- お役立ち記事
- A must-see for new employees in the manufacturing department! How to organize your workplace and increase efficiency with 5S activities
A must-see for new employees in the manufacturing department! How to organize your workplace and increase efficiency with 5S activities
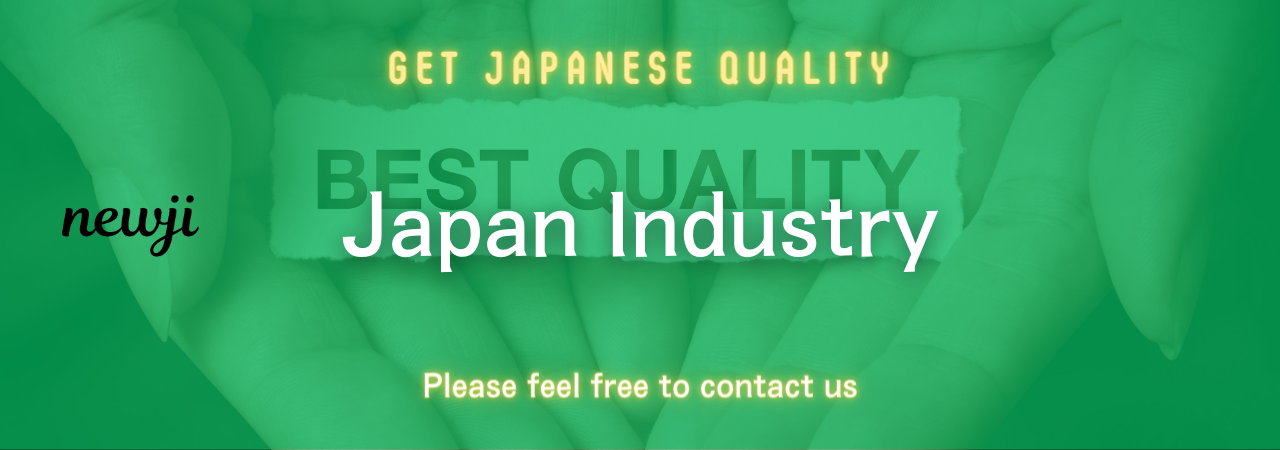
目次
Understanding 5S in the Workplace
Starting a new job can be both exciting and challenging, especially in the manufacturing department where efficiency is key.
To help new employees acclimate and succeed, the 5S methodology offers a structured approach to organizing the workplace.
The 5S system is a lean manufacturing technique that encompasses five Japanese words: Seiri, Seiton, Seiso, Seiketsu, and Shitsuke.
Translated to English, they mean Sort, Set in order, Shine, Standardize, and Sustain.
Let’s dive into each of these components and understand how they can transform your workspace into a more efficient and productive environment.
1. Sort (Seiri)
The first “S” in 5S stands for Sort, which involves separating essential items from non-essential ones in your workplace.
Focus on keeping only what’s necessary for daily operations.
By doing this, you eliminate clutter and create more space.
Start by categorizing tools, equipment, and materials.
Items that are rarely used should either be stored away from the immediate workspace or discarded if they are no longer needed.
This step not only tidies up your area but also enhances focus by minimizing distractions.
2. Set in Order (Seiton)
The second “S” revolves around organizing and arranging items for maximum efficiency.
Once you have sorted your tools and materials, it’s time to assign specific locations for each.
Everything should have a place, and everything should be in its place.
Consider the frequency of use for each item and place commonly used tools within easy reach.
Label shelves, drawers, and containers to make it easy for anyone to find and return items quickly.
This systematic arrangement minimizes the time spent searching for things, thus boosting productivity.
3. Shine (Seiso)
“Shine” emphasizes cleanliness and maintenance.
A clean workspace not only looks appealing but also reduces the likelihood of accidents or equipment malfunctions.
Develop a routine cleaning schedule that involves everyone in the team.
Encourage regular inspections to ensure that machines and tools are in optimal condition.
Small maintenance tasks, such as wiping surfaces and checking equipment for wear and tear, should be a part of daily operations.
By keeping the work area clean, you contribute to a safer and more inviting workspace.
4. Standardize (Seiketsu)
Standardization is the key to maintaining the improvements achieved through sorting, organizing, and cleaning.
Create standards and procedures that outline how tasks should be performed and how the workspace should be maintained.
Document these processes and make them accessible to all employees.
Regularly update these standards to incorporate feedback and improvements.
Standardization ensures consistency and helps everyone understand their roles and responsibilities clearly.
5. Sustain (Shitsuke)
The final “S” is about sustaining the practices and habits formed in the previous steps.
It requires discipline and commitment from everyone involved.
Regular training and reminders can help reinforce the importance of 5S, ensuring that it becomes a part of the company culture.
Encourage employees to participate in 5S audits and offer feedback on possible improvements.
Celebrate milestones and achievements in maintaining the 5S culture to motivate everyone to continue adhering to these standards.
Benefits of Implementing 5S
Adopting the 5S methodology in the manufacturing department provides numerous benefits:
1. **Improved Productivity:** By reducing waste and improving the flow of operations, employees can complete tasks more efficiently.
2. **Enhanced Safety:** A well-organized and clean workplace minimizes the risk of accidents, leading to a safer environment for everyone.
3. **Better Quality Control:** With everything ordered and standardized, there is less room for error, thus improving the overall quality of products.
4. **Increased Employee Morale:** A tidy and well-managed workspace can boost employee satisfaction and motivation.
5. **Cost Savings:** Efficient use of resources and reduced downtime lead to significant cost savings for the company.
Steps to Get Started with 5S
Getting started with 5S doesn’t have to be daunting.
Here are a few steps a new employee, along with colleagues, can take:
1. **Team Training:** Understand the 5S principles through workshops or training sessions.
2. **Assessment:** Evaluate the current workplace setup and identify areas requiring improvement.
3. **Action Plan:** Develop a plan for implementing each of the 5S steps, including timelines and responsibilities.
4. **Implementation:** Begin sorting and organizing your workspace.
Involve your team in the cleaning routine and establish new standards.
5. **Review and Adjust:** Regularly evaluate the effectiveness of the 5S practices and make adjustments as necessary.
Conclusion: Embrace Continuous Improvement
The 5S methodology is more than just a system of organizing the workplace; it’s about fostering a culture of continuous improvement.
By understanding and applying these principles, new employees can greatly contribute to the efficiency and productivity of the manufacturing department.
As you become familiar with the 5S process, remember that the ultimate goal is to create a work environment that is both efficient and enjoyable, leading to greater success for both you and your company.
資料ダウンロード
QCD調達購買管理クラウド「newji」は、調達購買部門で必要なQCD管理全てを備えた、現場特化型兼クラウド型の今世紀最高の購買管理システムとなります。
ユーザー登録
調達購買業務の効率化だけでなく、システムを導入することで、コスト削減や製品・資材のステータス可視化のほか、属人化していた購買情報の共有化による内部不正防止や統制にも役立ちます。
NEWJI DX
製造業に特化したデジタルトランスフォーメーション(DX)の実現を目指す請負開発型のコンサルティングサービスです。AI、iPaaS、および先端の技術を駆使して、製造プロセスの効率化、業務効率化、チームワーク強化、コスト削減、品質向上を実現します。このサービスは、製造業の課題を深く理解し、それに対する最適なデジタルソリューションを提供することで、企業が持続的な成長とイノベーションを達成できるようサポートします。
オンライン講座
製造業、主に購買・調達部門にお勤めの方々に向けた情報を配信しております。
新任の方やベテランの方、管理職を対象とした幅広いコンテンツをご用意しております。
お問い合わせ
コストダウンが利益に直結する術だと理解していても、なかなか前に進めることができない状況。そんな時は、newjiのコストダウン自動化機能で大きく利益貢献しよう!
(Β版非公開)