- お役立ち記事
- A must-see for new employees in the equipment management department! Fundamentals of reliability engineering and equipment lifecycle management
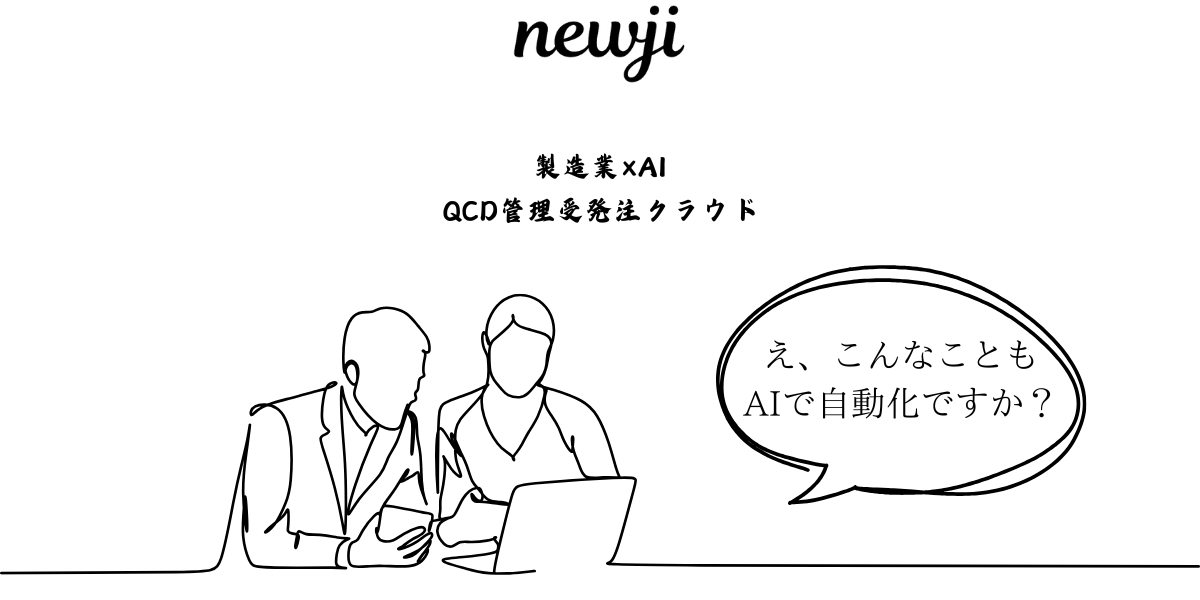
A must-see for new employees in the equipment management department! Fundamentals of reliability engineering and equipment lifecycle management
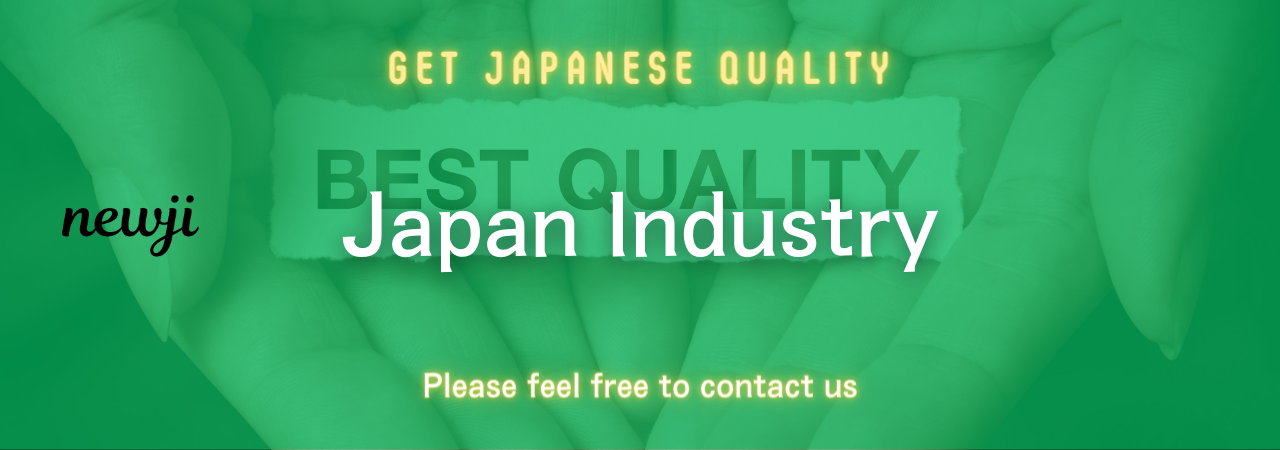
目次
Understanding Reliability Engineering
Reliability engineering is a crucial concept for anyone working in equipment management, especially for new employees.
At its core, reliability engineering is about ensuring that equipment performs its required functions under stated conditions for a specified period.
By focusing on the reliability of equipment, organizations can minimize downtime, reduce maintenance costs, and improve overall productivity.
New employees should recognize that the reliability of equipment is not just about how long it lasts but also about how well it performs during its lifecycle.
Reliability is measured through various metrics, such as mean time to failure (MTTF) and mean time between failures (MTBF).
Understanding these metrics will allow new employees to assess equipment performance effectively and make informed decisions regarding maintenance strategies.
Key Principles of Reliability Engineering
One of the key principles of reliability engineering is proactive maintenance.
Reactive maintenance, which involves fixing things after they break, can be costly and disruptive.
Instead, reliability engineering emphasizes predictive and preventive maintenance strategies.
Predictive maintenance involves using data and analytics to foresee potential failures, allowing for maintenance to be conducted at the optimal times.
Preventive maintenance, on the other hand, is about regularly scheduled maintenance tasks that are performed to keep equipment running smoothly.
Another crucial aspect of reliability engineering is root cause analysis.
When equipment fails, it’s important not only to repair it but also to understand why it failed in the first place.
Root cause analysis helps identify underlying issues that may cause repeated failures.
By addressing these root causes, organizations can prevent future downtime and extend the lifecycle of their equipment.
The Equipment Lifecycle Management Process
The equipment lifecycle encompasses every phase that an asset goes through—from acquisition to disposal.
Lifecycle management is about optimizing the use of equipment throughout each of these phases to extend its useful life and maximize return on investment (ROI).
Stages of Equipment Lifecycle
1. **Acquisition**:
The first stage involves selecting and acquiring the right equipment.
Decisions made during this phase can significantly impact future equipment performance and costs.
It’s essential to evaluate equipment based on its reliability, suitability, and long-term costs.
2. **Operation**:
Once equipment is acquired, the next phase is operation.
This is where equipment is put to use according to its designed purpose.
Proper operation includes training staff, following usage guidelines, and monitoring performance.
3. **Maintenance**:
Ongoing maintenance is crucial to extend equipment life.
During this phase, tasks such as routine checks, repairs, and upgrades are performed.
Effective maintenance reduces the likelihood of unexpected breakdowns and prolongs equipment efficiency.
4. **Retirement and Disposal**:
When equipment can no longer perform efficiently or costs too much to maintain, it enters the retirement phase.
Disposal involves removing the equipment from service, either through resale, recycling, or disposal in an environmentally friendly manner.
Importance of Equipment Lifecycle Management
Lifecycle management is essential because it enables organizations to make strategic decisions about when to replace equipment, ensuring that they do so at the most cost-effective time.
By tracking lifecycle costs, organizations can avoid reactive purchasing and instead plan for replacements ahead of time.
Moreover, lifecycle management fosters sustainability.
By managing equipment life accurately and efficiently, organizations can decrease their environmental footprint.
Choosing more durable or recyclable materials and properly maintaining equipment extends the life of assets and minimizes waste.
Bridging Reliability Engineering and Lifecycle Management
For new employees in the equipment management department, understanding both reliability engineering and lifecycle management can provide a solid foundation for effective asset management.
By integrating reliability engineering into the lifecycle management process, companies can enhance their equipment’s performance and longevity.
This integration is achieved by adopting reliability-centered maintenance, which focuses on identifying the most effective maintenance approach for each piece of equipment.
Furthermore, reliability engineering tools, such as failure mode and effect analysis (FMEA), can be applied throughout the equipment’s lifecycle to anticipate and mitigate potential problems.
These tools enable teams to prioritize maintenance activities based on their impact on equipment reliability, ensuring resources are used efficiently.
Conclusion
For new employees in the equipment management department, grasping the fundamentals of reliability engineering and lifecycle management is a must.
These concepts are interrelated and crucial for maintaining equipment performance while optimizing costs.
Remember, effective equipment management not only reduces downtime and maintenance expenses but also contributes to the overall sustainability goals of the organization.
Embracing these principles will equip new employees with the knowledge necessary to excel in their roles and make informed decisions that positively impact their company’s bottom line.
資料ダウンロード
QCD調達購買管理クラウド「newji」は、調達購買部門で必要なQCD管理全てを備えた、現場特化型兼クラウド型の今世紀最高の購買管理システムとなります。
ユーザー登録
調達購買業務の効率化だけでなく、システムを導入することで、コスト削減や製品・資材のステータス可視化のほか、属人化していた購買情報の共有化による内部不正防止や統制にも役立ちます。
NEWJI DX
製造業に特化したデジタルトランスフォーメーション(DX)の実現を目指す請負開発型のコンサルティングサービスです。AI、iPaaS、および先端の技術を駆使して、製造プロセスの効率化、業務効率化、チームワーク強化、コスト削減、品質向上を実現します。このサービスは、製造業の課題を深く理解し、それに対する最適なデジタルソリューションを提供することで、企業が持続的な成長とイノベーションを達成できるようサポートします。
オンライン講座
製造業、主に購買・調達部門にお勤めの方々に向けた情報を配信しております。
新任の方やベテランの方、管理職を対象とした幅広いコンテンツをご用意しております。
お問い合わせ
コストダウンが利益に直結する術だと理解していても、なかなか前に進めることができない状況。そんな時は、newjiのコストダウン自動化機能で大きく利益貢献しよう!
(Β版非公開)