- お役立ち記事
- A must-see for processing engineers in the precision machinery industry! How to finish complex shaped parts with high precision using EDM (Electro Discharge Machine)
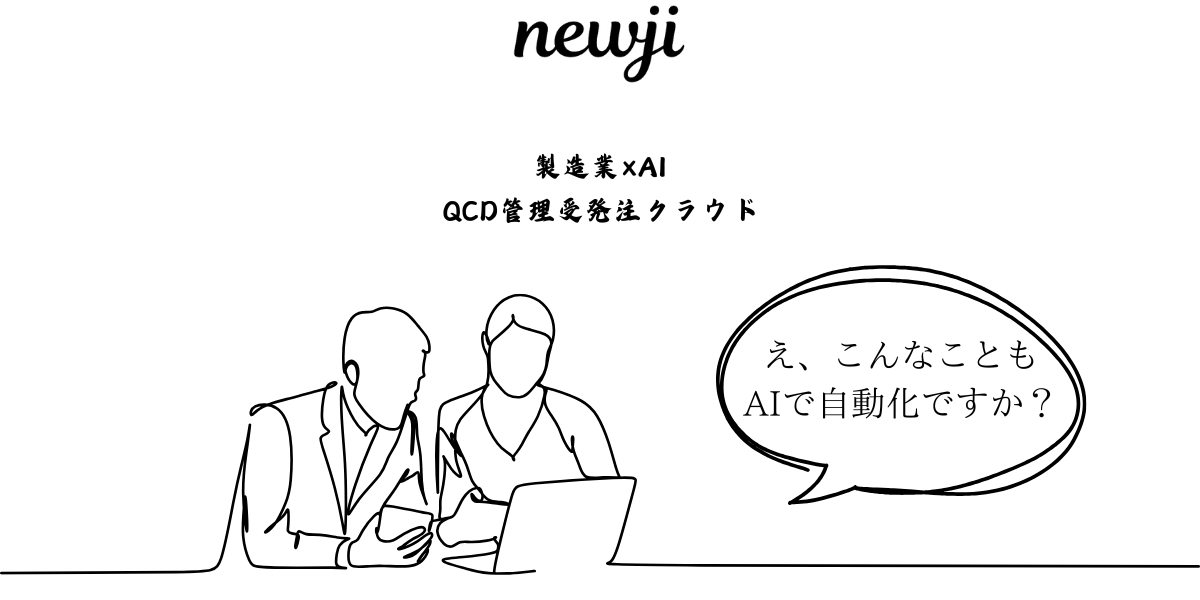
A must-see for processing engineers in the precision machinery industry! How to finish complex shaped parts with high precision using EDM (Electro Discharge Machine)
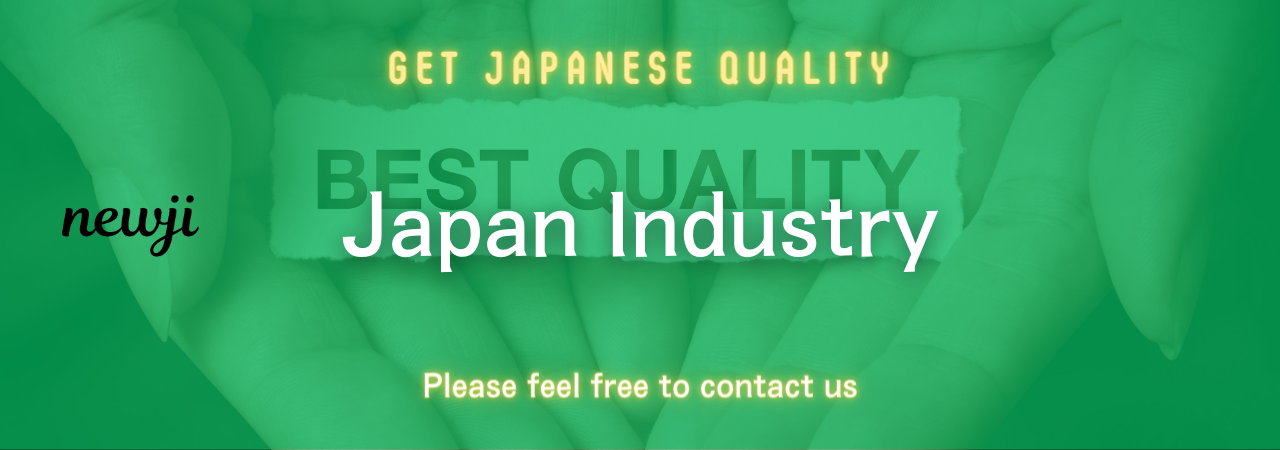
目次
Introduction to EDM
In the precision machinery industry, creating complex parts with extreme accuracy is an essential task.
To achieve this, engineers rely on a variety of methods and technologies, one of the most effective being the Electro Discharge Machine (EDM).
This tool is particularly beneficial for finishing parts with intricate shapes and high precision.
In this article, we’ll delve into how EDM works and why it is an indispensable tool for processing engineers dealing with complex shaped parts.
Understanding the Basics of EDM
EDM is a non-traditional machining process that removes material from a workpiece using electrical discharges or sparks.
These controlled electric discharges occur between an electrode and the workpiece submerged in a dielectric fluid, typically deionized water or oil.
The sparks generated by the EDM process melt and vaporize small amounts of material from the workpiece, allowing precise shaping of parts with complex geometries.
Types of EDM
There are two primary types of EDM: Sink EDM and Wire EDM.
Each has its own unique applications and advantages in the precision machining of complex parts.
1. **Sink EDM**: Also known as die-sinking EDM or cavity-type EDM, this method involves a shaped electrode that is incrementally lowered into the workpiece to produce a cavity that matches the electrode’s form.
It’s highly effective for creating intricate shapes and cavities, making it ideal for mold and die-making industries.
2. **Wire EDM**: This method uses a thin wire as the electrode to cut through metal workpieces.
Wire EDM is perfect for cutting intricate patterns or shapes in hard materials and is widely used for creating parts with tight tolerances and complex geometries.
Advantages of EDM in Precision Machining
EDM offers several significant advantages over traditional machining methods, particularly when it comes to processing parts with complex shapes and high precision.
1. Ability to Machine Hard Materials
One of the biggest advantages of EDM is its ability to work with very hard materials such as titanium, hardened steel, and carbides.
Traditional machining techniques can struggle with these materials, but EDM can effectively shape them without causing structural damage or stress.
2. Precision and Accuracy
EDM provides exceptional precision and accuracy, essential for industries where exact specifications are critical.
The process allows for extremely small tolerances and intricate detailing, making EDM ideal for aerospace, medical, and automotive industries.
3. No Mechanical Stresses
Unlike traditional machining methods that involve cutting tools and high pressure, EDM is a contactless technique.
This means there is no mechanical stress placed on the workpiece, which reduces the risk of warping or deformation, particularly with intricate or delicate parts.
4. Complex Geometry Capabilities
EDM excels in producing complex shapes that are difficult or impossible with conventional machining.
Because the process relies on electrical discharges rather than physical contact, it’s highly effective in creating sharp corners, deep cavities, and fine details.
Optimizing EDM Processes for Complex Shaped Parts
To maximize the effectiveness of EDM for machining complex parts, processing engineers should consider several key factors.
1. Electrode Design
The design of the electrode is crucial in sink EDM.
Engineers must carefully plan the electrode shape and material to ensure it can produce the desired cavity or feature on the workpiece.
Using advanced materials such as graphite or copper-tungsten can enhance performance and reduce wear.
2. Dielectric Fluid Selection
The choice of dielectric fluid impacts the quality and efficiency of the EDM process.
It serves as an insulating medium and helps remove eroded particles.
Depending on the application, deionized water or specific dielectric oils are selected to optimize spark generation and cooling.
3. Parameters and Controls
Adjusting the electrical parameters, such as current intensity, pulse duration, and discharge frequency, is critical for achieving the desired outcomes.
Accurate control over these variables helps manage surface finish and maintain dimensional accuracy.
Challenges and Considerations
While EDM boasts numerous advantages, it is not without challenges that engineers must navigate to achieve the best results when machining complex parts.
1. Slow Material Removal Rates
Compared to traditional machining, EDM is relatively slow in removing material.
This can result in longer processing times, particularly for large components.
Engineers need to balance precision needs with productivity goals when planning jobs.
2. Electrode Wear
Electrode wear is an inherent challenge in sink EDM, where the electrode gradually deteriorates during the process.
Selecting materials that minimize wear and planning for electrode replacement is a necessary part of the process.
3. Surface Roughness
While EDM can provide high precision, achieving ultra-smooth finishes can be challenging.
Multiple passes and finishing operations might be needed, especially when surface quality is crucial.
Conclusion
EDM is an indispensable tool for processing engineers in the precision machinery industry, especially when dealing with complex shaped parts requiring high precision.
By offering unparalleled accuracy and the ability to work with hard materials, EDM allows for innovative designs that push the boundaries of what is possible in manufacturing.
Understanding and optimizing variables such as electrode design, dielectric fluid selection, and electrical parameters are essential for achieving the best results.
Despite challenges such as slow material removal rates and electrode wear, EDM remains a powerful method to meet the demands of modern engineering and precision manufacturing.
資料ダウンロード
QCD調達購買管理クラウド「newji」は、調達購買部門で必要なQCD管理全てを備えた、現場特化型兼クラウド型の今世紀最高の購買管理システムとなります。
ユーザー登録
調達購買業務の効率化だけでなく、システムを導入することで、コスト削減や製品・資材のステータス可視化のほか、属人化していた購買情報の共有化による内部不正防止や統制にも役立ちます。
NEWJI DX
製造業に特化したデジタルトランスフォーメーション(DX)の実現を目指す請負開発型のコンサルティングサービスです。AI、iPaaS、および先端の技術を駆使して、製造プロセスの効率化、業務効率化、チームワーク強化、コスト削減、品質向上を実現します。このサービスは、製造業の課題を深く理解し、それに対する最適なデジタルソリューションを提供することで、企業が持続的な成長とイノベーションを達成できるようサポートします。
オンライン講座
製造業、主に購買・調達部門にお勤めの方々に向けた情報を配信しております。
新任の方やベテランの方、管理職を対象とした幅広いコンテンツをご用意しております。
お問い合わせ
コストダウンが利益に直結する術だと理解していても、なかなか前に進めることができない状況。そんな時は、newjiのコストダウン自動化機能で大きく利益貢献しよう!
(Β版非公開)