- お役立ち記事
- A must-see for managers of quality assurance departments in the pharmaceutical industry! How to thoroughly control manufacturing quality with GMP compliance
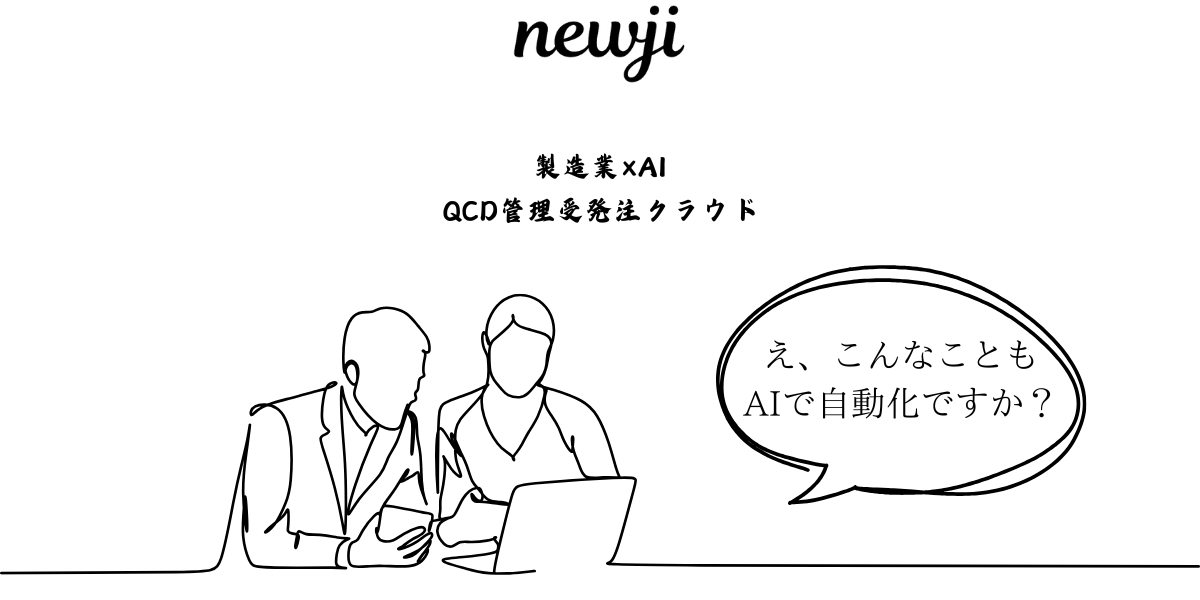
A must-see for managers of quality assurance departments in the pharmaceutical industry! How to thoroughly control manufacturing quality with GMP compliance
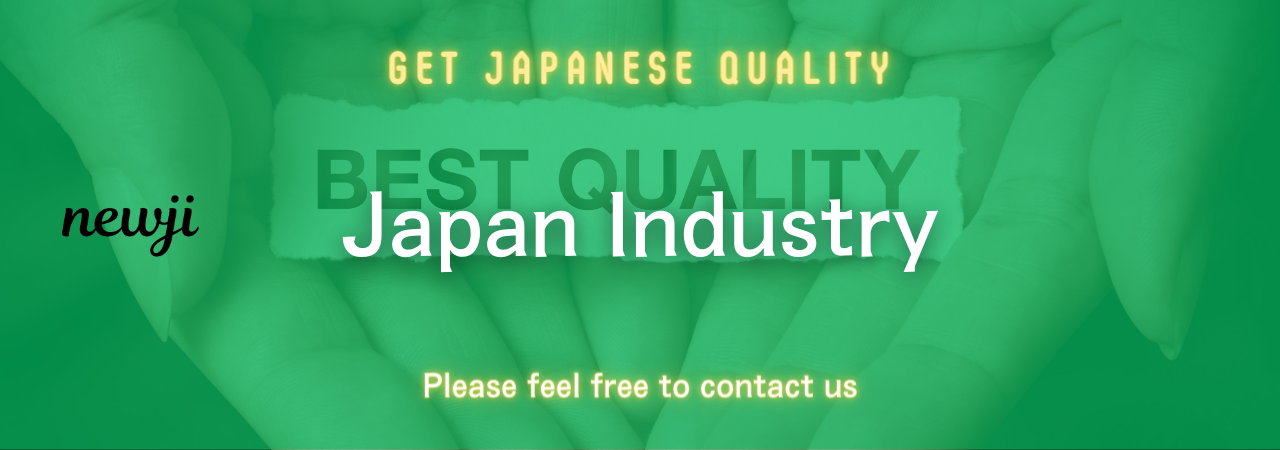
目次
Understanding GMP Compliance in Pharmaceutical Manufacturing
Good Manufacturing Practice (GMP) compliance is a critical component of quality assurance in the pharmaceutical industry.
It ensures that products are consistently produced and controlled according to quality standards.
GMP covers all aspects of production, from the starting materials to the final product delivered to consumers.
For managers overseeing quality assurance departments, mastering GMP compliance is essential to maintaining product integrity and safety.
In this article, we will explore the significance of GMP compliance and how it can be effectively implemented in pharmaceutical manufacturing.
The Importance of GMP Compliance
The pharmaceutical industry is highly regulated due to the potential impact of its products on public health.
GMP guidelines, issued by regulatory agencies like the FDA in the United States and the EMA in Europe, are designed to ensure the safety and efficacy of pharmaceutical products.
Compliance with these guidelines is mandatory and helps prevent incidents of contamination, errors in production, and inconsistencies in product quality.
GMP compliance is not just about regulatory obligation; it’s about protecting the end-user.
Quality assurance managers play a pivotal role in safeguarding the health of patients by ensuring that every product is made to the highest standards.
Strict adherence to GMP guidelines also helps in building trust with consumers and strengthens a company’s reputation in the market.
Key Components of GMP Compliance
Understanding the key components of GMP compliance is essential for effective quality assurance control.
Here are some critical aspects:
1. Quality Management System (QMS)
A well-structured Quality Management System is the backbone of GMP compliance.
QMS encompasses all operational procedures, policies, and practices to ensure product quality.
From procurement of raw materials to the final inspection of finished products, QMS ensures that all processes meet client specifications and comply with regulatory standards.
Quality assurance managers should regularly audit the QMS to identify any areas for improvement and to stay aligned with current GMP guidelines.
2. Standard Operating Procedures (SOP)
Standard Operating Procedures are detailed, written instructions to achieve uniformity in the performance of specific functions.
They are fundamental to GMP compliance, reducing variability and ensuring that each process is performed correctly.
Well-documented SOPs provide clear instructions to employees and serve as a reference for training and troubleshooting issues.
3. Training and Personnel
GMP compliance requires that all personnel are adequately trained to perform their duties.
Training programs should be thorough and ongoing, covering the latest GMP standards, safety practices, and company-specific protocols.
A competent and knowledgeable workforce is essential to maintain the quality and safety of pharmaceutical products.
4. Facility and Equipment
Facilities and equipment used in the manufacturing process must meet specific GMP requirements.
This includes ensuring proper design, construction, maintenance, and cleaning to prevent contamination and ensure consistent product quality.
Regular inspections and validations are necessary to confirm that all equipment is functioning correctly and reliably.
Implementing GMP Compliance in Manufacturing
For quality assurance managers to effectively implement GMP compliance, a strategic approach should be adopted.
Here are some steps to consider:
1. Conducting Comprehensive Risk Assessments
Risk assessment is a pivotal step in implementing GMP compliance.
It involves identifying, evaluating, and mitigating risks that could affect product quality.
By understanding potential hazards and how they can be controlled, quality assurance managers can prevent issues before they arise.
Risk assessments should be a continuous process, especially when new products, processes, or technologies are introduced.
2. Monitoring and Auditing
Regular monitoring and auditing are fundamental to maintaining GMP compliance.
These activities help to verify that the processes are being followed and that the quality management system is functioning effectively.
Internal audits can identify non-compliance areas and opportunities for enhancement, allowing proactive measures to be taken.
3. Change Control Management
In the fast-paced pharmaceutical industry, changes in processes, materials, or equipment are inevitable.
Effective change control management ensures that these changes do not negatively impact product quality or GMP compliance.
It requires formal procedures to evaluate, approve, and document any changes while assessing their potential impact on the manufacturability and quality of the product.
4. Continuous Improvement Culture
GMP compliance should be seen as a dynamic process rather than a static requirement.
Instilling a culture of continuous improvement within the organization encourages employees to seek out ways to enhance processes, minimize wastage, and improve product quality.
This proactive attitude not only ensures regulatory compliance but also enables the company to react quickly to any changes in the GMP environment.
Challenges in Maintaining GMP Compliance
Despite its importance, maintaining GMP compliance comes with its set of challenges.
Quality assurance managers need to stay vigilant and adaptable to overcome these hurdles:
1. Keeping Up with Regulatory Changes
The pharmaceutical industry is constantly evolving, and so are the regulations governing it.
Quality assurance managers must keep abreast of changes in GMP guidelines to ensure ongoing compliance.
This may require updating SOPs, retraining staff, and revising quality management practices.
2. Resource Constraints
Implementing and maintaining GMP compliance can be resource-intensive.
Limited budgets, staff, or time can hinder effective compliance efforts.
As a solution, prioritizing resources towards critical areas and employing technology, like data management systems, can streamline processes and improve efficiency.
3. Cross-department Collaboration
Achieving GMP compliance is not the sole responsibility of the quality assurance department.
It requires collaboration across various departments, such as production, procurement, and logistics.
Ensuring that everyone is aligned and understands their role is key to a successful GMP compliance program.
In conclusion, GMP compliance is integral to maintaining quality and ensuring safety in pharmaceutical manufacturing.
For quality assurance managers, thoroughly understanding and effectively implementing GMP guidelines is essential.
While challenges exist, strategic planning, continuous monitoring, and a commitment to improvement can ensure that high-quality products reach the consumers.
By doing so, pharmaceutical companies can safeguard public health, meet regulatory requirements, and build a strong reputation in the marketplace.
資料ダウンロード
QCD調達購買管理クラウド「newji」は、調達購買部門で必要なQCD管理全てを備えた、現場特化型兼クラウド型の今世紀最高の購買管理システムとなります。
ユーザー登録
調達購買業務の効率化だけでなく、システムを導入することで、コスト削減や製品・資材のステータス可視化のほか、属人化していた購買情報の共有化による内部不正防止や統制にも役立ちます。
NEWJI DX
製造業に特化したデジタルトランスフォーメーション(DX)の実現を目指す請負開発型のコンサルティングサービスです。AI、iPaaS、および先端の技術を駆使して、製造プロセスの効率化、業務効率化、チームワーク強化、コスト削減、品質向上を実現します。このサービスは、製造業の課題を深く理解し、それに対する最適なデジタルソリューションを提供することで、企業が持続的な成長とイノベーションを達成できるようサポートします。
オンライン講座
製造業、主に購買・調達部門にお勤めの方々に向けた情報を配信しております。
新任の方やベテランの方、管理職を対象とした幅広いコンテンツをご用意しております。
お問い合わせ
コストダウンが利益に直結する術だと理解していても、なかなか前に進めることができない状況。そんな時は、newjiのコストダウン自動化機能で大きく利益貢献しよう!
(Β版非公開)