- お役立ち記事
- A must-see for managers of quality assurance departments in the auto parts industry! Success stories of quality control based on ISO9001
A must-see for managers of quality assurance departments in the auto parts industry! Success stories of quality control based on ISO9001
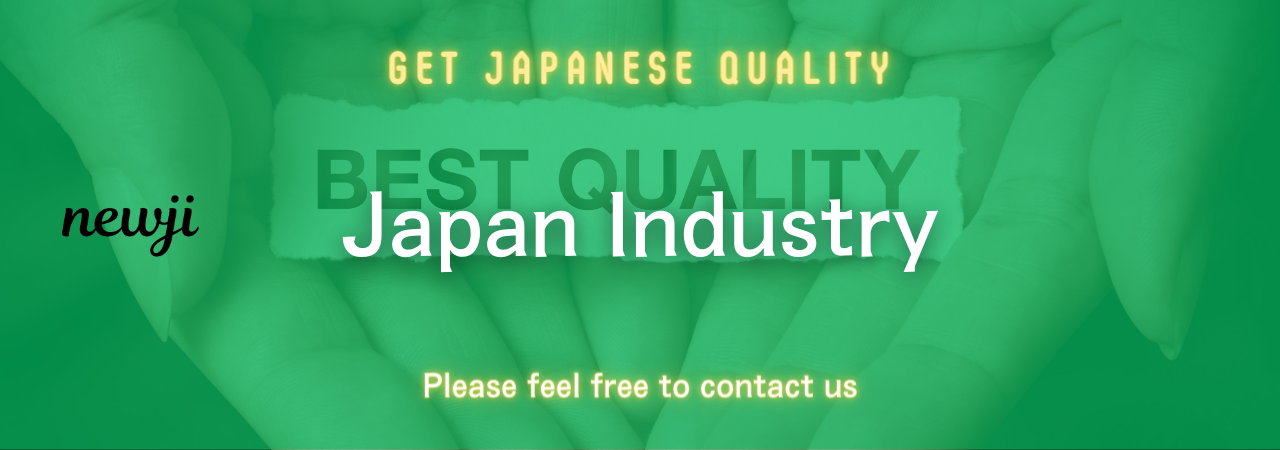
目次
Understanding ISO9001: A Foundation for Quality Control
ISO9001 is a globally recognized standard for quality management systems (QMS) that has become the cornerstone for companies aiming to ensure their products and services consistently meet customer and regulatory requirements.
For managers in the quality assurance departments of the auto parts industry, understanding and implementing ISO9001 can lead to improved business processes and enhanced product quality.
The certification provides a systematic framework that encourages consistency, reliability, and efficiency.
The Importance of ISO9001 in the Auto Parts Industry
The auto parts industry is highly competitive and demands high precision due to its direct impact on vehicle safety and performance.
Negligence in quality control can result in expensive recalls, damage to brand reputation, and, more importantly, threats to customer safety.
ISO9001 provides a robust framework that helps mitigate these risks by embedding quality control processes into the organizational culture.
Real-World Success Stories: Transforming Quality Assurance
There are numerous success stories from companies that have adopted ISO9001 as their guide to achieving a higher standard of quality control.
Let’s explore some real-world examples where this standard has made a significant impact.
Case Study: Company A’s Journey to Excellence
Company A, a leading supplier of automotive components, faced challenges with inconsistent product quality and customer complaints.
They decided to embrace ISO9001 to overhaul their quality management system.
By aligning their processes with the ISO standards, they were able to streamline their operations and ensure every part met the high-quality benchmarks required by their clients.
The first step involved a thorough gap analysis to identify areas needing improvement.
Company A then enhanced their documentation process to align with ISO9001 requirements, ensuring every procedure was clearly outlined and easily replicable.
They implemented regular training sessions, encouraging employees to understand the importance of quality control and their role in maintaining it.
The result was remarkable.
With the new system in place, Company A witnessed a 40% reduction in defects and a significant drop in customer complaints.
Their improved product quality led to increased trust among clients and boosted their market reputation.
Case Study: Company B Achieving Operational Efficiency
Company B, a mid-sized manufacturer of interior auto parts, struggled with inconsistent workflow and inefficiencies in their production line.
Seeking to rectify these issues, they adopted ISO9001 as a roadmap to refine their processes.
They began by restructuring their documentation and auditing procedures to mirror the ISO9001 framework.
This step ensured all processes were consistent with quality benchmarks and easily traceable.
Company B also focused on fostering a culture of continuous improvement.
They introduced regular team meetings to discuss updates and insights into their quality processes, involving staff at all levels.
The company established key performance indicators (KPIs) to measure the impact of changes and ensure ongoing compliance with ISO9001 standards.
These strategic adjustments resulted in a 30% reduction in production time while maintaining high-quality outputs.
The company not only enhanced their operational efficiency but also built stronger relationships with their clients, who appreciated the consistent product quality.
Implementing ISO9001 in Your Quality Control Strategy
For managers aiming to replicate such success, adopting ISO9001 requires a strategic approach.
Here are foundational steps to consider:
Conduct a Comprehensive Gap Analysis
Begin with a gap analysis to assess your current processes against ISO9001 standards.
This analysis will help identify areas needing improvement and establish a clear path for integration.
Develop Clear Documentation
Documentation is crucial in ISO9001 implementation.
Ensure that all processes, procedures, and responsibilities are well-documented.
This guarantees that everyone in the organization understands their role in maintaining quality standards.
Invest in Employee Training
Training is a vital component of implementing ISO9001.
Educate your employees about the importance of quality control and how their work impacts the overall quality management system.
Empowered employees are more likely to engage positively and contribute to a culture of quality.
Regular Audits and Reviews
To maintain ISO9001 compliance, conduct regular audits and reviews.
These assessments help ensure that processes remain aligned with standards and provide opportunities for continuous improvement.
Conclusion: The Path to Quality Assurance Excellence
The adoption of ISO9001 in quality assurance is not just a compliance exercise but a strategic move toward operational excellence and customer satisfaction.
Companies like the ones in our case studies demonstrate that when implemented effectively, ISO9001 can significantly enhance the quality of auto parts, reduce waste, and improve overall business performance.
For managers in the auto parts industry, embracing ISO9001 is a pathway to building robust quality assurance systems that protect consumers and elevate the company’s reputation.
Through structured processes and a commitment to continuous improvement, ISO9001 can transform quality control from a challenge into a story of success.
資料ダウンロード
QCD調達購買管理クラウド「newji」は、調達購買部門で必要なQCD管理全てを備えた、現場特化型兼クラウド型の今世紀最高の購買管理システムとなります。
ユーザー登録
調達購買業務の効率化だけでなく、システムを導入することで、コスト削減や製品・資材のステータス可視化のほか、属人化していた購買情報の共有化による内部不正防止や統制にも役立ちます。
NEWJI DX
製造業に特化したデジタルトランスフォーメーション(DX)の実現を目指す請負開発型のコンサルティングサービスです。AI、iPaaS、および先端の技術を駆使して、製造プロセスの効率化、業務効率化、チームワーク強化、コスト削減、品質向上を実現します。このサービスは、製造業の課題を深く理解し、それに対する最適なデジタルソリューションを提供することで、企業が持続的な成長とイノベーションを達成できるようサポートします。
オンライン講座
製造業、主に購買・調達部門にお勤めの方々に向けた情報を配信しております。
新任の方やベテランの方、管理職を対象とした幅広いコンテンツをご用意しております。
お問い合わせ
コストダウンが利益に直結する術だと理解していても、なかなか前に進めることができない状況。そんな時は、newjiのコストダウン自動化機能で大きく利益貢献しよう!
(Β版非公開)