- お役立ち記事
- A must-see for managers of quality assurance departments in the auto parts manufacturing industry! How to proceed with quality audit based on ISO9001
A must-see for managers of quality assurance departments in the auto parts manufacturing industry! How to proceed with quality audit based on ISO9001
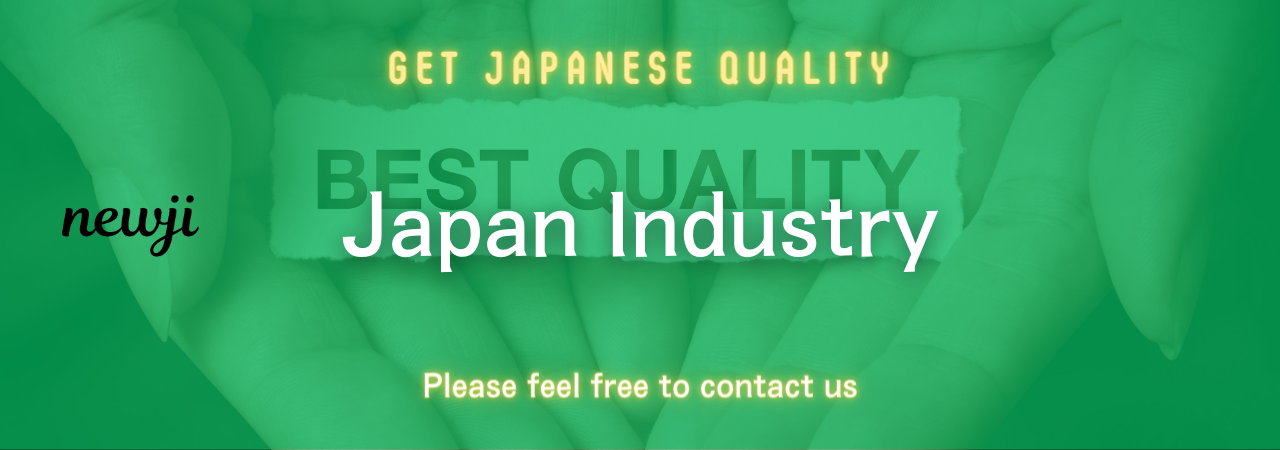
目次
Understanding ISO 9001
The ISO 9001 standard is a globally recognized framework that provides guidelines for establishing a quality management system (QMS).
It is applicable to any organization, regardless of size or industry, and is designed to help businesses ensure that they consistently meet customer and regulatory requirements.
For managers in the auto parts manufacturing industry, implementing ISO 9001 can significantly boost the quality of your products and processes.
It’s a vital tool to enhance customer satisfaction and improve overall efficiency.
Why Is a Quality Audit Important?
A quality audit is an essential exercise for any manufacturing entity.
It allows businesses to ensure that their QMS is effective and aligns with the organizational and customer demands.
For auto parts manufacturers, quality audits can help identify risks, non-conformities, and areas for improvement in production processes.
This is particularly crucial in an industry where precision and reliability are critical.
By conducting regular quality audits, managers can ensure that defects are minimized, processes are optimized, and quality assurance is upheld.
Preparing for a Quality Audit
The key to a successful quality audit lies in preparation.
This involves a thorough understanding of ISO 9001 requirements and ensuring that your company’s QMS is compliant.
First, review your existing processes and documentation.
Ensure all records are complete, accurate, and easily accessible.
Documentation should include quality policies, objectives, procedures, and work instructions.
Next, assemble a cross-functional team that includes members from various departments such as production, quality control, and supply chain.
This team should conduct an internal audit to identify any gaps or areas that require attention before the official audit.
Additionally, communication is crucial; make sure all employees understand the importance of the audit and their role in achieving compliance.
Identifying Key Areas for Review
During the audit preparation, focus on specific areas that are critical in ISO 9001 compliance for auto parts manufacturing.
These areas may include:
– **Design and Development**: Ensure that all product designs meet customer specifications and regulatory requirements.
– **Supplier Management**: Verify that suppliers are evaluated regularly and that quality criteria are established.
– **Production Control**: Check that production processes are efficient, and equipment is maintained to avoid defects.
– **Non-conformance Handling**: Confirm that there is a process in place for identifying and addressing any non-conformances.
By concentrating on these areas, you can ensure that your processes align with the requirements of ISO 9001 and industry best practices.
Conducting the Quality Audit
Once preparation is complete, it’s time to conduct the audit.
Begin the audit by reviewing documentation and process flows to verify that procedures are in place as stated in your QMS.
Conduct interviews with staff to assess their understanding of processes and their role in the quality management system.
Observations should be made in real-time to get an accurate assessment of how processes are carried out on the shop floor.
Make sure to record any observations and collect evidence of all findings.
Experienced auditors will also look beyond the checklist, identifying not just compliance but opportunities for improvements.
This value-added approach helps in continuous improvement of the QMS.
Addressing Audit Findings
Post-audit, managers should focus on addressing findings and implementing corrective actions.
For non-conformities, conduct a root cause analysis to determine underlying issues.
Develop a corrective action plan that includes responsibilities, deadlines, and methods for tracking progress.
It is crucial to quickly implement solutions to prevent recurrence and improve the QMS.
Continuous monitoring and reevaluation ensure ongoing compliance and process optimization.
Document any changes made and communicate them across the organization to build a culture of quality.
Benefits of Quality Audits
Quality audits under ISO 9001 significantly enhance the efficiency and quality of processes in the auto parts industry.
By ensuring alignment with international standards, companies can improve market competitiveness and gain customer trust.
Moreover, audits help identify cost-saving opportunities by optimizing resource use and reducing waste.
They also pave the way for more reliable and higher-quality products, reducing the risk of recalls and warranty claims.
Ultimately, regular quality audits instill a culture of continuous improvement and customer focus that benefits the entire organization.
Conclusion
For managers in the auto parts manufacturing industry, understanding and implementing ISO 9001 quality audits is imperative.
By preparing effectively and addressing audit findings, your organization can uphold the highest standards of quality assurance.
This ensures product reliability, customer satisfaction, and operational excellence in the competitive automotive industry.
Investing in a robust quality management system is not just a regulatory requirement; it’s a strategic advantage that drives business success.
資料ダウンロード
QCD調達購買管理クラウド「newji」は、調達購買部門で必要なQCD管理全てを備えた、現場特化型兼クラウド型の今世紀最高の購買管理システムとなります。
ユーザー登録
調達購買業務の効率化だけでなく、システムを導入することで、コスト削減や製品・資材のステータス可視化のほか、属人化していた購買情報の共有化による内部不正防止や統制にも役立ちます。
NEWJI DX
製造業に特化したデジタルトランスフォーメーション(DX)の実現を目指す請負開発型のコンサルティングサービスです。AI、iPaaS、および先端の技術を駆使して、製造プロセスの効率化、業務効率化、チームワーク強化、コスト削減、品質向上を実現します。このサービスは、製造業の課題を深く理解し、それに対する最適なデジタルソリューションを提供することで、企業が持続的な成長とイノベーションを達成できるようサポートします。
オンライン講座
製造業、主に購買・調達部門にお勤めの方々に向けた情報を配信しております。
新任の方やベテランの方、管理職を対象とした幅広いコンテンツをご用意しております。
お問い合わせ
コストダウンが利益に直結する術だと理解していても、なかなか前に進めることができない状況。そんな時は、newjiのコストダウン自動化機能で大きく利益貢献しよう!
(Β版非公開)