- お役立ち記事
- A must-see for managers of quality control departments in the food processing industry! Techniques for identifying the root cause of quality problems using why-why analysis
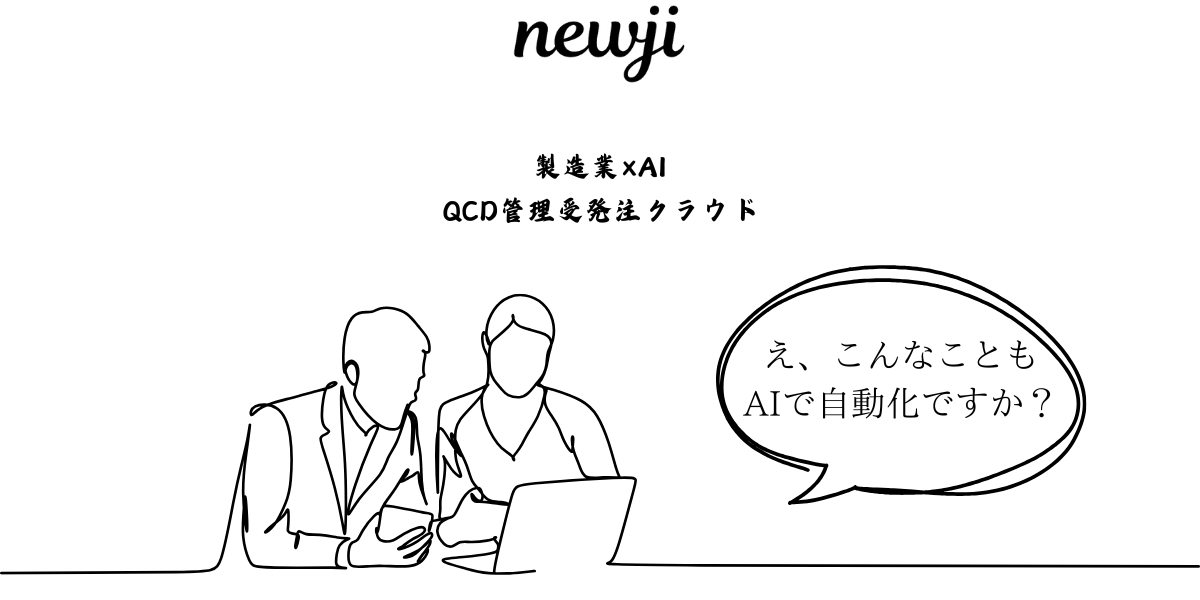
A must-see for managers of quality control departments in the food processing industry! Techniques for identifying the root cause of quality problems using why-why analysis
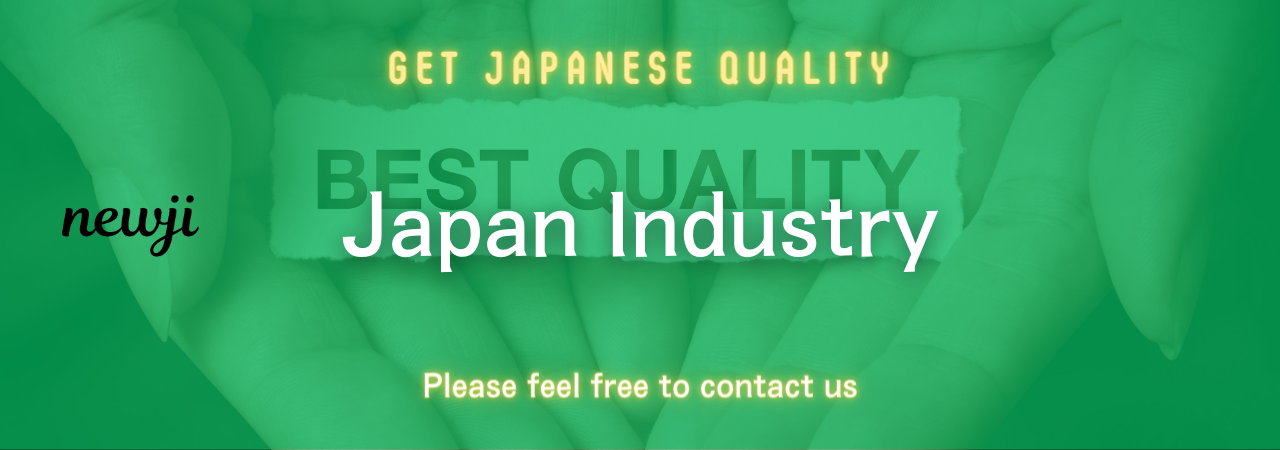
目次
Understanding Why-Why Analysis
Why-why analysis is a powerful tool used to identify the root cause of problems.
Particularly effective in the quality control sector of the food processing industry, this method shines by consistently drilling down to the core of any issue, leading to effective and sustainable solutions.
In essence, why-why analysis involves repeatedly asking the question “why” to uncover the layers of a given problem.
By doing so, managers and quality control teams can prevent recurring issues and can develop robust corrective measures.
This technique not only helps in the identification of root causes but also fosters a culture of critical thinking and problem-solving within the team.
How to Conduct a Why-Why Analysis
Using why-why analysis is both straightforward and rewarding.
Implementing this tool in your quality control processes begins with pinpointing the specific problem you aim to address.
Step 1: Clearly Define the Problem
Start by articulating the problem clearly.
In the context of food processing, this might be related to a defect in product quality, equipment malfunction, or discrepancy in processing standards.
For example, you may notice that a batch of products failed to meet safety standards.
Step 2: Ask “Why?” Multiple Times
Once the problem is defined, delve deeper by asking “why” it occurred.
Continue this process repeatedly.
Typically, five iterations are sufficient to arrive at the foundational cause.
However, this number can vary based on the complexity of the problem.
Let’s consider the problem of the failed batch.
The first “why” might uncover that the temperature during processing was not correctly maintained.
The second “why” could reveal that the temperature sensor was malfunctioning.
This process continues until the root of the problem is clearly identified.
Step 3: Document Each Response
As responses accumulate, it’s crucial to document each step of your analysis.
This record not only helps in creating accountability but also serves as a valuable reference for future problem-solving scenarios.
Step 4: Verify the Root Cause
After identifying a possible root cause, it’s important to verify its accuracy.
This involves checking data, reviewing records, and perhaps recreating the problem in a controlled environment.
In our example, re-evaluate the temperature sensor’s performance under similar conditions.
Step 5: Implement Preventative Measures
Once the root cause is verified, take corrective action to address it.
Solutions could range from replacing defective equipment to revising standard operating procedures.
The goal is to eliminate the root cause to prevent recurrence.
Additionally, put systems in place to monitor the solution’s effectiveness over time.
The Benefits of Why-Why Analysis in Quality Control
The application of why-why analysis in food processing quality control offers several benefits, making it an indispensable part of any manager’s toolkit.
Enhances Problem-Solving Skills
Engaging regularly in why-why analysis hones problem-solving skills.
The team becomes adept at anticipating potential issues and viewing problems from multiple angles, fostering a proactive approach to quality control.
Focuses on Root Causes
Instead of simply addressing symptoms, why-why analysis targets the root of problems.
This ensures that solutions are not temporary fixes but rather long-term resolutions that improve overall process integrity.
Facilitates Team Collaboration
When teams collaborate on why-why analysis, there’s a shared understanding and ownership of the problem and its solutions.
This team-based approach encourages open communication and collective learning.
Reduces Costs and Improves Efficiency
By preventing recurring issues, companies can save on costs associated with rework, waste, and compliance breaches.
Furthermore, process efficiency is improved when underlying problems are eradicated, boosting productivity.
Challenges and Considerations
Despite its effectiveness, the why-why analysis isn’t without challenges.
Being aware of potential pitfalls can enhance its application.
Time-Consuming Nature
Thoroughly performing a why-why analysis can be time-intensive, especially if several iterations are needed to drill down to a root cause.
Time management and setting priorities are crucial for balancing analysis with routine tasks.
Requires Accurate Data
The accuracy of a why-why analysis is contingent on the availability of precise data.
Ensure that data collection and management systems are reliable and up-to-date.
Avoiding Assumptions
There’s a risk of jumping to conclusions or making assumptions throughout the process.
To mitigate this, approach each “why” objectively and support findings with evidence.
Conclusion
Why-why analysis is a strategic tool that can transform quality control processes in the food processing industry.
By focusing on root causes rather than mere symptoms, managers and their teams can develop sustainable and effective solutions.
Learning and implementing this method encourages a proactive, collaborative culture where problem-solving becomes second nature.
In the rapidly evolving landscape of food processing, why-why analysis equips quality control departments with a clear pathway to continuous improvement and excellence.
資料ダウンロード
QCD調達購買管理クラウド「newji」は、調達購買部門で必要なQCD管理全てを備えた、現場特化型兼クラウド型の今世紀最高の購買管理システムとなります。
ユーザー登録
調達購買業務の効率化だけでなく、システムを導入することで、コスト削減や製品・資材のステータス可視化のほか、属人化していた購買情報の共有化による内部不正防止や統制にも役立ちます。
NEWJI DX
製造業に特化したデジタルトランスフォーメーション(DX)の実現を目指す請負開発型のコンサルティングサービスです。AI、iPaaS、および先端の技術を駆使して、製造プロセスの効率化、業務効率化、チームワーク強化、コスト削減、品質向上を実現します。このサービスは、製造業の課題を深く理解し、それに対する最適なデジタルソリューションを提供することで、企業が持続的な成長とイノベーションを達成できるようサポートします。
オンライン講座
製造業、主に購買・調達部門にお勤めの方々に向けた情報を配信しております。
新任の方やベテランの方、管理職を対象とした幅広いコンテンツをご用意しております。
お問い合わせ
コストダウンが利益に直結する術だと理解していても、なかなか前に進めることができない状況。そんな時は、newjiのコストダウン自動化機能で大きく利益貢献しよう!
(Β版非公開)