- お役立ち記事
- A must-see for operators in the automotive industry! Practical guidelines for aluminum welding using pulse welding
A must-see for operators in the automotive industry! Practical guidelines for aluminum welding using pulse welding
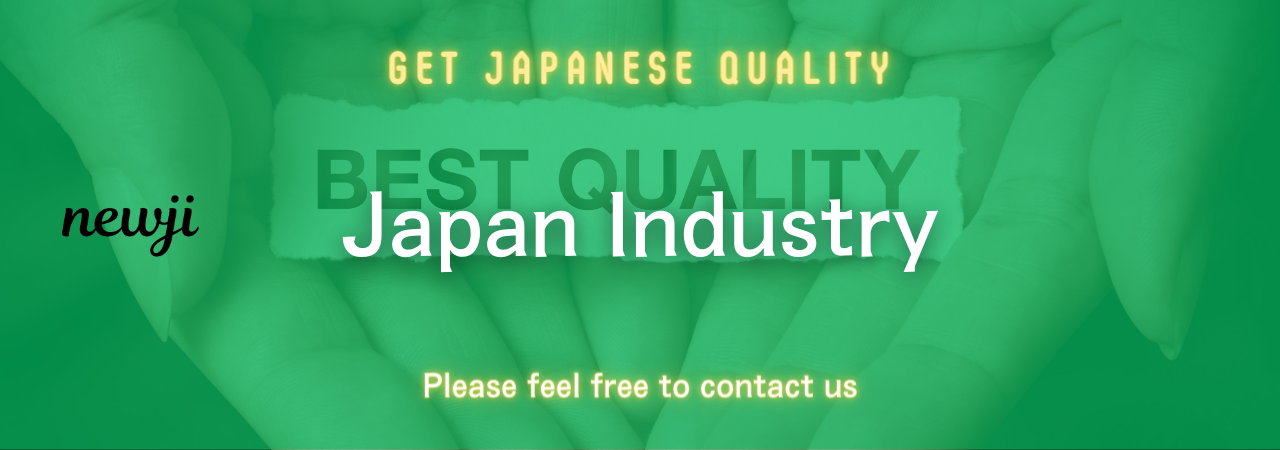
目次
Understanding the Basics of Aluminum Welding
Aluminum welding is an essential process in the automotive industry.
This metal is widely used for its lightweight and strong properties, making it a popular choice for car bodies and components.
However, welding aluminum can be more challenging than other types of metal due to its high thermal conductivity and oxidation characteristics.
These factors require specific techniques to ensure strong, reliable welds.
The Challenges of Aluminum Welding
One of the main challenges in aluminum welding is its high thermal conductivity.
This means that heat dissipates quickly through the metal, which can make it difficult to maintain the temperature needed for effective welding.
If the metal cools down too quickly, the weld may not fully penetrate, resulting in weak joints.
Additionally, aluminum forms an oxide layer on its surface that must be removed before welding.
This layer can prevent proper fusion if not cleaned thoroughly.
Specialized tools and techniques are necessary to remove this oxide layer and prepare the metal for welding.
Pulse Welding: A Modern Solution
Pulse welding is a technique highly recommended for aluminum welding in the automotive industry.
This method uses controlled pulses of electrical energy to focus heat on the welding area.
The use of pulses allows the weld to penetrate properly without overheating the surrounding metal, which can be a common problem with continuous welding methods.
Advantages of Pulse Welding for Aluminum
Pulse welding offers several advantages that make it well-suited for working with aluminum in the automotive sector.
1. **Minimized Heat Distortion**: By applying heat in short, controlled bursts, pulse welding minimizes overall heat input.
This reduces the risk of heat distortion, which can be a challenge with aluminum due to its thermal conductivity.
2. **Enhanced Control**: The precise nature of pulse welding allows operators to control the welding process more accurately.
This results in better weld quality and reduced defects, which is essential for maintaining the structural integrity of automotive parts.
3. **Increased Penetration**: Pulse welding enables deeper penetration of the weld, ensuring a strong bond between the aluminum pieces.
This is particularly important for safety-critical components where weld strength is crucial.
Practical Guidelines for Pulse Welding Aluminum
For operators in the automotive industry looking to harness the benefits of pulse welding for aluminum, following practical guidelines can significantly improve welding outcomes.
1. Proper Preparation
Before starting the welding process, it’s vital to properly prepare the aluminum surface.
This means thoroughly cleaning the metal to remove any oxide layer and contaminants.
Grinding or using a dedicated aluminum cleaner is typically recommended to ensure the metal surface is clean and ready for welding.
In a busy automotive workshop, skipping this step can lead to weak welds and additional rework, affecting productivity and costs.
2. Use Appropriate Equipment
Choosing the right welding equipment is crucial for successful pulse welding.
It’s essential to use a pulse-capable TIG or MIG welding machine that can deliver precise energy pulses.
Some machines are equipped with advanced pulse settings specifically designed for aluminum.
These settings automatically adjust parameters such as pulse frequency, peak current, and background current, simplifying the process for operators.
3. Mastering Technique
While pulse welding offers many automated advantages, skill still plays a role in achieving the best results.
Operators should be trained in maintaining a consistent torch angle and utilizing proper travel speed during welding.
This will help ensure uniform welds with strong, defect-free joints.
Practicing on scrap pieces of aluminum can help operators refine their technique before welding critical components.
Important Safety Considerations
When engaging in any welding operation, safety should always be a top priority.
1. Protective Gear
Welders must wear appropriate protective gear, including helmets with appropriate filters to protect their eyes from harmful light emissions.
High-quality welding gloves, flame-resistant clothing, and respirators are also essential to protect against harmful fumes and heat.
2. Ventilation
Ensuring good ventilation in the welding area is critical.
This reduces the risk of inhaling harmful fumes that can result from the welding process.
Ventilation systems can range from basic fans to more complex extraction systems, depending on the size and workload of the shop.
Conclusion
Aluminum welding using pulse welding techniques presents numerous benefits for the automotive industry.
These advantages include improved control, minimized heat distortion, and increased penetration, resulting in stronger and more reliable welds.
By adhering to the practical guidelines outlined, automotive operators can enhance their welding processes, achieve better results, and maintain the quality and safety standards expected in the industry.
Pulse welding is a valuable skill in the modern automotive workshop, and mastering its application can lead to greater efficiency and productivity, ultimately supporting the creation of safer and more efficient vehicles.
資料ダウンロード
QCD調達購買管理クラウド「newji」は、調達購買部門で必要なQCD管理全てを備えた、現場特化型兼クラウド型の今世紀最高の購買管理システムとなります。
ユーザー登録
調達購買業務の効率化だけでなく、システムを導入することで、コスト削減や製品・資材のステータス可視化のほか、属人化していた購買情報の共有化による内部不正防止や統制にも役立ちます。
NEWJI DX
製造業に特化したデジタルトランスフォーメーション(DX)の実現を目指す請負開発型のコンサルティングサービスです。AI、iPaaS、および先端の技術を駆使して、製造プロセスの効率化、業務効率化、チームワーク強化、コスト削減、品質向上を実現します。このサービスは、製造業の課題を深く理解し、それに対する最適なデジタルソリューションを提供することで、企業が持続的な成長とイノベーションを達成できるようサポートします。
オンライン講座
製造業、主に購買・調達部門にお勤めの方々に向けた情報を配信しております。
新任の方やベテランの方、管理職を対象とした幅広いコンテンツをご用意しております。
お問い合わせ
コストダウンが利益に直結する術だと理解していても、なかなか前に進めることができない状況。そんな時は、newjiのコストダウン自動化機能で大きく利益貢献しよう!
(Β版非公開)