- お役立ち記事
- A must-see for new employees in the chemical plant feed pump manufacturing industry! Designed for both corrosion resistance and pressure resistance
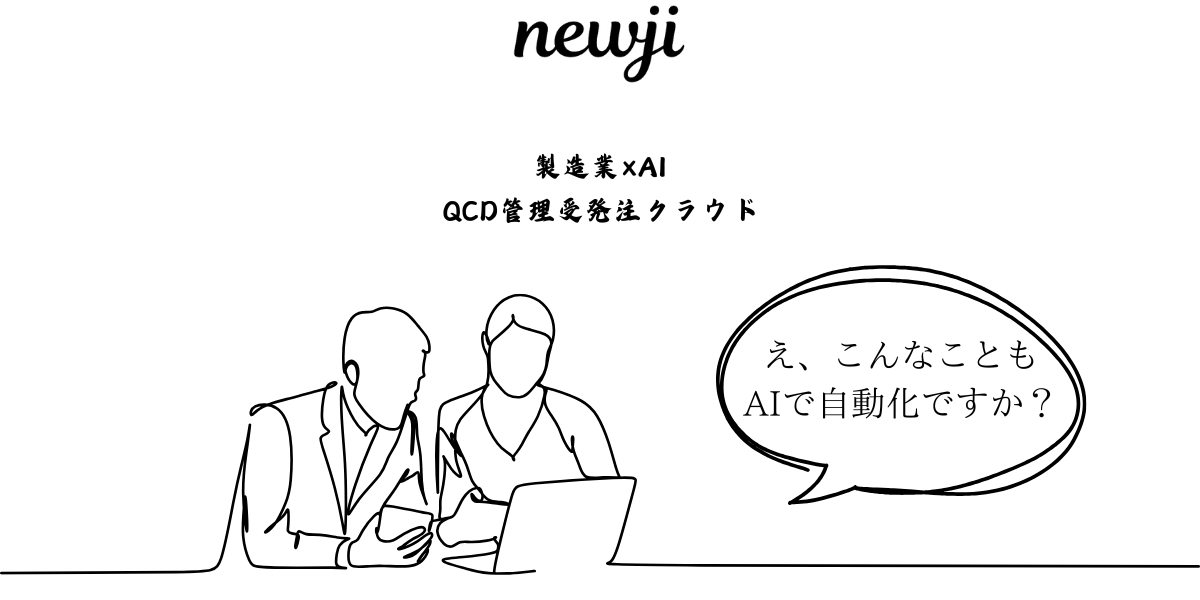
A must-see for new employees in the chemical plant feed pump manufacturing industry! Designed for both corrosion resistance and pressure resistance
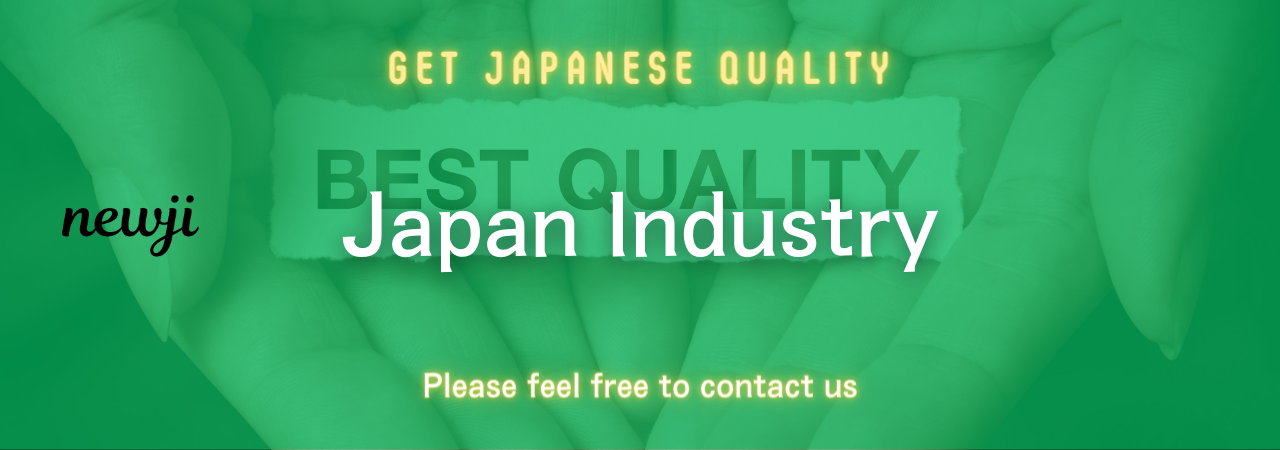
目次
Introduction to Chemical Plant Feed Pumps
Chemical plants are pivotal in numerous industries, having the critical task of transforming raw materials into valuable products.
A key component in these plants is the feed pump, which plays an essential role in maintaining efficiency and effectiveness in operations.
For new employees venturing into the feed pump manufacturing industry, understanding the importance of designing pumps with both corrosion resistance and pressure resistance is crucial.
This article serves as an introduction to these fundamental aspects, essential for success in this field.
Understanding Corrosion Resistance
Corrosion is the gradual destruction of materials, typically metals, due to chemical reactions with their environment.
In chemical plants, feed pumps are often exposed to harsh chemicals, which can lead to corrosion over time.
Corrosion resistance is, therefore, a vital feature in pump design to ensure longevity and efficient operation.
Material selection is critical in achieving corrosion resistance.
Materials such as stainless steel, titanium, and specialized polymers are commonly used due to their high resistance to corrosive substances.
Understanding the properties of these materials and their suitability for various chemicals is important for new employees in the feed pump manufacturing industry.
Coatings and linings are also employed to enhance corrosion resistance.
Innovative coatings, like epoxy and rubber linings, provide an additional layer of protection against corrosive chemicals.
For new employees, familiarizing themselves with the types of coatings available and their application techniques is beneficial.
Emphasizing Pressure Resistance
Pressure resistance refers to a pump’s ability to withstand fluids’ high pressures without failure.
Chemical processes often involve transferring fluids under substantial pressure, making pressure-resistant design a primary concern.
For a feed pump to be pressure resistant, it must be precisely designed and fabricated with appropriate materials that can endure high-pressure conditions.
New employees need to understand the importance of proper design specifications, such as wall thickness and structural integrity, to handle pressure variations effectively.
Testing and quality control are imperative for ensuring pressure resistance.
Manufacturers conduct rigorous pressure tests and inspections to verify that the pumps meet the necessary standards before deployment.
Learning about the testing protocols and quality assurance processes is valuable for those new to the industry.
The Need for Dual Resistance
While corrosion and pressure resistance can be addressed individually, the real challenge lies in developing pumps that excel in both areas simultaneously.
In many chemical processes, conditions are both corrosive and high-pressure, demanding dual-resistant solutions.
By integrating the principles of corrosion and pressure resistance, manufacturers can produce feed pumps that offer optimal performance and durability.
For new employees, grasping the concept of dual resistance is fundamental to delivering products that exceed client expectations in the chemical industry.
Design Innovations for Enhanced Performance
Recent advancements in technology have paved the way for innovative designs that enhance the durability and efficiency of feed pumps.
Employing computational fluid dynamics (CFD) in designing feed pumps allows engineers to simulate fluid flow and optimize pump geometry.
This approach leads to designs that minimize wear and enhance pressure and corrosion resistance.
Additionally, additive manufacturing, like 3D printing, enables the production of complex components with precise specifications, ideal for creating custom corrosion and pressure-resistant parts.
For new employees, understanding these technological advancements is crucial for staying competitive and innovative in the field.
Best Practices for Maintenance
Even with the best design, regular maintenance is necessary to ensure continued performance and longevity of feed pumps.
Establishing a proactive maintenance schedule can help identify signs of wear and corrosion early, preventing costly downtimes and equipment failures.
For those new to the industry, learning the basics of pump maintenance, including cleaning, inspection, and part replacement, is essential.
It’s also important to foster a culture of safety by adhering to strict safety guidelines during maintenance and operation.
Understanding safety protocols and ensuring they’re followed diligently is a responsibility new employees should prioritize in their roles.
Conclusion
Entering the feed pump manufacturing industry within chemical plants offers exciting opportunities for new employees.
Understanding the fundamental principles of corrosion and pressure resistance is key to succeeding in this field.
By grasping the importance of dual resistance, embracing innovative design technologies, and adhering to best practices for maintenance and safety, new employees can contribute significantly to producing high-quality, reliable feed pumps.
This knowledge not only enhances personal expertise but also drives the success and efficiency of chemical plant operations.
資料ダウンロード
QCD調達購買管理クラウド「newji」は、調達購買部門で必要なQCD管理全てを備えた、現場特化型兼クラウド型の今世紀最高の購買管理システムとなります。
ユーザー登録
調達購買業務の効率化だけでなく、システムを導入することで、コスト削減や製品・資材のステータス可視化のほか、属人化していた購買情報の共有化による内部不正防止や統制にも役立ちます。
NEWJI DX
製造業に特化したデジタルトランスフォーメーション(DX)の実現を目指す請負開発型のコンサルティングサービスです。AI、iPaaS、および先端の技術を駆使して、製造プロセスの効率化、業務効率化、チームワーク強化、コスト削減、品質向上を実現します。このサービスは、製造業の課題を深く理解し、それに対する最適なデジタルソリューションを提供することで、企業が持続的な成長とイノベーションを達成できるようサポートします。
オンライン講座
製造業、主に購買・調達部門にお勤めの方々に向けた情報を配信しております。
新任の方やベテランの方、管理職を対象とした幅広いコンテンツをご用意しております。
お問い合わせ
コストダウンが利益に直結する術だと理解していても、なかなか前に進めることができない状況。そんな時は、newjiのコストダウン自動化機能で大きく利益貢献しよう!
(Β版非公開)