- お役立ち記事
- A must-see for managers of equipment technology departments! Improving equipment reliability and predicting lifespan using Weibull analysis
月間76,176名の
製造業ご担当者様が閲覧しています*
*2025年3月31日現在のGoogle Analyticsのデータより
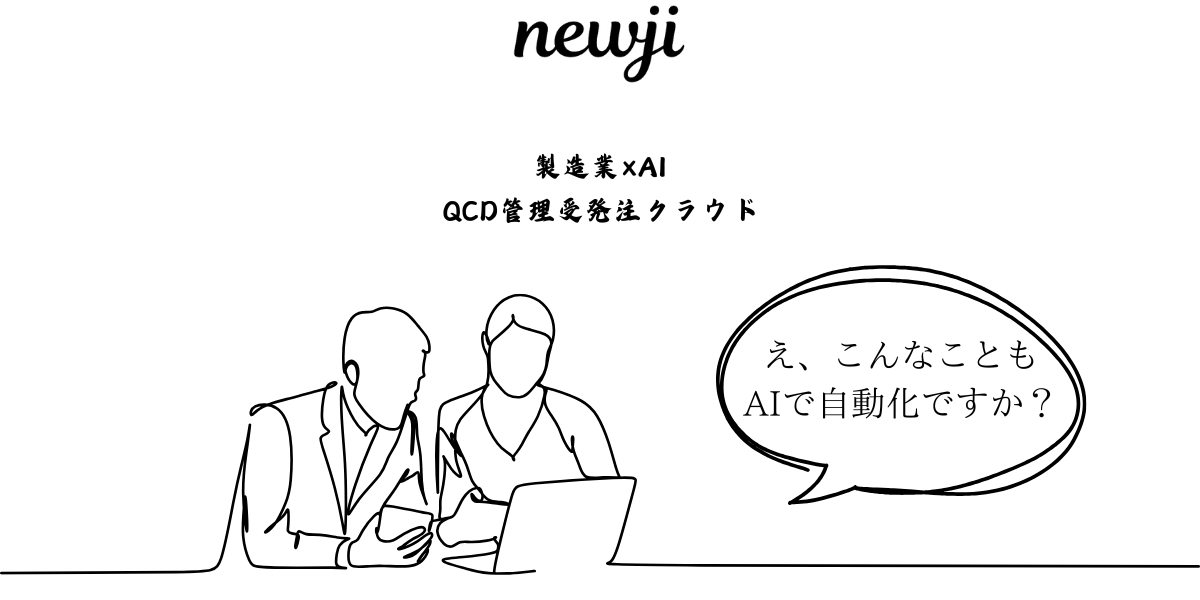
A must-see for managers of equipment technology departments! Improving equipment reliability and predicting lifespan using Weibull analysis
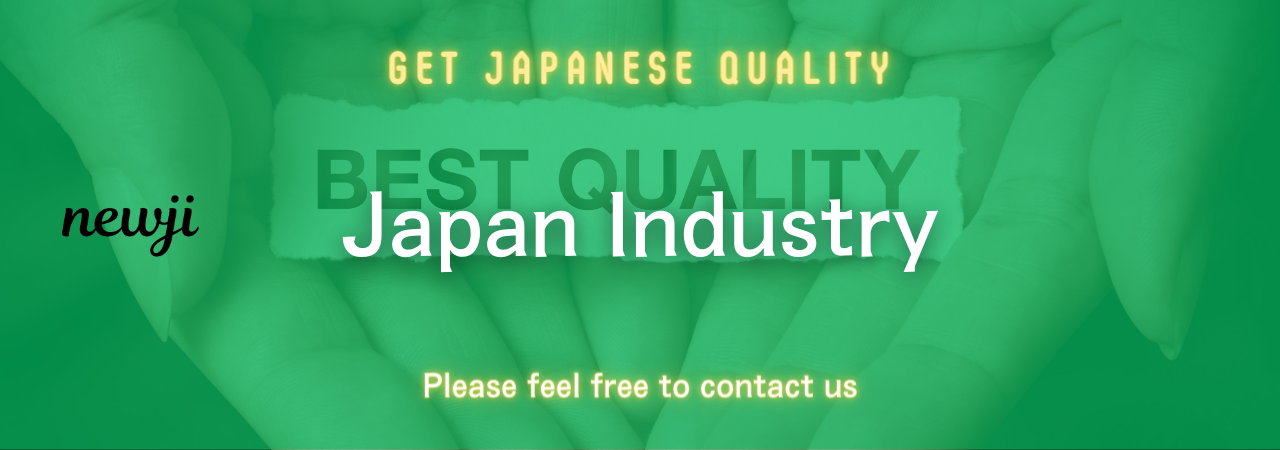
目次
Introduction to Weibull Analysis
Weibull analysis is a powerful statistical tool used to evaluate equipment reliability and predict the lifespan of machinery.
It is highly beneficial for managers in equipment technology departments aiming to enhance their maintenance strategies and ensure optimal performance.
By understanding the failure patterns and lifespan of equipment, managers can make more informed decisions on maintenance scheduling, spare parts inventory, and replacement timing.
Understanding the Weibull Distribution
The Weibull distribution is a versatile life data distribution model that can accommodate various types of failure rate conditions.
It is characterized by two parameters: the shape parameter (beta) and the scale parameter (eta).
The shape parameter (beta) helps in understanding the distribution of failures, whether they occur early in the lifecycle, randomly, or during the wear-out phase.
– When beta < 1, failures are more likely to occur in the early stages, often due to manufacturing defects or poor handling. - When beta = 1, it indicates a constant failure rate, typically seen in electronic components. - When beta > 1, failures increase over time, usually indicating wear and tear.
The scale parameter (eta) indicates the life at which 63.2% of products will have failed, providing a measure of the typical life expectancy of the equipment.
Benefits of Weibull Analysis in Equipment Management
Weibull analysis offers several benefits that are crucial for managing equipment reliability:
– **Predictive Maintenance**: By using Weibull analysis, managers can forecast when equipment is likely to fail and schedule maintenance activities beforehand. This predictive approach minimizes unplanned downtime and optimizes maintenance resources.
– **Cost Efficiency**: Predictive maintenance, supported by Weibull analysis, reduces the costs associated with emergency repairs and loss of production. It helps in budgeting for future maintenance expenses and optimizing the inventory of spare parts.
– **Informed Decision Making**: With concrete data from Weibull analysis, managers can make data-driven decisions regarding equipment replacement, upgrades, and lifecycle extension.
Steps for Conducting Weibull Analysis
Conducting Weibull analysis involves several systematic steps:
1. Data Collection
The first step is to gather historical failure data of equipment.
This data should include the time-to-failure or the cycles until failure for each unit.
Accurate data collection is paramount to the success of the analysis.
2. Data Preparation
Prepare the collected data by organizing it into a consistent format.
Ensure that you account for censored and uncensored data points.
Censoring occurs when only a portion of the unit’s lifespan is observed because the test is terminated early or the unit is still operational.
3. Parameter Estimation
Estimate the parameters (beta and eta) using statistical software or engineering tools.
Various methods, such as Maximum Likelihood Estimation (MLE) and Rank Regression, can be used to calculate these values.
The chosen method should match the nature of the collected data and the specific needs of the analysis.
4. Model Fitting
Fit the Weibull distribution model to the prepared data.
This involves ensuring that the model accurately represents the equipment’s failure behavior.
Model fitting can be validated using goodness-of-fit tests and visual inspections of plotted data points.
5. Reliability Estimation
Once the model is fitted, calculate the reliability of the equipment at various time points.
Reliability is the probability that the equipment will perform without failure over a specified period under normal operating conditions.
6. Generate Insights
Interpret the results to derive meaningful insights, facilitating maintenance strategies and decision-making processes.
Practical Application of Weibull Analysis
Imagine a manufacturing plant experiencing frequent breakdowns of its conveyor belt system.
By applying Weibull analysis, the maintenance team can determine whether these failures are random incidents or part of a larger pattern.
If the analysis shows increased failure rates as the lifespan progresses, it may indicate that the belts wear out over time, necessitating timely replacements rather than reactive repairs.
Using Results for Maintenance Strategies
– **Proactive Replacements**: Schedule component replacements before the expected wear-out period to prevent unexpected downtimes.
– **Spare Parts Management**: Plan inventory based on expected wear-out times, ensuring that critical parts are always on hand.
– **Maintenance Scheduling**: Adjust maintenance frequencies and labor allocations based on the probability of failures over time.
Challenges in Weibull Analysis
While Weibull analysis is highly beneficial, there are challenges:
– **Data Quality**: Inaccurate or incomplete failure data can lead to misleading results.
It’s crucial to ensure that data collection practices are robust and comprehensive.
– **Complexity**: Understanding and interpreting Weibull parameters may require specialized statistical knowledge.
Training or collaboration with reliability engineers may be necessary for accurate analysis.
– **Model Assumption**: The success of Weibull analysis depends on the assumption that the equipment failures follow a Weibull distribution.
In cases where failures follow a different pattern, alternative models might be more appropriate.
Conclusion
For managers in equipment technology departments, Weibull analysis represents a critical methodology for improving reliability and prolonging equipment lifespan.
By accurately predicting failures and scheduling maintenance proactively, organizations can save costs, reduce downtime, and enhance operational efficiency.
When implementing Weibull analysis, the emphasis should always be on high-quality data collection and interpretation to reap its full benefits.
資料ダウンロード
QCD管理受発注クラウド「newji」は、受発注部門で必要なQCD管理全てを備えた、現場特化型兼クラウド型の今世紀最高の受発注管理システムとなります。
ユーザー登録
受発注業務の効率化だけでなく、システムを導入することで、コスト削減や製品・資材のステータス可視化のほか、属人化していた受発注情報の共有化による内部不正防止や統制にも役立ちます。
NEWJI DX
製造業に特化したデジタルトランスフォーメーション(DX)の実現を目指す請負開発型のコンサルティングサービスです。AI、iPaaS、および先端の技術を駆使して、製造プロセスの効率化、業務効率化、チームワーク強化、コスト削減、品質向上を実現します。このサービスは、製造業の課題を深く理解し、それに対する最適なデジタルソリューションを提供することで、企業が持続的な成長とイノベーションを達成できるようサポートします。
製造業ニュース解説
製造業、主に購買・調達部門にお勤めの方々に向けた情報を配信しております。
新任の方やベテランの方、管理職を対象とした幅広いコンテンツをご用意しております。
お問い合わせ
コストダウンが利益に直結する術だと理解していても、なかなか前に進めることができない状況。そんな時は、newjiのコストダウン自動化機能で大きく利益貢献しよう!
(β版非公開)