- お役立ち記事
- A must-see for managers of quality assurance departments in the steel industry! How to conduct an internal audit in accordance with ISO9001
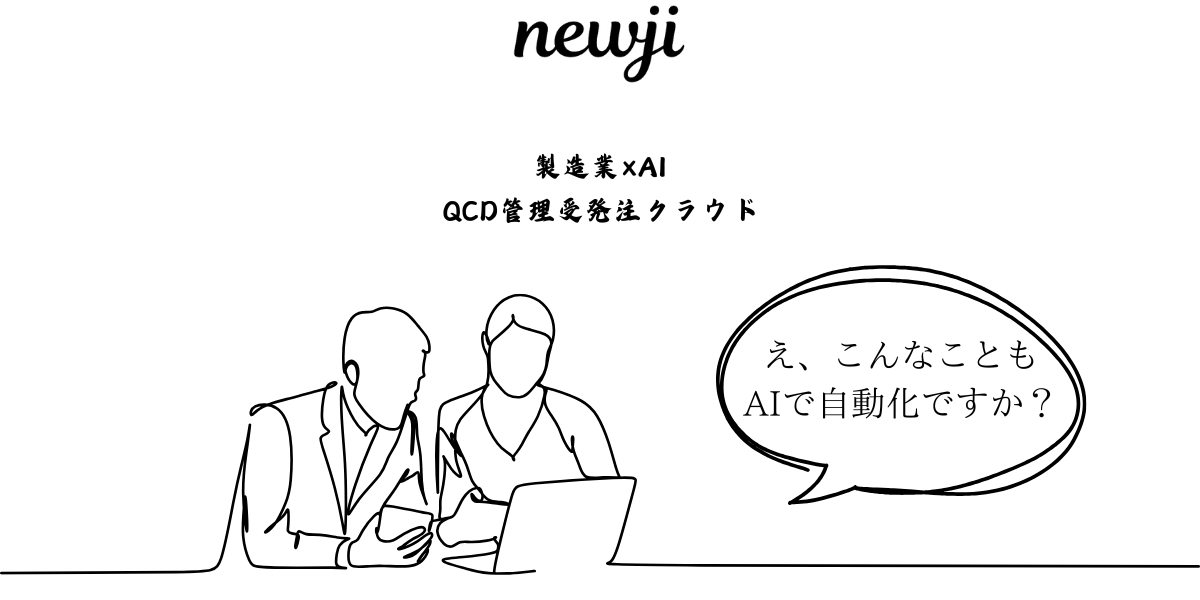
A must-see for managers of quality assurance departments in the steel industry! How to conduct an internal audit in accordance with ISO9001
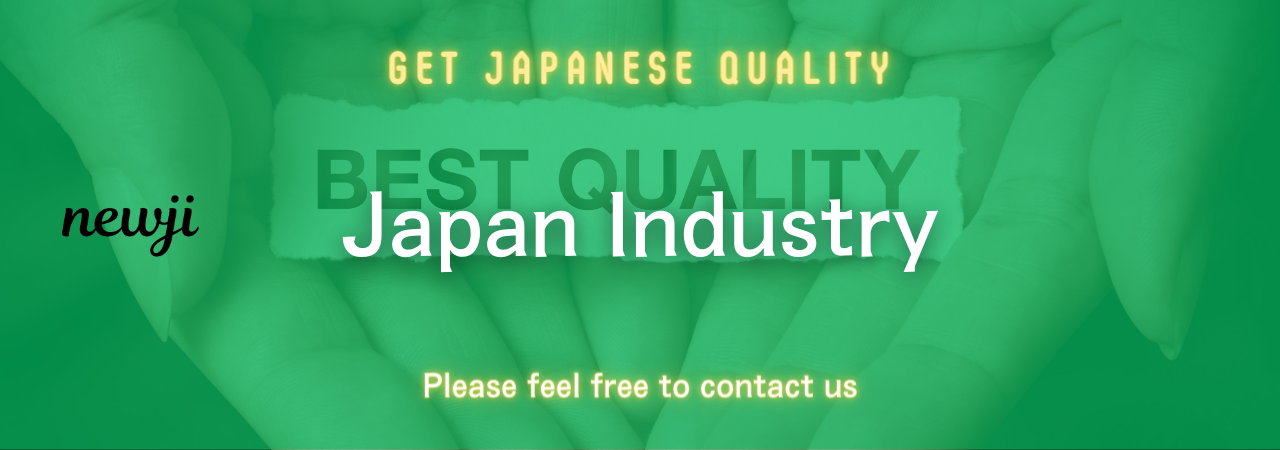
In the steel industry, quality is paramount.
With the competitiveness of the industry, maintaining a high standard of quality is a necessity.
An essential aspect of ensuring consistent quality is conducting effective internal audits in line with ISO9001 standards.
For managers of quality assurance departments, understanding how to properly conduct these internal audits is crucial for their operations and company success.
目次
Understanding ISO9001 Standards
ISO9001 is the international standard for a quality management system (QMS).
It helps organizations ensure they meet customer and other stakeholder needs within statutory and regulatory requirements.
Often emphasized in ISO9001 are a customer focus, leadership, engagement of people, process approach, improvement, evidence-based decision making, and relationship management.
These principles guide companies to create an effective quality management system.
The Role of Internal Audits
Internal audits serve as the backbone of maintaining ISO9001 standards.
They are systematic, independent, and documented processes aimed at obtaining audit evidence and evaluating it objectively.
The goal is to determine the extent to which quality management criteria are met.
Internal audits also serve to assess the effectiveness of the QMS and identify areas for improvement.
Preparing for the Internal Audit
Preparation is key when conducting an internal audit.
The first step is to clearly understand the scope and objectives of the audit.
Define what will be audited, including departments, processes, and areas to focus on.
Get to know the processes within the steel production line that are critical to quality standards and compliance.
Planning the Audit Schedule
Create a detailed audit plan and schedule.
This plan should include the audit timeline, resource allocation, and personnel involved.
Arranging these schedules and resources in advance ensures the audit proceeds smoothly and efficiently.
Training the Audit Team
A well-trained audit team is essential.
Team members should be knowledgeable about ISO9001 standards and the company’s specific processes.
Continual learning through training sessions and workshops is important to keep them up-to-date with any changes or revisions in standards.
Conducting the Audit
When executing the audit, objectivity and thoroughness should be emphasized.
Inspect the processes, check compliance with documented procedures, and collect relevant data.
Use checklists to ensure no critical aspect is overlooked.
In the steel industry, pay careful attention to the production stages, from raw material selection to the final product.
Interviewing Employees
Employee interviews can provide insights into how processes are carried out and understood at every level of the organization.
These interviews should be conducted as informal discussions so employees feel comfortable sharing their honest views on the processes.
Gathering Evidence
Collect data and records that support your findings.
Documented records of manufacturing processes, changes, and quality checks are crucial.
This evidence will be the foundation of your audit report and the basis for future improvements.
Reporting Findings
After conducting the audit, compile a detailed report presenting the findings.
This report should include areas of non-compliance, observations, and potential risks.
Lead auditors must ensure the report is objective, clear, and backed by the evidence gathered.
Communicating Findings
Once the report is prepared, communicate the findings to top management and relevant staff.
Clear communication ensures everyone understands the issues and urgency for corrective actions.
Engaging the leadership in this conversation is crucial for policy adjustments and resource allocation aimed at addressing findings.
Implementing Corrective Actions
Based on the audit findings, corrective actions should be recommended and implemented.
These actions should be aimed at addressing non-conformities and making improvements where needed.
A well-defined corrective action plan will list steps to be taken, responsible individuals, and timelines for implementation.
Monitoring and Re-evaluation
After implementing corrective actions, continuous monitoring should follow to ensure effectiveness.
Regular follow-up audits help in reassessing the measures taken and sustaining the improvements.
This cycle not only maintains but enhances quality standards over time.
Continuous Improvement
Internal audits should not just be a box-ticking exercise.
Instead, they should foster a culture of continuous improvement within the organization.
Emphasizing improvements based on findings allows for the refinement of processes, leading to better efficiency, reduced waste, and higher-quality products.
In conclusion, conducting an internal audit in alignment with ISO9001 standards is not just about compliance; it’s about improving an organization’s performance and quality output.
As a manager of quality assurance in the steel industry, mastering this process will enhance your operations and sustain the competitive edge in a demanding market.
By applying these practices, the organization can ensure that customer requirements are consistently met, and quality becomes a defining feature of the brand.
資料ダウンロード
QCD調達購買管理クラウド「newji」は、調達購買部門で必要なQCD管理全てを備えた、現場特化型兼クラウド型の今世紀最高の購買管理システムとなります。
ユーザー登録
調達購買業務の効率化だけでなく、システムを導入することで、コスト削減や製品・資材のステータス可視化のほか、属人化していた購買情報の共有化による内部不正防止や統制にも役立ちます。
NEWJI DX
製造業に特化したデジタルトランスフォーメーション(DX)の実現を目指す請負開発型のコンサルティングサービスです。AI、iPaaS、および先端の技術を駆使して、製造プロセスの効率化、業務効率化、チームワーク強化、コスト削減、品質向上を実現します。このサービスは、製造業の課題を深く理解し、それに対する最適なデジタルソリューションを提供することで、企業が持続的な成長とイノベーションを達成できるようサポートします。
オンライン講座
製造業、主に購買・調達部門にお勤めの方々に向けた情報を配信しております。
新任の方やベテランの方、管理職を対象とした幅広いコンテンツをご用意しております。
お問い合わせ
コストダウンが利益に直結する術だと理解していても、なかなか前に進めることができない状況。そんな時は、newjiのコストダウン自動化機能で大きく利益貢献しよう!
(Β版非公開)