- お役立ち記事
- A must-see for leaders in the processing technology department of the steel industry! The secret to producing high-purity steel through the vacuum smelting process
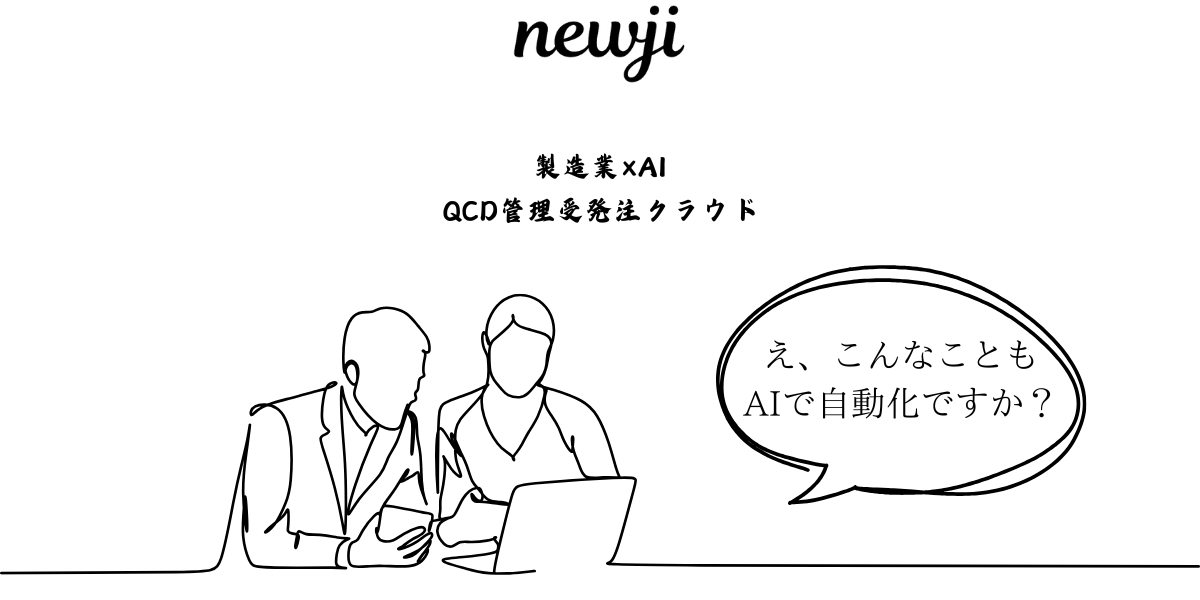
A must-see for leaders in the processing technology department of the steel industry! The secret to producing high-purity steel through the vacuum smelting process
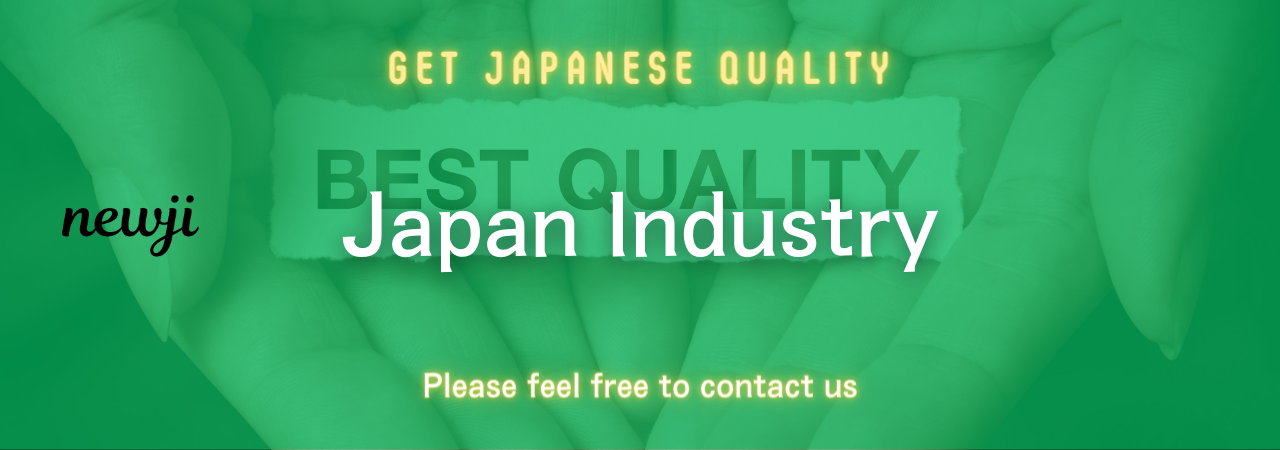
目次
Understanding the Vacuum Smelting Process
The steel industry plays a crucial role in the development of modern infrastructure, providing essential materials for construction, transportation, and manufacturing.
One significant advancement in steel processing technology is the vacuum smelting process.
This innovative method has enabled the production of high-purity steel, which is essential for various high-performance applications.
The vacuum smelting process involves melting steel under reduced pressure conditions.
This occurs in a vacuum induction furnace where the atmosphere is rigorously controlled, allowing undesirable gases and impurities to be eliminated efficiently.
The result is high-purity steel, with fewer inclusions and improved mechanical properties.
Advantages of Vacuum Smelting
One of the primary benefits of vacuum smelting is the significant reduction in impurities, such as hydrogen, nitrogen, and carbon, which can adversely affect steel’s performance.
By reducing these contaminants, vacuum smelting enhances the material’s strength, ductility, and resistance to fatigue and corrosion.
Another advantage is the ability to produce steel with specific chemical compositions tailored to meet the demands of exacting applications.
This high degree of compositional control ensures consistency and reliability in the finished product, which is vital for critical industries like aerospace and automotive manufacturing.
Additionally, the vacuum smelting process enhances the microstructural integrity of steel.
The controlled environment minimizes the formation of unwanted phases, such as carbides and nitrides, which can compromise steel’s mechanical properties.
As a result, vacuum smelting produces steel with a more uniform microstructure, leading to predictable performance in demanding conditions.
The Steps of the Vacuum Smelting Process
Understanding the vacuum smelting process requires an appreciation of its sequential steps, each meticulously designed to optimize steel quality.
Preparation and Melting
The process begins with the selection of raw materials.
High-quality scrap steel or specially prepared alloy components are chosen to ensure the desired chemical composition.
These materials are then placed in a vacuum induction furnace.
In this furnace, electromagnetic induction is used to generate heat, causing the materials to melt uniformly.
As the melting progresses, the furnace is evacuated of air to create the necessary vacuum conditions.
This low-pressure environment is critical to preventing oxidation and contamination during the melting phase.
Degassing and Refining
Once the steel has melted, the next crucial step is degassing.
By further reducing the pressure and maintaining the vacuum, gases dissolved in the molten steel are encouraged to escape.
This step significantly decreases the levels of hydrogen and oxygen, which are detrimental to steel’s mechanical properties.
During refining, specific alloying elements are added to the molten steel to achieve the desired chemical composition.
These elements are carefully selected to ensure optimal performance characteristics in the final product.
Solidification
After refining, the molten steel is slowly cooled and solidified under vacuum conditions.
This controlled cooling process ensures the development of a refined microstructure with superior mechanical properties.
The ingots produced are then subjected to further processing, such as rolling or forging, to form the final product.
Applications of High-Purity Steel
High-purity steel produced through vacuum smelting is highly sought after in industries where performance and reliability are paramount.
Aerospace Industry
In the aerospace industry, materials must withstand extreme conditions, including high temperatures, pressures, and vibrations.
High-purity steel’s enhanced strength and fatigue resistance make it an ideal choice for components such as aircraft landing gear, turbine blades, and engine parts.
Automotive Industry
The automotive industry benefits from high-purity steel in the production of advanced vehicle components.
Its superior strength-to-weight ratio and resistance to corrosion contribute to the development of safer and more fuel-efficient vehicles.
Energy Sector
In the energy sector, high-purity steel is essential for constructing critical infrastructure.
Its durability and resistance to hydrogen embrittlement make it a vital material for building pipelines, nuclear reactors, and wind turbine towers.
Future Prospects and Innovations
The vacuum smelting process continues to evolve with technological advancements, opening new possibilities for producing even purer steel with enhanced properties.
Researchers are exploring the potential of integrating artificial intelligence and machine learning into the process.
These technologies could optimize the smelting parameters, resulting in even greater control over the steel’s composition and microstructure.
Moreover, efforts are being made to improve the sustainability of the vacuum smelting process.
Developing more energy-efficient furnaces and reducing emissions are priorities for the industry, aligning with global efforts to minimize environmental impact.
The increasing demands for high-performance materials in various industries ensure that the vacuum smelting process remains a key focus for future innovations in steelmaking.
In conclusion, the vacuum smelting process has revolutionized the production of high-purity steel, offering significant benefits in terms of purity, performance, and reliability.
Understanding and optimizing this process is crucial for leaders in the steel industry’s processing technology department, as the demand for superior materials continues to grow in multiple sectors.
資料ダウンロード
QCD調達購買管理クラウド「newji」は、調達購買部門で必要なQCD管理全てを備えた、現場特化型兼クラウド型の今世紀最高の購買管理システムとなります。
ユーザー登録
調達購買業務の効率化だけでなく、システムを導入することで、コスト削減や製品・資材のステータス可視化のほか、属人化していた購買情報の共有化による内部不正防止や統制にも役立ちます。
NEWJI DX
製造業に特化したデジタルトランスフォーメーション(DX)の実現を目指す請負開発型のコンサルティングサービスです。AI、iPaaS、および先端の技術を駆使して、製造プロセスの効率化、業務効率化、チームワーク強化、コスト削減、品質向上を実現します。このサービスは、製造業の課題を深く理解し、それに対する最適なデジタルソリューションを提供することで、企業が持続的な成長とイノベーションを達成できるようサポートします。
オンライン講座
製造業、主に購買・調達部門にお勤めの方々に向けた情報を配信しております。
新任の方やベテランの方、管理職を対象とした幅広いコンテンツをご用意しております。
お問い合わせ
コストダウンが利益に直結する術だと理解していても、なかなか前に進めることができない状況。そんな時は、newjiのコストダウン自動化機能で大きく利益貢献しよう!
(Β版非公開)