- お役立ち記事
- A must-see for production engineers in the precision machining end mill manufacturing industry! Material selection to achieve both cutting precision and durability
月間77,185名の
製造業ご担当者様が閲覧しています*
*2025年2月28日現在のGoogle Analyticsのデータより
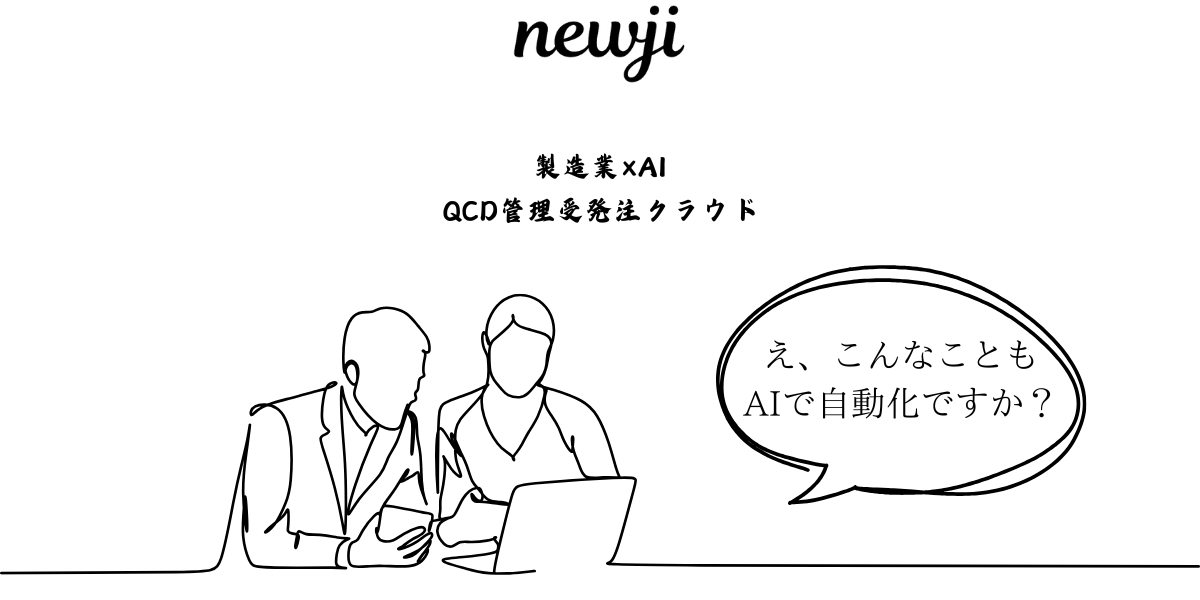
A must-see for production engineers in the precision machining end mill manufacturing industry! Material selection to achieve both cutting precision and durability
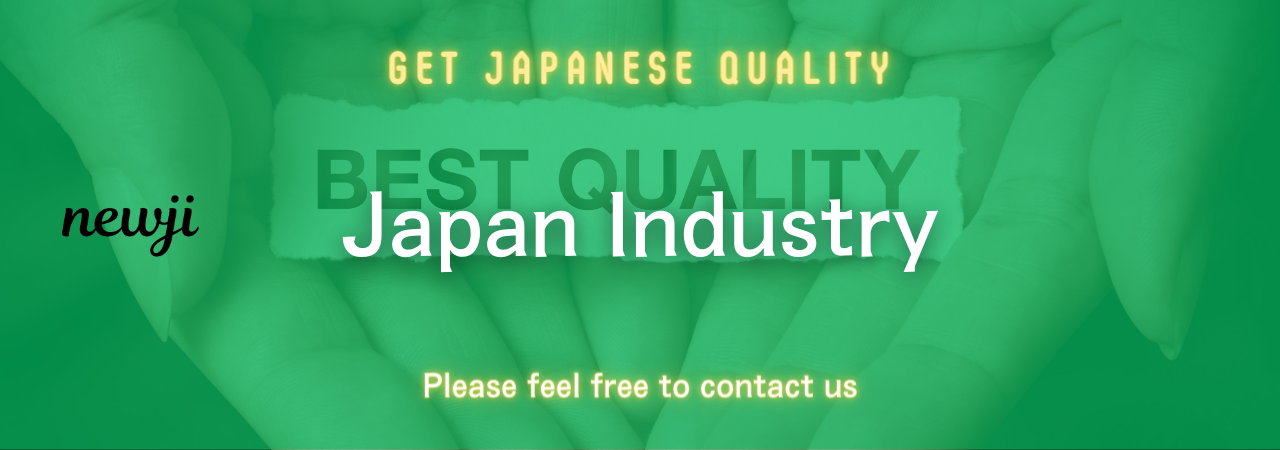
Understanding the Importance of Material Selection
In the precision machining end mill manufacturing industry, the choice of material plays a crucial role in determining the final product’s cutting precision and durability.
Production engineers are constantly in the pursuit of achieving the perfect balance between these two vital factors.
Selecting the right material requires an in-depth understanding of the characteristics that contribute to enhancing the performance of end mills.
The ideal material should not only withstand high levels of stress and heat but also maintain its sharpness over extended periods of usage.
The Relationship Between Material Properties and Cutting Precision
Cutting precision is largely influenced by the material’s hardness and wear resistance.
Materials with high hardness levels are less likely to deform, allowing for more accurate cuts.
Wear resistance, on the other hand, ensures that the cutting edges remain sharp for a longer duration, which aids in maintaining consistent precision.
However, it’s essential to avoid materials that are too brittle, as they might break under the stress of high-speed machining.
Sustainability and Economic Viability
While precision and durability are paramount, production engineers must also consider the sustainability and economic viability of the materials they choose.
Manufacturing end mills from readily available and sustainable materials can significantly reduce production costs and environmental impact.
This requires a careful assessment of the supply chain and an understanding of resource management in the materials selection process.
Commonly Used Materials in End Mill Manufacturing
Several materials are commonly utilized in the production of precision end mills, each offering unique benefits.
Let’s take a closer look at some of the most prevalent options:
1. **High-Speed Steel (HSS)**
High-Speed Steel is known for its toughness and ability to withstand high temperatures during cutting operations.
It’s a popular choice for general-purpose milling, providing a good balance between durability and cost.
2. **Carbide**
Carbide is preferred for its exceptional hardness and wear resistance, making it suitable for high-precision machining.
It’s particularly effective in cutting applications requiring high speeds.
3. **Cobalt Steel Alloys**
This material offers improved wear resistance and heat resistance over standard HSS.
It’s ideal for applications that necessitate extended tool life and cutting in tough materials.
Innovations in Material Technology
The precision machining industry continuously benefits from advancements in material technology.
These innovations aim to enhance the properties of existing materials and develop new alloys that offer superior performance.
Examples include advanced coatings that increase wear resistance and reduce friction, leading to improved efficiency and longevity of end mills.
Additionally, composites and ceramic materials are being explored for their potential to offer high strength and superior heat resistance.
Testing and Quality Assurance
An integral part of the material selection process involves rigorous testing and quality assurance.
Quality control measures ensure that the chosen materials meet the required specifications for performance and safety.
This involves standardized testing procedures to evaluate factors such as tensile strength, hardness, and resistance to wear and heat.
By adhering to stringent quality assurance protocols, production engineers can guarantee the reliability and effectiveness of their end mills.
Conclusion: The Path to Precision and Durability
For production engineers in the precision machining end mill manufacturing industry, achieving cutting precision and durability is a multifaceted challenge.
Material selection is at the heart of this pursuit, requiring a comprehensive understanding of the material properties and their impact on performance.
By choosing the right materials, staying informed about technological advancements, and maintaining strict quality assurance processes, production engineers can fabricate end mills that not only perform exceptionally but also stand the test of time.
In this ever-evolving industry, the quest for the perfect balance between cutting precision and durability continues to drive innovation and excellence.
資料ダウンロード
QCD管理受発注クラウド「newji」は、受発注部門で必要なQCD管理全てを備えた、現場特化型兼クラウド型の今世紀最高の受発注管理システムとなります。
ユーザー登録
受発注業務の効率化だけでなく、システムを導入することで、コスト削減や製品・資材のステータス可視化のほか、属人化していた受発注情報の共有化による内部不正防止や統制にも役立ちます。
NEWJI DX
製造業に特化したデジタルトランスフォーメーション(DX)の実現を目指す請負開発型のコンサルティングサービスです。AI、iPaaS、および先端の技術を駆使して、製造プロセスの効率化、業務効率化、チームワーク強化、コスト削減、品質向上を実現します。このサービスは、製造業の課題を深く理解し、それに対する最適なデジタルソリューションを提供することで、企業が持続的な成長とイノベーションを達成できるようサポートします。
製造業ニュース解説
製造業、主に購買・調達部門にお勤めの方々に向けた情報を配信しております。
新任の方やベテランの方、管理職を対象とした幅広いコンテンツをご用意しております。
お問い合わせ
コストダウンが利益に直結する術だと理解していても、なかなか前に進めることができない状況。そんな時は、newjiのコストダウン自動化機能で大きく利益貢献しよう!
(β版非公開)