- お役立ち記事
- A must-see for production engineers in the plastic molding industry! Guidelines for achieving high strength joints with ultrasonic welding
A must-see for production engineers in the plastic molding industry! Guidelines for achieving high strength joints with ultrasonic welding
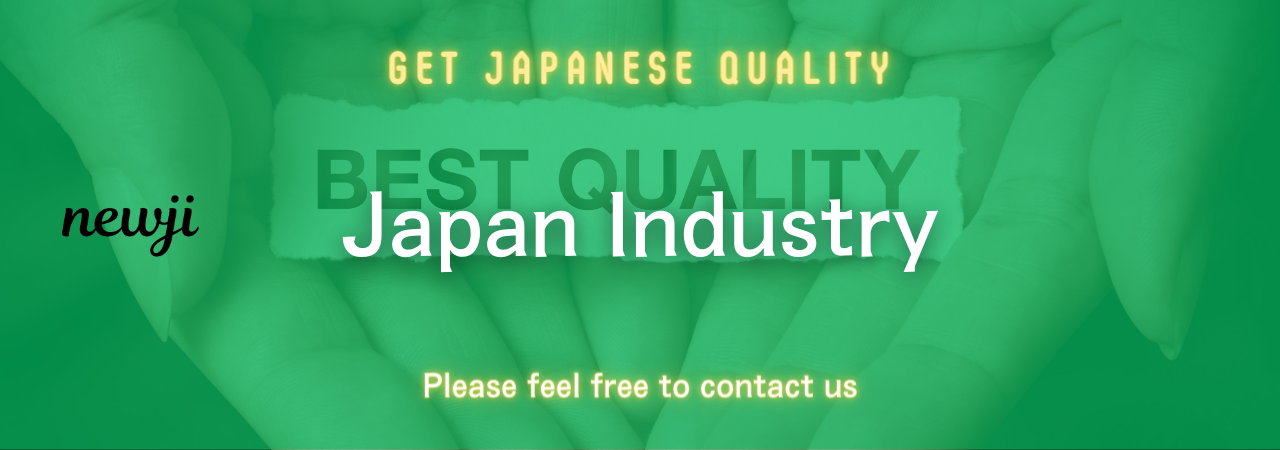
目次
Understanding Ultrasonic Welding in Plastic Molding
Ultrasonic welding is a widely-used technique in the plastic molding industry due to its speed and efficiency.
It involves the use of high-frequency ultrasonic vibrations to join plastic parts together.
This method has gained popularity for its ability to create strong and reliable joints without the need for additional materials such as adhesives or fasteners.
In this section, we will explore the basics of ultrasonic welding, its advantages, and its applications in plastic molding.
How Ultrasonic Welding Works
In the ultrasonic welding process, two plastic components are held together while high-frequency sound waves are directed at the interface of the parts.
These sound waves cause the material at the joint to heat up and melt, allowing the parts to fuse together as they cool.
The entire process is fast, often taking just a few seconds to complete, and is highly suitable for mass production.
Advantages of Ultrasonic Welding
There are several advantages to using ultrasonic welding in the plastic molding industry.
Firstly, it provides a clean and efficient way to join parts, eliminating the need for solvents, adhesives, or mechanical fasteners.
This not only reduces production time and cost but also minimizes the risk of introducing harmful chemicals into the environment.
Secondly, ultrasonic welding creates strong and reliable joints.
The process is capable of producing bonds that can withstand considerable stress and strain, making it ideal for applications where strength is critical.
Lastly, the process is highly adaptable and can be used with a wide range of thermoplastic materials, including those that are commonly used in the plastic molding industry.
Guidelines for Achieving High Strength Joints
Achieving high-strength joints with ultrasonic welding requires careful attention to several factors.
These guidelines will help ensure that your ultrasonic welding processes consistently produce strong and reliable joints.
Material Selection
The choice of material is crucial in achieving a strong ultrasonic weld.
Thermoplastics, such as ABS, polystyrene, and polypropylene, are generally well-suited for ultrasonic welding.
However, not all plastics are equally compatible, and the molecular composition of the materials plays a significant role in weldability.
To maximize joint strength, it is essential to select materials that are known to be compatible with each other.
Joint Design
Proper joint design is another critical factor in achieving high-strength ultrasonic welds.
The design should facilitate efficient energy transfer and allow for adequate melting of the material at the interface.
Common joint designs include energy directors and shear joints, both of which are engineered to concentrate the ultrasonic energy at the desired location to produce a strong weld.
Welding Parameters
Setting the correct welding parameters is essential for consistent and high-quality welds.
These parameters include the amplitude, pressure, and duration of the welding process.
The amplitude must be adjusted according to the material’s characteristics and thickness to ensure proper energy transfer.
Adequate pressure is necessary to hold the parts in place during welding and prevent defects such as voids or porosity.
The duration of the ultrasonic welding process must be carefully controlled to achieve the required melt and cooling time, ensuring a complete and strong bond.
Quality Control and Testing
Implementing a robust quality control system is crucial to achieving high-strength ultrasonic welds.
Regular inspections and testing of welded joints can help identify potential weaknesses or defects before they become significant issues.
Visual Inspection
A visual inspection is a simple yet effective method to assess the quality of an ultrasonic weld.
Look for uniformity in the weld seam and check for visible defects such as flash, cracks, or incomplete joints.
While visual inspection is helpful, it should be combined with other testing methods for a comprehensive evaluation.
Destructive Testing
Destructive testing involves applying stress to a welded joint until it fails.
This method provides valuable data on the joint’s strength and performance, helping to identify any underlying issues with the welding process or material selection.
Nondestructive Testing
Nondestructive testing allows for the assessment of joint quality without damaging the part.
Techniques such as ultrasonic testing or X-ray inspection can detect internal defects and provide a detailed analysis of the weld’s integrity.
These testing methods are particularly useful in high-volume production environments where preserving the sample is essential.
Applications and Industry Trends
Ultrasonic welding is used in various industries, including automotive, electronics, and medical devices, to produce high-strength plastic components.
With advancements in technology, the capabilities of ultrasonic welding are continually expanding, offering new possibilities for production engineers in the plastic molding industry.
Automotive Industry
In the automotive sector, ultrasonic welding is used to manufacture components such as dashboards, bumpers, and interior trim.
The method’s ability to produce strong, lightweight joints aligns with the industry’s focus on enhancing vehicle performance and fuel efficiency.
Electronics Industry
Ultrasonic welding is ideal for producing small, intricate electronic components.
It ensures a secure and conductive connection between plastic housings and metal contacts, which is critical for the performance and reliability of electronic devices.
Medical Devices
In the medical field, the need for sterile and reliable components is paramount.
Ultrasonic welding allows for the assembly of medical devices such as catheters, surgical instruments, and fluid delivery systems without compromising cleanliness or integrity.
In conclusion, understanding and implementing the guidelines for achieving high strength joints with ultrasonic welding can significantly enhance production outcomes in the plastic molding industry.
By focusing on material selection, joint design, welding parameters, and robust quality control measures, production engineers can ensure their processes consistently yield durable and reliable products.
資料ダウンロード
QCD調達購買管理クラウド「newji」は、調達購買部門で必要なQCD管理全てを備えた、現場特化型兼クラウド型の今世紀最高の購買管理システムとなります。
ユーザー登録
調達購買業務の効率化だけでなく、システムを導入することで、コスト削減や製品・資材のステータス可視化のほか、属人化していた購買情報の共有化による内部不正防止や統制にも役立ちます。
NEWJI DX
製造業に特化したデジタルトランスフォーメーション(DX)の実現を目指す請負開発型のコンサルティングサービスです。AI、iPaaS、および先端の技術を駆使して、製造プロセスの効率化、業務効率化、チームワーク強化、コスト削減、品質向上を実現します。このサービスは、製造業の課題を深く理解し、それに対する最適なデジタルソリューションを提供することで、企業が持続的な成長とイノベーションを達成できるようサポートします。
オンライン講座
製造業、主に購買・調達部門にお勤めの方々に向けた情報を配信しております。
新任の方やベテランの方、管理職を対象とした幅広いコンテンツをご用意しております。
お問い合わせ
コストダウンが利益に直結する術だと理解していても、なかなか前に進めることができない状況。そんな時は、newjiのコストダウン自動化機能で大きく利益貢献しよう!
(Β版非公開)