- お役立ち記事
- A must-see for new employees in the production technology department! Basics of the Toyota Production System and practical methods on site
A must-see for new employees in the production technology department! Basics of the Toyota Production System and practical methods on site
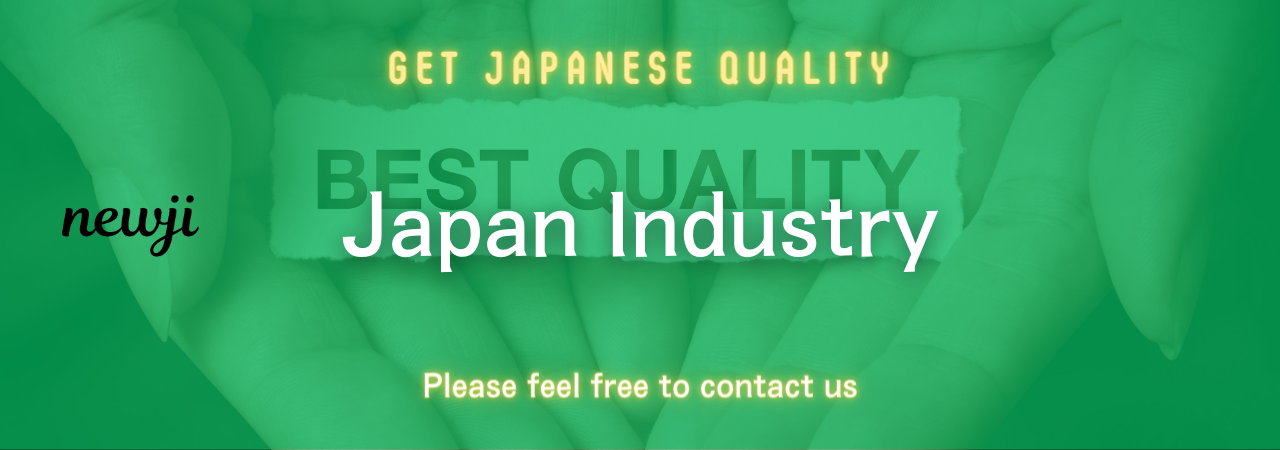
目次
Understanding the Toyota Production System
The Toyota Production System (TPS) is a comprehensive approach to manufacturing that emphasizes efficiency and waste reduction.
It was developed by Toyota, one of the world’s leading automobile manufacturers, to enhance productivity and improve product quality.
This system is not just a set of simple rules but a holistic philosophy that has been adopted by various industries around the globe.
At the core of TPS are two fundamental principles: Just-In-Time (JIT) and Jidoka.
JIT ensures that each process produces only what is needed by the next process in a continuous flow.
This minimizes waste and reduces inventory costs.
Jidoka, on the other hand, refers to automation with a human touch.
It empowers workers to stop the production line whenever a defect is detected, ensuring that quality issues are addressed immediately.
The Pillars of the TPS
To grasp the TPS fully, new employees must familiarize themselves with its main components.
1. Just-In-Time Production
Just-In-Time is all about having the right materials and products at the right time and place.
This approach helps to minimize lead times, reduces storage costs, and keeps inventory low.
In practice, this means closely monitoring the supply chain and production schedules to align perfectly with customer demand.
For new production technology department employees, understanding how to implement JIT can drastically improve efficiency and productivity in their roles.
2. Jidoka (Automation with a Human Touch)
Jidoka is the concept of enabling workers to halt production to address problems immediately.
Machines are designed to stop automatically when an issue occurs, allowing human operators to focus on resolving it.
This proactive approach helps in maintaining high quality and prevents defects from multiplying along the assembly line.
For new employees, embracing Jidoka means actively engaging in quality control and being vigilant about potential issues in the production process.
Practical Methods on Site
Implementing the Toyota Production System on the factory floor requires practical methods and a strong commitment to the system’s principles. Here are some practical ways to put TPS into action:
1. 5S Methodology
The 5S methodology is a workplace organization technique that promotes efficiency and effectiveness.
It stands for Sort, Set in order, Shine, Standardize, and Sustain.
– **Sort:** Identify what is necessary and remove unnecessary items from the workspace.
– **Set in order:** Organize the necessary items so that they can be easily accessed.
– **Shine:** Clean the workspace to ensure a tidy and safe environment.
– **Standardize:** Establish procedures to maintain the first three S’s.
– **Sustain:** Develop habits and routines to follow these practices consistently.
By applying the 5S methodology, employees can help maintain a productive and orderly work environment.
2. Kaizen (Continuous Improvement)
Kaizen is a philosophy that focuses on continuous improvement, involving all employees from management to the shop floor.
It encourages everyone to look for small ways to enhance processes and eliminate waste.
New employees should actively participate in Kaizen activities and suggest ideas for improvement.
Engagement in Kaizen leads to a better understanding of processes and contributes to a culture of innovation.
3. Kanban System
The Kanban system is a visual workflow management method used to achieve JIT production.
It relies on cards or signals, known as Kanbans, to communicate what needs to be produced, how much, and by when.
This system helps in synchronizing supply with demand and reduces excess inventory.
New employees can learn to manage the Kanban system by understanding how to monitor product flow and responding to demand changes effectively.
The Role of Technology in TPS
Technology plays a crucial role in the successful implementation of the Toyota Production System.
From advanced machinery to data analytics, technology can enhance the accuracy and efficiency of production processes.
New employees should familiarize themselves with the latest technology used within their department and understand how it integrates with TPS principles.
Being adept with technology will allow them to automate repetitive tasks, collect data more efficiently, and analyze production metrics to identify areas for improvement.
Challenges and Solutions
While the Toyota Production System offers significant benefits, implementing it can present certain challenges.
Resistance to change, lack of understanding, and inadequate training are common hurdles new employees might face.
Overcoming Resistance
Resistance to change can be addressed through clear communication and involvement.
When employees understand the benefits of TPS and are involved in its implementation, they are more likely to embrace it.
Providing Adequate Training
Comprehensive training programs should be provided to ensure new employees fully grasp the TPS concepts and practices.
Mentorship from experienced employees can also aid in smoother transitions.
Conclusion
For new employees in the production technology department, understanding the Toyota Production System is essential.
By embracing its principles and applying practical methods on site, they can significantly enhance their efficiency and contribute to the company’s success.
TPS is more than a production methodology; it is a mindset of continuous improvement and excellence.
With the right approach and determination, new employees can become valuable assets in driving innovation and quality in the manufacturing process.
資料ダウンロード
QCD調達購買管理クラウド「newji」は、調達購買部門で必要なQCD管理全てを備えた、現場特化型兼クラウド型の今世紀最高の購買管理システムとなります。
ユーザー登録
調達購買業務の効率化だけでなく、システムを導入することで、コスト削減や製品・資材のステータス可視化のほか、属人化していた購買情報の共有化による内部不正防止や統制にも役立ちます。
NEWJI DX
製造業に特化したデジタルトランスフォーメーション(DX)の実現を目指す請負開発型のコンサルティングサービスです。AI、iPaaS、および先端の技術を駆使して、製造プロセスの効率化、業務効率化、チームワーク強化、コスト削減、品質向上を実現します。このサービスは、製造業の課題を深く理解し、それに対する最適なデジタルソリューションを提供することで、企業が持続的な成長とイノベーションを達成できるようサポートします。
オンライン講座
製造業、主に購買・調達部門にお勤めの方々に向けた情報を配信しております。
新任の方やベテランの方、管理職を対象とした幅広いコンテンツをご用意しております。
お問い合わせ
コストダウンが利益に直結する術だと理解していても、なかなか前に進めることができない状況。そんな時は、newjiのコストダウン自動化機能で大きく利益貢献しよう!
(Β版非公開)