- お役立ち記事
- A must-see for production engineers in the ceramic insulator manufacturing industry! Manufacturing method to achieve both heat resistance and insulation performance
A must-see for production engineers in the ceramic insulator manufacturing industry! Manufacturing method to achieve both heat resistance and insulation performance
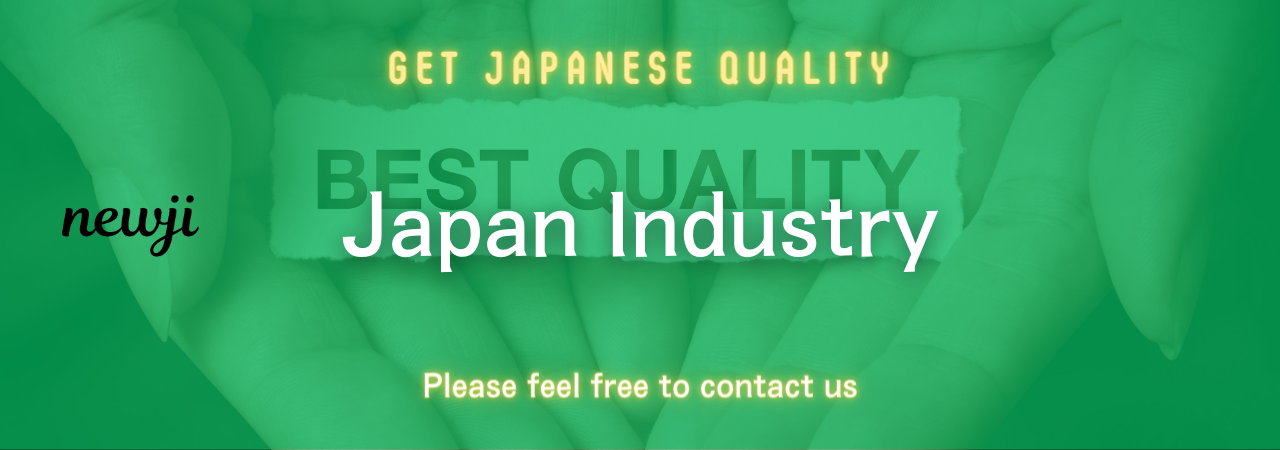
目次
Understanding Ceramic Insulators
Ceramic insulators are a crucial component in various industrial applications, particularly where heat resistance and electrical insulation are required.
These insulators are typically used to prevent the passage of electricity along unwanted paths, ensuring safety and efficiency in electrical systems.
In industries such as electronics, power generation, and transportation, the demand for high-performance ceramic insulators is ever-increasing.
Ceramics are inherently capable of withstanding high temperatures while preventing electrical conductivity.
However, manufacturing ceramic insulators that achieve optimal heat resistance and excellent insulation performance requires a thorough understanding of materials and production processes.
Materials Used in Ceramic Insulator Manufacturing
The choice of materials significantly influences the performance characteristics of ceramic insulators.
Commonly used materials include alumina, zirconia, silicon carbide, and beryllium oxide.
Each material offers unique properties that contribute to the insulator’s overall performance.
– **Alumina:** Known for its excellent electrical insulation and thermal conductivity, alumina is one of the most widely used materials in ceramic insulators.
– **Zirconia:** Offers high fracture toughness and thermal resistance, making it ideal for applications exposed to extreme temperatures.
– **Silicon Carbide:** Valued for its high strength and thermal conductivity, silicon carbide is often used in demanding environments.
– **Beryllium Oxide:** Provides superior heat resistance and excellent dielectric properties, though its use is limited due to health concerns.
Selecting the right material depends on the specific requirements of the intended application and environmental conditions the insulator will face.
The Manufacturing Process
The process of manufacturing ceramic insulators involves several critical stages, each of which plays a vital role in ensuring the final product meets desired specifications.
1. Material Preparation
This stage involves selecting the appropriate raw materials and preparing them for further processing.
The materials are typically mixed with additives that enhance specific properties, such as strength and thermal conductivity.
The mixture is then ground to a fine powder to ensure uniformity and ease of shaping.
2. Shaping
Once the materials are prepared, they are formed into the desired shape using various methods.
Common shaping techniques include extrusion, injection molding, and pressing.
The choice of method depends on the complexity and size of the insulator design.
Advanced computer-aided design (CAD) tools assist engineers in crafting precise and intricate shapes tailored to their applications.
3. Drying
After shaping, the ceramic forms need to be dried to remove moisture, which can affect the integrity of the pieces during firing.
Controlled drying environments help prevent cracking and warping, ensuring the insulators maintain their designed dimensions.
4. Sintering
Sintering is a critical stage where the ceramic pieces are subjected to high temperatures in a kiln.
This process binds the particles together, enhancing the mechanical strength and thermal stability of the insulator.
Careful control of sintering temperatures and duration ensures the insulators achieve the desired density and structural integrity.
5. Finishing
Once sintering is complete, the insulators undergo finishing processes to achieve the final specifications.
This stage may include grinding, polishing, and coating to enhance surface properties and meet precise technical requirements.
Quality control measures are implemented throughout this process to ensure each insulator meets the rigorous standards expected in industrial applications.
Achieving Optimal Heat Resistance and Insulation
To achieve both heat resistance and insulation performance, manufacturers focus on several key aspects throughout the production process:
– **Material Selection:** Choosing materials with inherent thermal and dielectric properties is fundamental.
Advanced research into new ceramic compositions and nano-materials continues to expand the possibilities for improved performance.
– **Process Control:** Maintaining precise control over each stage of manufacturing ensures consistent quality.
Variables such as temperature, pressure, and time are meticulously monitored to optimize the properties of the final product.
– **Innovative Techniques:** Adoption of cutting-edge technologies like 3D printing and laser sintering enables the production of complex geometries and enhanced material properties.
These techniques can significantly improve both the efficiency and performance of ceramic insulators.
– **Post-Manufacturing Testing:** Rigorous testing methods such as thermal analysis, dielectric breakdown testing, and mechanical stress tests validate the insulators’ capabilities.
These tests provide assurances that the insulators will perform reliably under the specified conditions.
Challenges and Innovations in the Industry
While the fundamental principles of ceramic insulator manufacturing remain consistent, the industry faces ongoing challenges and opportunities for innovation.
Advancements in material science and engineering open doors to new possibilities, pushing the boundaries of what ceramic insulators can achieve.
One of the primary challenges is balancing cost efficiency with performance.
Research into cost-effective manufacturing processes without compromising on quality is vital for remaining competitive in the market.
Moreover, sustainability has become a focal point for the industry.
Developing eco-friendly materials and energy-efficient production techniques align with the growing demand for environmentally conscious practices.
The pursuit of improved performance has led to the exploration of nano-ceramics and composite materials.
These innovative materials hold the potential to provide even greater heat resistance and insulation properties, paving the way for next-generation insulators.
Conclusion
The manufacturing of ceramic insulators is a complex but rewarding process that requires a meticulous approach to material selection and production methods.
As the industry continues to evolve, manufacturers are pushed to innovate and refine their processes to meet the increasing demands for performance and sustainability.
By understanding the materials and technologies involved, production engineers can significantly enhance the capabilities of ceramic insulators, ensuring they remain indispensable components across a wide array of applications.
資料ダウンロード
QCD調達購買管理クラウド「newji」は、調達購買部門で必要なQCD管理全てを備えた、現場特化型兼クラウド型の今世紀最高の購買管理システムとなります。
ユーザー登録
調達購買業務の効率化だけでなく、システムを導入することで、コスト削減や製品・資材のステータス可視化のほか、属人化していた購買情報の共有化による内部不正防止や統制にも役立ちます。
NEWJI DX
製造業に特化したデジタルトランスフォーメーション(DX)の実現を目指す請負開発型のコンサルティングサービスです。AI、iPaaS、および先端の技術を駆使して、製造プロセスの効率化、業務効率化、チームワーク強化、コスト削減、品質向上を実現します。このサービスは、製造業の課題を深く理解し、それに対する最適なデジタルソリューションを提供することで、企業が持続的な成長とイノベーションを達成できるようサポートします。
オンライン講座
製造業、主に購買・調達部門にお勤めの方々に向けた情報を配信しております。
新任の方やベテランの方、管理職を対象とした幅広いコンテンツをご用意しております。
お問い合わせ
コストダウンが利益に直結する術だと理解していても、なかなか前に進めることができない状況。そんな時は、newjiのコストダウン自動化機能で大きく利益貢献しよう!
(Β版非公開)