- お役立ち記事
- A must-see for new employees in the equipment technology department! Fundamentals and practices for maximizing equipment reliability through TPM activities
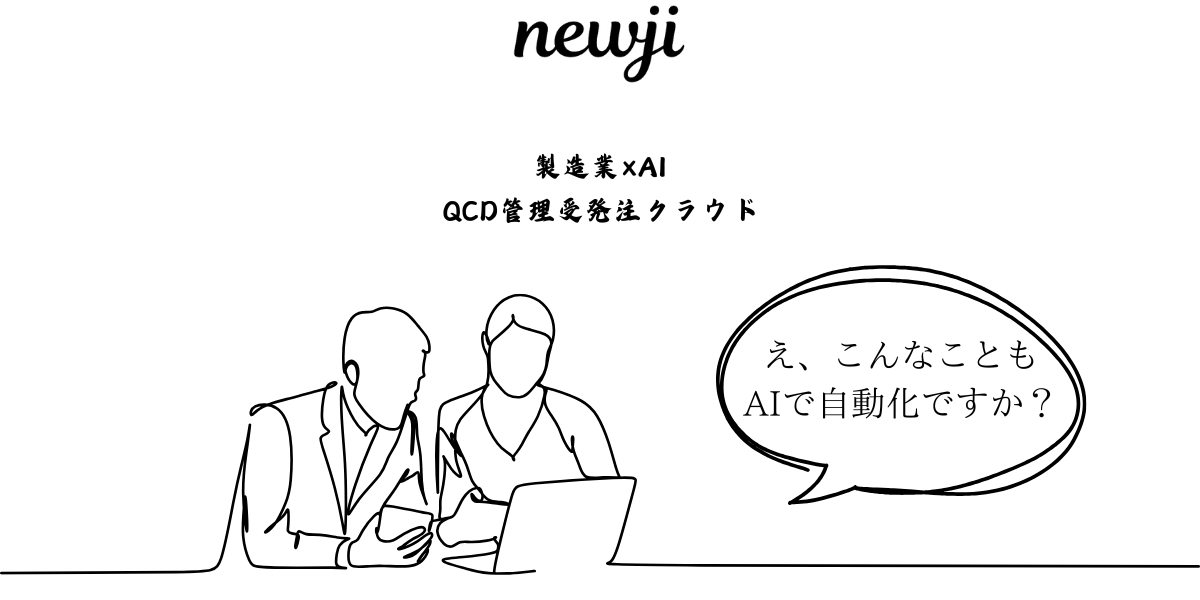
A must-see for new employees in the equipment technology department! Fundamentals and practices for maximizing equipment reliability through TPM activities
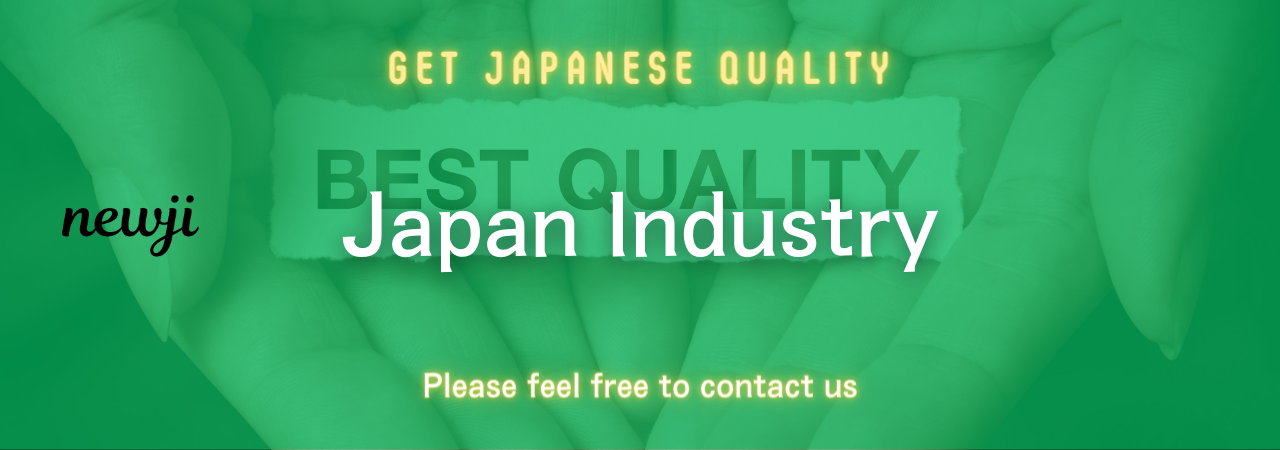
目次
Understanding Equipment Reliability
In the realm of equipment technology, one of the most critical aspects for any new employee to grasp is equipment reliability.
Ensuring that machinery operates smoothly and consistently without frequent breakdowns is pivotal.
This not only minimizes downtime but also boosts productivity and efficiency within the company.
A reliable system means less time and resources spent on repairs, which can significantly impact a company’s bottom line.
Equipment reliability can be understood as the probability that a machine will perform its intended function without failure over a specified period.
This concept is often emphasized in industries such as manufacturing, where continuous operation is crucial.
As a new employee, learning to maximize equipment reliability is imperative for your personal success and the company’s prosperity.
The Fundamentals of TPM
Total Productive Maintenance (TPM) plays a fundamental role in achieving equipment reliability.
TPM is a proactive approach that involves everyone in the organization, from machine operators to top management, in maintaining and improving equipment.
The goal is to increase production while promoting workplace safety and quality assurance.
TPM is rooted in several pillars, including autonomous maintenance, planned maintenance, and quality maintenance.
Understanding these pillars helps in laying the groundwork for effective TPM activities within your department.
With autonomous maintenance, operators take responsibility for maintaining their equipment, fostering a sense of ownership and pride.
Planned maintenance involves scheduling regular checks to prevent unexpected failures.
Quality maintenance focuses on integrating quality management into every phase of production to ensure machines run smoothly.
Autonomous Maintenance
Autonomous maintenance is a key component of TPM encouraging operators to perform routine checks and simple maintenance tasks.
By promoting awareness and knowledge among operators, companies can significantly enhance equipment reliability.
This process involves the cleaning and inspection of machinery, allowing operators to detect and report any irregularities early on.
These small, proactive steps can prevent significant issues, reducing breakdowns and improving the overall lifespan of the equipment.
As a new employee, embracing autonomous maintenance means taking initiative.
Learn about the machinery you work with, understand its working parts, and maintain a keen eye for any signs of wear and tear.
Planned Maintenance
Planned maintenance is another foundational aspect of TPM, which involves scheduling maintenance tasks systematically.
The practice relies on data analysis and historical reports to predict and prevent potential equipment failures before they occur.
By scheduling maintenance activities during downtime or non-peak hours, companies can limit the disruption to production schedules.
Collaborating closely with maintenance teams to track machine performance, downtime, and past issues is vital.
This knowledge enables new employees to contribute effectively to maintenance strategies, ensuring machinery is always in optimal working condition.
Quality Maintenance
Quality maintenance integrates quality assurance into TPM, ensuring that equipment consistently performs to specified technical standards.
This process involves regular monitoring and inspection, utilizing technology and calibration tools to assess equipment conditions.
By ensuring that every process meets quality requirements, companies can avoid defects and unnecessary wear on machinery.
For a new employee, understanding quality maintenance involves learning the benchmarks your equipment must adhere to.
Familiarize yourself with inspection tools and procedures, and always follow the predefined standards for machine operations.
Practices for Maximizing Equipment Reliability
Maximizing equipment reliability involves a combination of adopting TPM strategies and implementing best practices in everyday operations.
The following are some essential practices that can help enhance equipment reliability in your department.
Regular Training and Development
Consistent training and development are crucial to ensuring that all team members are well-versed in equipment handling and maintenance.
This ongoing education helps employees stay updated on the latest technology and methods for equipment care.
Training programs should be thorough, hands-on, and tailored to meet the equipment and technology used within the company.
As a new employee, actively seek opportunities to learn from experienced colleagues and attend training sessions.
Stay curious, ask questions, and strive to improve your understanding of equipment management.
Effective Communication and Reporting
Clear communication channels can significantly enhance the reliability of equipment.
Encouraging team members to report any observed issues or irregularities immediately helps create a responsive maintenance culture.
Regular meetings between operators, maintenance staff, and management ensure everyone is on the same page regarding equipment status and needs.
As a newcomer, being proactive in communication is imperative.
Document and share observations promptly to contribute to a seamless flow of information and quick resolutions for any emerging issues.
Innovating with Technology
Leveraging technology is a powerful tool for improving equipment reliability.
Incorporating predictive maintenance tools, IoT sensors, and data analytics can provide real-time monitoring and insights into equipment health.
These technologies can predict when machinery may require maintenance, allowing for interventions before a minor issue turns into a major problem.
Showing interest in these advanced technologies and understanding how they impact machinery performance can position you as a valuable asset to your team.
Stay informed about the latest technological advancements and consider their potential applications within your department.
Conclusion
Understanding the fundamentals of equipment reliability and TPM practices is essential for new employees to thrive in the equipment technology department.
By embracing autonomous maintenance, planned maintenance, and quality maintenance, you can contribute to maximizing equipment uptime and productivity.
Adopting best practices in training, communication, and technology ensures that your approach to equipment reliability is proactive and robust.
Incorporating these methods into your daily routine will not only enhance machinery performance but also foster a culture of continuous improvement and efficiency within your organization.
As a new member of the team, your commitment to these principles will significantly impact your career and the company’s success.
資料ダウンロード
QCD調達購買管理クラウド「newji」は、調達購買部門で必要なQCD管理全てを備えた、現場特化型兼クラウド型の今世紀最高の購買管理システムとなります。
ユーザー登録
調達購買業務の効率化だけでなく、システムを導入することで、コスト削減や製品・資材のステータス可視化のほか、属人化していた購買情報の共有化による内部不正防止や統制にも役立ちます。
NEWJI DX
製造業に特化したデジタルトランスフォーメーション(DX)の実現を目指す請負開発型のコンサルティングサービスです。AI、iPaaS、および先端の技術を駆使して、製造プロセスの効率化、業務効率化、チームワーク強化、コスト削減、品質向上を実現します。このサービスは、製造業の課題を深く理解し、それに対する最適なデジタルソリューションを提供することで、企業が持続的な成長とイノベーションを達成できるようサポートします。
オンライン講座
製造業、主に購買・調達部門にお勤めの方々に向けた情報を配信しております。
新任の方やベテランの方、管理職を対象とした幅広いコンテンツをご用意しております。
お問い合わせ
コストダウンが利益に直結する術だと理解していても、なかなか前に進めることができない状況。そんな時は、newjiのコストダウン自動化機能で大きく利益貢献しよう!
(Β版非公開)