- お役立ち記事
- A must-see for leaders in the production technology department of the auto parts industry! How to dramatically improve component strength with friction stir welding (FSW)
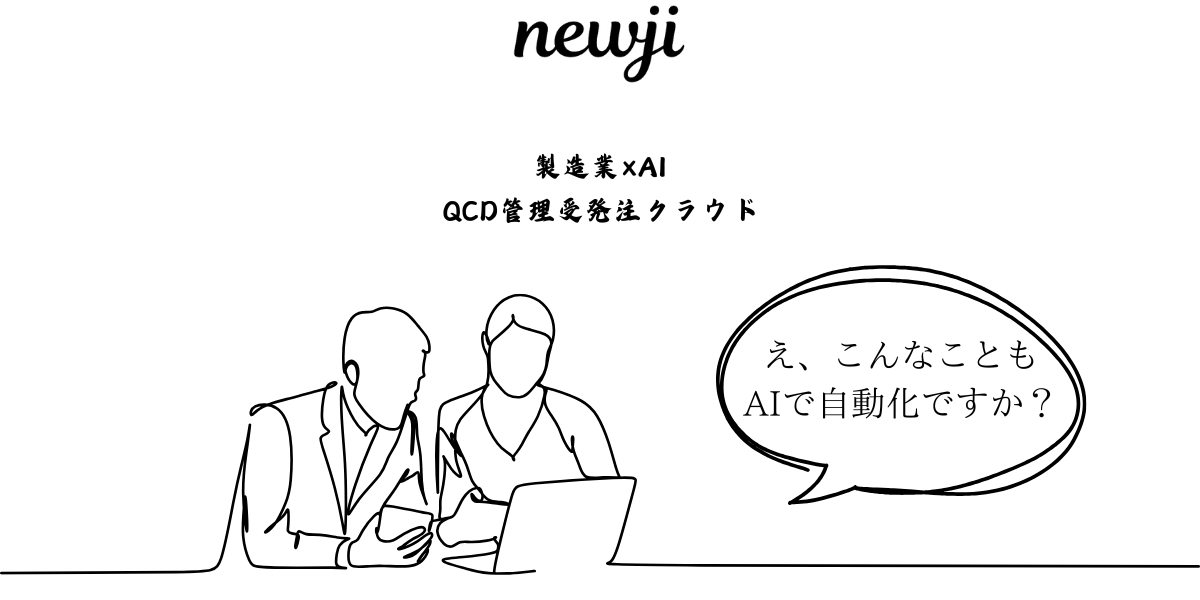
A must-see for leaders in the production technology department of the auto parts industry! How to dramatically improve component strength with friction stir welding (FSW)
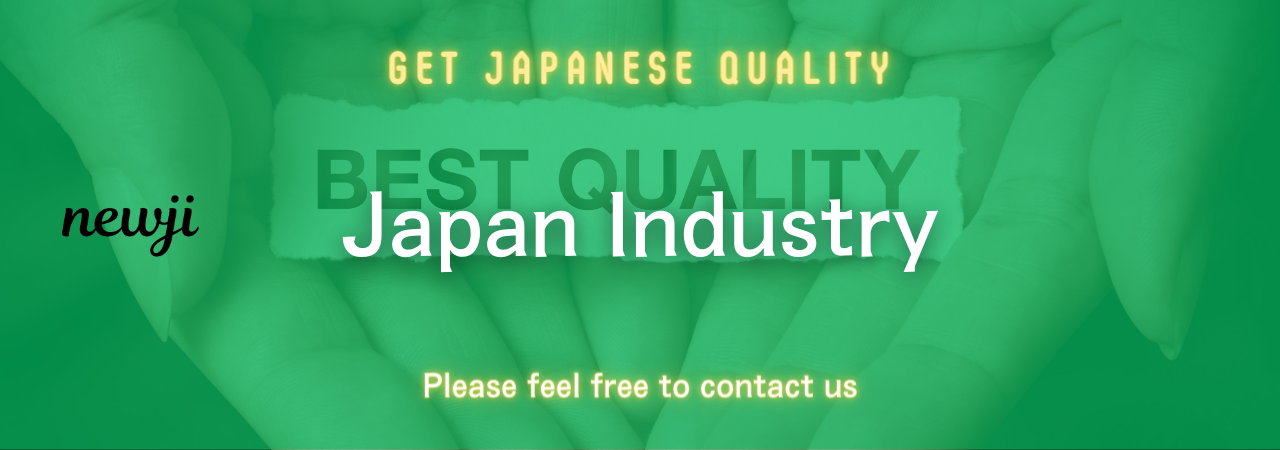
目次
Understanding Friction Stir Welding (FSW)
Friction Stir Welding (FSW) is a cutting-edge technology revolutionizing the welding process in various industries, particularly in the auto parts sector.
This technique involves the joining of materials using a rotating tool that generates frictional heat, causing the material to soften and fuse without reaching the melting point.
The process results in a weld with superior strength and durability compared to traditional welding methods.
FSW is gaining increasing popularity due to its ability to improve component strength while minimizing defects and distortions.
The Benefits of FSW in Auto Parts Manufacturing
FSW offers several advantages over conventional welding methods, making it an ideal choice for the production of auto parts.
One of the primary benefits is the significant improvement in the mechanical properties of the welded components.
The joint produced by FSW exhibits higher tensile strength and fatigue resistance, which is essential for parts subjected to high stress and strain.
Another notable advantage is the minimal heat-affected zone (HAZ) in FSW.
Traditional welding often leads to a large HAZ, which can weaken the materials at the weld’s edges.
In contrast, FSW generates less heat, preserving the material’s properties and ensuring greater structural integrity.
Furthermore, FSW eliminates common welding defects like porosity and cracking, resulting in reliable and high-quality welds.
Enhanced Efficiency and Cost-Effective Solutions
Implementing FSW in the auto parts industry also leads to enhanced manufacturing efficiency.
The process is highly automated, reducing the need for manual labor and minimizing operator errors.
This automation contributes to decreased production time, allowing manufacturers to meet increasing demands without compromising quality.
In terms of cost-effectiveness, FSW eliminates the need for consumables such as filler materials and shielding gases.
This reduction in resource consumption results in lower production costs, making FSW an economically viable option for auto parts manufacturers.
Moreover, the durability and strength of FSW joints lead to longer-lasting components, reducing the need for replacements and repairs over time.
Applications of FSW in Auto Parts
Friction Stir Welding is suited for a wide range of applications within the automotive industry.
One prominent use is in the manufacturing of lightweight components, which are crucial for enhancing fuel efficiency.
FSW is particularly effective in welding aluminum and magnesium alloys, which are increasingly used in automotive parts to reduce vehicle weight.
FSW is also employed in the production of body panels, chassis components, and heat exchangers.
These parts require precise and robust joints to withstand the rigorous demands of the automotive environment.
The superior strength of FSW welds ensures these components perform reliably, contributing to vehicle safety and performance.
Challenges and Considerations
While FSW presents many benefits, there are challenges and considerations manufacturers must address to implement it effectively.
One challenge is the initial setup cost, which can be significant due to the need for specialized equipment and training.
However, the long-term benefits and savings often outweigh these initial expenses.
Furthermore, there is a learning curve associated with mastering FSW, as operators must acquire new skills to manage the process.
Continuous training and investment in talent development are critical for maximizing the potential of FSW technology.
Future Trends and Developments
The future of Friction Stir Welding in the auto parts industry looks promising, with ongoing research and advancements in technology.
One trend is the development of improved tool materials and designs, enhancing the efficiency and versatility of the FSW process.
Additionally, advancements in robotics and automation are making FSW even more accessible and efficient, allowing for greater precision and repeatability.
Manufacturers continue to explore the integration of FSW with other innovative technologies, such as additive manufacturing, to further enhance the capabilities and applications of this welding method.
Conclusion
For leaders in the production technology department of the auto parts industry, embracing Friction Stir Welding is a strategic move towards enhancing component strength and overall manufacturing quality.
With its numerous advantages, including improved mechanical properties, reduced defects, and cost savings, FSW is poised to become a standard in automotive manufacturing.
By understanding the benefits, applications, and future trends of FSW, industry leaders can make informed decisions that drive innovation and competitiveness in their operations.
資料ダウンロード
QCD調達購買管理クラウド「newji」は、調達購買部門で必要なQCD管理全てを備えた、現場特化型兼クラウド型の今世紀最高の購買管理システムとなります。
ユーザー登録
調達購買業務の効率化だけでなく、システムを導入することで、コスト削減や製品・資材のステータス可視化のほか、属人化していた購買情報の共有化による内部不正防止や統制にも役立ちます。
NEWJI DX
製造業に特化したデジタルトランスフォーメーション(DX)の実現を目指す請負開発型のコンサルティングサービスです。AI、iPaaS、および先端の技術を駆使して、製造プロセスの効率化、業務効率化、チームワーク強化、コスト削減、品質向上を実現します。このサービスは、製造業の課題を深く理解し、それに対する最適なデジタルソリューションを提供することで、企業が持続的な成長とイノベーションを達成できるようサポートします。
オンライン講座
製造業、主に購買・調達部門にお勤めの方々に向けた情報を配信しております。
新任の方やベテランの方、管理職を対象とした幅広いコンテンツをご用意しております。
お問い合わせ
コストダウンが利益に直結する術だと理解していても、なかなか前に進めることができない状況。そんな時は、newjiのコストダウン自動化機能で大きく利益貢献しよう!
(Β版非公開)