- お役立ち記事
- A must-see for leaders in quality assurance departments in the precision machinery industry! Guaranteeing product quality by introducing a traceability system
A must-see for leaders in quality assurance departments in the precision machinery industry! Guaranteeing product quality by introducing a traceability system
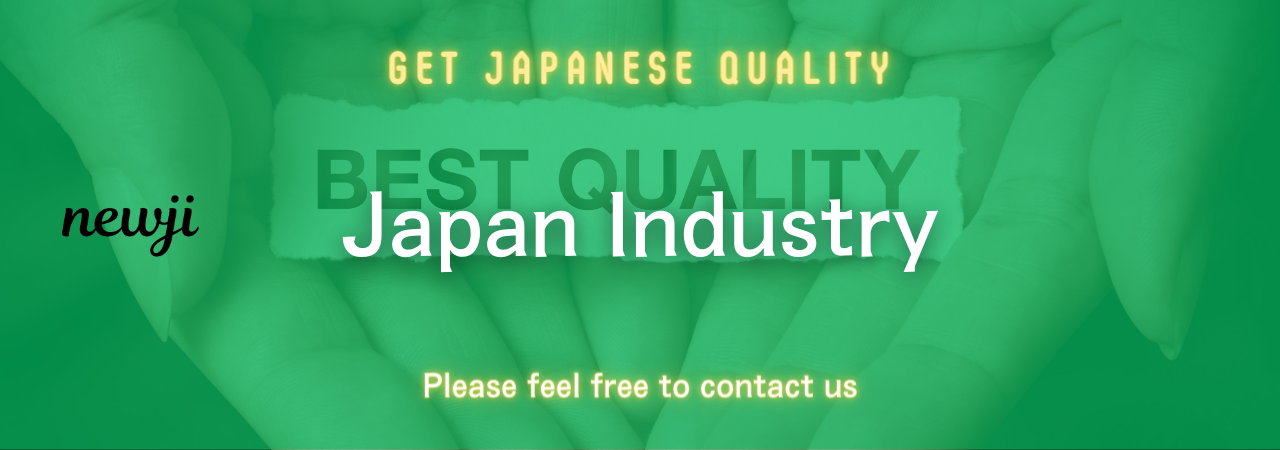
目次
Understanding Traceability Systems
Traceability is a crucial concept in the precision machinery industry, ensuring that products are of high quality and meet the specified standards.
It involves tracking and documenting each stage of the manufacturing process, from raw materials to the final product.
A traceability system allows companies to trace every component used, providing transparency and accountability.
In the precision machinery industry, where accuracy and reliability are paramount, a traceability system can prevent potential mishaps and ensure the highest quality standards.
By maintaining a detailed record of all processes, companies can quickly identify and address any issues that arise.
This not only helps in maintaining quality but also builds trust with clients who rely on consistent and reliable products.
The Importance of Product Quality Assurance
In the precision machinery industry, product quality is non-negotiable.
The slightest deviation can lead to significant issues, resulting in customer dissatisfaction and potential financial losses.
Quality assurance is the bedrock upon which trust is built between manufacturers and clients.
Incorporating a traceability system aids in comprehensive quality assurance by documenting every step of production.
It creates a database where every component can be checked against quality benchmarks.
This level of scrutiny ensures that any defects can be traced back to their source, allowing for quick resolution and preventing future occurrences.
Moreover, it provides a historical record of product performance, helping in the continuous improvement of manufacturing processes.
With rigorous quality assurance in place, companies can confidently guarantee their products, reinforcing their reputation for excellence.
How a Traceability System Benefits Precision Machinery Firms
Implementing a traceability system brings numerous advantages to precision machinery firms:
Enhanced Quality Control
With all production stages documented, any deviations from the standard can be promptly detected and corrected.
This proactive approach minimizes defects and enhances overall product quality.
Improved Compliance
Precision machinery companies often have to meet stringent regulatory standards.
A traceability system helps ensure compliance by providing clear documentation of all processes, making audits and regulatory assessments more streamlined.
Efficient Problem Resolution
When issues do occur, a traceability system allows for swift identification of the root cause.
This leads to faster resolutions, reducing downtime and minimizing losses.
Increased Customer Confidence
Clients have peace of mind knowing that their products are made to the highest standards and can be traced throughout the manufacturing process.
This builds strong customer relationships and encourages repeat business.
Data-Driven Decision Making
With access to historical data and performance insights, companies can make informed decisions on process improvements and strategic directions.
A data-driven approach enhances operational efficiency and drives innovation.
Steps to Implement a Traceability System
Implementing a traceability system requires a thoughtful approach to ensure it meets the specific needs of a precision machinery firm.
Here are essential steps to consider:
Identify Key Processes
Begin by pinpointing critical processes where traceability is necessary.
This could involve key production stages, critical components, or specific materials that need tracking.
Select the Right Technology
Choose appropriate technology solutions that fit the company’s size and complexity.
This could range from barcode systems to advanced software solutions that integrate with existing processes.
Data Integration
Ensure that all relevant data sources are integrated into the traceability system.
This ensures seamless communication and easy access to data for analysis and decision-making.
Employee Training
Train employees on the importance of traceability and how to use the system effectively.
A well-trained workforce is critical to ensuring accurate data capture and system utilization.
Continuous Monitoring and Improvement
Once implemented, continuously monitor the system’s effectiveness and make improvements as necessary.
Regularly review data to identify trends and areas for further enhancement.
Challenges and Considerations
While a traceability system offers great benefits, it’s not without challenges.
Cost
Implementing traceability can be costly, especially for smaller businesses.
However, viewing it as a long-term investment in quality and efficiency can mitigate initial concerns.
Complexity
The transition to a traceability system may seem complex.
Careful planning and phased implementation can ease the process and reduce disruptions.
Data Management
Managing and analyzing large amounts of data requires robust data management systems.
Investing in the right software tools and data analytics capabilities is crucial.
Cultural Shift
Fostering a culture of transparency and accountability is essential for successful traceability.
Leadership must advocate for and drive this cultural shift within the organization.
Conclusion
For leaders in quality assurance departments in the precision machinery industry, implementing a traceability system is essential for ensuring product quality and maintaining competitive advantage.
With benefits such as improved quality control, regulatory compliance, and customer satisfaction, it’s a strategic investment that ensures precision, reliability, and excellence.
By prioritizing traceability, companies can uphold the highest quality standards, retain customer trust, and future-proof their operations in an increasingly demanding market landscape.
資料ダウンロード
QCD調達購買管理クラウド「newji」は、調達購買部門で必要なQCD管理全てを備えた、現場特化型兼クラウド型の今世紀最高の購買管理システムとなります。
ユーザー登録
調達購買業務の効率化だけでなく、システムを導入することで、コスト削減や製品・資材のステータス可視化のほか、属人化していた購買情報の共有化による内部不正防止や統制にも役立ちます。
NEWJI DX
製造業に特化したデジタルトランスフォーメーション(DX)の実現を目指す請負開発型のコンサルティングサービスです。AI、iPaaS、および先端の技術を駆使して、製造プロセスの効率化、業務効率化、チームワーク強化、コスト削減、品質向上を実現します。このサービスは、製造業の課題を深く理解し、それに対する最適なデジタルソリューションを提供することで、企業が持続的な成長とイノベーションを達成できるようサポートします。
オンライン講座
製造業、主に購買・調達部門にお勤めの方々に向けた情報を配信しております。
新任の方やベテランの方、管理職を対象とした幅広いコンテンツをご用意しております。
お問い合わせ
コストダウンが利益に直結する術だと理解していても、なかなか前に進めることができない状況。そんな時は、newjiのコストダウン自動化機能で大きく利益貢献しよう!
(Β版非公開)