- お役立ち記事
- A must-see for leaders in the design department of the automatic packaging machine seal bar manufacturing industry! Balancing efficient sealing and wear resistance
A must-see for leaders in the design department of the automatic packaging machine seal bar manufacturing industry! Balancing efficient sealing and wear resistance
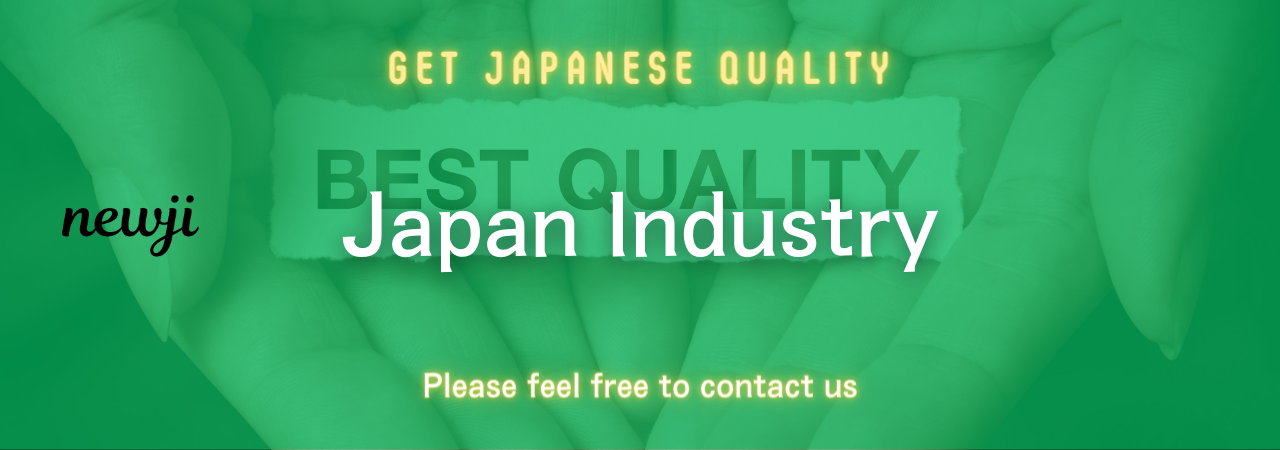
Understanding the Importance of Sealing in Packaging Machines
In the world of automatic packaging machines, the seal bar plays a critical role in ensuring product integrity.
A well-functioning seal bar is essential for maintaining product freshness, preventing contamination, and securing packaging.
It’s the component of the machine that applies heat and pressure to two pieces of packaging material to bond them together.
Balancing efficiency and durability in these seal bars is a challenge that leaders in the design department must address.
Efficient sealing is necessary to keep up with production demands, while the wear resistance of the seal bar ensures longevity and reduces the need for frequent replacements.
The Role of the Design Leader
Leaders in the design department are tasked with creating seal bars that can fulfill the dual objectives of performance and durability.
This requires a deep understanding of materials, machine mechanics, and the specific requirements of the packaging industry.
A leader must see the bigger picture, ensuring that the products are not only of high quality but also cost-effective.
The key is to leverage innovative materials and design strategies that provide both effective sealing and wear resistance.
This includes exploring various alloys and coatings that can withstand the high pressures and temperatures required in sealing processes.
Materials Matter
Choosing the right materials is a fundamental step in balancing efficient sealing with wear resistance.
Seal bars are typically made from stainless steel or aluminum due to their excellent properties, including corrosion resistance and thermal conductivity.
However, each material has its own strengths and limitations.
Stainless steel, for instance, is known for its strength and durability, making it suitable for high-pressure applications.
This metal is also resistant to rust and can handle a variety of temperatures.
On the other hand, aluminum is lightweight and easily conducts heat, which can enhance efficiency and reduce energy consumption in some applications.
Depending on the specific needs of the production line, leaders might consider integrating additional elements like titanium or specific coatings to enhance the surface properties of the seal bars.
Innovative Coatings and Treatments
Coatings and surface treatments can significantly extend the lifespan of seal bars, reducing wear and tear.
For instance, Teflon coatings are popular due to their low friction properties and resistance to heat and chemical reactions.
These coatings can minimize the adhesion of packaging materials to the seal bar, reducing the risk of damage and residue build-up.
Similarly, treatments like nitriding and plasma spraying can be used to harden the surface of the seal bar, making it more resistant to wear.
These processes introduce layers of hardened material, enhancing durability without compromising the efficiency of the sealing process.
Precision Engineering for Optimal Performance
Precision engineering is crucial in designing seal bars that offer both effective sealing and resistance to wear.
Accurate machining and manufacturing techniques ensure that seal bars meet the required specifications and can integrate seamlessly with packaging machines.
Computer-Aided Design (CAD) and Computer-Aided Manufacturing (CAM) tools allow engineers to simulate and test different designs before actual production.
These tools help in predicting the performance of seal bars under various conditions, allowing for adjustments that may enhance efficiency and durability.
Regular Maintenance and Monitoring
Despite the best design efforts, regular maintenance and monitoring are necessary to sustain the performance of seal bars.
Ensuring that seal bars are regularly inspected and maintained can help identify potential issues before they lead to machine downtime.
Implementing a maintenance schedule is vital.
This schedule should include regular cleaning, checking for wear, and occasionally recalibrating the settings to ensure consistent sealing.
By investing in proper maintenance practices, companies can maximize the lifespan of their seal bars and maintain production efficiency.
Balancing Cost and Quality
For leaders in this industry, it’s crucial to find a balance between cost and quality.
High-quality materials and coatings may come at a higher cost, but the benefits of reduced downtime and longer-lasting equipment can lead to cost savings in the long run.
Decisions regarding material and design must be weighed with the expected return on investment.
Leaders must ensure that investments in higher-quality components are justified by enhanced machine performance and lower maintenance costs over time.
The Future of Seal Bar Design
As technology advances, the future of seal bar design will likely see more sophisticated materials and manufacturing techniques.
The integration of smart technology may lead to what are known as “smart seal bars,” which could self-monitor for signs of wear and optimize their performance in real-time.
Research into nanotechnology might introduce materials with never-before-seen properties, offering better performance and even greater resistance to wear.
Leaders in design must stay abreast of these trends to maintain their competitive edge in the packaging industry.
By understanding the complexities of seal bar materials, coatings, and engineering, the design department can develop solutions that meet the evolving needs of automatic packaging machines, balancing efficiency with durability to achieve optimal performance.
資料ダウンロード
QCD調達購買管理クラウド「newji」は、調達購買部門で必要なQCD管理全てを備えた、現場特化型兼クラウド型の今世紀最高の購買管理システムとなります。
ユーザー登録
調達購買業務の効率化だけでなく、システムを導入することで、コスト削減や製品・資材のステータス可視化のほか、属人化していた購買情報の共有化による内部不正防止や統制にも役立ちます。
NEWJI DX
製造業に特化したデジタルトランスフォーメーション(DX)の実現を目指す請負開発型のコンサルティングサービスです。AI、iPaaS、および先端の技術を駆使して、製造プロセスの効率化、業務効率化、チームワーク強化、コスト削減、品質向上を実現します。このサービスは、製造業の課題を深く理解し、それに対する最適なデジタルソリューションを提供することで、企業が持続的な成長とイノベーションを達成できるようサポートします。
オンライン講座
製造業、主に購買・調達部門にお勤めの方々に向けた情報を配信しております。
新任の方やベテランの方、管理職を対象とした幅広いコンテンツをご用意しております。
お問い合わせ
コストダウンが利益に直結する術だと理解していても、なかなか前に進めることができない状況。そんな時は、newjiのコストダウン自動化機能で大きく利益貢献しよう!
(Β版非公開)