- お役立ち記事
- A must-see for managers of process technology departments in the semiconductor industry! Effective implementation strategy for double patterning technology
A must-see for managers of process technology departments in the semiconductor industry! Effective implementation strategy for double patterning technology
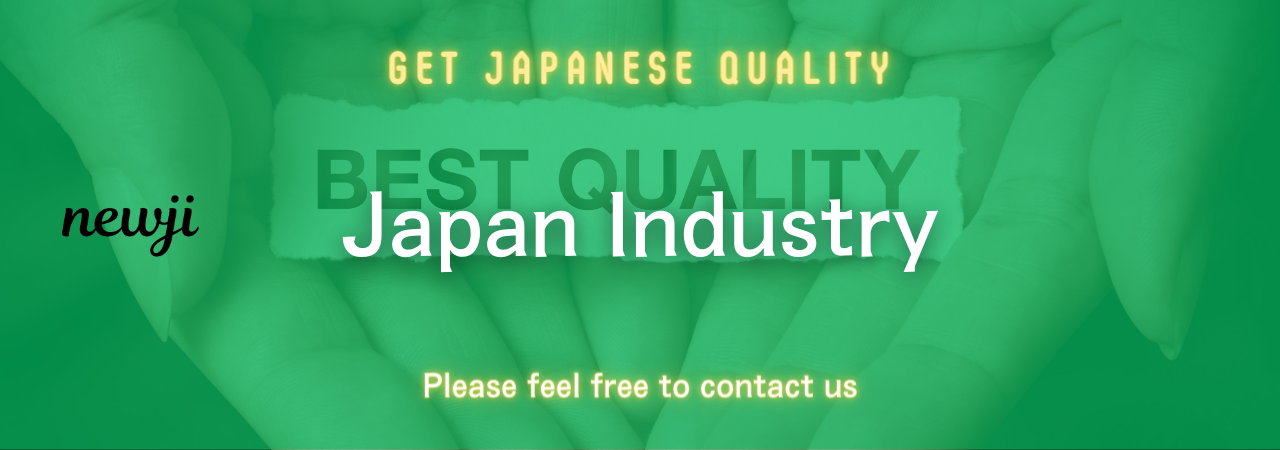
目次
Understanding Double Patterning Technology
Double patterning technology (DPT) has become a pivotal process in semiconductor manufacturing, especially as device scaling continues to push the boundaries of traditional photolithography.
In simple terms, DPT is a technique used to increase the resolution of photolithography by essentially doubling the number of patterns that can be created on a semiconductor wafer.
There are two main types of double patterning techniques: litho-etch-litho-etch (LELE) and self-aligned double patterning (SADP).
LELE involves patterning, etching, and then repeating the process to achieve finer features.
SADP, on the other hand, uses a spacer layer to define finer features between previously patterned lines.
Understanding these methods and when to use them is critical for managers in the semiconductor industry.
They need to oversee their effective implementation to meet the growing demands of smaller, faster, and more efficient chips.
Why Double Patterning Is Essential
As the semiconductor industry continues to evolve, driven by Moore’s Law, the demand for chips with smaller nodes and higher performance increases.
This necessitates finer feature creation on wafers, which traditional single patterning cannot achieve effectively on its own.
Thus, double patterning becomes essential.
DPT provides a practical approach to overcoming the limits of optical photolithography by enabling manufacturers to continue scaling down device features.
By utilizing double patterning, companies can keep up with technological advancements and maintain competitiveness in the market.
Furthermore, double patterning offers a cost-effective solution before transitioning to next-generation technologies such as extreme ultraviolet (EUV) lithography.
It serves as an interim solution, keeping the manufacturing processes efficient without a complete overhaul of existing technology.
Challenges in Implementing Double Patterning
While double patterning offers distinct advantages, its implementation comes with challenges that require strategic planning and expertise.
One of the primary challenges is the increased complexity in the manufacturing process.
Double patterning requires multiple lithography and etching steps, which can increase the potential for errors and defects.
Another concern is the alignment precision needed for the two patterning layers.
Any misalignment can lead to critical dimension variations, affecting device performance and yield.
This necessitates tighter control over the photolithography tools and processes, demanding more sophisticated equipment and skilled personnel.
Additionally, the cost factor cannot be ignored.
Though double patterning is cheaper than adopting entirely new technologies, it still incurs higher costs than traditional single patterning due to the additional process steps.
Managers need to balance these costs with the benefits of improved device performance and scaling.
Strategies for Effective Implementation
To effectively implement double patterning technology, managers should consider a strategic approach encompassing the following key steps:
1. Educate and Train Staff
It is crucial to ensure that all staff involved in the process are adequately trained and understand the intricacies of double patterning technology.
Regular workshops and training sessions can help technicians and engineers stay updated with the latest trends and challenges.
2. Invest in Advanced Equipment
Investing in cutting-edge lithography tools is vital for maintaining the precision required in double patterning processes.
State-of-the-art equipment can help manage alignment issues and ensure high yield production, justifying the initial cost with long-term benefits.
3. Collaborate with Technology Providers
Building strong partnerships with equipment and technology providers can offer significant advantages.
These collaborations can facilitate knowledge exchange and provide access to the latest innovations, helping companies stay ahead in the competitive market.
4. Monitor and Optimize Processes
Regular monitoring and optimization of manufacturing processes are essential to identify bottlenecks and areas for improvement.
Employing advanced analytical tools can provide insights into process variability and enable managers to make informed decisions for process adjustments.
5. Plan for Scalability
As technologies evolve, so should the processes that support them.
Planning for scalability ensures that the company’s infrastructure can handle future demands without major interruptions or overhauls.
Benefits of Effective Double Patterning Implementation
Implementing double patterning technology efficiently can yield several significant benefits:
Enhanced device performance through finer feature creation, leading to faster and more efficient semiconductors.
Increased competitiveness in the market by keeping up with technological advancements and consumer demands.
Better cost management by maximizing the utility of existing equipment and postponing the shift to more expensive technologies.
Improved yield and reduced defect rates through optimized processes and precise control over alignment and etching steps.
Conclusion
For managers in the semiconductor industry, the effective implementation of double patterning technology is not just a choice but a necessity.
By understanding the intricacies of this technology and navigating its challenges, managers can ensure that their companies remain competitive and continue to innovate.
Strategic planning, investment in equipment, and continuous staff training are key to leveraging the full potential of double patterning technology, leading to enhanced product performance and market success.
資料ダウンロード
QCD調達購買管理クラウド「newji」は、調達購買部門で必要なQCD管理全てを備えた、現場特化型兼クラウド型の今世紀最高の購買管理システムとなります。
ユーザー登録
調達購買業務の効率化だけでなく、システムを導入することで、コスト削減や製品・資材のステータス可視化のほか、属人化していた購買情報の共有化による内部不正防止や統制にも役立ちます。
NEWJI DX
製造業に特化したデジタルトランスフォーメーション(DX)の実現を目指す請負開発型のコンサルティングサービスです。AI、iPaaS、および先端の技術を駆使して、製造プロセスの効率化、業務効率化、チームワーク強化、コスト削減、品質向上を実現します。このサービスは、製造業の課題を深く理解し、それに対する最適なデジタルソリューションを提供することで、企業が持続的な成長とイノベーションを達成できるようサポートします。
オンライン講座
製造業、主に購買・調達部門にお勤めの方々に向けた情報を配信しております。
新任の方やベテランの方、管理職を対象とした幅広いコンテンツをご用意しております。
お問い合わせ
コストダウンが利益に直結する術だと理解していても、なかなか前に進めることができない状況。そんな時は、newjiのコストダウン自動化機能で大きく利益貢献しよう!
(Β版非公開)