- お役立ち記事
- A must-see for process engineers in the semiconductor manufacturing industry! How to improve resist film uniformity using spin coating technology
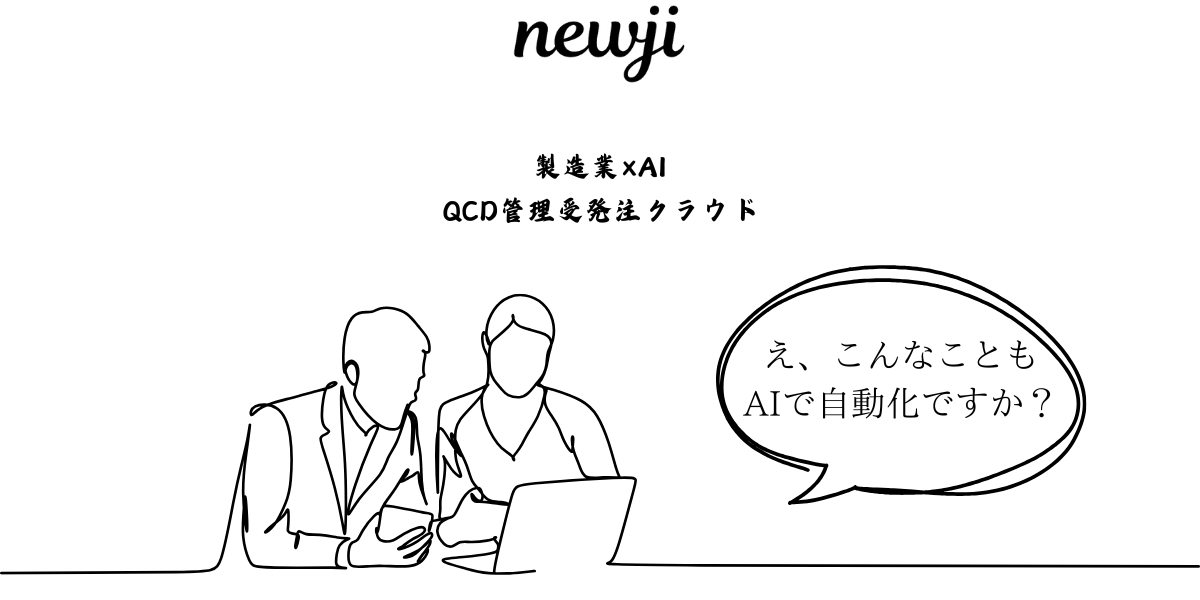
A must-see for process engineers in the semiconductor manufacturing industry! How to improve resist film uniformity using spin coating technology
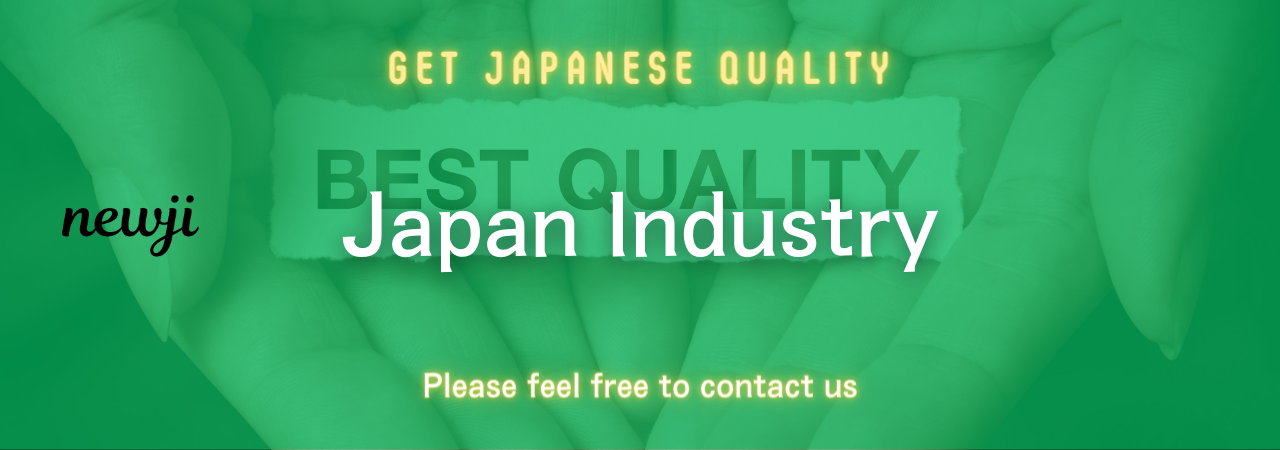
目次
Understanding Spin Coating Technology
Spin coating is a critical process in semiconductor manufacturing, especially when it comes to applying resist films uniformly over substrates.
The method involves depositing a liquid solution onto a spinning surface, where the centripetal force causes the solution to spread out and form a thin, even layer.
The thickness of the layer can be finely controlled by adjusting parameters such as the spin speed, spin time, and solution viscosity, making spin coating a versatile technique for various applications.
The uniformity of resist films is crucial for the precision and functionality of semiconductor devices.
Inconsistencies can lead to defects in the microscopic patterns etched onto silicon wafers, affecting the performance and yield of the final products.
For process engineers, understanding the nuances of spin coating technology is vital to enhancing resist film uniformity and, consequently, the quality of semiconductor components.
Key Parameters for Film Uniformity
Achieving optimal film uniformity requires careful management of multiple parameters during the spin coating process.
Some of the most influential factors include the viscosity of the resist solution, the spin speed, and the duration of spinning.
Resist Solution Viscosity
The viscosity of the resist solution directly impacts how it behaves when subjected to centrifugal forces.
A higher viscosity solution tends to form thicker films, while lower viscosity can help achieve thinner films.
Process engineers must select the appropriate viscosity to match the desired film thickness, taking into account the initial concentration of the resist and any solvent evaporation that may occur during spinning.
Spin Speed
Spin speed is a critical parameter that significantly affects film thickness and uniformity.
Higher speeds generally lead to thinner films as the increased centrifugal force spreads the resist more thoroughly across the substrate.
However, too high a speed can introduce shear forces that lead to non-uniformities or defects.
Process engineers must find a balance where the speed is enough to ensure uniform coverage without compromising the integrity of the resist layer.
Spin Time
The duration of spinning, or spin time, is another crucial aspect that influences resist film uniformity.
Longer spin times allow more time for the resist to level out and for solvent evaporation to occur, potentially leading to a more uniform film.
Yet, there is a trade-off as excessive spinning can also lead to over-thinning and edge bead formation, where excess material accumulates at the edges of the substrate.
Advanced Techniques for Improved Uniformity
In addition to traditional spin coating parameters, various advanced techniques can further enhance resist film uniformity.
These techniques include multi-stage spin coating, controlled atmosphere processing, and using anti-static measures.
Multi-Stage Spin Coating
Multi-stage spin coating involves varying the spin speed or duration in phases, rather than relying on a single, constant spin condition.
This approach can help mitigate issues like edge beading and ensures that the film is evenly distributed even on substrates with challenging geometries.
By implementing a gradual increase or decrease in spin speed, process engineers can tailor the film formation process to achieve better uniformity.
Controlled Atmosphere Processing
Humidity and temperature are environmental factors that can significantly affect the evaporation rate of solvents within the resist solution.
By conducting the spin coating process in a controlled atmosphere, process engineers can minimize variations caused by environmental changes.
This control leads to more consistent results and reduces the likelihood of defects that arise from uneven solvent evaporation.
Anti-Static Measures
Static electricity can attract particles and cause irregularities on the resist film.
Implementing anti-static measures, such as ionizing air guns or conductive work surfaces, can help minimize these unwanted effects.
This practice is particularly important in cleanroom environments where even microscopic particles can lead to significant defects in semiconductor devices.
Monitoring and Quality Control
To ensure that the spin coating process consistently yields uniform resist films, ongoing monitoring and quality control are essential.
Process engineers should regularly use techniques such as ellipsometry or profilometry to measure film thickness and uniformity across wafers.
Ellipsometry
Ellipsometry is a non-destructive optical technique that measures the change in polarization as light reflects off a thin film surface.
By analyzing these changes, engineers can determine the film thickness with high precision.
It offers the advantage of providing rapid and accurate measurements, making it ideal for use in quality control during semiconductor manufacturing.
Profilometry
Profilometry involves scanning the film surface with a stylus or optical sensor to profile its topology.
This technique allows engineers to detect surface irregularities, such as edge beads or thickness variations, and make necessary adjustments to the spin coating process.
Regular profilometry checks ensure that any deviations from desired specifications are caught and corrected promptly.
Conclusion
Spin coating is a sophisticated yet essential technique in the production of semiconductor devices.
By mastering the control of parameters such as viscosity, spin speed, and time, and employing advanced techniques like multi-stage coating and controlled atmosphere processing, process engineers can significantly enhance resist film uniformity.
Continual monitoring through ellipsometry and profilometry ensures consistent quality and helps maintain the high standards required in the semiconductor manufacturing industry.
Implementing these strategies allows process engineers to optimize their manufacturing processes, ultimately leading to higher-quality and more reliable semiconductor products.
資料ダウンロード
QCD調達購買管理クラウド「newji」は、調達購買部門で必要なQCD管理全てを備えた、現場特化型兼クラウド型の今世紀最高の購買管理システムとなります。
ユーザー登録
調達購買業務の効率化だけでなく、システムを導入することで、コスト削減や製品・資材のステータス可視化のほか、属人化していた購買情報の共有化による内部不正防止や統制にも役立ちます。
NEWJI DX
製造業に特化したデジタルトランスフォーメーション(DX)の実現を目指す請負開発型のコンサルティングサービスです。AI、iPaaS、および先端の技術を駆使して、製造プロセスの効率化、業務効率化、チームワーク強化、コスト削減、品質向上を実現します。このサービスは、製造業の課題を深く理解し、それに対する最適なデジタルソリューションを提供することで、企業が持続的な成長とイノベーションを達成できるようサポートします。
オンライン講座
製造業、主に購買・調達部門にお勤めの方々に向けた情報を配信しております。
新任の方やベテランの方、管理職を対象とした幅広いコンテンツをご用意しております。
お問い合わせ
コストダウンが利益に直結する術だと理解していても、なかなか前に進めることができない状況。そんな時は、newjiのコストダウン自動化機能で大きく利益貢献しよう!
(Β版非公開)