- お役立ち記事
- A must-see for production technology department managers! How to increase productivity with factory automation
月間76,176名の
製造業ご担当者様が閲覧しています*
*2025年3月31日現在のGoogle Analyticsのデータより
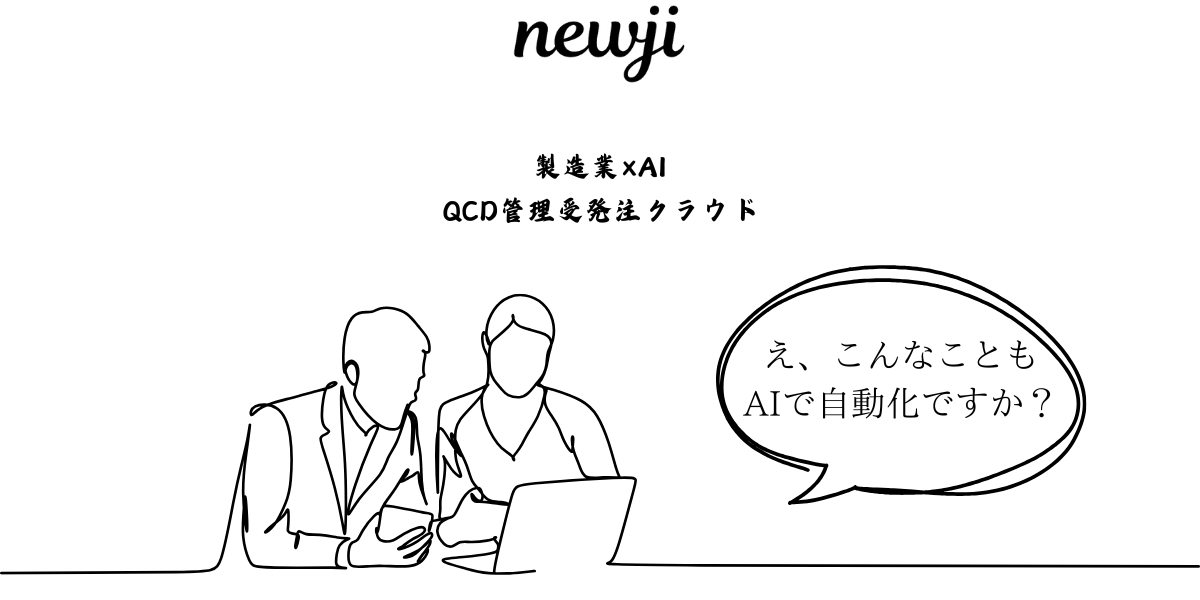
A must-see for production technology department managers! How to increase productivity with factory automation
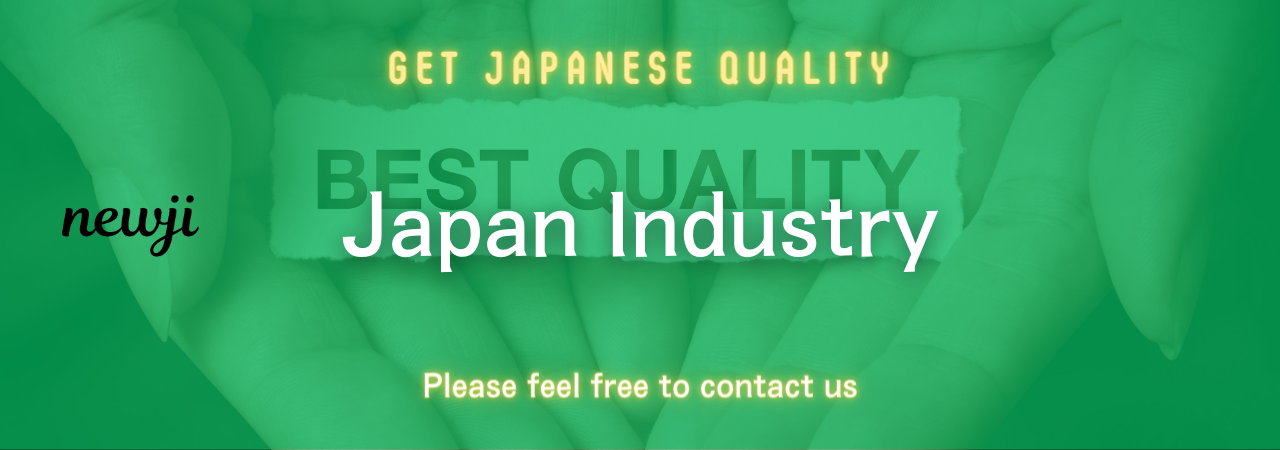
目次
Understanding Factory Automation
Factory automation is the use of control systems, such as computers or robots, for handling different processes and machinery in an industrial setting.
Automation in the manufacturing industry helps to streamline operations, reduce errors, and improve the overall efficiency.
It is an essential component for staying competitive in today’s fast-paced industrial world.
As production technology department managers, embracing factory automation can significantly enhance productivity.
This involves implementing modern techniques and equipment to automate tasks that were previously done manually.
Automation doesn’t just mean replacing human efforts; it’s about creating a harmonious environment where machines and humans work together effectively.
The Benefits of Factory Automation
Increased productivity is the primary reason why companies invest in factory automation.
When machines take over repetitive tasks, human workers can focus on more innovative and value-adding activities.
This results in a more efficient workflow, leading to increased production rates and output levels.
Factory automation also enhances product quality.
Machines can perform tasks with a high degree of precision and consistency, reducing the likelihood of errors.
This results in better-quality products and ensures customer satisfaction.
Another significant benefit is cost reduction.
While the initial investment in automation technology can be substantial, the long-term savings in labor costs, minimized waste, and reduced errors offset this initial expenditure.
Automation leads to lower production costs and increases competitiveness in the market.
Challenges of Implementing Factory Automation
Despite its many advantages, implementing factory automation also comes with challenges.
For example, the high initial cost of acquiring and installing automation equipment can be a hurdle for many companies.
Additionally, integrating new systems with existing ones might require significant time and resources.
There is also the fear among workers about losing jobs due to automation.
While some roles may indeed become redundant, automation often creates new job opportunities, especially in areas like system maintenance, programming, and supervision.
Training workers to adapt to the new systems is crucial in addressing this issue.
Furthermore, technology is rapidly evolving, which means that systems could become obsolete quicker, necessitating frequent updates and upgrades.
Keeping up with technological advancements requires continuous investment, both in terms of finance and human resources.
How to Successfully Implement Factory Automation
Successful implementation of factory automation begins with thorough planning and assessment.
Determine which areas of production would benefit the most from automation and prioritize these processes.
Conduct a costs-benefits analysis to ensure that the investment makes financial sense.
Engage both technical experts and employees in the evaluation process.
Technical experts can assess which technologies and systems would best suit the company’s needs, while employees can provide insights into day-to-day operations and potential areas of improvement.
Investing in high-quality equipment from reputable manufacturers is essential to avoid operational downtimes.
Cheap equipment might seem cost-effective initially but could lead to frequent breakdowns and maintenance costs in the long run.
Training employees is a critical component of implementing factory automation.
Providing training programs helps workers feel more comfortable with new systems and increases operational efficiency.
Encouraging a culture of continuous learning will empower employees to adapt to technological changes.
Lastly, start with small changes and gradually increase the level of automation.
This allows the company to identify and address potential issues with minimal disruption to production.
The Role of Technology in Factory Automation
Technology plays a fundamental role in factory automation.
Innovative advancements like the Internet of Things (IoT), machine learning, and artificial intelligence bring significant benefits in data collection, analysis, and operational efficiency.
IoT connects various devices and systems within the factory, enabling seamless communication.
This connectivity allows for real-time monitoring and control of equipment and processes, providing managers with valuable insights to make data-driven decisions.
Machine learning systems can forecast equipment failures and perform predictive maintenance, minimizing unexpected downtimes.
These systems learn from historical data to optimize processes, improve product quality, and enhance productivity.
Artificial intelligence creates smart production lines that can adapt to changing conditions.
AI-powered robots can perform complex tasks, analyze data, and make autonomous decisions.
This results in reduced human intervention and more efficient production processes.
Future Trends in Factory Automation
The future of factory automation looks promising with several trends evolving.
One such trend is the increasing integration of automation with other digital technologies.
For instance, combining automation with augmented reality (AR) can assist workers in complex assembly processes or equipment repairs.
Collaborative robots, or cobots, are also becoming more commonplace.
These robots are designed to work alongside humans, enhancing productivity while ensuring safety.
Cobots are flexible, easy to program, and suitable for tasks that require human collaboration.
Sustainable manufacturing is another upcoming trend.
Factory automation can play a role in reducing energy consumption and waste production.
Automated systems optimize resource usage and improve energy efficiency, contributing to sustainability goals.
The concept of the smart factory is also gaining traction, with automation taking center-stage.
Smart factories integrate advanced technologies to create an interconnected environment that fosters innovation and efficiency.
With these advancements on the horizon, embracing factory automation is crucial for staying competitive.
Production technology department managers play a vital role in driving this transformation and ultimately helping their companies thrive in the industrial landscape.
資料ダウンロード
QCD管理受発注クラウド「newji」は、受発注部門で必要なQCD管理全てを備えた、現場特化型兼クラウド型の今世紀最高の受発注管理システムとなります。
ユーザー登録
受発注業務の効率化だけでなく、システムを導入することで、コスト削減や製品・資材のステータス可視化のほか、属人化していた受発注情報の共有化による内部不正防止や統制にも役立ちます。
NEWJI DX
製造業に特化したデジタルトランスフォーメーション(DX)の実現を目指す請負開発型のコンサルティングサービスです。AI、iPaaS、および先端の技術を駆使して、製造プロセスの効率化、業務効率化、チームワーク強化、コスト削減、品質向上を実現します。このサービスは、製造業の課題を深く理解し、それに対する最適なデジタルソリューションを提供することで、企業が持続的な成長とイノベーションを達成できるようサポートします。
製造業ニュース解説
製造業、主に購買・調達部門にお勤めの方々に向けた情報を配信しております。
新任の方やベテランの方、管理職を対象とした幅広いコンテンツをご用意しております。
お問い合わせ
コストダウンが利益に直結する術だと理解していても、なかなか前に進めることができない状況。そんな時は、newjiのコストダウン自動化機能で大きく利益貢献しよう!
(β版非公開)