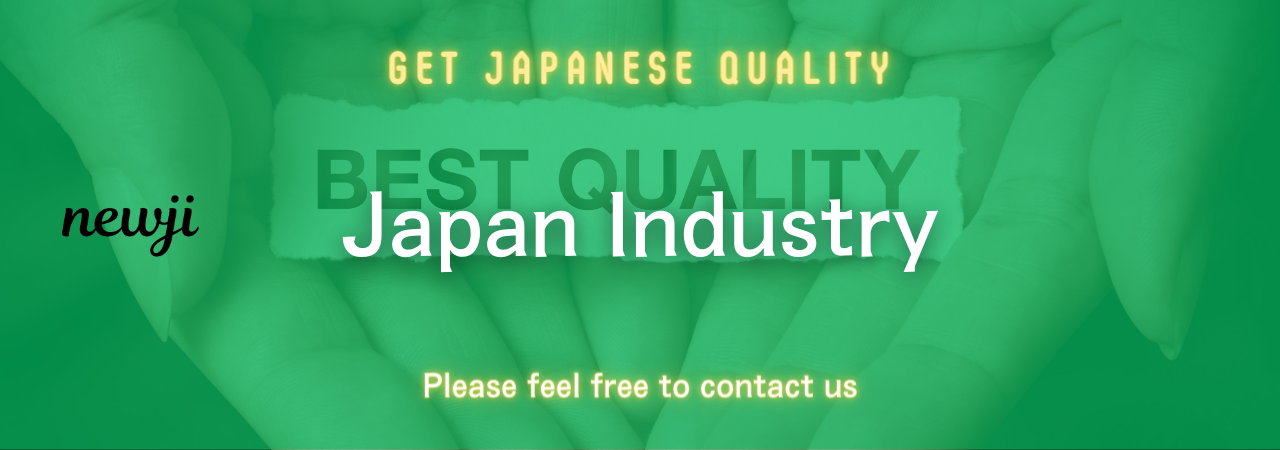
目次
Introduction to Digitalization through IoT and Big Data
In the rapidly evolving world of manufacturing, digital transformation is no longer a luxury but a necessity.
IT department managers play a crucial role in driving this change by leveraging IoT (Internet of Things) and big data to digitalize production sites.
This article explores the benefits, steps, and strategic considerations for effectively integrating these technologies in a manufacturing environment.
Understanding IoT and Big Data
What is IoT?
IoT refers to the network of physical devices connected over the internet, capable of collecting and sharing data.
In the context of manufacturing, IoT devices can include sensors, machines, and equipment that communicate real-time data across the production site.
This connectivity enhances operational efficiency, reduces downtime, and supports predictive maintenance.
What is Big Data?
Big data involves the massive volumes of structured and unstructured data generated from various sources.
In manufacturing, this data comes from IoT devices, production logs, supply chain information, and more.
Analyzing big data helps in making informed decisions about improving production processes, forecasting demand, and optimizing resource allocation.
Benefits of Digitalizing Production with IoT and Big Data
Enhanced Efficiency and Productivity
By implementing IoT devices, production sites can automate many processes, reducing the need for manual intervention.
Big data analytics allows for identifying bottlenecks and inefficiencies in real-time, leading to improved workflow and productivity.
Predictive Maintenance
With IoT sensors continuously monitoring equipment health and performance, potential issues can be identified before they lead to breakdowns.
This data-driven approach to maintenance minimizes downtime, extends machinery life, and reduces repair costs.
Improved Safety and Quality Control
IoT devices can monitor environmental conditions and equipment status to ensure both safety and quality standards are continually met.
Big data analytics can identify patterns or anomalies that indicate potential safety hazards or quality issues, allowing for prompt corrective actions.
Steps to Digitalize Your Production Site
Step 1: Assess Current Capabilities and Requirements
Begin by evaluating your current production processes and identifying areas where IoT and big data can offer the most impact.
Gather input from various stakeholders, including production teams, IT personnel, and management, to understand their requirements and expectations.
Step 2: Develop a Digitalization Strategy
Create a comprehensive strategy that outlines the goals, scope, and timeline for digitalization.
This should include defining key performance indicators (KPIs) that will measure the success of the implementation and establishing a roadmap for integrating IoT devices and big data analytics into existing processes.
Step 3: Invest in the Right Technology
Select the IoT devices and data analytics platforms that align with your production requirements and digital strategy.
Consider factors like scalability, ease of integration, and vendor support during the selection process.
Step 4: Implement and Integrate
Deploy IoT devices across the production site and seamlessly integrate them with existing systems and networks.
Ensure that there is a robust infrastructure in place to handle data flow and that all devices are properly configured for optimal performance.
Step 5: Train Your Team
Provide thorough training for all relevant personnel to familiarize them with the new technologies.
This includes understanding how to operate IoT devices, interpreting data analytics, and using insights for decision-making.
Step 6: Monitor and Optimize
Continuously monitor the performance of IoT systems and the quality of data analytics.
Use feedback and insights to refine processes, enhance algorithms, and ensure that the technology evolves with the changing needs of the production site.
Strategic Considerations for IT Managers
Data Security and Privacy
Ensure that robust security measures are in place to protect sensitive production data and prevent unauthorized access.
Implement encryption, authentication protocols, and regular security audits to maintain privacy and compliance with industry standards.
Cost Management
While digitalizing production offers long-term cost savings, the initial investments can be significant.
Carefully manage budgets, prioritize high-impact areas, and consider scalable solutions that grow with your production needs.
Collaboration and Communication
Facilitate strong collaboration between IT teams, production staff, and management to ensure that everyone is aligned with digitalization goals.
Regular communication across departments will help in troubleshooting issues, facilitating innovation, and achieving seamless integration.
Conclusion
Digitalizing production sites using IoT and big data is a strategic move that can significantly enhance operational efficiency, safety, and competitiveness.
By understanding the technologies, benefits, and key steps involved, IT department managers can skillfully guide their organizations into a more connected and data-driven future.
Through careful planning, investment, and continuous optimization, digital transformation will empower manufacturing operations to thrive in the modern landscape.
資料ダウンロード
QCD調達購買管理クラウド「newji」は、調達購買部門で必要なQCD管理全てを備えた、現場特化型兼クラウド型の今世紀最高の購買管理システムとなります。
ユーザー登録
調達購買業務の効率化だけでなく、システムを導入することで、コスト削減や製品・資材のステータス可視化のほか、属人化していた購買情報の共有化による内部不正防止や統制にも役立ちます。
NEWJI DX
製造業に特化したデジタルトランスフォーメーション(DX)の実現を目指す請負開発型のコンサルティングサービスです。AI、iPaaS、および先端の技術を駆使して、製造プロセスの効率化、業務効率化、チームワーク強化、コスト削減、品質向上を実現します。このサービスは、製造業の課題を深く理解し、それに対する最適なデジタルソリューションを提供することで、企業が持続的な成長とイノベーションを達成できるようサポートします。
オンライン講座
製造業、主に購買・調達部門にお勤めの方々に向けた情報を配信しております。
新任の方やベテランの方、管理職を対象とした幅広いコンテンツをご用意しております。
お問い合わせ
コストダウンが利益に直結する術だと理解していても、なかなか前に進めることができない状況。そんな時は、newjiのコストダウン自動化機能で大きく利益貢献しよう!
(Β版非公開)