- お役立ち記事
- A must-see for new employees in the equipment management department! Fundamentals and effective practices of TPM (total production maintenance)
A must-see for new employees in the equipment management department! Fundamentals and effective practices of TPM (total production maintenance)
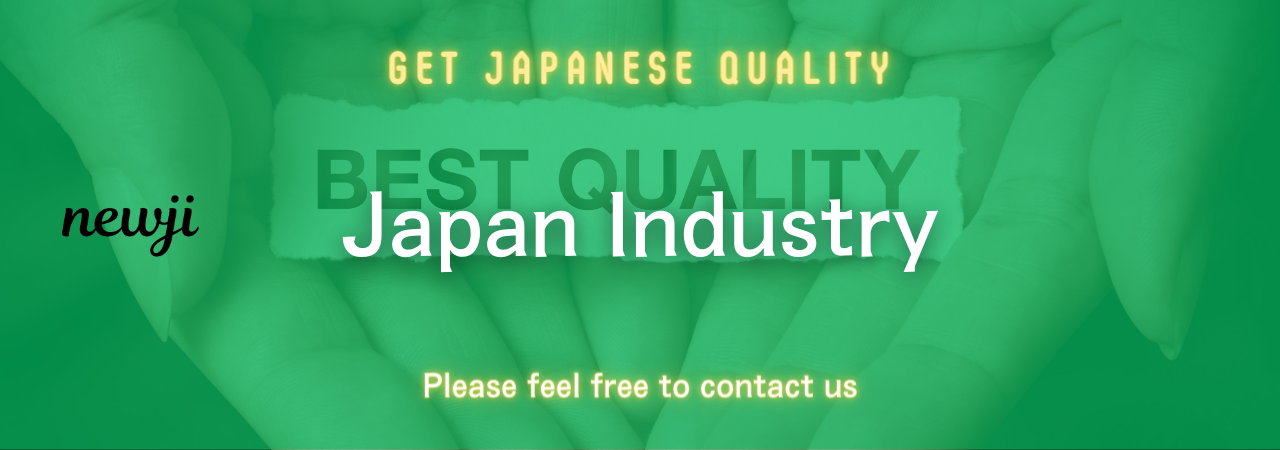
目次
Understanding the Basics of TPM
Total Productive Maintenance, commonly referred to as TPM, is an essential management system designed to optimize productivity and equipment efficiency in manufacturing industries.
It originated in Japan and has since spread globally, due to its effectiveness in fostering a productive work environment.
At its core, TPM involves every employee, ensuring that maintenance responsibilities are shared among all, not just a dedicated team.
This collective effort minimizes downtime, enhances equipment reliability, and improves overall productivity.
For newcomers to the equipment management department, grasping the basics of TPM is crucial for contributing effectively to your organization.
The Pillars of TPM
TPM is structured around eight key pillars, each focusing on specific areas for improvement.
1. **Autonomous Maintenance:** Empowers operators to manage daily maintenance tasks. This reduces machine downtime by enabling quick response to issues.
2. **Planned Maintenance:** Involves scheduling maintenance tasks during non-production hours. This proactive approach prevents unexpected breakdowns.
3. **Quality Maintenance:** Aims to maintain equipment to consistently deliver high-quality products, reducing defects and improving reliability.
4. **Focused Improvement:** Encourages small, consistent improvements. Teams identify and eliminate minor inefficiencies, leading to substantial gains over time.
5. **Early Equipment Management:** Integrates maintenance considerations into equipment design and installation, ensuring easier upkeep.
6. **Training and Education:** Emphasizes developing skills and knowledge through regular training, empowering employees to handle maintenance challenges.
7. **Safety, Health, and Environment:** Prioritizes creating a safe, healthy, and environmentally friendly workplace, aligning with TPM goals.
8. **Office TPM:** Extends TPM principles to administrative functions, promoting efficiency and waste reduction beyond production areas.
The Role of New Employees in TPM
As a new employee in the equipment management department, you play a pivotal role in implementing and maintaining TPM practices.
Your fresh perspective is invaluable for identifying opportunities for improvement.
Engaging with TPM at the ground level requires an open mind and a willingness to learn and adapt.
Here are some ways you can contribute effectively:
1. **Observation and Reporting:** Regularly monitor equipment to identify unusual patterns or potential issues. Reporting these early can prevent major disruptions.
2. **Collaboration:** Work closely with team members from different departments. Sharing insights and brainstorming together fosters innovative solutions.
3. **Knowledge Sharing:** Attend TPM training sessions and share learnings with colleagues. Collective knowledge boosts overall competency.
4. **Participate in Improvement Initiatives:** Take active part in small group improvement projects. These initiatives are excellent opportunities to contribute and learn.
Effective TPM Practices
Implementing TPM effectively requires thoughtful strategies and commitment from all levels of the organization.
Here are some best practices that can help:
Foster a Culture of Responsibility
Encourage a sense of ownership among all employees regarding equipment care.
When everyone feels responsible, maintenance becomes a shared goal, enhancing commitment and motivation.
Implement Visual Management
Use visual tools such as charts, labels, and color-coded systems to communicate equipment status and maintenance schedules.
Visual cues make it easier for everyone to stay informed and proactive.
Regular Equipment Audits
Conduct regular audits to assess equipment condition.
These evaluations help identify wear and tear, providing data for informed maintenance planning.
Leverage Technology
Utilize digital tools and software for tracking maintenance activities, scheduling, and reporting.
Technology enhances efficiency and accuracy in managing TPM processes.
Recognize and Reward Contributions
Acknowledge and reward employees who actively contribute to TPM initiatives.
Recognition boosts morale and encourages continued engagement.
Overcoming Challenges in TPM
While TPM presents numerous benefits, there can be challenges in its implementation.
Common obstacles include:
– **Resistance to Change:** Employees accustomed to traditional maintenance practices may resist new methods.
Overcome this through education, demonstrating the benefits, and involving them in the transition process.
– **Inadequate Training:** Without proper training, employees may struggle to perform maintenance tasks effectively.
Investing in comprehensive training ensures that everyone is equipped with the necessary skills.
– **Lack of Management Support:** Successful TPM relies on support from the top.
Management must be visibly committed and provide resources for TPM initiatives.
– **Time Constraints:** Balancing production demands with maintenance can be difficult.
Planning and scheduling maintenance during non-peak hours can alleviate these pressures.
The Impact of TPM on Business Success
By fostering a proactive maintenance culture, TPM leads to several tangible benefits:
– **Increased Equipment Uptime:** Efficient maintenance practices reduce unplanned downtime, ensuring continuous production.
– **Cost Efficiency:** Preventative measures decrease costly emergency repairs and extend equipment lifespan.
– **Higher Product Quality:** Consistent equipment performance leads to higher-quality outputs, boosting customer satisfaction.
– **Employee Empowerment:** Involving employees in maintenance decisions fosters a sense of empowerment and ownership, improving workplace morale.
– **Competitive Advantage:** Businesses that implement TPM effectively gain a competitive edge through improved efficiency and reduced production costs.
In conclusion, understanding and applying the principles of TPM is vital for any new employee in the equipment management department.
By focusing on collaboration, continuous improvement, and preventative maintenance, TPM ensures that equipment runs efficiently and production targets are met consistently.
Embracing TPM practices not only benefits the organization but also enhances your personal growth and contribution to your team’s success.
資料ダウンロード
QCD調達購買管理クラウド「newji」は、調達購買部門で必要なQCD管理全てを備えた、現場特化型兼クラウド型の今世紀最高の購買管理システムとなります。
ユーザー登録
調達購買業務の効率化だけでなく、システムを導入することで、コスト削減や製品・資材のステータス可視化のほか、属人化していた購買情報の共有化による内部不正防止や統制にも役立ちます。
NEWJI DX
製造業に特化したデジタルトランスフォーメーション(DX)の実現を目指す請負開発型のコンサルティングサービスです。AI、iPaaS、および先端の技術を駆使して、製造プロセスの効率化、業務効率化、チームワーク強化、コスト削減、品質向上を実現します。このサービスは、製造業の課題を深く理解し、それに対する最適なデジタルソリューションを提供することで、企業が持続的な成長とイノベーションを達成できるようサポートします。
オンライン講座
製造業、主に購買・調達部門にお勤めの方々に向けた情報を配信しております。
新任の方やベテランの方、管理職を対象とした幅広いコンテンツをご用意しております。
お問い合わせ
コストダウンが利益に直結する術だと理解していても、なかなか前に進めることができない状況。そんな時は、newjiのコストダウン自動化機能で大きく利益貢献しよう!
(Β版非公開)