- お役立ち記事
- A must-see for managers of production control departments in the steel industry! How to utilize MRP to efficiently manage raw materials
A must-see for managers of production control departments in the steel industry! How to utilize MRP to efficiently manage raw materials
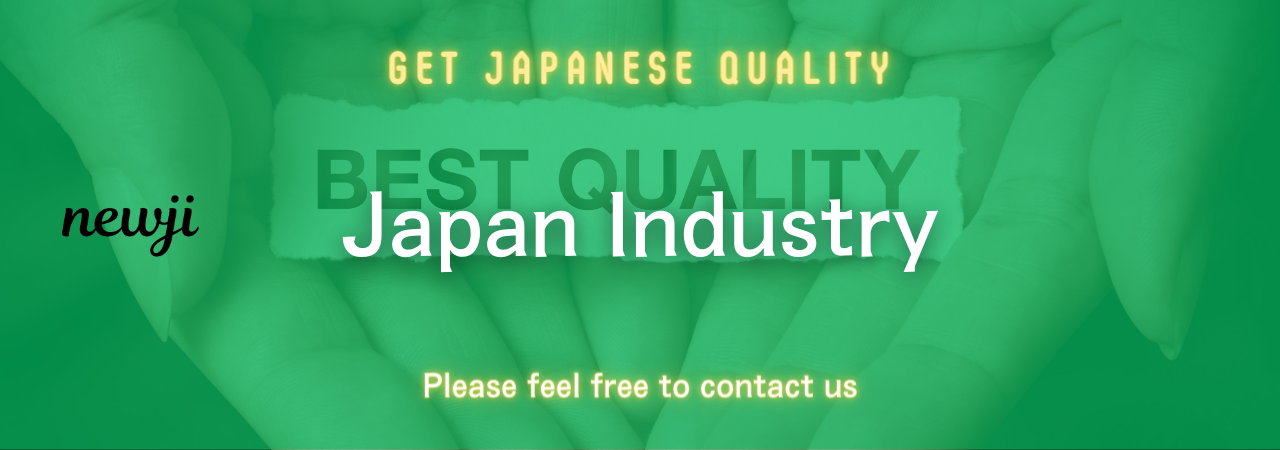
目次
Understanding MRP and Its Role in the Steel Industry
Material Requirements Planning (MRP) is an invaluable tool for the steel industry, offering a structured approach to managing raw materials efficiently.
MRP is designed to facilitate the proper scheduling and procurement of inventory, aligning production schedules with customer demands.
For production control departments in the steel industry, understanding MRP’s capability and integrating it into their processes is crucial to enhance productivity and streamline operations.
The steel industry involves complex manufacturing processes, with numerous products and by-products.
Accurate management of raw materials is therefore essential.
This is where MRP comes into play, offering systematic planning to ensure the right amount of the right materials is available at the right time.
The Components of MRP Systems
MRP systems comprise several core components that work together to optimize production control:
1. Master Production Schedule (MPS)
This element outlines the specific products to be manufactured, their quantities, and the schedule for completion.
It acts as a compass, guiding production control managers in planning and allocating resources efficiently.
2. Bill of Materials (BOM)
The BOM is a comprehensive list detailing all raw materials, components, and assemblies required for production.
In the steel industry, this includes specific grades and quantities of steel, alloys, and other materials.
Accurate BOM data is vital for minimizing material waste and ensuring production aligns with specifications.
3. Inventory Status Records
These records keep track of current inventory levels, including raw materials, work-in-progress items, and finished goods.
Properly maintained inventory records allow managers to avoid overstock or stockouts, reducing costs and optimizing storage space.
4. Material Requirements Planning (MRP) Software
With technology advancements, MRP systems have evolved into sophisticated software solutions.
They provide real-time data access and automate many planning processes.
This automation saves time and reduces human error, ensuring more accurate and reliable planning.
Benefits of MRP in Managing Raw Materials
The adoption of MRP systems in production control can bring numerous advantages for managers in the steel industry:
1. Enhanced Forecasting and Demand Planning
MRP systems offer sophisticated forecasting tools that account for historical data, market trends, and demand variations.
This functionality helps managers predict future material needs accurately, reducing unnecessary inventory build-up.
2. Improved Efficiency and Productivity
By providing a clear blueprint for production schedules and material procurement, MRP systems help minimize downtime and enhance workflow efficiency.
The systematic approach facilitates a smoother transition from materials management to actual production.
3. Cost Reduction and Waste Minimization
Effective MRP implementation reduces the risk of overproduction and material shortage, leading to lower holding costs and waste.
By knowing precisely what materials are needed and when, companies can negotiate better purchasing terms with suppliers.
4. Better Supplier and Inventory Management
An MRP system enables tighter control over supplier relationships and inventory management.
Managers can track supplier performance, ensuring timely delivery and maintaining optimal inventory levels.
5. Flexibility and Adaptability
In an industry subject to fluctuations in demand and supply chain disruptions, the flexibility offered by MRP systems is invaluable.
Managers can adjust production plans rapidly in response to changes, maintaining operational continuity.
Challenges in Implementing MRP Systems
While the benefits are significant, implementing an MRP system in the steel industry does come with its challenges:
1. Initial Setup and Costs
The adoption of an MRP system requires a substantial initial investment, both in terms of resources and time.
Training staff and aligning operations to suit the new system can be daunting for companies.
2. Data Accuracy and Integrity
The effectiveness of MRP relies heavily on data accuracy.
Inaccuracies in the MPS, BOM, or inventory records can lead to propagation of errors throughout the system.
3. Resistance to Change
Adopting new technology often meets with resistance from employees accustomed to traditional methods.
Effective change management strategies are essential for a smooth transition to an MRP system.
4. System Maintenance and Upgrades
MRP systems require regular updates to keep up with changing technology and industry standards.
Continuous maintenance ensures the system remains efficient and effective.
Strategies for Successful MRP Implementation
To overcome these challenges, production control managers can follow several strategies:
1. Strong Leadership and Vision
A clear vision and leadership are essential to guide the team through the transition process.
Management must communicate the benefits and necessity of the MRP system to all stakeholders effectively.
2. Comprehensive Training Programs
Training is vital for ensuring all team members understand how the system works and how it benefits their daily tasks.
This investment will pay off in increased efficiency and reduced implementation time.
3. Robust Data Management Practices
Implementing strict data management policies will enhance data accuracy and reliability within the MRP system.
Regular audits and cross-checks can help maintain data integrity.
4. Continuous Monitoring and Feedback
Ongoing assessment of the MRP system’s performance through regular monitoring and feedback loops will allow managers to make timely adjustments.
These ensure the system aligns with the company’s evolving needs.
In conclusion, while integrating an MRP system in the steel industry can be challenging, the benefits far outweigh the hurdles.
By focusing on proper planning, training, and stakeholder engagement, production control managers can leverage MRP systems to improve raw material management significantly.
Ultimately, MRP enhances operational efficiency, reduces costs, and allows companies to respond agilely to market demands.
資料ダウンロード
QCD調達購買管理クラウド「newji」は、調達購買部門で必要なQCD管理全てを備えた、現場特化型兼クラウド型の今世紀最高の購買管理システムとなります。
ユーザー登録
調達購買業務の効率化だけでなく、システムを導入することで、コスト削減や製品・資材のステータス可視化のほか、属人化していた購買情報の共有化による内部不正防止や統制にも役立ちます。
NEWJI DX
製造業に特化したデジタルトランスフォーメーション(DX)の実現を目指す請負開発型のコンサルティングサービスです。AI、iPaaS、および先端の技術を駆使して、製造プロセスの効率化、業務効率化、チームワーク強化、コスト削減、品質向上を実現します。このサービスは、製造業の課題を深く理解し、それに対する最適なデジタルソリューションを提供することで、企業が持続的な成長とイノベーションを達成できるようサポートします。
オンライン講座
製造業、主に購買・調達部門にお勤めの方々に向けた情報を配信しております。
新任の方やベテランの方、管理職を対象とした幅広いコンテンツをご用意しております。
お問い合わせ
コストダウンが利益に直結する術だと理解していても、なかなか前に進めることができない状況。そんな時は、newjiのコストダウン自動化機能で大きく利益貢献しよう!
(Β版非公開)