- お役立ち記事
- A must-see for operators in the precision machinery industry! Techniques for finishing high-precision parts with ultrasonic polishing
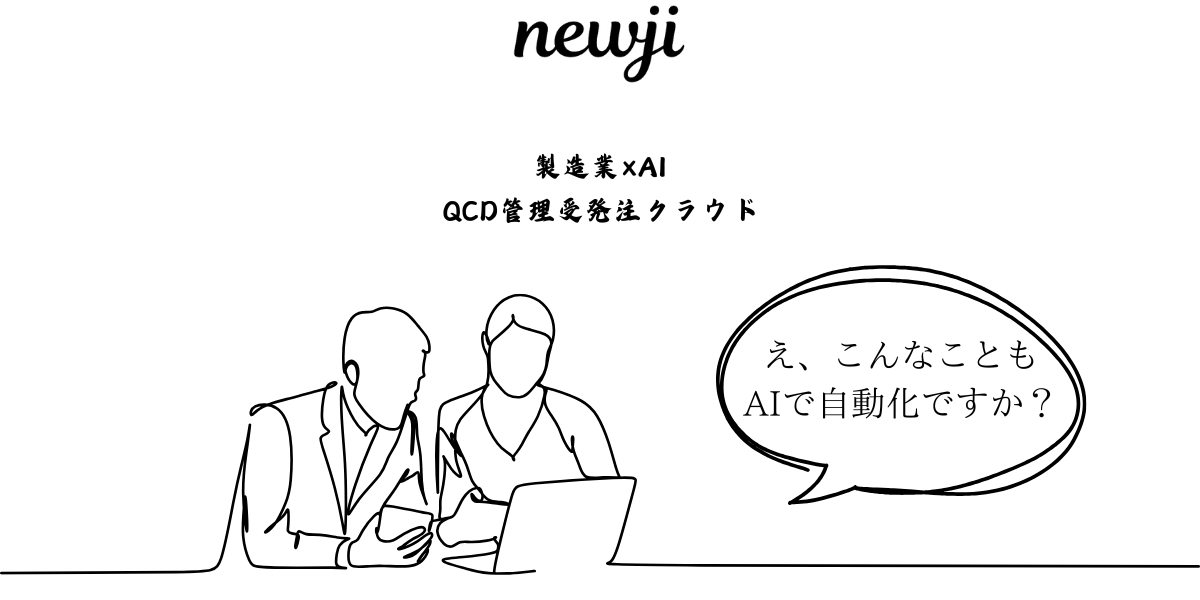
A must-see for operators in the precision machinery industry! Techniques for finishing high-precision parts with ultrasonic polishing
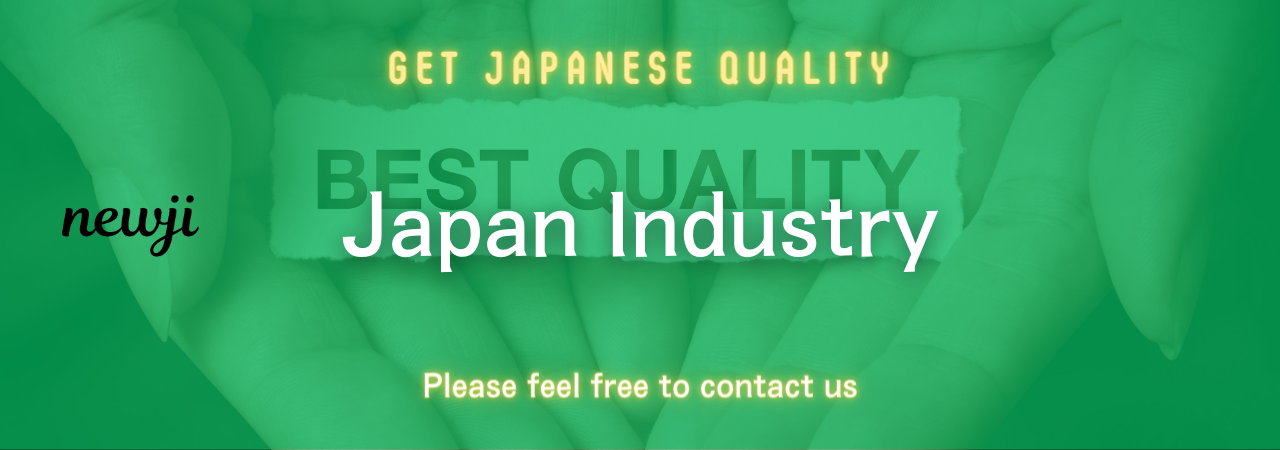
目次
Understanding Ultrasonic Polishing
Ultrasonic polishing is a refined technique widely used in the precision machinery industry to achieve high-quality finishes on intricate parts.
This process employs ultrasonic vibrations to polish delicate components, ensuring even the smallest details are smooth and precise.
Ultrasonic polishing is particularly beneficial for materials that are difficult to machine, offering a gentle yet effective method to enhance part surfaces.
The primary advantage of ultrasonic polishing is its ability to reach areas that conventional techniques cannot.
This is achieved by utilizing tools that vibrate at ultrasonic frequencies, allowing abrasives to remove imperfections meticulously without damaging the workpiece.
The result is a highly polished part with exceptional accuracy and finish, meeting the stringent standards required in the precision machinery field.
Why Precision Matters
In the precision machinery industry, accuracy is paramount.
Parts must often meet tolerances within microns, requiring exceptional attention to detail during production.
High-precision components are crucial in many applications, from aerospace to medical devices, where the slightest deviation can affect performance.
Ultrasonic polishing stands out as a preferred method when finishing such parts due to its precision capabilities.
It removes surface irregularities, reduces roughness, and enhances the overall quality of the components.
This method guarantees the finished product will operate smoothly, increasing its longevity and reliability in demanding environments.
Applications of Ultrasonic Polishing
Ultrasonic polishing is versatile and finds applications across various industries.
In the automotive industry, it is used to fine-tune engine components, improving efficiency and reducing friction.
In electronics, it ensures that connectors and other small parts meet exact specifications, avoiding any potential operational issues.
The medical field also benefits significantly from ultrasonic polishing.
Surgical instruments and implants require flawless surfaces to prevent infections and ensure patient safety.
Ultrasonic polishing helps achieve these hygiene standards by providing a perfectly smooth finish.
The Ultrasonic Polishing Process
Understanding the steps involved in ultrasonic polishing can demystify its effectiveness.
The process begins with selecting the appropriate tool and abrasive material corresponding to the part’s material and desired finish.
Tool selection is crucial, as it must match the geometry of the workpiece for thorough polishing.
Once the tooling is prepared, the component is immersed in a liquid medium.
This medium not only helps in smooth polishing but also cools the workpiece during the process.
The ultrasonic tool then vibrates at high frequencies, causing the abrasive particles to impact the surface lightly, progressively removing minute imperfections.
The process requires careful monitoring, as excessive polishing can lead to over-finishing, potentially altering the part’s dimensions.
Operators must balance the intensity and duration of polishing to ensure the desired outcome without compromising the component’s structural integrity.
Key Benefits of Ultrasonic Polishing
Ultrasonic polishing offers several distinct advantages that make it an essential technique in precision machining.
First, it delivers unparalleled precision, achieving finishes that other polishing methods may struggle to provide.
The technique is especially advantageous for complex shapes and hard-to-reach areas, where conventional polishing methods might fall short.
Moreover, ultrasonic polishing is known for its efficiency.
It reduces the time required to achieve a high-quality finish, enhancing productivity while maintaining superior accuracy.
This efficiency translates to cost savings, making ultrasonic polishing a cost-effective solution for companies.
Another benefit is the preservation of the part’s integrity.
Unlike more aggressive polishing techniques, ultrasonic methods minimize stress and deformation on the workpiece.
This ensures the component maintains its geometric accuracy and functional properties, critical for high-performance applications.
Challenges in Ultrasonic Polishing
Despite its advantages, ultrasonic polishing poses certain challenges.
One significant hurdle is the initial cost of the equipment, which can be higher than that of traditional methods.
However, the return on investment often outweighs the upfront expense due to the increased precision and efficiency offered.
Additionally, the technique requires skilled operators who understand the intricacies of ultrasonic polishing.
Training is necessary to ensure optimal results, as improper use can lead to undesirable finishes or damage to the part.
Material compatibility is another concern, as not all materials respond equally well to ultrasonic waves.
Operators must carefully select suitable abrasives and frequencies based on the specific material to avoid surface damage.
Future of Ultrasonic Polishing
As technology advances, ultrasonic polishing is expected to evolve further, integrating with automation and smart manufacturing technologies.
This evolution will likely enhance process control, allowing for even greater precision and repeatability.
In addition, research continues into developing new abrasives and polishing mediums that enhance the capabilities of ultrasonic polishing.
These innovations promise to broaden the range of materials and applications, solidifying ultrasonic polishing’s role in the future of precision machining.
Conclusion
Ultrasonic polishing remains a crucial technique within the precision machinery industry.
Its ability to produce high-quality finishes on complex parts is unmatched, offering a reliable solution to meet strict industry requirements.
While it presents challenges in terms of cost and operator skill, the benefits it provides in terms of precision, efficiency, and part integrity are invaluable.
As the industry advances towards more automated and precise manufacturing processes, embracing ultrasonic polishing techniques will ensure companies remain at the forefront of high-precision production.
資料ダウンロード
QCD調達購買管理クラウド「newji」は、調達購買部門で必要なQCD管理全てを備えた、現場特化型兼クラウド型の今世紀最高の購買管理システムとなります。
ユーザー登録
調達購買業務の効率化だけでなく、システムを導入することで、コスト削減や製品・資材のステータス可視化のほか、属人化していた購買情報の共有化による内部不正防止や統制にも役立ちます。
NEWJI DX
製造業に特化したデジタルトランスフォーメーション(DX)の実現を目指す請負開発型のコンサルティングサービスです。AI、iPaaS、および先端の技術を駆使して、製造プロセスの効率化、業務効率化、チームワーク強化、コスト削減、品質向上を実現します。このサービスは、製造業の課題を深く理解し、それに対する最適なデジタルソリューションを提供することで、企業が持続的な成長とイノベーションを達成できるようサポートします。
オンライン講座
製造業、主に購買・調達部門にお勤めの方々に向けた情報を配信しております。
新任の方やベテランの方、管理職を対象とした幅広いコンテンツをご用意しております。
お問い合わせ
コストダウンが利益に直結する術だと理解していても、なかなか前に進めることができない状況。そんな時は、newjiのコストダウン自動化機能で大きく利益貢献しよう!
(Β版非公開)