- お役立ち記事
- A must-see for operators in the machining industry! Tips for achieving high-precision inner diameter finishing with honing
A must-see for operators in the machining industry! Tips for achieving high-precision inner diameter finishing with honing
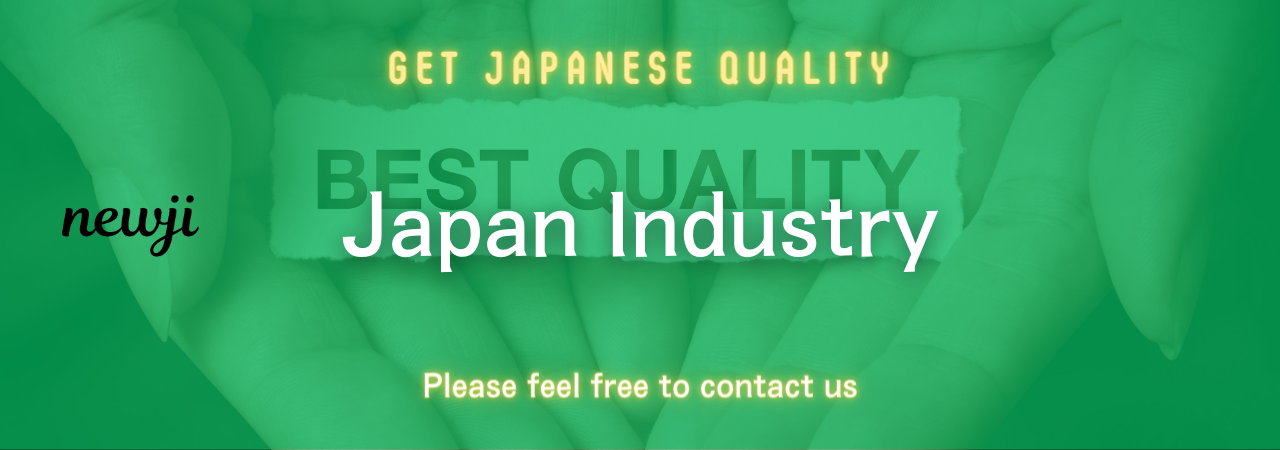
Understanding Honing in Machining
Honing is a critical process in the machining industry designed to improve the precision of inner diameters in various components.
This technique involves an abrasive stone or tool that is used to smooth out or correct the dimensions of a surface.
While honing is broadly used for various purposes, its primary goal in machining is to refine the finish and ensure tight tolerances are met.
When aiming for high-precision inner diameter finishing, honing stands out as a preferred method due to its ability to achieve more controlled and uniform results.
The Benefits of Honing for Inner Diameter Finishing
Honing is often chosen over other machining techniques due to several key advantages.
Firstly, it offers exceptional control over surface finish and can bring about a consistent surface texture, which is crucial for parts that need to fit together precisely.
Moreover, honing can improve the roundness and straighten any deviations present in cylindrical holes, making it perfect for high-precision requirements.
Another benefit of honing is its ability to remove minimal material, allowing for modifications without significant waste.
This is particularly advantageous for costly materials or when maintaining part integrity is paramount.
Choosing the Right Honing Tools
Selecting the appropriate tooling is vital for achieving high-precision inner diameter finishes.
Honing tools can vary significantly depending on the material being worked on and the desired finish.
Common honing tools include diamond abrasives for harder materials and aluminum oxide or silicon carbide for more common machining needs.
It’s important to select a tool that aligns with the material’s hardness and the level of precision required.
In some cases, customized honing tools might be necessary to meet specific tolerances and quality standards.
Setting the Correct Honing Conditions
Achieving success in honing requires more than just the right tool; it’s essential to establish optimal conditions for the process.
Key factors to consider include the honing speed, pressure, and the type of lubricant used during the operation.
Controlling the speed ensures that material removal is consistent without causing excessive heat that could damage the workpiece.
Likewise, the pressure needs to be carefully adjusted to maintain tool life and avoid deforming the component.
Lubricants play a critical role in cooling and cleaning, and choosing the right one can significantly affect the overall finish and tool wear.
Honing Techniques for Different Materials
Different materials require tailored honing techniques to achieve the best results.
For metals like steel, a slower speed with high abrasive quality may be needed to create a smooth and precise finish.
Meanwhile, softer materials might benefit from variable abrasives to prevent over-cutting or distortion.
Understanding the material properties and how they interact with the honing tool can help in adjusting techniques for optimal performance.
Maintaining Consistency in Honing
Consistency is key in honing, especially when producing parts at scale.
Implementing a monitoring system can ensure that quality is maintained throughout the process.
Regular inspections and measurements should be part of the honing routine to catch any deviations early.
Automation can also improve consistency by controlling variables like speed and pressure automatically, reducing errors and enhancing repeatability.
Challenges and Solutions in Precision Honing
While honing is effective, it is not without its challenges.
One common issue is maintaining the sharpness of the honing stones, as worn-out abrasives can lead to poor finishes.
Regular maintenance and timely replacement of the honing tools are essential to counter this challenge.
Another challenge is managing thermal expansion, which can affect the tolerances and alignment of components.
Using adequate cooling systems and choosing the right lubrication can mitigate these issues effectively.
Quality Control in Honing Processes
Implementing rigorous quality control measures ensures that honed parts meet the highest standards.
Using precision measurement tools, such as calipers and micrometers, can help in verifying the dimensions and surface finishes of honed interiors.
Statistical process control methods may also be applied to manage variations and enhance production quality.
Incorporating feedback loops from quality control checks can lead to continuous improvements in the honing process, ultimately achieving greater precision.
Conclusion
For operators in the machining industry, honing offers a reliable method for achieving high-precision inner diameter finishes.
By selecting the right tools, maintaining optimal conditions, and employing strict quality control, manufacturers can produce components of the highest precision and quality.
Understanding the nuances of honing can help operators overcome challenges and consistently meet the rigorous demands of modern machining applications.
資料ダウンロード
QCD調達購買管理クラウド「newji」は、調達購買部門で必要なQCD管理全てを備えた、現場特化型兼クラウド型の今世紀最高の購買管理システムとなります。
ユーザー登録
調達購買業務の効率化だけでなく、システムを導入することで、コスト削減や製品・資材のステータス可視化のほか、属人化していた購買情報の共有化による内部不正防止や統制にも役立ちます。
NEWJI DX
製造業に特化したデジタルトランスフォーメーション(DX)の実現を目指す請負開発型のコンサルティングサービスです。AI、iPaaS、および先端の技術を駆使して、製造プロセスの効率化、業務効率化、チームワーク強化、コスト削減、品質向上を実現します。このサービスは、製造業の課題を深く理解し、それに対する最適なデジタルソリューションを提供することで、企業が持続的な成長とイノベーションを達成できるようサポートします。
オンライン講座
製造業、主に購買・調達部門にお勤めの方々に向けた情報を配信しております。
新任の方やベテランの方、管理職を対象とした幅広いコンテンツをご用意しております。
お問い合わせ
コストダウンが利益に直結する術だと理解していても、なかなか前に進めることができない状況。そんな時は、newjiのコストダウン自動化機能で大きく利益貢献しよう!
(Β版非公開)