- お役立ち記事
- A must-see for new employees! The basics of the “PDCA cycle” that management expects and how to effectively utilize it
月間76,176名の
製造業ご担当者様が閲覧しています*
*2025年3月31日現在のGoogle Analyticsのデータより
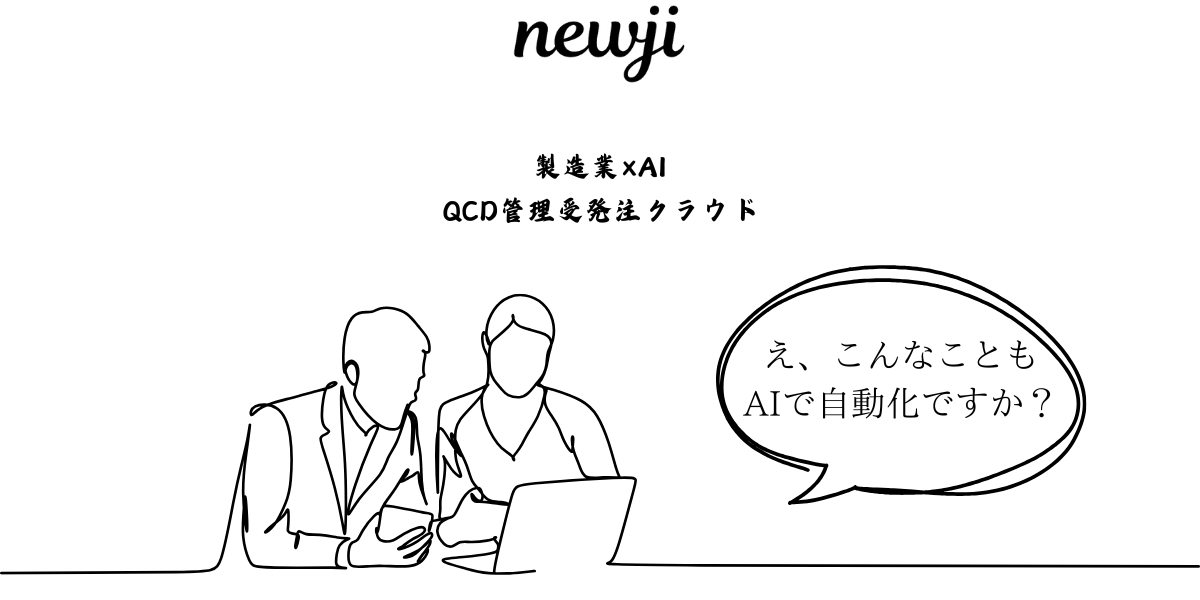
A must-see for new employees! The basics of the “PDCA cycle” that management expects and how to effectively utilize it
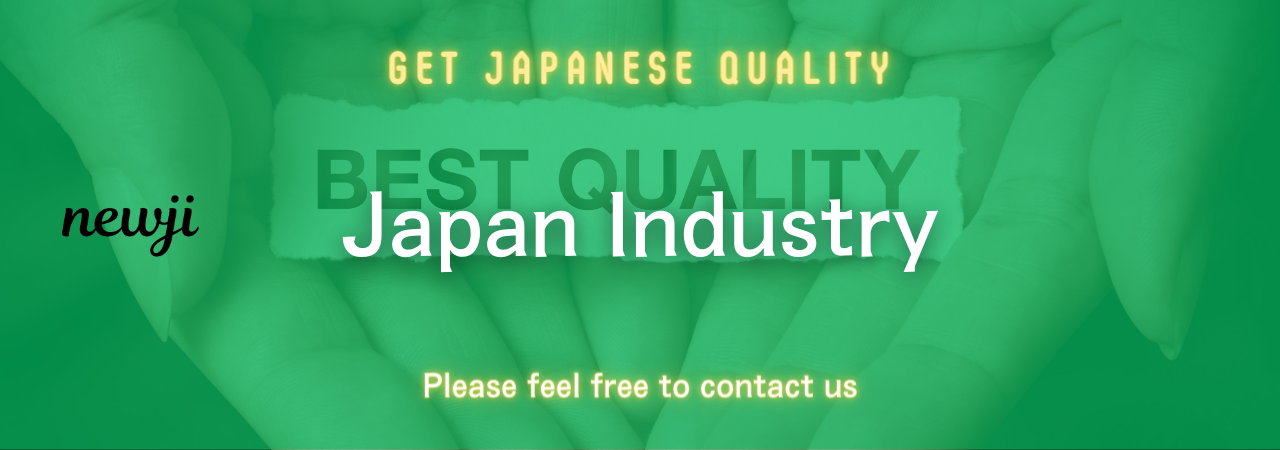
目次
Understanding the PDCA Cycle
The PDCA cycle is an essential tool for both businesses and employees when it comes to problem-solving and continuous improvement.
PDCA stands for Plan, Do, Check, and Act.
This cycle is a simple, effective way to ensure that projects and processes are continuously improving.
Management often expects employees to utilize the PDCA cycle to ensure work efficiency and productivity.
Breaking Down the PDCA Cycle
Let’s explore each phase of the PDCA cycle and understand its importance in the workplace.
Plan
In the planning phase, you identify a goal or a problem that needs resolution.
You must gather all necessary information to form a comprehensive plan.
This includes defining objectives, determining resources, and outlining steps for implementation.
Planning is crucial to ensure that actions align with business goals and strategies.
Do
The “Do” phase is the execution stage.
Here, you implement the plan formulated in the previous step.
This is the phase where actions are taken, and the plan comes to life.
It’s important to keep documentation of what occurs during this phase for future reference and analysis.
Check
In the checking phase, you evaluate the results from the “Do” phase.
This involves measuring success, identifying problems, and comparing outcomes with expected results.
Checking ensures that everything is consistent with the objectives set in the planning phase.
Act
The final stage is to take corrective actions based on the evaluation.
If the plan worked well, it becomes the new standard.
If there were discrepancies, adjustments must be made to improve future performance.
This continuous learning fosters a culture of ongoing improvement.
The Importance of the PDCA Cycle for New Employees
The PDCA cycle is crucial for new employees to understand.
Mastering it helps you develop problem-solving skills, allowing for effective and efficient work.
It ingrains a methodical mindset, ensuring mistakes aren’t repeated but used as learning opportunities.
Driving Continuous Improvement
A fundamental aspect of the PDCA cycle is its emphasis on continuous improvement.
With the cycle, employees focus on regular enhancements rather than waiting for problems to arise.
It encourages proactivity in identifying potential areas for growth.
Boosting Team Collaboration
The PDCA cycle can significantly enhance team collaboration.
It provides a clear framework that team members can follow, ensuring everyone is on the same page.
This reduces misunderstandings and streamlines communication among colleagues.
Enhancing Decision-Making Skills
By using the PDCA cycle, new employees can improve their decision-making skills.
It requires critical thinking, analysis, and evaluation—skills essential to making informed decisions.
New employees learn the importance of assessing both successes and failures.
Effectively Utilizing the PDCA Cycle
Utilizing the PDCA cycle effectively requires conscious effort and understanding.
Let’s explore how to make the most of this framework.
Start with Clear Objectives
Ensure that the objectives in the planning phase are clear and achievable.
Clear goals set the foundation for what you want to achieve with the cycle.
A well-defined objective guides your actions, adjustments, and evaluations.
Embrace Documentation
Documentation is vital throughout the PDCA cycle.
It serves as a record of actions taken and results observed, which is crucial for the checking phase.
Detailed documentation facilitates easier analysis and adjustment.
Learn from Outcomes
In the PDCA cycle, learning from outcomes is key.
Whether results are successful or not, there’s always an opportunity to learn and grow.
Encourage a culture where both successes and failures are viewed as learning tools.
Aim for Small, Incremental Changes
Instead of aiming for large transformations, focus on making small, incremental changes.
This allows you to adjust quickly if things don’t go as planned.
Small changes lead to significant improvements over time.
Conclusion
The PDCA cycle is a foundational concept every new employee should master.
It equips you with the skills needed for effective problem-solving and continuous improvement.
By understanding and applying the PDCA cycle, you not only meet management expectations but also enhance your efficiency and productivity.
Remember to plan thoroughly, act deliberately, check outcomes, and adapt as needed.
Embrace the PDCA cycle as a pathway to professional growth and success in the workplace.
資料ダウンロード
QCD管理受発注クラウド「newji」は、受発注部門で必要なQCD管理全てを備えた、現場特化型兼クラウド型の今世紀最高の受発注管理システムとなります。
ユーザー登録
受発注業務の効率化だけでなく、システムを導入することで、コスト削減や製品・資材のステータス可視化のほか、属人化していた受発注情報の共有化による内部不正防止や統制にも役立ちます。
NEWJI DX
製造業に特化したデジタルトランスフォーメーション(DX)の実現を目指す請負開発型のコンサルティングサービスです。AI、iPaaS、および先端の技術を駆使して、製造プロセスの効率化、業務効率化、チームワーク強化、コスト削減、品質向上を実現します。このサービスは、製造業の課題を深く理解し、それに対する最適なデジタルソリューションを提供することで、企業が持続的な成長とイノベーションを達成できるようサポートします。
製造業ニュース解説
製造業、主に購買・調達部門にお勤めの方々に向けた情報を配信しております。
新任の方やベテランの方、管理職を対象とした幅広いコンテンツをご用意しております。
お問い合わせ
コストダウンが利益に直結する術だと理解していても、なかなか前に進めることができない状況。そんな時は、newjiのコストダウン自動化機能で大きく利益貢献しよう!
(β版非公開)