- お役立ち記事
- A must-see for leaders in the design department of the stainless steel filter manufacturing industry for medical devices! Technology that increases corrosion resistance and precision
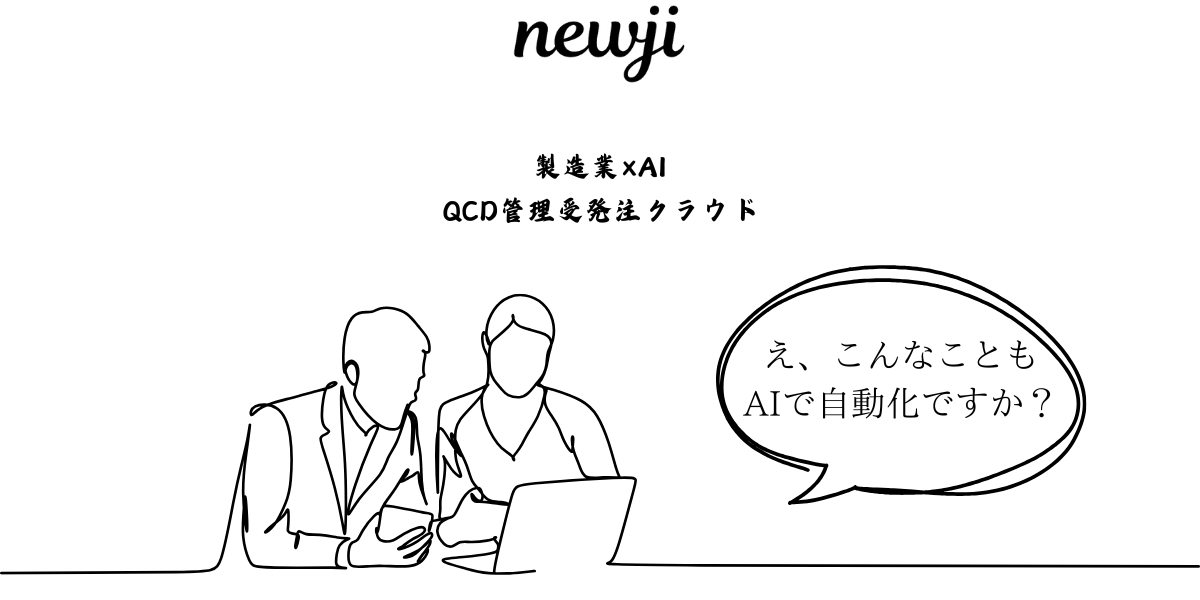
A must-see for leaders in the design department of the stainless steel filter manufacturing industry for medical devices! Technology that increases corrosion resistance and precision
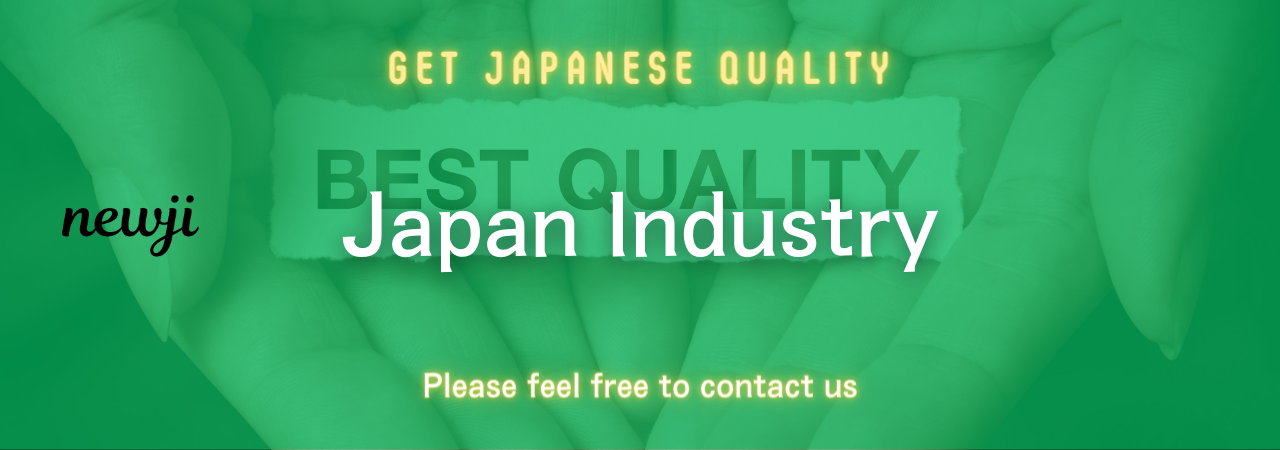
目次
Understanding the Importance of Stainless Steel Filters
Stainless steel filters play a crucial role in the manufacturing of medical devices.
These filters are known for their durability and resistance to corrosion, making them ideal for creating high-quality medical equipment.
As a leader in the design department, understanding the technology behind these filters is essential.
Not only do they ensure the safety and efficiency of medical devices, but they also help maintain the integrity of the equipment over time.
Medical devices often require components that can withstand harsh environments without degrading.
This is where stainless steel filters come in.
Their corrosion resistance ensures longevity and reliability, which are significant factors in the healthcare industry.
Moreover, precision in manufacturing these filters directly impacts the performance of medical devices.
Therefore, investing in technology that enhances these attributes is vital for continued success.
Advancements in Technology to Enhance Corrosion Resistance
Recent advancements in technology have led to significant improvements in the corrosion resistance of stainless steel filters.
Through innovative alloying techniques and surface treatments, the durability of these filters has increased exponentially.
The introduction of chromium, nickel, and molybdenum in the alloy composition has proven to be particularly effective.
These elements enhance the passive layer on stainless steel, making it more resistant to environmental and chemical degradation.
Additionally, surface treatments such as passivation and electropolishing have also contributed to improved corrosion resistance.
Passivation removes surface contaminants and strengthens the protective oxide layer, while electropolishing smoothens the metal surface, reducing crevices where corrosion may start.
These technological advancements have collectively enhanced the longevity and performance of stainless steel filters, ensuring that medical devices remain uncompromised in their functionality.
Precision Manufacturing Processes for Ultimate Performance
Precision in manufacturing is not only a benefit but a necessity in the production of stainless steel filters for medical devices.
The intricacies of intricate design and the need for exact specifications mean that precision is key to meeting industry standards.
With the advent of advanced manufacturing technologies such as laser cutting and electron beam welding, the level of precision achievable today is remarkable.
These technologies allow for precise control during the manufacturing process, ensuring that every filter meets exacting standards.
Furthermore, computer-aided design (CAD) software plays a critical role in precision engineering.
By creating virtual prototypes, designers can foresee potential issues and make necessary adjustments before production begins.
This not only saves time and resources but also ensures that the final products are of the highest quality.
Moreover, 3D printing technology has emerged as a revolutionary tool in creating complex structures with notable precision.
This technology allows for the creation of bespoke filter designs that cater to specific medical device requirements, thus broadening the scope of applications for stainless steel filters.
Ensuring Quality through Rigorous Testing
Quality assurance is fundamental in the production of stainless steel filters for medical devices.
Given the critical nature of their end-use, these filters must undergo rigorous testing processes to ensure they meet all industry standards.
Nondestructive testing methods, such as ultrasonic testing and radiographic testing, are often employed to evaluate the integrity and strength of the filters without causing any damage.
These testing methods help identify any defects or weaknesses that might compromise the performance of the filters.
Additionally, corrosion testing is vital to ensure that the filters can withstand exposure to various harsh conditions without deteriorating.
Salt spray testing, for instance, simulates long-term exposure to corrosive environments, providing a clear understanding of the filter’s performance under such conditions.
By engaging in these rigorous testing protocols, manufacturers can guarantee that their stainless steel filters provide reliable and long-lasting service in medical devices.
Collaboration for Continuous Improvement
Innovation in the stainless steel filter industry is driven by continuous collaboration among designers, engineers, and researchers.
By working together, these professionals can share insights, develop new ideas, and refine existing technologies to improve the performance of stainless steel filters.
Regular engagement with medical device manufacturers also provides valuable feedback that can guide the advancement of filter technology.
Understanding the specific needs and applications of medical devices helps in developing filters that are more tailored to end-user requirements.
Educational programs and workshops are also instrumental in keeping professionals updated with the latest trends and technological advancements in the industry.
These platforms encourage knowledge exchange and foster an environment for creative problem-solving.
Through continuous collaboration and learning, the future of stainless steel filters for medical devices looks promising and bright.
Conclusion
For leaders in the design department of the stainless steel filter manufacturing industry for medical devices, staying ahead of the curve is crucial.
With advancements in corrosion resistance and precision manufacturing technology, the potential for innovation and improvement is extensive.
By embracing these technological advancements, conducting rigorous testing, and fostering a collaborative environment, manufacturers can ensure that they are producing the highest quality stainless steel filters.
These efforts will not only increase the efficiency and reliability of medical devices but will also position the industry for future success.
資料ダウンロード
QCD調達購買管理クラウド「newji」は、調達購買部門で必要なQCD管理全てを備えた、現場特化型兼クラウド型の今世紀最高の購買管理システムとなります。
ユーザー登録
調達購買業務の効率化だけでなく、システムを導入することで、コスト削減や製品・資材のステータス可視化のほか、属人化していた購買情報の共有化による内部不正防止や統制にも役立ちます。
NEWJI DX
製造業に特化したデジタルトランスフォーメーション(DX)の実現を目指す請負開発型のコンサルティングサービスです。AI、iPaaS、および先端の技術を駆使して、製造プロセスの効率化、業務効率化、チームワーク強化、コスト削減、品質向上を実現します。このサービスは、製造業の課題を深く理解し、それに対する最適なデジタルソリューションを提供することで、企業が持続的な成長とイノベーションを達成できるようサポートします。
オンライン講座
製造業、主に購買・調達部門にお勤めの方々に向けた情報を配信しております。
新任の方やベテランの方、管理職を対象とした幅広いコンテンツをご用意しております。
お問い合わせ
コストダウンが利益に直結する術だと理解していても、なかなか前に進めることができない状況。そんな時は、newjiのコストダウン自動化機能で大きく利益貢献しよう!
(Β版非公開)