- お役立ち記事
- A must-see for production engineers in the cosmetics manufacturing industry! Techniques to improve productivity by increasing automation in the filling process
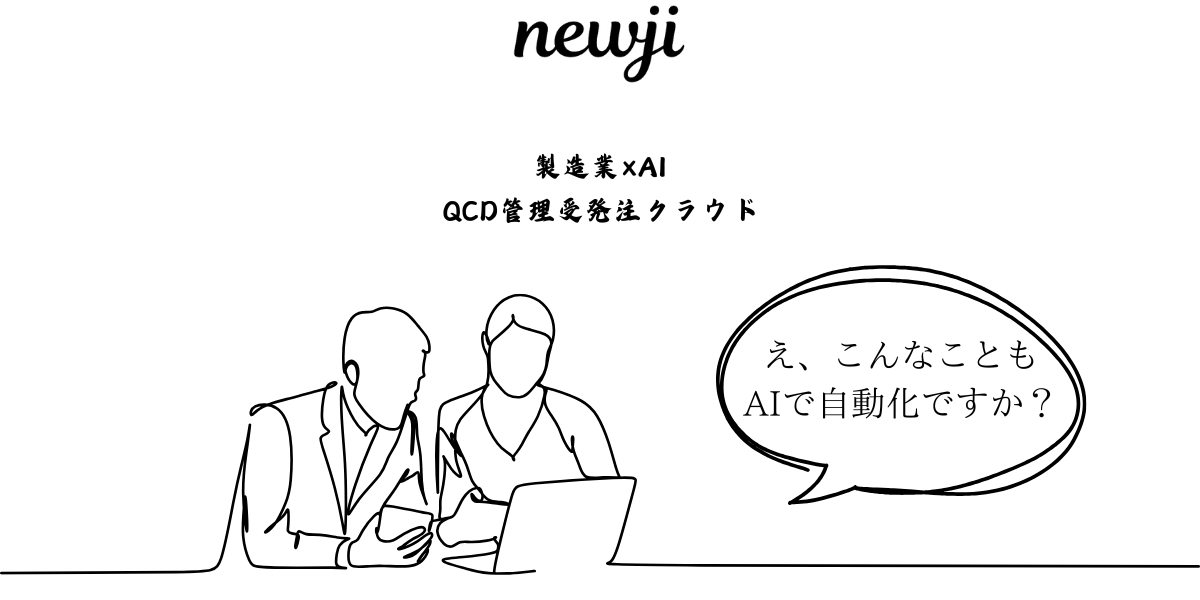
A must-see for production engineers in the cosmetics manufacturing industry! Techniques to improve productivity by increasing automation in the filling process
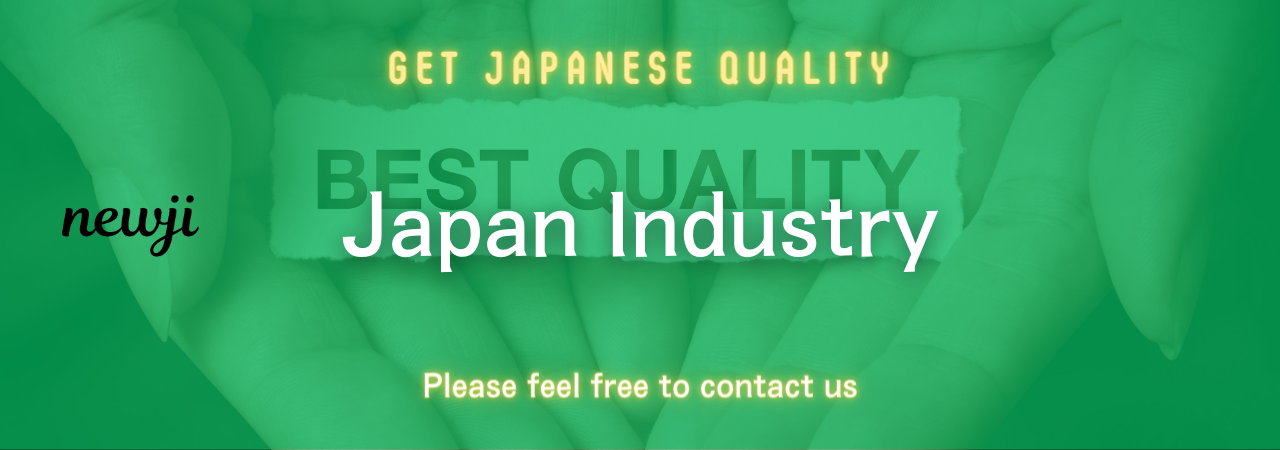
目次
Introduction to Automation in Cosmetics Manufacturing
In the bustling world of cosmetics manufacturing, production engineers constantly seek ways to enhance productivity while maintaining quality.
One area ripe for improvement is the filling process, where automation can bring significant advantages.
Automation in the cosmetics industry helps streamline operations, reduce labor costs, and minimize human error.
By adopting automated systems, companies can ensure faster turnaround times and increased consistency in product quality.
This article will explore key techniques to enhance productivity by boosting automation in the filling process.
The Importance of Automation in the Filling Process
The filling process in cosmetics manufacturing involves dispensing products into containers.
This crucial step ensures that each unit contains the correct volume, consistency, and appearance.
In high-demand scenarios, manual filling can become a bottleneck due to its time-consuming nature and susceptibility to errors.
Automation eliminates these issues by providing continuous, reliable operation.
Robotic machinery and automated systems can precisely measure, fill, and seal containers without the need for constant human intervention.
This increased efficiency can significantly boost production capacity and output.
Techniques for Improving Automation in Filling
1. Integrate Advanced Dispenser Technologies
One core aspect of automation is the dispenser technology used in the filling process.
Advanced dispensers can accurately measure and control the flow of product into containers.
This technology ensures that each unit is filled consistently, reducing waste and improving product quality.
Adopting technologies like servo-driven pumps or peristaltic pumps can provide better control over product dispensing.
These systems can handle a wide range of viscosities, making them versatile for different types of cosmetics.
2. Use Robotics for Precision and Efficiency
Incorporating robotics into the filling process offers precision and reliability.
Robots equipped with vision systems can handle complex filling tasks, like precise alignment of containers and caps.
Their speed and accuracy surpass manual efforts, resulting in higher productivity rates.
Robots also bring flexibility to the production line, allowing quick changes to accommodate different product types and container sizes.
This adaptability is invaluable in a fast-paced industry with diverse product portfolios.
3. Implement Smart Sensors and Data Analytics
Smart sensors play an essential role in enhancing the filling process.
They monitor various parameters such as pressure, temperature, and viscosity to ensure optimal filling conditions.
Data collected from these sensors can be analyzed to identify inefficiencies and potential issues in real-time.
This level of insight allows engineers to make informed decisions for process improvements and troubleshooting.
Data analytics also aids in predictive maintenance, reducing downtimes and unexpected stoppages.
4. Employ Automated Quality Control Systems
Quality control is vital in cosmetics manufacturing to deliver consistently high-standard products.
Automated quality control systems can inspect filled products for irregularities, such as air bubbles or incorrect levels.
These systems use cameras and laser sensors for non-destructive testing, ensuring no product is wasted.
Integrating automated quality control into the production line guarantees that only flawless products reach customers.
This not only saves on costs associated with reworks but also protects brand reputation.
5. Optimize Production Workflow
For automation to truly enhance productivity, optimizing the entire production workflow is essential.
Streamlining processes to minimize idle times and reduce manual interventions can significantly boost productivity.
Using software solutions that integrate and coordinate different stages of production can result in a smooth, continuous flow.
Workflow optimization can also highlight delays and bottlenecks, providing opportunities for further enhancements.
The Benefits of Increased Automation
Investing in automation technologies for the filling process offers numerous benefits.
Firstly, it reduces the need for intensive labor, lowering operational costs in the long run.
With machines operating 24/7, production lines can run continuously, meeting high demands efficiently.
Automation also minimizes human errors, ensuring consistent product quality across all units.
This reliability is crucial in maintaining customer trust and satisfaction in such a quality-sensitive industry.
Moreover, automating the filling process improves workplace safety by reducing manual handling and repetitive tasks that could lead to injuries.
Engineers can focus more on strategic tasks and process improvements, resulting in a more innovative and agile operation.
Overcoming Challenges in Automation Implementation
While the benefits of automation are clear, implementing these systems comes with its challenges.
Initial investment costs can be significant, deterring some manufacturers from adopting automation.
However, the long-term gains in efficiency, quality, and cost savings often outweigh these upfront expenses.
Additionally, transitioning to automated systems requires thorough planning and skilled personnel for maintenance and operation.
Providing training for employees is essential to ensure a smooth transition and maximize the full potential of automated solutions.
Conclusion: Embracing the Future of Cosmetics Manufacturing
As the cosmetics industry continues to evolve, so must the technologies that support it.
Automation in the filling process is not just an option but a necessity for staying competitive and meeting consumer demands.
Production engineers who embrace these advancements will find themselves at the forefront of innovation, leading their companies to greater success.
By implementing these techniques, manufacturers can improve productivity, maintain high-quality standards, and ensure a safer and more efficient workplace.
Automation is the key to unlocking the industry’s full potential, paving the way for a brighter and more sustainable future.
資料ダウンロード
QCD調達購買管理クラウド「newji」は、調達購買部門で必要なQCD管理全てを備えた、現場特化型兼クラウド型の今世紀最高の購買管理システムとなります。
ユーザー登録
調達購買業務の効率化だけでなく、システムを導入することで、コスト削減や製品・資材のステータス可視化のほか、属人化していた購買情報の共有化による内部不正防止や統制にも役立ちます。
NEWJI DX
製造業に特化したデジタルトランスフォーメーション(DX)の実現を目指す請負開発型のコンサルティングサービスです。AI、iPaaS、および先端の技術を駆使して、製造プロセスの効率化、業務効率化、チームワーク強化、コスト削減、品質向上を実現します。このサービスは、製造業の課題を深く理解し、それに対する最適なデジタルソリューションを提供することで、企業が持続的な成長とイノベーションを達成できるようサポートします。
オンライン講座
製造業、主に購買・調達部門にお勤めの方々に向けた情報を配信しております。
新任の方やベテランの方、管理職を対象とした幅広いコンテンツをご用意しております。
お問い合わせ
コストダウンが利益に直結する術だと理解していても、なかなか前に進めることができない状況。そんな時は、newjiのコストダウン自動化機能で大きく利益貢献しよう!
(Β版非公開)