- お役立ち記事
- A must-see for process control leaders in the pharmaceutical manufacturing industry! Enhance real-time management of manufacturing with PAT (Process Analysis Technology)
A must-see for process control leaders in the pharmaceutical manufacturing industry! Enhance real-time management of manufacturing with PAT (Process Analysis Technology)
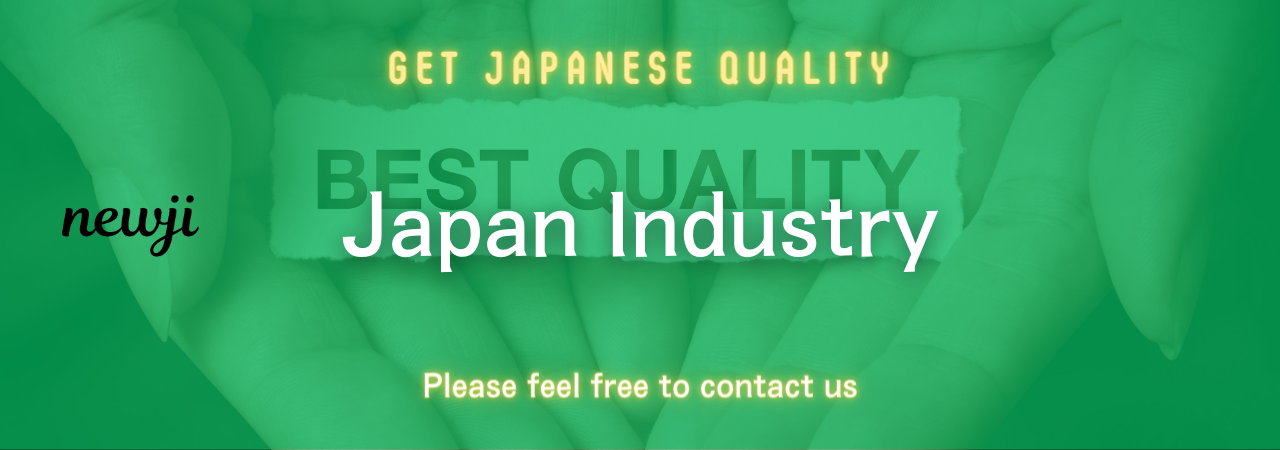
目次
Understanding PAT in Pharmaceutical Manufacturing
Process Analytical Technology (PAT) is a system for designing, analyzing, and controlling manufacturing through real-time measurements of critical quality and performance attributes of raw and in-process materials and processes.
This technology aims to ensure the quality of the final product.
In pharmaceutical manufacturing, where precision and reliability are paramount, PAT plays a crucial role in maintaining the integrity and quality of products.
By integrating PAT, companies can optimize their processes, reduce waste, and improve overall efficiency.
This technology provides real-time feedback, allowing for immediate adjustments during production.
Such proactive measures can prevent the production of substandard products and reduce the need for final product testing.
The Core Components of PAT
To fully grasp the benefits of PAT, it’s important to understand its core components.
These include:
1. **Process Understanding**: This involves mapping out and understanding all the variables and interactions in the manufacturing process.
A comprehensive process model is developed to monitor critical quality attributes (CQAs) and critical process parameters (CPPs).
2. **Risk-Based Approach**: PAT emphasizes a risk-based approach to manage the lifecycles of pharmaceutical products.
By identifying and focusing on high-risk areas, companies can ensure that they are addressing the most crucial quality challenges.
3. **Multivariate Tools**: These tools are used for designing, analyzing, and controlling the manufacturing processes.
They collect and interpret complex data sets to provide insights into the manufacturing operations.
4. **Process Control Tools**: These tools involve the standardization of machinery and equipment to maintain consistency in product manufacture.
Through real-time monitoring and control, manufacturers can maintain tight control over their processes.
5. **Continuous Improvement and Feedback**: PAT fosters a culture of continuous improvement.
By leveraging real-time data, manufacturers can make better decisions, leading to improvements in manufacturing efficiency and product quality.
Benefits of Implementing PAT
The implementation of PAT in pharmaceutical manufacturing comes with a variety of benefits.
These benefits are not only limited to the enhancement of product quality but also extend to operational efficiency and compliance.
Improved Product Quality
PAT’s primary goal is to improve product quality.
By implementing real-time monitoring and control, pharmaceutical manufacturers can ensure consistency in their products.
This approach minimizes deviations and errors, reducing the likelihood of product recalls and maintaining brand integrity.
Increased Efficiency and Cost Reduction
Efficiency is key in manufacturing, and PAT helps streamline operations.
By optimizing processes and reducing waste, companies can significantly cut down production costs.
The reduction in time spent on quality checks and manual inspections also contributes to overall cost savings.
Enhanced Regulatory Compliance
The pharmaceutical industry is heavily regulated.
PAT helps in meeting compliance requirements by providing detailed data and documentation.
This data supports regulatory audits and inspections, ensuring that manufacturing processes meet the necessary guidelines.
Flexibility and Scalability
PAT provides the flexibility to adapt manufacturing processes quickly in response to changes in market demand or regulatory requirements.
It also supports scalability, allowing companies to efficiently expand operations as needed without compromising quality.
Challenges in PAT Implementation
While the advantages of PAT are clear, implementing it does come with its challenges.
Understanding these challenges is essential for a successful integration into manufacturing processes.
High Initial Costs
One of the main barriers to the adoption of PAT is the initial investment required.
The technology needs specialized equipment, trained personnel, and a thorough overhaul of existing processes.
However, the long-term benefits usually outweigh the upfront costs.
Complexity and Technical Expertise
Implementing PAT requires a deep understanding of both the technology and the existing manufacturing processes.
This complexity necessitates expert knowledge, making it important to have skilled personnel who can manage the system effectively.
Data Management and Analysis
PAT generates a significant amount of data that must be effectively managed and interpreted.
This requires robust data systems and skilled analysts to extract meaningful insights.
Steps to Successful PAT Implementation
To overcome these challenges and successfully implement PAT, pharmaceutical companies should follow a structured approach.
Conduct a Thorough Assessment
Begin with a comprehensive assessment of current manufacturing processes.
Identify areas where PAT can add the most value and define clear objectives for its implementation.
Invest in Training
Ensure that staff are adequately trained to understand and operate PAT systems.
Invest in continuous training programs to keep up with advancements in the technology and to enhance the skills of personnel.
Leverage Pilot Projects
Start with pilot projects to demonstrate PAT’s potential benefits.
These smaller-scale implementations can help in understanding the technology better and formulating strategies for a larger rollout.
Collaborate with Experts
Engage with industry experts and vendors during the implementation process.
Their insights and experience can help avoid common pitfalls and ensure a smoother integration of PAT into existing systems.
Conclusion
Process Analytical Technology (PAT) holds the potential to revolutionize pharmaceutical manufacturing.
By providing real-time insights and fostering greater control over production processes, PAT enhances product quality and operational efficiency.
While implementation poses certain challenges, a strategic approach can unlock significant benefits.
For leaders in pharmaceutical manufacturing, embracing PAT is a step towards future-proofing operations, achieving compliance, and maintaining competitive advantage in a highly regulated industry.
資料ダウンロード
QCD調達購買管理クラウド「newji」は、調達購買部門で必要なQCD管理全てを備えた、現場特化型兼クラウド型の今世紀最高の購買管理システムとなります。
ユーザー登録
調達購買業務の効率化だけでなく、システムを導入することで、コスト削減や製品・資材のステータス可視化のほか、属人化していた購買情報の共有化による内部不正防止や統制にも役立ちます。
NEWJI DX
製造業に特化したデジタルトランスフォーメーション(DX)の実現を目指す請負開発型のコンサルティングサービスです。AI、iPaaS、および先端の技術を駆使して、製造プロセスの効率化、業務効率化、チームワーク強化、コスト削減、品質向上を実現します。このサービスは、製造業の課題を深く理解し、それに対する最適なデジタルソリューションを提供することで、企業が持続的な成長とイノベーションを達成できるようサポートします。
オンライン講座
製造業、主に購買・調達部門にお勤めの方々に向けた情報を配信しております。
新任の方やベテランの方、管理職を対象とした幅広いコンテンツをご用意しております。
お問い合わせ
コストダウンが利益に直結する術だと理解していても、なかなか前に進めることができない状況。そんな時は、newjiのコストダウン自動化機能で大きく利益貢献しよう!
(Β版非公開)