- お役立ち記事
- A must-see for purchasing managers in the manufacturing industry! 30 “Cost Reduction Success Stories”
月間76,176名の
製造業ご担当者様が閲覧しています*
*2025年3月31日現在のGoogle Analyticsのデータより
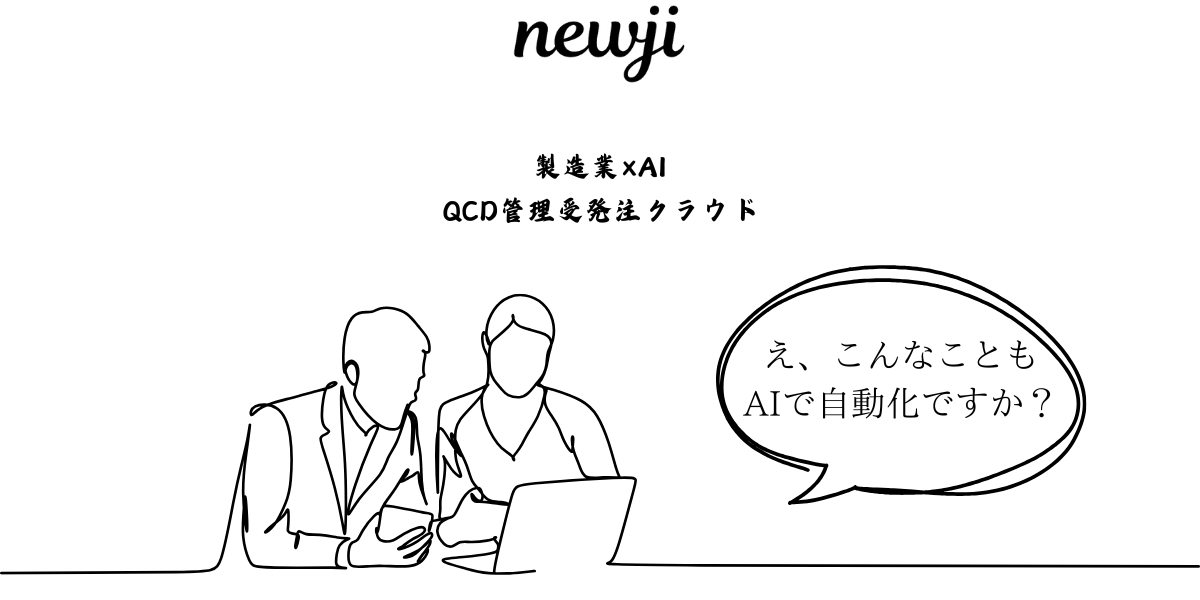
A must-see for purchasing managers in the manufacturing industry! 30 “Cost Reduction Success Stories”
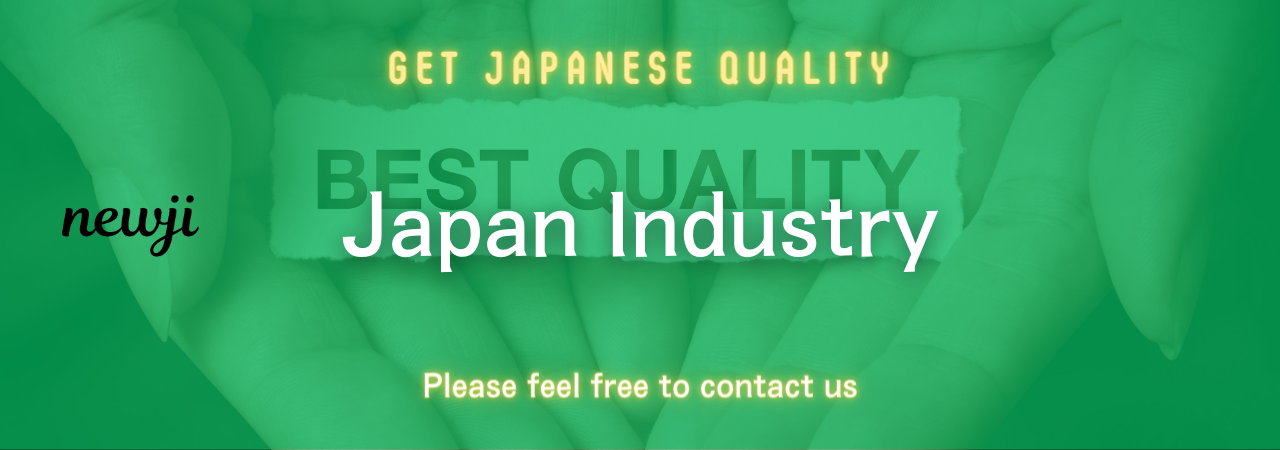
目次
Introduction
In the manufacturing industry, cost reduction is more vital than ever to stay competitive and profitable.
Purchasing managers play a critical role in achieving these cost savings, making their actions and decisions crucial.
This article will explore 30 success stories of cost reduction strategies that are transforming the manufacturing industry.
Here’s a must-see guide for purchasing managers looking to optimize their operations and trim unnecessary expenses.
Streamlining Supplier Relationships
1. Supplier Consolidation
Purchasing managers have successfully reduced costs by consolidating their supplier base.
By working with fewer suppliers, companies have been able to negotiate better terms, reduce administrative costs, and improve quality control.
2. Vendor Negotiations
Effective negotiation with vendors can lead to significant savings.
An example from a packaging company shows how revisiting pricing terms and bulk order discounts saved 15% on annual procurement costs.
3. Long-term Contracts
Establishing long-term contracts with suppliers can lock in prices and reduce exposure to market fluctuations.
This approach helped an electronics manufacturer maintain stable costs over three years.
4. Collaborative Supplier Partnerships
Fostering a collaborative environment with suppliers can lead to innovations that reduce costs.
For instance, a car manufacturer co-created a new material with a supplier, resulting in cheaper production and improved vehicle performance.
Enhancing Inventory Management
5. Just-in-Time Inventory
Implementing a just-in-time inventory system has allowed manufacturers to reduce holding costs significantly, as demonstrated by a consumer goods company that cut warehouse expenses by 20%.
6. Inventory Cycle Counts
Regularly performing inventory cycle counts ensures accuracy and minimizes excess stock.
A pharmaceutical company increased inventory accuracy by 98% and significantly reduced obsolescence costs.
7. Demand Forecasting
Accurate demand forecasting can prevent overproduction and reduce waste.
A beverage company employed advanced analytics to improve forecast accuracy, saving millions in production costs.
Optimizing Procurement Processes
8. E-Procurement Systems
Implementing e-procurement systems has streamlined purchasing processes, reduced transaction costs, and increased compliance.
A major appliance manufacturer saved considerable time and money annually by digitizing procurement.
9. Bulk Purchasing
By buying in bulk, companies can benefit from economies of scale and reduced per-unit costs.
A textile manufacturer leveraged bulk buying to slash fabric costs by 25%.
10. Standardization of Components
Standardizing components across different product lines can reduce costs and simplify supply chains.
An aerospace company used this strategy to cut costs by 12% and minimize parts inventory.
Improving Operational Efficiency
11. Lean Manufacturing
Adopting lean manufacturing principles reduces waste and increases efficiency.
A furniture maker implemented lean practices and improved productivity by 30%.
12. Automation of Repetitive Tasks
Automation of mundane tasks speeds up processes and reduces labor costs.
A parts supplier automated its order processing, reducing headcount by 10% while improving accuracy.
13. Energy Efficiency Measures
Investing in energy conservation measures can yield significant savings over time.
A steel mill installed energy-efficient equipment, reducing electricity costs by 18%.
Utilizing Technology and Innovation
14. Advanced Analytics
Harnessing data and analytics can unlock hidden cost-saving opportunities.
An electronics firm used data analytics to streamline its logistics process, saving 15% on transportation costs.
15. 3D Printing
3D printing can lower production costs by reducing material waste and enabling more complex designs.
A tool manufacturer used 3D printing to produce complex parts at a fraction of traditional manufacturing costs.
16. Internet of Things (IoT)
IoT technology provides real-time data to optimize production processes and reduce downtime.
An automotive company reduced maintenance costs by 20% by using IoT for predictive maintenance.
Value Engineering
17. Design for Manufacturability
Designing products with manufacturing efficiency in mind can reduce production costs.
A smartphone manufacturer revised its assembly line process, resulting in a 15% production cost decrease.
18. Material Substitution
Substituting materials with more cost-effective alternatives without sacrificing quality can lead to savings.
A clothing brand switched to alternative fibers, cutting material costs by 10%.
19. Product Redesign for Cost Efficiency
Revisiting product designs for cost efficiency led an electronics company to simplify circuit boards, lowering production costs by 20%.
Training and Workforce Management
20. Employee Training Programs
Investing in employee training has increased productivity and reduced error rates.
A food manufacturer trained staff in Six Sigma techniques, enhancing performance and saving costs.
21. Cross-Training Employees
Cross-training employees ensures greater flexibility and reduces dependence on specialized staff.
A machinery plant implemented cross-training, lowering operational disruptions and saving on overtime costs.
22. Empowering Employees
Empowering employees to identify cost-saving initiatives can result in significant improvements.
An electronics factory encouraged employee input on efficiencies, cutting costs by 8%.
Environmental and Waste Management
23. Recycling Programs
Recycling initiatives can reduce waste disposal costs and generate revenue from recycled materials.
A packaging company introduced a recycling program, cutting waste costs by 25%.
24. Waste Reduction Strategies
Minimizing waste ensures better resource utilization and cost savings.
A beverage manufacturer optimized its bottling process, reducing waste by 30%.
25. Sustainable Sourcing
Choosing sustainable materials can reduce costs long-term and improve corporate responsibility.
An apparel company sourced sustainable fabrics, leading to cost savings and a stronger brand reputation.
Financial Management Practices
26. Cost Audits
Regular cost audits can uncover unnecessary expenses and potential savings.
A chemical firm conducted audits that identified several inefficient practices, saving 10% of annual costs.
27. Budget Forecasting
Accurate budget forecasting avoids overspending and ensures funds are allocated effectively.
A consumer electronics company improved its budget forecasting, leading to better control of financial resources.
28. Cost-Benefit Analysis
Assessing the cost versus benefit of projects ensures smarter investments.
A medical device manufacturer implemented cost-benefit analyses that optimized project investments, saving capital.
Outsourcing and Strategic Partnerships
29. Strategic Sourcing
Strategic sourcing can uncover lower-cost suppliers with similar quality levels.
An automobile parts company shifted suppliers, cutting costs by 15% without sacrificing quality.
30. Outsourcing Non-Core Functions
Outsourcing non-core functions has allowed several companies to concentrate on core competencies.
A heavy machinery enterprise outsourced payroll and administration, realizing substantial savings.
Conclusion
Each of these strategies offers an effective means to reduce costs and improve efficiency in the manufacturing industry.
For purchasing managers, understanding and implementing these success stories could significantly enhance their company’s profitability.
Continual innovation and dedication to cost management are pivotal to sustaining a competitive edge.
Readers can use this guide to explore their own cost-saving initiatives and drive tangible financial benefits in their organizations.
資料ダウンロード
QCD管理受発注クラウド「newji」は、受発注部門で必要なQCD管理全てを備えた、現場特化型兼クラウド型の今世紀最高の受発注管理システムとなります。
ユーザー登録
受発注業務の効率化だけでなく、システムを導入することで、コスト削減や製品・資材のステータス可視化のほか、属人化していた受発注情報の共有化による内部不正防止や統制にも役立ちます。
NEWJI DX
製造業に特化したデジタルトランスフォーメーション(DX)の実現を目指す請負開発型のコンサルティングサービスです。AI、iPaaS、および先端の技術を駆使して、製造プロセスの効率化、業務効率化、チームワーク強化、コスト削減、品質向上を実現します。このサービスは、製造業の課題を深く理解し、それに対する最適なデジタルソリューションを提供することで、企業が持続的な成長とイノベーションを達成できるようサポートします。
製造業ニュース解説
製造業、主に購買・調達部門にお勤めの方々に向けた情報を配信しております。
新任の方やベテランの方、管理職を対象とした幅広いコンテンツをご用意しております。
お問い合わせ
コストダウンが利益に直結する術だと理解していても、なかなか前に進めることができない状況。そんな時は、newjiのコストダウン自動化機能で大きく利益貢献しよう!
(β版非公開)