- お役立ち記事
- A must-see for processing engineers in the precision machinery industry! Practical guidelines for ultra-precision cutting using diamond tools
月間76,176名の
製造業ご担当者様が閲覧しています*
*2025年3月31日現在のGoogle Analyticsのデータより
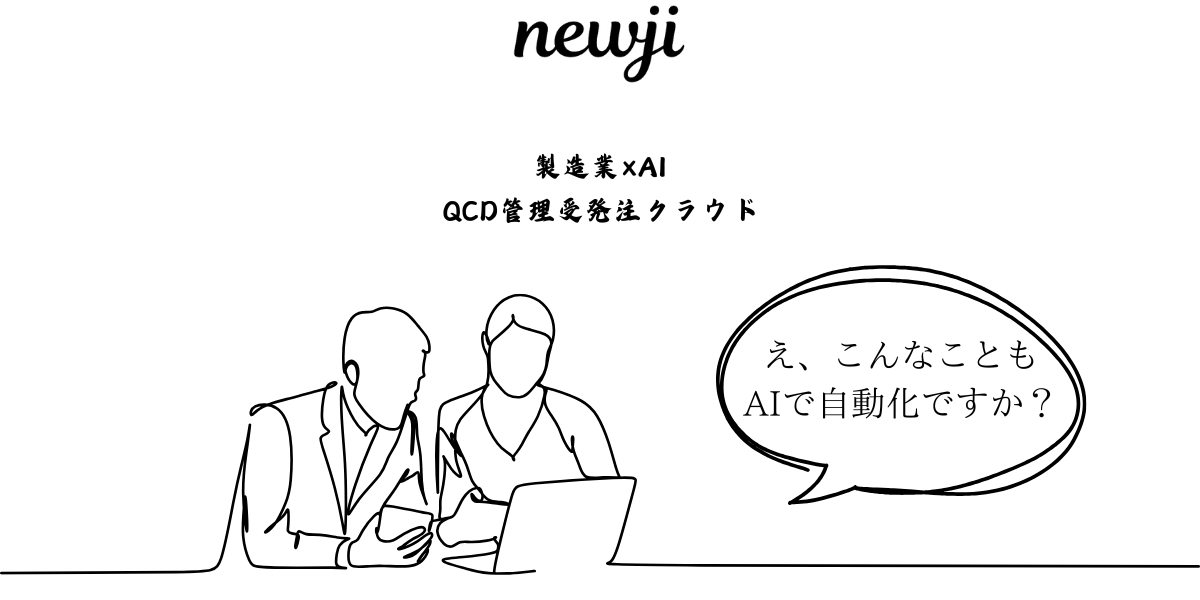
A must-see for processing engineers in the precision machinery industry! Practical guidelines for ultra-precision cutting using diamond tools
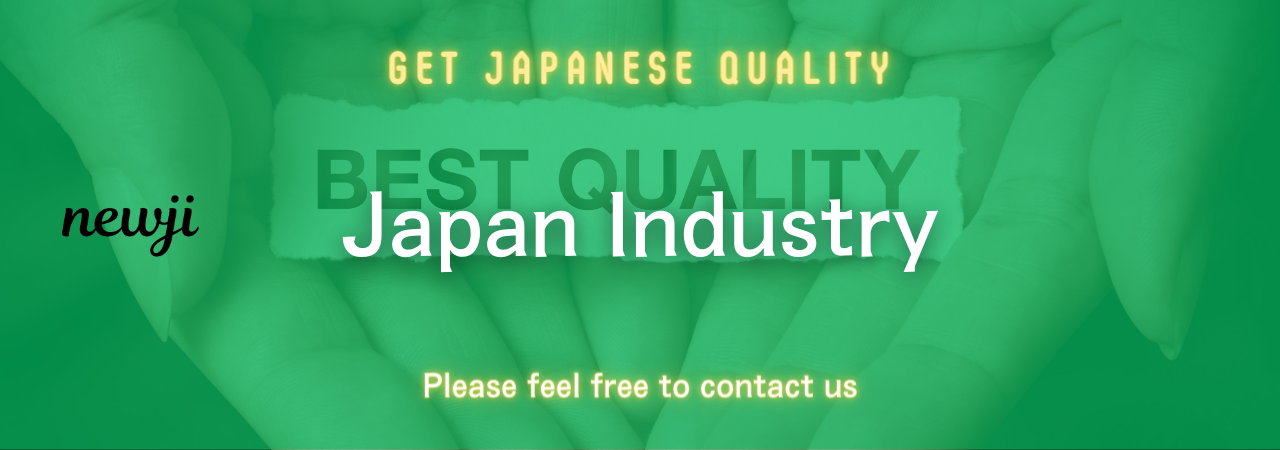
目次
Introduction to Ultra-Precision Cutting
Ultra-precision cutting is a critical process in the precision machinery industry, particularly when working with demanding applications like the manufacturing of optical components, electronic devices, and aerospace components.
It involves using highly accurate machinery and methods to achieve tight tolerances and exceptional surface finishes.
One of the key tools used in ultra-precision cutting is the diamond tool due to its unrivaled hardness and cutting ability.
By understanding and implementing proper techniques, engineers can optimize their processes, maximize tool life, and achieve superior results.
Why Use Diamond Tools?
Diamond tools are preferred in ultra-precision cutting for several reasons.
First, diamonds are the hardest known material, which enables them to easily cut through hard materials without excessive wear.
Their hardness also allows for the production of sharp cutting edges, which is crucial for achieving smooth and accurate cuts.
Apart from their durability and cutting ability, diamond tools can be manufactured with extremely precise geometries, enabling more controlled and consistent machining processes.
This precision is essential in industries where even the slightest deviation can lead to suboptimal performance or failure of the final product.
The Basics of Ultra-Precision Cutting
Choosing the Right Diamond Tool
Selecting the appropriate diamond tool is the first step in ensuring successful ultra-precision cutting.
When choosing a diamond tool, engineers should consider factors such as the material to be machined, the desired surface finish, and the cutting parameters.
Different materials will have different requirements, and understanding their properties will assist in tool selection.
For example, ultra-precision machining of softer materials may require tools with finer diamond grains, while harder materials might necessitate coarser grains.
Additionally, the tool’s geometry must align with the specific application requirements.
Machine Setup and Calibration
Proper machine setup is key to achieving ultra-precision results.
Machines used in precision cutting must be meticulously calibrated and maintained to ensure accuracy and repeatability.
This includes verifying the machine’s kinematic integrity, aligning the spindle, and ensuring smooth motion control.
Keeping the machine environment clean and thermally stable is also crucial, as temperature variations can affect the machining process and final results.
Controlling Cutting Parameters
Cutting parameters—like feed rate, depth of cut, and cutting speed—play a significant role in the success of an ultra-precision cutting operation.
Engineers must carefully control these parameters to strike a balance between tool life and production efficiency.
Excessively high speeds or deep cuts can lead to increased wear and tear on the diamond tool, whereas overly conservative settings may decrease productivity.
Continual monitoring and adjustment of these parameters based on real-time feedback are vital for optimizing the process.
Techniques for Ultra-Precision Cutting
Single-Point Diamond Turning (SPDT)
Single-Point Diamond Turning is a popular technique for achieving ultra-smooth surfaces and intricate shapes.
SPDT uses a single diamond-tipped tool to cut the workpiece with extreme accuracy.
This technique is ideal for machining spherical, aspherical, and freeform surfaces, which are common in optical lens manufacturing.
SPDT requires a robust understanding of material behavior, tool geometry, and cutting parameters to achieve optimal outcomes.
Micro-Milling and Micro-Grinding
Micro-milling and micro-grinding are techniques that employ diamond tools to produce intricate and finely detailed components.
These methods are especially useful in creating micro-scale features that are not achievable through traditional machining techniques.
Micro-milling uses rotating diamond tools to machine small features, while micro-grinding employs abrasive processes to achieve polished surfaces.
Both techniques require an in-depth knowledge of the specific machine capabilities and cutting dynamics.
Ultra-Precision Grinding and Lapping
Ultra-precision grinding and lapping are abrasive techniques used for achieving mirror-like finishes and precise dimensions.
These processes use diamond abrasives to remove material at micro-levels, ensuring excellent surface quality.
Ultra-precision lapping is particularly beneficial for producing ultra-flat surfaces and achieving tight tolerances.
It involves moving the workpiece across a rotating planar surface embedded with diamond abrasives.
Best Practices for Optimizing Performance
Regular Tool Maintenance
Regular maintenance of diamond tools is vital to sustaining their cutting performance.
Cleaning tools after each use, inspecting them for wear, and replacing them when necessary will help prolong their lifespan and ensure consistent results.
Implementing a tool maintenance routine can also identify potential issues before they impact production.
Monitoring and Feedback Systems
Incorporating monitoring systems within the machining process allows engineers to track performance metrics in real-time.
These systems can detect anomalies such as excessive tool wear, vibrations, and temperature changes, providing valuable data for process adjustments.
Utilizing such feedback promotes timely interventions that prevent defects and improve overall precision.
Training and Continuous Improvement
Investing in employee training and fostering a culture of continuous improvement are essential for maintaining high standards in ultra-precision cutting.
Training ensures that operators understand the operational nuances of the machinery and are equipped to make informed decisions during the cutting process.
Encouraging knowledge sharing and embracing the latest technological advancements can further enhance process efficiency and quality.
Conclusion
Ultra-precision cutting using diamond tools represents a cornerstone of modern precision machining.
By selecting the right tools, controlling parameters, and applying the appropriate techniques, engineers can achieve exceptional results.
Continual maintenance, real-time monitoring, and effective training are fundamental for maintaining high performance and pushing the boundaries of what’s possible in the precision machinery industry.
Ultimately, adhering to these practical guidelines will empower engineers to meet the ever-evolving demands of advanced manufacturing applications.
資料ダウンロード
QCD管理受発注クラウド「newji」は、受発注部門で必要なQCD管理全てを備えた、現場特化型兼クラウド型の今世紀最高の受発注管理システムとなります。
ユーザー登録
受発注業務の効率化だけでなく、システムを導入することで、コスト削減や製品・資材のステータス可視化のほか、属人化していた受発注情報の共有化による内部不正防止や統制にも役立ちます。
NEWJI DX
製造業に特化したデジタルトランスフォーメーション(DX)の実現を目指す請負開発型のコンサルティングサービスです。AI、iPaaS、および先端の技術を駆使して、製造プロセスの効率化、業務効率化、チームワーク強化、コスト削減、品質向上を実現します。このサービスは、製造業の課題を深く理解し、それに対する最適なデジタルソリューションを提供することで、企業が持続的な成長とイノベーションを達成できるようサポートします。
製造業ニュース解説
製造業、主に購買・調達部門にお勤めの方々に向けた情報を配信しております。
新任の方やベテランの方、管理職を対象とした幅広いコンテンツをご用意しております。
お問い合わせ
コストダウンが利益に直結する術だと理解していても、なかなか前に進めることができない状況。そんな時は、newjiのコストダウン自動化機能で大きく利益貢献しよう!
(β版非公開)