- お役立ち記事
- A must-see for operators in the precision machinery industry! Key points for finishing and surface modification of high-precision parts using electrolytic polishing
月間76,176名の
製造業ご担当者様が閲覧しています*
*2025年3月31日現在のGoogle Analyticsのデータより
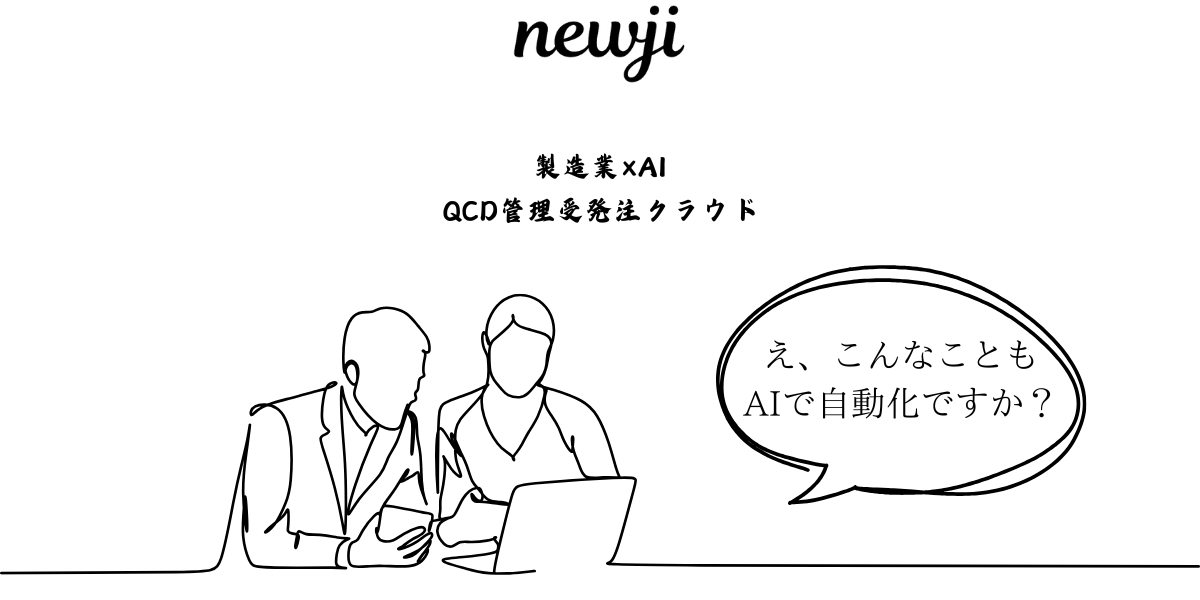
A must-see for operators in the precision machinery industry! Key points for finishing and surface modification of high-precision parts using electrolytic polishing
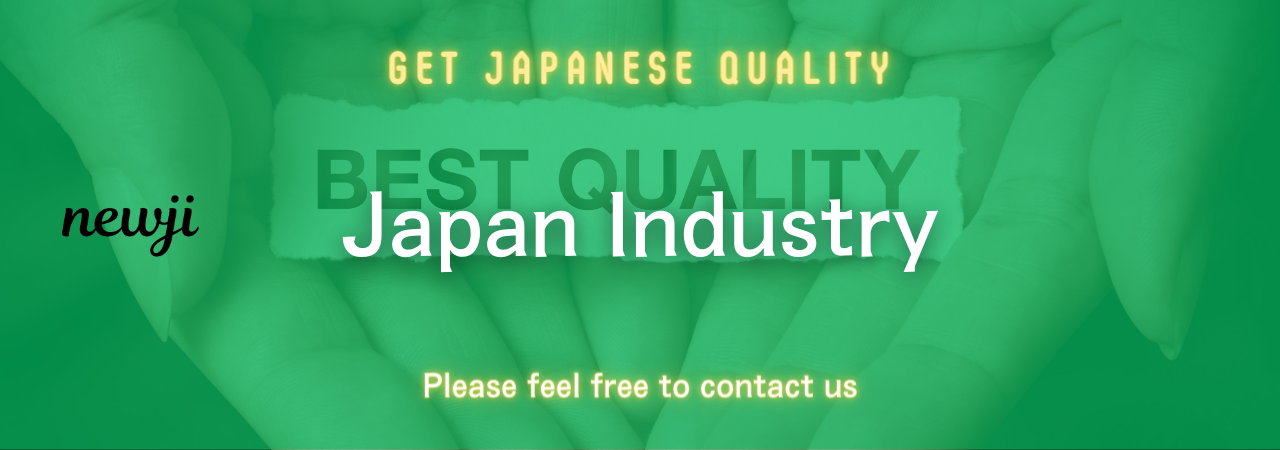
目次
Introduction to Electrolytic Polishing
Electrolytic polishing, often called electro-polishing, is a valuable method used in the precision machinery industry for finishing and surface modification of high-precision parts.
This process not only enhances the appearance of components but also improves their performance by reducing surface roughness and removing micro-burrs.
It’s an essential technique for operators in the industry who aim to produce high-quality parts with excellent surface finishes.
How Electrolytic Polishing Works
The electrolytic polishing process involves the use of an electrolytic cell, where the part to be polished acts as the anode.
A suitable electrolyte, often an acidic solution, is used to facilitate the process.
When an electric current passes through the cell, the surface material of the anode is dissolved, leading to a smoother and more polished surface.
The process selectively removes peaks of roughness without affecting the entire surface, which is why it is so effective in enhancing the finish.
This method is particularly beneficial for complex geometries and internal surfaces that are difficult to polish mechanically.
Advantages of Electrolytic Polishing
Electrolytic polishing offers several advantages over traditional mechanical polishing methods.
Firstly, it provides a superior smooth finish, which is crucial for improving the functionality and longevity of precision parts.
A smoother surface helps in reducing friction and wear, thereby extending the life of parts in motion.
Secondly, it is a non-mechanical process, meaning there’s no risk of introducing new scratches or deforming the part.
This attribute is particularly significant for delicate components where maintaining exact dimensions is crucial.
Another significant advantage is the enhanced corrosion resistance achieved through electro-polishing.
The process removes surface contaminants and creates a chromium-rich oxide layer on stainless steel, for example, boosting its corrosion resistance.
This property is particularly vital for components used in harsh or corrosive environments.
Applications of Electrolytic Polishing
Electrolytic polishing is widely used across various industries, including aerospace, medical, and food processing.
In the aerospace industry, for instance, components require high precision and a flawless finish to ensure safety and performance.
Electro-polishing is used to enhance the fatigue strength and reduce the risk of stress corrosion cracking.
In the medical field, components such as surgical instruments and implants demand a high level of cleanliness and smoothness to prevent bacterial attachment and ensure patient safety.
Electro-polishing delivers a superior finish, meeting stringent medical standards.
The food processing industry benefits from electro-polishing as it creates a sanitary finish that is easy to clean and maintain.
This is critical for components in direct contact with food, ensuring hygiene and safety.
Key Points in Electrolytic Polishing of High-Precision Parts
When it comes to polishing high-precision parts, several key points must be considered to achieve the desired results.
Operators must carefully select the appropriate electrolyte and determine the correct current density and temperature.
These parameters can greatly influence the outcome, and getting them right is crucial for success.
Monitoring the time of the process is also vital.
Over-polishing can lead to loss of dimension and structural integrity, while under-polishing may result in incomplete smoothing.
It requires precise control and monitoring to strike a perfect balance.
Choosing the Right Equipment
The selection of equipment is another critical consideration.
Sophisticated equipment with precise controls is essential for achieving consistent results.
Advanced systems can offer automated controls for better repeatability and efficiency in mass production settings.
Quality Control and Inspection
Quality control and inspection are crucial post-process steps.
Documenting the before and after conditions of the parts helps in assessing the effectiveness of the process.
Using tools such as surface profilometers to measure roughness can confirm whether the desired finish has been achieved.
Safety Considerations
Safety is paramount when conducting electrolytic polishing.
Operators should ensure proper ventilation and use personal protective equipment to shield against splashes and fumes from the acidic electrolytes.
Following industry safety standards and guidelines mitigates the risks associated with the process.
Conclusion
Electrolytic polishing is a must-know process for operators in the precision machinery industry, offering significant benefits in finishing and surface modification of high-precision parts.
Its ability to produce a flawless, smooth surface without compromising the part’s integrity is invaluable, particularly for complex geometries and sensitive applications.
By understanding the process parameters, selecting the appropriate equipment, and adhering to safety protocols, operators can greatly enhance the quality and performance of precision parts.
Electrolytic polishing remains an indispensable tool in achieving high standards in various demanding industries.
資料ダウンロード
QCD管理受発注クラウド「newji」は、受発注部門で必要なQCD管理全てを備えた、現場特化型兼クラウド型の今世紀最高の受発注管理システムとなります。
ユーザー登録
受発注業務の効率化だけでなく、システムを導入することで、コスト削減や製品・資材のステータス可視化のほか、属人化していた受発注情報の共有化による内部不正防止や統制にも役立ちます。
NEWJI DX
製造業に特化したデジタルトランスフォーメーション(DX)の実現を目指す請負開発型のコンサルティングサービスです。AI、iPaaS、および先端の技術を駆使して、製造プロセスの効率化、業務効率化、チームワーク強化、コスト削減、品質向上を実現します。このサービスは、製造業の課題を深く理解し、それに対する最適なデジタルソリューションを提供することで、企業が持続的な成長とイノベーションを達成できるようサポートします。
製造業ニュース解説
製造業、主に購買・調達部門にお勤めの方々に向けた情報を配信しております。
新任の方やベテランの方、管理職を対象とした幅広いコンテンツをご用意しております。
お問い合わせ
コストダウンが利益に直結する術だと理解していても、なかなか前に進めることができない状況。そんな時は、newjiのコストダウン自動化機能で大きく利益貢献しよう!
(β版非公開)