- お役立ち記事
- A must-see for production engineers in the auto parts manufacturing industry! Cost reduction and product strength improvement using cold forging technology
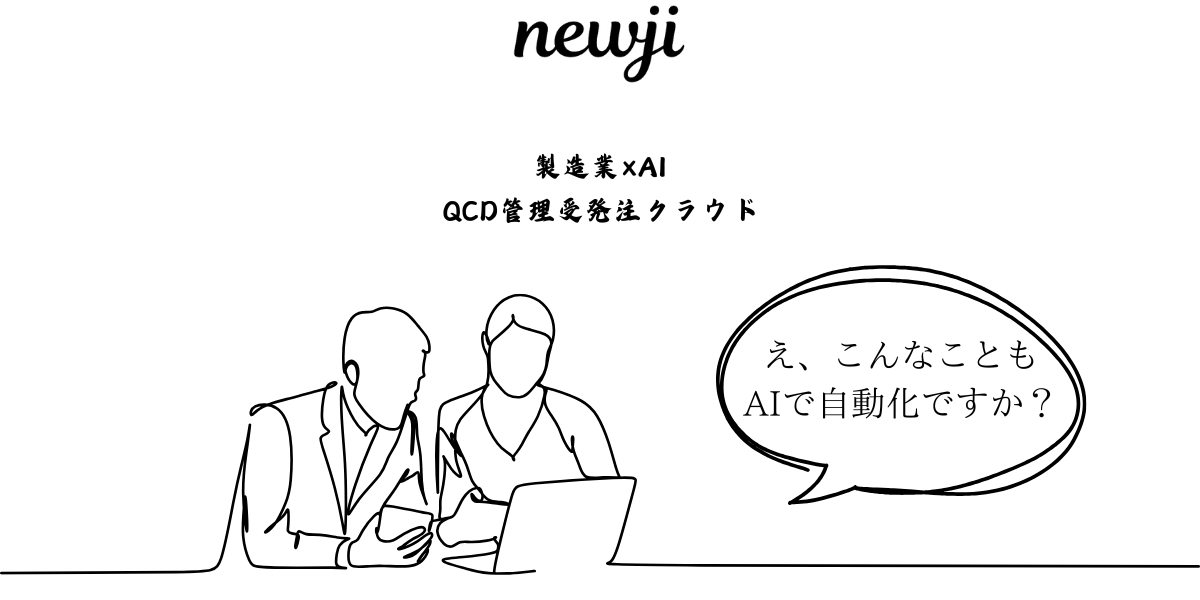
A must-see for production engineers in the auto parts manufacturing industry! Cost reduction and product strength improvement using cold forging technology
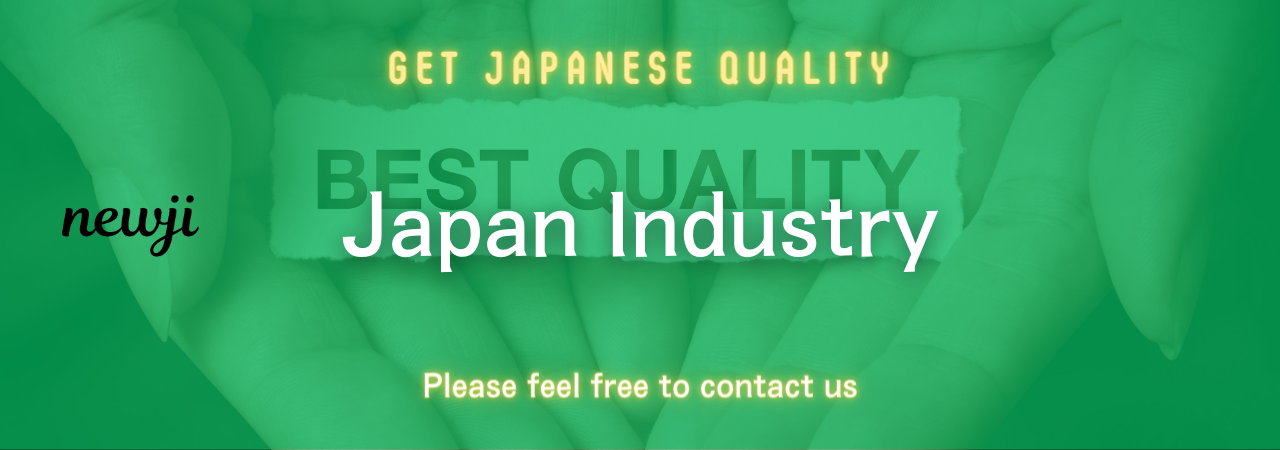
目次
Introduction to Cold Forging Technology
The auto parts manufacturing industry is constantly in search of methods to reduce costs while maintaining or enhancing product strength and quality.
One technology that offers promising solutions is cold forging.
This metalworking process stands out distinctively due to its efficiency in material use and its ability to produce extremely durable components.
In this article, we will explore how cold forging can help production engineers achieve cost reduction and improve product strength.
What is Cold Forging?
Cold forging, often referred to as cold forming, involves deforming metal at room temperature to create precise shapes.
This process differs from hot forging where metal is heated before being shaped.
Cold forging typically uses punches and dies to alter the form of metal, providing a high degree of dimensional accuracy and surface finish.
Key materials used in cold forging include aluminum, brass, and steel, making it an ideal choice for auto parts manufacturing.
The Process of Cold Forging
The cold forging process involves several critical steps.
To begin with, the metal is prepared and positioned in a die.
A punch then forcibly shapes the metal into the desired form.
Depending on the complexity of the part, multiple strokes of the punch might be necessary.
Once the piece is formed, it undergoes finishing processes to remove any surface imperfections and ensure dimensional accuracy.
Advantages of Cold Forging
Cold forging offers numerous advantages that are particularly beneficial in the auto parts manufacturing sector.
Firstly, the process maximizes material utilization, reducing waste considerably.
This leads to cost savings as less raw material is needed to produce each part.
Secondly, cold forging considerably enhances the mechanical strength of the metal.
The process of deforming metal at room temperature leads to work hardening, which increases the material’s fatigue resistance and tensile strength.
This results in more durable parts that can better withstand the demands of automotive applications.
Additionally, cold forging ensures high precision and excellent surface finish, reducing the need for additional machining.
This decreases production time and labor costs, further contributing to cost reduction.
Applications in the Auto Parts Industry
Cold forging finds extensive applications in producing various auto parts.
Common components include gears, bolts, nuts, and axles.
These parts benefit greatly from the strength and precision offered by cold forging.
Moreover, as vehicle designs become more complex with an emphasis on efficiency and performance, cold forging provides the flexibility required to produce intricate and lightweight components.
This adaptability makes it an invaluable asset in the design and manufacturing of modern automotive parts.
Cost Reduction through Material Efficiency
One of the leading benefits of cold forging is its efficient use of materials.
The near-net shape forming means there is minimal excess metal, significantly cutting down waste.
For production engineers focused on reducing costs, this material efficiency translates directly into lower material expenses.
The reduced need for machining and finishing operations also contributes to cost savings.
Precision in cold forging eliminates the reliance on costly and time-intensive post-processing methods, streamlining production and minimizing labor costs.
Improvement in Product Strength
The enhancement in product strength is another pivotal advantage of cold forging.
As the process involves deforming metal without the application of heat, the resultant components are inherently stronger.
This strength is a critical factor in the longevity and reliability of automotive parts, which are subjected to various stresses and strains during operation.
Furthermore, the enhanced mechanical properties provided by cold forging align with the industry’s push towards creating longer-lasting, efficient vehicles.
Parts that maintain structural integrity over extended periods contribute to reduced maintenance and repair costs in the long term.
Conclusion
Cold forging technology emerges as a game-changer for production engineers in the auto parts manufacturing industry.
Its capacity for cost savings and the enhancement of product strength offers a dual benefit that cannot be overlooked in today’s competitive market.
By integrating cold forging into manufacturing practices, companies can not only reduce expenses but also produce superior parts that meet the high demands of automotive applications.
As the industry continues to evolve, embracing such advanced technologies will be paramount for sustainability and growth.
資料ダウンロード
QCD調達購買管理クラウド「newji」は、調達購買部門で必要なQCD管理全てを備えた、現場特化型兼クラウド型の今世紀最高の購買管理システムとなります。
ユーザー登録
調達購買業務の効率化だけでなく、システムを導入することで、コスト削減や製品・資材のステータス可視化のほか、属人化していた購買情報の共有化による内部不正防止や統制にも役立ちます。
NEWJI DX
製造業に特化したデジタルトランスフォーメーション(DX)の実現を目指す請負開発型のコンサルティングサービスです。AI、iPaaS、および先端の技術を駆使して、製造プロセスの効率化、業務効率化、チームワーク強化、コスト削減、品質向上を実現します。このサービスは、製造業の課題を深く理解し、それに対する最適なデジタルソリューションを提供することで、企業が持続的な成長とイノベーションを達成できるようサポートします。
オンライン講座
製造業、主に購買・調達部門にお勤めの方々に向けた情報を配信しております。
新任の方やベテランの方、管理職を対象とした幅広いコンテンツをご用意しております。
お問い合わせ
コストダウンが利益に直結する術だと理解していても、なかなか前に進めることができない状況。そんな時は、newjiのコストダウン自動化機能で大きく利益貢献しよう!
(Β版非公開)