- お役立ち記事
- A must-see for managers of process management departments in the chemical manufacturing industry! Points for effective introduction of centrifugal separation technology and trouble avoidance
月間76,176名の
製造業ご担当者様が閲覧しています*
*2025年3月31日現在のGoogle Analyticsのデータより
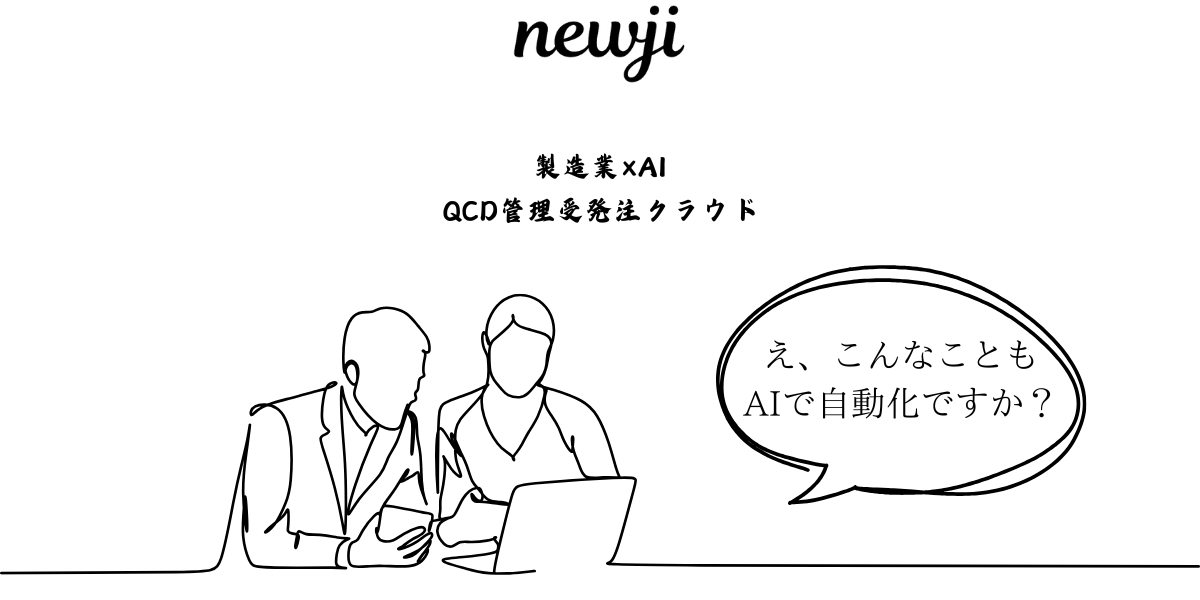
A must-see for managers of process management departments in the chemical manufacturing industry! Points for effective introduction of centrifugal separation technology and trouble avoidance
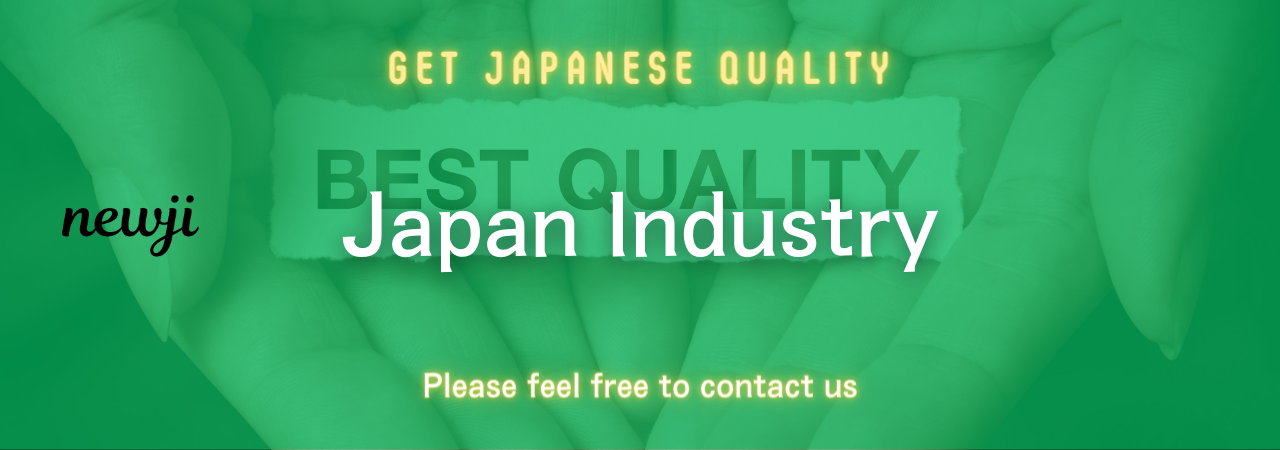
目次
Understanding Centrifugal Separation Technology
Centrifugal separation technology is a significant advancement in the chemical manufacturing industry.
By leveraging centrifugal force, this technology enables the efficient separation of components based on their densities.
This process is fundamental in ensuring the purity and quality of chemical products.
Understanding how this technology works is crucial for process management departments aiming to implement it effectively.
At its core, centrifugal separation employs a spinning motion to create a force perpendicular to the object’s axis.
This force pushes components outward, allowing the separation of materials with varying densities.
For instance, heavier particles move to the outer edges, while lighter ones remain closer to the center.
This principle is applied across various industries, particularly in chemical manufacturing, where precise separation is vital.
Implementing Centrifugal Separation Technology
For process management departments in the chemical manufacturing industry, effectively introducing centrifugal separation technology involves several critical steps.
First, it is important to have a clear understanding of the specific needs and goals of your process.
This understanding will guide you in selecting the appropriate equipment and technology that can meet these needs.
Next, consider the type and capacity of the centrifugal separators required.
Different processes may demand different types of equipment based on factors such as the volume of material, size of particles, and desired end-product quality.
Engage with equipment suppliers to discuss your specific requirements and gain insights into the available options.
Furthermore, training is essential for the personnel involved in operating and maintaining centrifugal separation equipment.
Invest in training programs to ensure that your team is well-versed in the nuances of the technology, including its operational procedures and safety protocols.
This preparedness is critical in preempting any potential issues and ensuring smooth operational flow.
Customization and Adaptation
Centrifugal separation technology is not a one-size-fits-all solution.
Customization plays a crucial role in aligning the technology with the unique demands of your processes.
Work closely with technology providers to tailor the equipment settings and configurations according to your specific process requirements.
Adaptation to changes is also vital.
Over time, changes in raw materials or production scales may necessitate adjustments in the centrifugal separation technology.
Having a flexible system that can accommodate such changes without compromising efficiency is an asset to your operational strategy.
Avoiding Common Pitfalls
While the benefits of centrifugal separation technology are immense, there are potential pitfalls that must be avoided to ensure seamless operation and product quality.
Regular Maintenance and Calibration
One of the most common areas where issues arise is in the maintenance and calibration of the equipment.
Centrifugal separators operate under high speeds and pressures, making them susceptible to wear and tear.
Regular maintenance schedules, including inspections and part replacements, are vital in preventing equipment breakdowns and extending the lifespan of the machinery.
Calibration is another essential aspect that requires attention.
Ensure that the equipment is correctly calibrated for the specific separation tasks it is intended to perform.
Inaccurate calibration can lead to inefficient separations, resulting in lower product quality and potential financial losses.
Monitoring and Control Systems
Implement advanced monitoring and control systems to observe the performance of the centrifugal separation technology in real time.
These systems can alert operators to deviations from normal operating conditions, enabling timely interventions before issues escalate.
Consider integrating automated control systems that can adjust parameters dynamically to maintain optimal performance.
Managing Feed Characteristics
The characteristics of the materials fed into the centrifugal separator significantly influence its efficiency.
Ensure that feed materials are consistent in terms of size, density, and flow rate.
Inconsistent feed characteristics can result in imbalanced separation and lower efficiency.
Develop a comprehensive plan for managing feed preparation to streamline input processes and reduce the likelihood of operational issues.
Addressing Environmental Concerns
Centrifugal separation technology, like any industrial process, may have environmental impacts.
Implement measures to address waste management and emissions resulting from the separation process.
Comply with local and international environmental regulations to minimize any adverse effects.
Consider adopting sustainable practices, such as recycling separated components or utilizing environmentally friendly solvents.
Maximizing the Benefits
Maximizing the benefits of centrifugal separation technology requires a strategic approach focused on continuous improvement and innovation.
Data-Driven Decision-Making
Leverage data analytics to monitor the performance of the centrifugal separation process continuously.
Analyzing data helps identify trends, areas for improvement, and potential issues before they manifest.
Data-driven decision-making ensures the technology’s performance is constantly optimized to meet the evolving demands of the manufacturing process.
Collaborative Efforts
Encourage collaboration between process engineers, equipment manufacturers, and technology providers.
This collaboration can lead to innovative solutions and enhancements in centrifugal separation technology.
Regularly engage in knowledge sharing and industry events to keep abreast of the latest developments and best practices.
Commitment to Quality
Ultimately, the commitment to product quality drives the successful implementation of centrifugal separation technology.
Emphasize quality control measures at every stage of the separation process to ensure that the final products meet or exceed industry standards.
Implement robust quality assurance protocols to consistently deliver top-quality chemical products to your customers.
In conclusion, the effective introduction of centrifugal separation technology in the chemical manufacturing industry hinges on understanding the technology, implementing it thoughtfully, avoiding common pitfalls, and maximizing its benefits.
By taking a strategic and comprehensive approach, process management departments can significantly enhance their operational efficiency and product quality, securing a competitive edge in the industry.
資料ダウンロード
QCD管理受発注クラウド「newji」は、受発注部門で必要なQCD管理全てを備えた、現場特化型兼クラウド型の今世紀最高の受発注管理システムとなります。
ユーザー登録
受発注業務の効率化だけでなく、システムを導入することで、コスト削減や製品・資材のステータス可視化のほか、属人化していた受発注情報の共有化による内部不正防止や統制にも役立ちます。
NEWJI DX
製造業に特化したデジタルトランスフォーメーション(DX)の実現を目指す請負開発型のコンサルティングサービスです。AI、iPaaS、および先端の技術を駆使して、製造プロセスの効率化、業務効率化、チームワーク強化、コスト削減、品質向上を実現します。このサービスは、製造業の課題を深く理解し、それに対する最適なデジタルソリューションを提供することで、企業が持続的な成長とイノベーションを達成できるようサポートします。
製造業ニュース解説
製造業、主に購買・調達部門にお勤めの方々に向けた情報を配信しております。
新任の方やベテランの方、管理職を対象とした幅広いコンテンツをご用意しております。
お問い合わせ
コストダウンが利益に直結する術だと理解していても、なかなか前に進めることができない状況。そんな時は、newjiのコストダウン自動化機能で大きく利益貢献しよう!
(β版非公開)