- お役立ち記事
- A must-see for managers of equipment technology departments! How to leverage reliability engineering to enhance equipment maintenance
月間76,176名の
製造業ご担当者様が閲覧しています*
*2025年3月31日現在のGoogle Analyticsのデータより
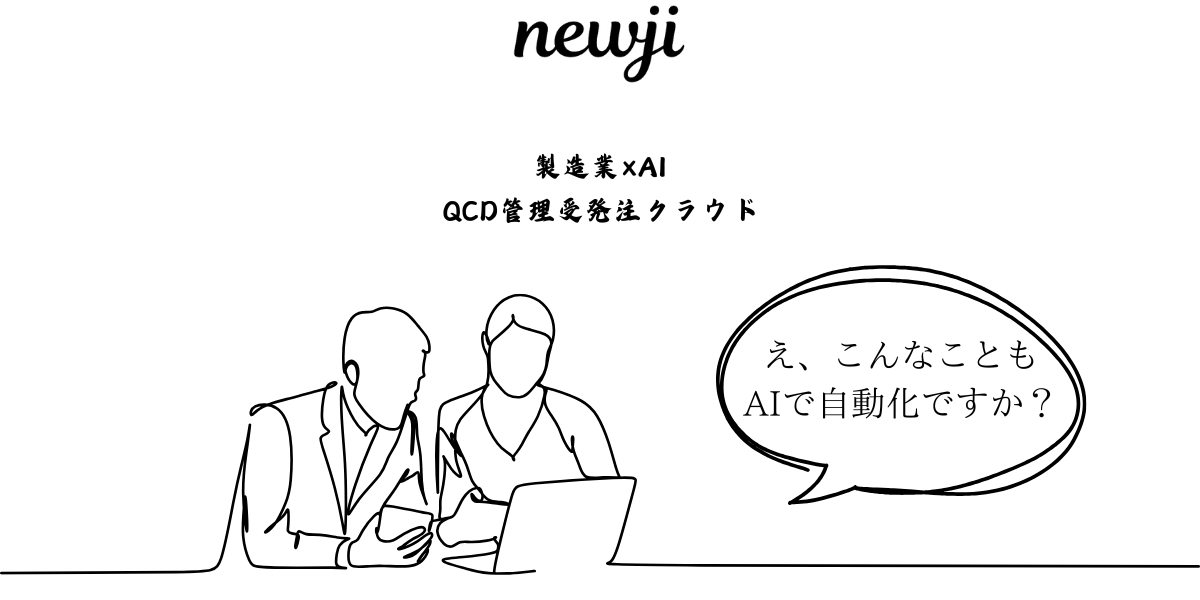
A must-see for managers of equipment technology departments! How to leverage reliability engineering to enhance equipment maintenance
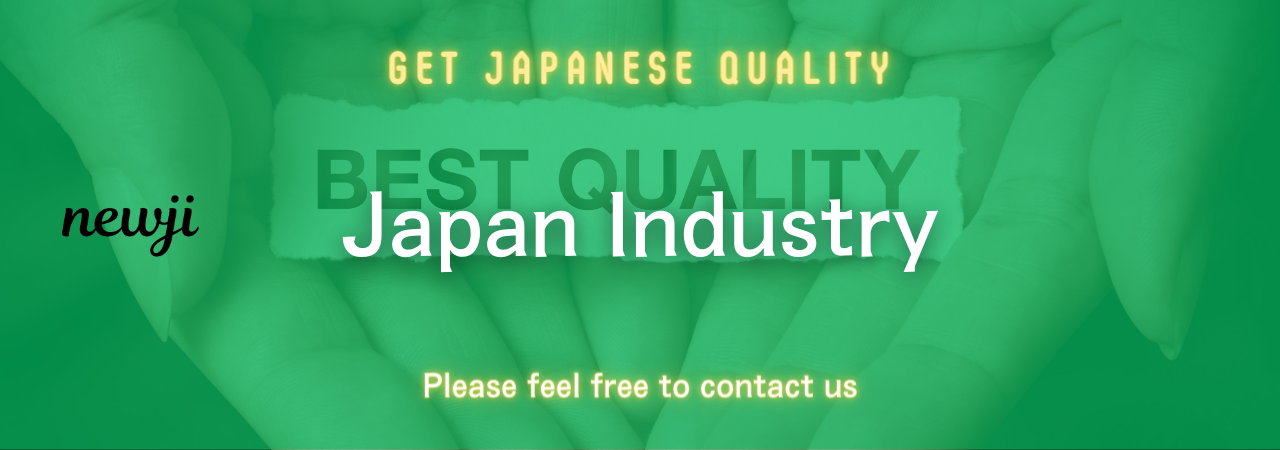
目次
Understanding Reliability Engineering
Reliability engineering is a crucial discipline within the field of engineering that focuses on ensuring that equipment and systems perform their required functions without failure for a specified period.
This engineering field plays a vital role in enhancing equipment maintenance by identifying potential failures and implementing strategies to prevent them.
By leveraging reliability engineering, managers of equipment technology departments can significantly improve the performance, safety, and cost-effectiveness of their operations.
Reliability engineering involves techniques and methodologies such as failure modes and effects analysis (FMEA), root cause analysis (RCA), and predictive maintenance.
By applying these methodologies, engineers can predict when failures might occur and what the consequences might be, allowing for proactive measures to be taken.
This prevents downtime and extends the life cycle of equipment, resulting in greater efficiency and reduced maintenance costs.
The Role of Reliability Engineering in Equipment Maintenance
The integration of reliability engineering into equipment maintenance provides numerous benefits.
One of the most significant advantages is the ability to maximize equipment uptime.
Through the predictive capabilities of reliability engineering, unexpected breakdowns can be minimized, providing a seamless operation.
Reliability engineering also enhances safety in equipment maintenance.
By understanding potential failure modes and their impacts, engineers can devise strategies to mitigate risks, ensuring that both machinery and operators remain safe.
This contributes to a safer working environment and reduces the need for corrective maintenance and repairs.
Cost savings are another significant benefit.
While investment in reliability engineering may require initial expenditures, the long-term savings achieved through reduced equipment failure, lower repair costs, and decreased downtime far outweigh the initial costs.
This approach leads to better resource allocation and optimal performance of equipment.
Implementing Reliability Engineering Practices
To effectively leverage reliability engineering in equipment maintenance, managers should focus on a few key steps:
1. Establish a Reliability-Centric Culture
Creating a culture that prioritizes reliability is essential.
Managers should encourage teams to adopt reliability-focused practices and strive for excellence in maintenance.
Training sessions and workshops can help raise awareness and build the necessary skills among staff.
2. Conduct Failure Mode and Effects Analysis (FMEA)
FMEA is a proactive tool used to identify potential failure modes, their causes, and effects.
It allows engineers to prioritize risks and implement appropriate measures to prevent failures.
By systematically analyzing potential pitfalls, managers can enhance the reliability of the equipment.
3. Implement Predictive Maintenance Techniques
Predictive maintenance involves using data and analytics to predict when maintenance should be performed.
This approach uses techniques like vibration analysis, thermography, and oil analysis to determine the optimal time for equipment servicing.
By predicting maintenance needs accurately, downtime is minimized, and costly emergency repairs are avoided.
4. Conduct Root Cause Analysis (RCA)
When failures do occur, root cause analysis helps determine the underlying reasons.
Understanding the root cause allows for long-term solutions rather than temporary fixes.
RCA is integral to reliability engineering as it ensures problems are not only resolved but also prevented in the future.
Measuring the Impact of Reliability Engineering
The success of reliability engineering practices can be measured through several key performance indicators (KPIs).
1. Equipment Uptime
One of the primary metrics is the increase in equipment uptime.
By reducing unexpected breakdowns and optimizing maintenance schedules, managers can ensure equipment is operational for longer periods.
2. Maintenance Costs
Monitoring maintenance costs is another crucial metric.
Effective reliability engineering should result in decreased maintenance expenses over time, reflecting the efficiency of the practices implemented.
3. Failure Rates
A reduction in failure rates is a direct indicator of successful reliability engineering.
Lower failure rates mean fewer disruptions and more efficient operations.
4. Safety Incidents
Tracking safety incidents can gauge the effectiveness of risk mitigation strategies developed through reliability engineering.
A decrease in safety incidents indicates an improved safety environment, benefiting both employees and operations.
Challenges in Implementing Reliability Engineering
Despite its advantages, implementing reliability engineering comes with challenges.
These challenges can include the initial cost of training and technology, resistance to change within the organization, and the requirement for specialized knowledge and skills.
To overcome these hurdles, continuous management support is crucial.
Investments in training and technology should be viewed as long-term contributions to operational excellence.
Promoting a gradual shift in culture towards a reliability-centered mindset can alleviate resistance and enhance employee buy-in.
Furthermore, collaboration with external experts or consultants can provide valuable insights and accelerate the adoption of reliability engineering practices.
Conclusion
Leveraging reliability engineering can transform equipment maintenance practices, leading to increased efficiency, safety, and cost-effectiveness.
By adopting and implementing strategies such as FMEA, predictive maintenance, and RCA, equipment technology department managers can ensure their operations are running at optimal levels.
Overcoming challenges, measuring impact through KPIs, and cultivating a reliability-centric culture are crucial steps in achieving success with reliability engineering.
By doing so, managers will not only improve the performance of their machinery but also contribute significantly to the overall productivity and profitability of their organization.
資料ダウンロード
QCD管理受発注クラウド「newji」は、受発注部門で必要なQCD管理全てを備えた、現場特化型兼クラウド型の今世紀最高の受発注管理システムとなります。
ユーザー登録
受発注業務の効率化だけでなく、システムを導入することで、コスト削減や製品・資材のステータス可視化のほか、属人化していた受発注情報の共有化による内部不正防止や統制にも役立ちます。
NEWJI DX
製造業に特化したデジタルトランスフォーメーション(DX)の実現を目指す請負開発型のコンサルティングサービスです。AI、iPaaS、および先端の技術を駆使して、製造プロセスの効率化、業務効率化、チームワーク強化、コスト削減、品質向上を実現します。このサービスは、製造業の課題を深く理解し、それに対する最適なデジタルソリューションを提供することで、企業が持続的な成長とイノベーションを達成できるようサポートします。
製造業ニュース解説
製造業、主に購買・調達部門にお勤めの方々に向けた情報を配信しております。
新任の方やベテランの方、管理職を対象とした幅広いコンテンツをご用意しております。
お問い合わせ
コストダウンが利益に直結する術だと理解していても、なかなか前に進めることができない状況。そんな時は、newjiのコストダウン自動化機能で大きく利益貢献しよう!
(β版非公開)