- お役立ち記事
- A must-see for machining department managers! Latest tool technology and improved cutting accuracy
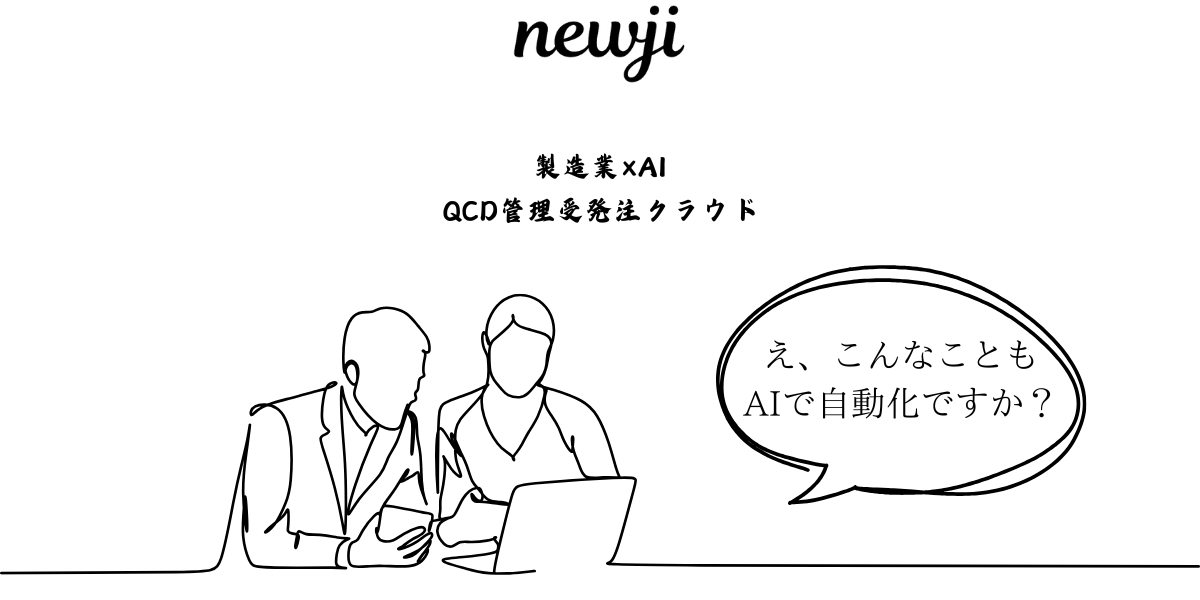
A must-see for machining department managers! Latest tool technology and improved cutting accuracy
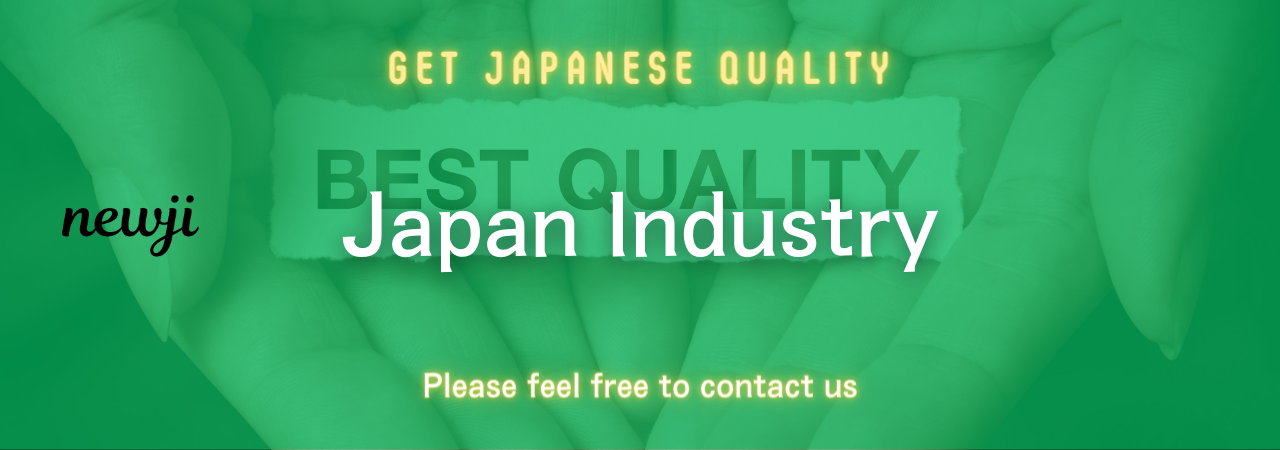
目次
Introduction to the Latest Tool Technology
The world of machining is evolving at a rapid pace, with technological advancements introducing new tools and techniques.
For machining department managers, staying updated with the latest tool technology is essential not only for maintaining cutting precision but also for enhancing operational efficiency.
These innovations are designed to improve the quality of work, reduce costs, and increase the speed of production processes.
In this article, we will delve into the latest developments in tool technology and how they can contribute to improved cutting accuracy in machining operations.
Understanding Cutting Tools in Machining
Cutting tools are the backbone of any machining operation.
They are specifically crafted to remove material from a workpiece, shaping it according to the desired specifications.
The efficiency of a cutting tool is determined by factors such as material composition, cutting speed, tool geometry, and coating.
For machining department managers, choosing the right cutting tool is crucial to achieving optimal results.
Recent advancements in tool technology have significantly enhanced these determinants, leading to improved performance and durability of cutting tools.
Let’s explore these innovations that have revolutionized the machining industry.
Advanced Material Composition
One of the key areas of development in cutting tools is the composition of materials.
Traditionally, high-speed steel (HSS) and carbide have been popular choices.
However, new materials have entered the market, offering superior wear resistance and cutting speed.
Cubic boron nitride (CBN) and polycrystalline diamond (PCD) are two such materials gaining traction.
CBN tools are excellent for machining hard ferrous materials, providing a longer tool life.
PCD tools, on the other hand, are ideal for non-ferrous materials like aluminum, offering high cutting speeds and exceptional surface finish.
These advanced materials not only enhance cutting accuracy but also significantly reduce downtime for tool changes and maintenance.
This leads to increased productivity and cost savings for machining departments.
Innovations in Tool Geometry
The geometry of a cutting tool directly affects its performance.
Innovations in tool design have led to the development of cutting tools with optimized angles, edges, and flute configurations.
These changes result in reduced cutting forces, improved chip removal, and minimized tool wear.
The incorporation of complex geometrical features like variable helix angles and chip breakers ensures smoother cutting processes.
This innovation reduces vibration and noise during machining, contributing to better dimensional accuracy and surface quality.
Experimentation with tool geometry allows for more precision in complex machining tasks, providing machinists with the ability to handle intricate components with ease.
Advanced Tool Coatings
Coating technology has also seen significant advancements, enhancing the performance and lifespan of cutting tools.
Coatings like titanium nitride (TiN), titanium carbonitride (TiCN), and aluminum titanium nitride (AlTiN) are commonly used to reduce friction, improve heat resistance, and extend the working life of cutting tools.
The latest development is the application of nano-structured coatings, which offer superior hardness and oxidation resistance.
These coatings improve the tool’s ability to cut at higher speeds and withstand higher temperatures, thus increasing overall productivity.
The adoption of multi-layered coatings has also proven beneficial for machining harder materials, maintaining sharpness and cutting accuracy over extended periods.
Enhanced Cutting Techniques
In addition to advancements in tool technology, there are improvements in cutting techniques that contribute to increased accuracy and efficiency.
High-speed machining (HSM) and dry machining are gaining popularity due to their ability to enhance surface finish and reduce environmental impact.
HSM involves machining at high spindle speeds and feed rates, which allows for reduced cycle times and increased output.
This technique is especially beneficial for materials that are difficult to machine using conventional methods.
Dry machining, on the other hand, eliminates the need for cutting fluids, reducing environmental concerns and operational costs.
It is ideal for machining materials that do not require constant cooling, maintaining tool integrity over longer runs.
Implementing Technology in Machining Departments
For machining department managers, integrating these technologies involves a strategic approach.
The transition to using advanced cutting tools and techniques should be gradual and well-planned to avoid production disruptions.
It is essential to provide training for machinists on the operation and maintenance of new tools and equipment.
This ensures that the workforce is well-equipped to handle the technological changes and can maximize the benefits of new innovations.
Regular evaluation of tool performance and cutting techniques should be conducted to continually assess improvements and identify areas for enhancement.
Conclusion
The advent of new tool technology and improved cutting techniques presents exciting opportunities for machining departments to enhance cutting accuracy and productivity.
By adopting advanced materials, innovative geometries, and effective coating solutions, department managers can stay at the forefront of the machining industry.
Staying informed and embracing these technological advancements not only bolsters the quality of machining operations but also ensures a competitive edge in the manufacturing sector.
With careful implementation and ongoing training, machining departments can achieve unprecedented levels of efficiency and precision, driving success in today’s dynamic industrial landscape.
資料ダウンロード
QCD調達購買管理クラウド「newji」は、調達購買部門で必要なQCD管理全てを備えた、現場特化型兼クラウド型の今世紀最高の購買管理システムとなります。
ユーザー登録
調達購買業務の効率化だけでなく、システムを導入することで、コスト削減や製品・資材のステータス可視化のほか、属人化していた購買情報の共有化による内部不正防止や統制にも役立ちます。
NEWJI DX
製造業に特化したデジタルトランスフォーメーション(DX)の実現を目指す請負開発型のコンサルティングサービスです。AI、iPaaS、および先端の技術を駆使して、製造プロセスの効率化、業務効率化、チームワーク強化、コスト削減、品質向上を実現します。このサービスは、製造業の課題を深く理解し、それに対する最適なデジタルソリューションを提供することで、企業が持続的な成長とイノベーションを達成できるようサポートします。
オンライン講座
製造業、主に購買・調達部門にお勤めの方々に向けた情報を配信しております。
新任の方やベテランの方、管理職を対象とした幅広いコンテンツをご用意しております。
お問い合わせ
コストダウンが利益に直結する術だと理解していても、なかなか前に進めることができない状況。そんな時は、newjiのコストダウン自動化機能で大きく利益貢献しよう!
(Β版非公開)