- お役立ち記事
- A must-see for process control leaders in the pharmaceutical manufacturing industry! Enhance real-time management of manufacturing with PAT (Process Analysis Technology)
月間76,176名の
製造業ご担当者様が閲覧しています*
*2025年3月31日現在のGoogle Analyticsのデータより
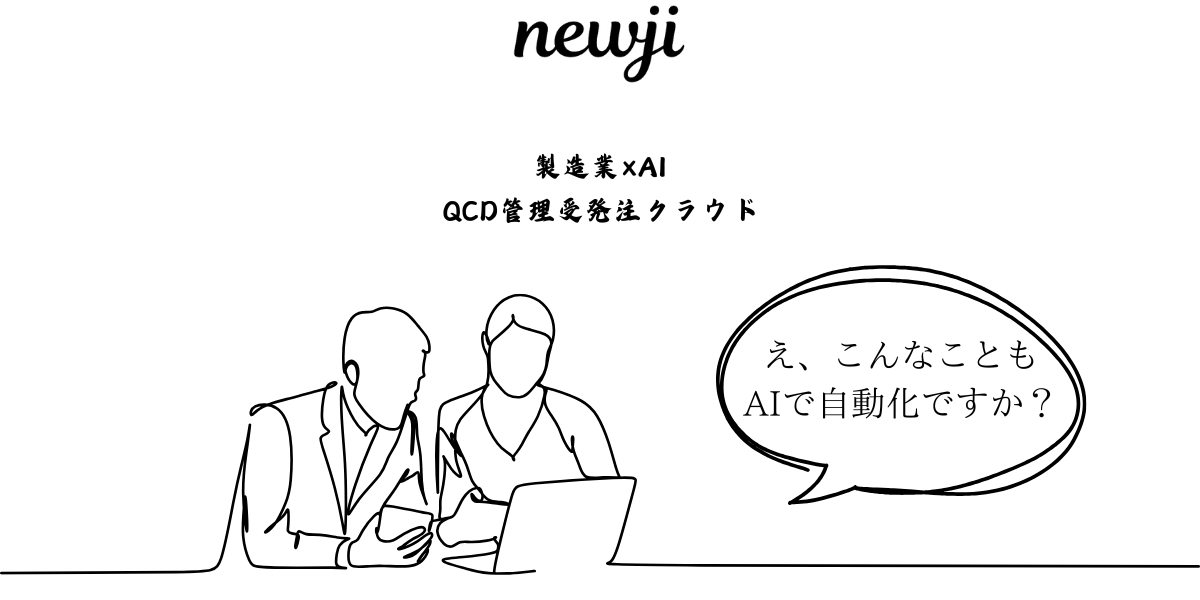
A must-see for process control leaders in the pharmaceutical manufacturing industry! Enhance real-time management of manufacturing with PAT (Process Analysis Technology)
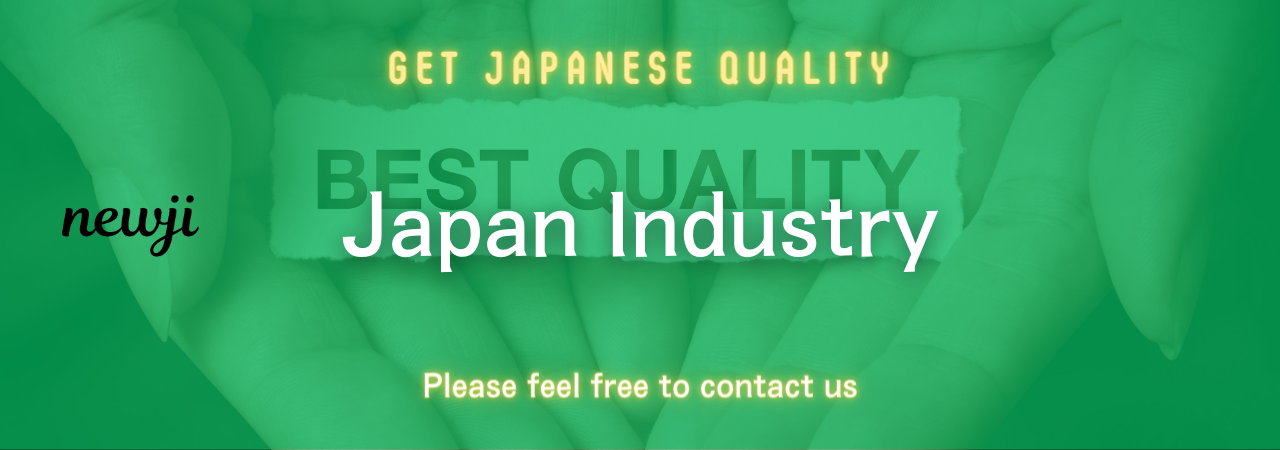
Understanding PAT: The Game-Changer in Pharmaceutical Manufacturing
Pharmaceutical manufacturing is a highly intricate process that requires precision and control at every step.
With the growing complexity of drugs and regulatory demands, ensuring quality and consistency in drug production is more crucial than ever.
This is where Process Analytical Technology (PAT) steps in to revolutionize the field.
PAT is a system designed to analyze and control manufacturing through timely measurements.
It provides real-time data that enables manufacturers to monitor critical quality and performance attributes of raw and in-process materials.
Adopting PAT in pharmaceutical manufacturing can lead to more efficient processes, reduced costs, and higher quality products.
The Role of Real-Time Monitoring
In traditional manufacturing settings, quality testing is often carried out at the end of the production cycle.
This can lead to delays and inefficiencies, as issues are detected only after significant time and resources have already been invested.
PAT changes this approach by allowing for real-time monitoring of manufacturing processes.
This means that any deviations from the desired quality or production standards can be immediately detected and corrected.
By integrating sensors and analytical instruments directly into the production line, manufacturers can continuously assess parameters such as temperature, pressure, and chemical composition.
Real-time monitoring helps in minimizing waste and variances in production batches.
It ensures that the process remains within specified limits, thus maintaining the quality of the final product.
Benefits of Implementing PAT in Pharmaceutical Manufacturing
The adoption of PAT offers numerous benefits for pharmaceutical manufacturers.
Here are some key advantages:
1. Enhanced Quality and Consistency
With PAT, manufacturers can maintain consistent quality across all production batches.
By constantly monitoring and adjusting the processes, variations and discrepancies can be minimized, leading to consistently high-quality products.
This is especially important in the pharmaceutical industry, where even minor deviations can lead to significant consequences.
2. Improved Efficiency and Cost Reduction
PAT enables manufacturers to optimize their processes by providing insights into efficiency bottlenecks.
These insights help in reducing cycle times and energy consumption, leading to significant cost savings.
Additionally, real-time data allows for more agile decision-making and adjustments, which can help avoid costly reworks and product recalls.
3. Accelerated Product Development
By using PAT, manufacturers can better understand their production processes and the effects of different variables.
This understanding can accelerate the development phase of new drugs, as researchers can quickly test and refine processes to achieve desired outcomes.
With faster development comes quicker time-to-market for new products, providing a competitive advantage.
4. Compliance with Regulatory Standards
The pharmaceutical industry is heavily regulated, with strict guidelines ensuring product efficacy and safety.
PAT helps manufacturers meet these regulatory requirements by providing transparent and accurate data on the production process.
With PAT, manufacturers can easily demonstrate compliance with regulatory standards during inspections and audits.
Implementing PAT: Considerations and Challenges
While the benefits of PAT are clear, implementing this technology in pharmaceutical manufacturing requires careful planning and execution.
1. Integration with Existing Systems
One of the challenges in adopting PAT is integrating it with existing production infrastructure.
Manufacturers need to ensure that sensors, instruments, and data acquisition systems are compatible with their current systems.
It may also involve upgrading or modifying equipment to accommodate the new technology.
2. Training and Skill Development
Implementing PAT requires specialized knowledge and skills.
Employees need to be trained in using the technology, interpreting data, and making data-driven decisions.
It’s crucial to build a team with the right expertise to maximize the potential of PAT.
3. Initial Investment and ROI
Adopting PAT involves an upfront investment in technology and training.
Manufacturers must weigh these costs against the potential return on investment through enhanced efficiency, reduced wastage, and improved product quality.
Future Trends and Innovations in PAT
As technology continues to advance, so does PAT.
Here are some emerging trends that are likely to shape the future of pharmaceutical manufacturing:
1. Artificial Intelligence and Machine Learning
Integrating AI and machine learning with PAT systems can enhance data analysis, pattern recognition, and predictive insights.
AI can help identify anomalies and suggest corrective actions in real-time, further enhancing process control and efficiency.
2. Automation and Robotics
Combining PAT with automation and robotics allows for fully automated manufacturing processes.
This reduces human intervention, minimizing errors and enhancing precision in production.
3. Cloud-Based Analytics
Cloud computing enables manufacturers to store and analyze vast amounts of data.
Real-time data from PAT systems can be analyzed in the cloud, providing insights accessible from anywhere.
This facilitates faster decision-making and collaboration across global teams.
In conclusion, Process Analytical Technology is a pivotal tool for process control leaders in the pharmaceutical manufacturing industry.
It offers enhanced real-time management of manufacturing by providing valuable insights into the production process.
By embracing PAT, manufacturers are well-equipped to meet the challenges of modern pharmaceutical production while ensuring the highest standards of quality and efficiency.
資料ダウンロード
QCD管理受発注クラウド「newji」は、受発注部門で必要なQCD管理全てを備えた、現場特化型兼クラウド型の今世紀最高の受発注管理システムとなります。
ユーザー登録
受発注業務の効率化だけでなく、システムを導入することで、コスト削減や製品・資材のステータス可視化のほか、属人化していた受発注情報の共有化による内部不正防止や統制にも役立ちます。
NEWJI DX
製造業に特化したデジタルトランスフォーメーション(DX)の実現を目指す請負開発型のコンサルティングサービスです。AI、iPaaS、および先端の技術を駆使して、製造プロセスの効率化、業務効率化、チームワーク強化、コスト削減、品質向上を実現します。このサービスは、製造業の課題を深く理解し、それに対する最適なデジタルソリューションを提供することで、企業が持続的な成長とイノベーションを達成できるようサポートします。
製造業ニュース解説
製造業、主に購買・調達部門にお勤めの方々に向けた情報を配信しております。
新任の方やベテランの方、管理職を対象とした幅広いコンテンツをご用意しております。
お問い合わせ
コストダウンが利益に直結する術だと理解していても、なかなか前に進めることができない状況。そんな時は、newjiのコストダウン自動化機能で大きく利益貢献しよう!
(β版非公開)