- お役立ち記事
- A must-see for leaders in the R&D department! Successful example of process optimization using response surface methodology
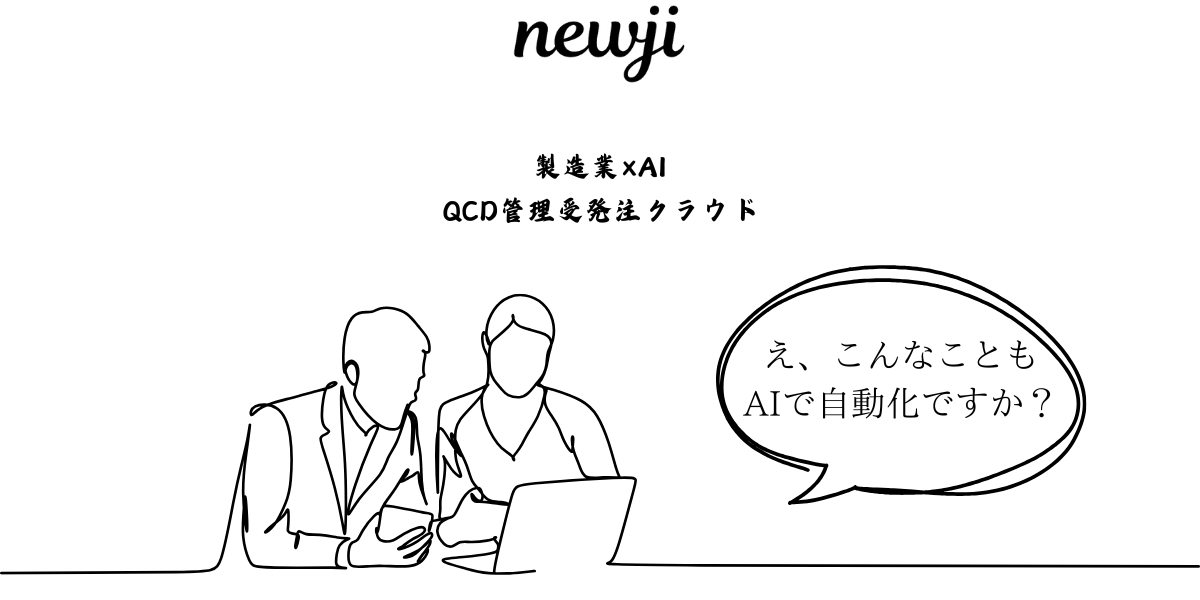
A must-see for leaders in the R&D department! Successful example of process optimization using response surface methodology
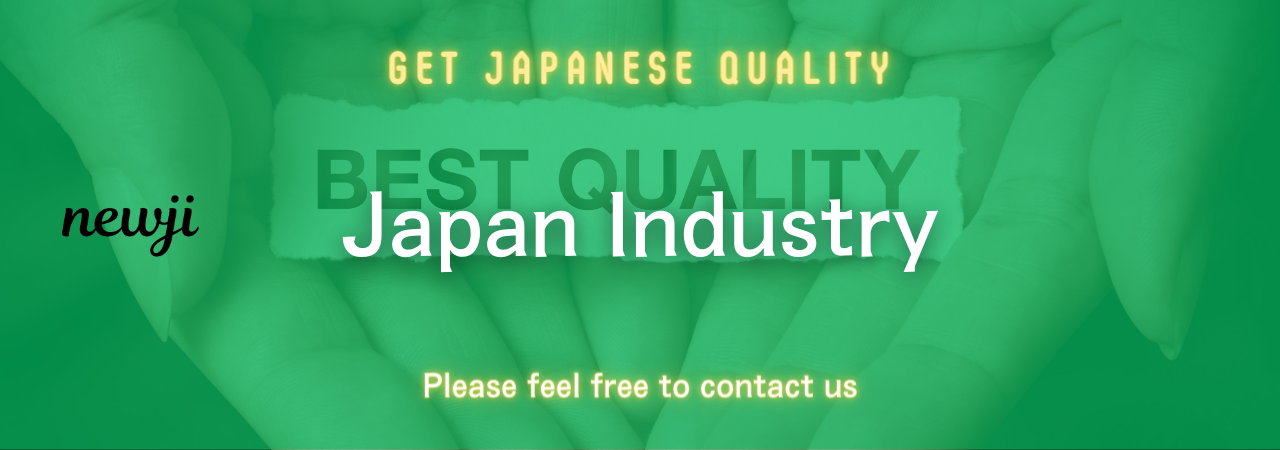
目次
Introduction to Response Surface Methodology
In today’s fast-paced business environment, companies continually seek ways to improve processes and enhance productivity.
For leaders in Research and Development (R&D) departments, optimizing processes can be a game changer, leading to increased efficiency and better product outcomes.
One influential tool in achieving this is Response Surface Methodology (RSM).
This statistical method is crucial for developing, improving, and optimizing processes.
RSM is a collection of mathematical and statistical techniques useful for modeling and analyzing problems where a response of interest is influenced by several variables.
Its primary goal is to optimize this response.
It’s a potent tool for leaders in R&D as it provides a structured approach to process improvement, offering insights that can lead to significant advancements.
Understanding the Basics of RSM
To successfully harness the power of RSM, leaders must first understand its foundational concepts.
The methodology starts with the design of experiments (DOE).
DOE helps systematically plan experiments aiming to understand the effect of variables on output.
RSM takes this further by creating a model that represents the system’s processes.
This model helps predict and analyze the response when variables change, thus identifying optimal operational settings.
By using this predictive model, R&D leaders can efficiently explore the effects of several simultaneous factors and identify their interactions.
The Benefits of RSM in Process Optimization
One of the key benefits of RSM is its ability to provide a comprehensive understanding of the complex processes involved in product development.
This understanding enables R&D leaders to make informed decisions about process improvements.
Another advantage is cost reduction.
Through RSM, organizations can determine the most influential factors affecting a process and focus resources on them, minimizing waste and reducing operational costs.
Additionally, it facilitates quicker product development cycles by identifying optimal conditions sooner.
Furthermore, RSM improves quality assurance.
By accurately identifying process variables that impact quality, R&D leaders can ensure consistent product quality.
This consistency is paramount in industries where precision and reliability are critical, such as pharmaceuticals and electronics.
Implementing RSM: A Step-by-Step Guide
For R&D leaders considering RSM, understanding the implementation process is crucial. Here’s a basic guide to getting started:
1. **Define the Problem**: Begin by clearly defining the process or response you wish to optimize.
Set specific goals and identify all influential variables.
2. **Design the Experiment**: Utilize statistical software to design experiments.
Choose a suitable experiment plan that considers all variables and potential interactions.
3. **Conduct Experiments**: Run the experiments according to the designed plan, ensuring that all necessary data are collected accurately.
4. **Develop the Model**: Use collected data to build a mathematical model that represents the process.
This model will help predict how variable changes affect the response.
5. **Optimize the Process**: With the model, determine the optimal variable combinations to achieve desired response levels.
6. **Validate Results**: Conduct additional experiments to verify that the predicted optimal conditions yield expected improvements.
7. **Implementation and Monitoring**: Finally, implement the optimized process in real-world conditions and continuously monitor the outcomes to ensure sustained performance.
Successful Example of RSM in Action
To better illustrate the potential of RSM, consider its application in the automotive industry.
An R&D team faced challenges with the paint application process.
Inconsistencies resulted in increased waste and defects, impacting both costs and productivity.
By applying RSM, the team defined the critical variables affecting paint application, such as temperature, viscosity, and spray time.
The RSM model allowed them to simulate various scenarios and identify optimal parameters.
After implementing the changes, the team observed a significant reduction in paint-related defects.
This optimization led to cost savings and improved product quality, demonstrating RSM’s real-world impact.
Challenges and Considerations
While RSM can dramatically improve processes, there are challenges leaders must consider.
Data accuracy is paramount.
Incorrect or incomplete data can lead to faulty models and suboptimal outcomes.
It’s also crucial to ensure the RSM model is simple enough for practical use but complex enough to capture necessary details.
Balancing this can be challenging and might require iterative adjustments.
Furthermore, regular monitoring and adjustments are necessary even after optimization.
Changes in external conditions or materials can affect the process, necessitating tweaks to maintain optimal performance.
Conclusion
For leaders in the R&D department, optimizing processes can mean the difference between mediocrity and excellence.
Response Surface Methodology provides a structured, data-driven approach to explore complex interactions and improve processes effectively.
While the initial setup and modeling require effort, the long-term benefits of applying RSM are undeniable.
From cost reduction to enhanced quality, RSM equips R&D leaders with the tools needed to drive their organizations towards sustainable success.
By understanding and implementing RSM, leaders can foster innovation, maintain competitive advantage, and ensure top-tier product quality and economic efficiency.
資料ダウンロード
QCD調達購買管理クラウド「newji」は、調達購買部門で必要なQCD管理全てを備えた、現場特化型兼クラウド型の今世紀最高の購買管理システムとなります。
ユーザー登録
調達購買業務の効率化だけでなく、システムを導入することで、コスト削減や製品・資材のステータス可視化のほか、属人化していた購買情報の共有化による内部不正防止や統制にも役立ちます。
NEWJI DX
製造業に特化したデジタルトランスフォーメーション(DX)の実現を目指す請負開発型のコンサルティングサービスです。AI、iPaaS、および先端の技術を駆使して、製造プロセスの効率化、業務効率化、チームワーク強化、コスト削減、品質向上を実現します。このサービスは、製造業の課題を深く理解し、それに対する最適なデジタルソリューションを提供することで、企業が持続的な成長とイノベーションを達成できるようサポートします。
オンライン講座
製造業、主に購買・調達部門にお勤めの方々に向けた情報を配信しております。
新任の方やベテランの方、管理職を対象とした幅広いコンテンツをご用意しております。
お問い合わせ
コストダウンが利益に直結する術だと理解していても、なかなか前に進めることができない状況。そんな時は、newjiのコストダウン自動化機能で大きく利益貢献しよう!
(Β版非公開)