- お役立ち記事
- A must-see for quality assurance department leaders in the aircraft parts manufacturing industry! Delamination detection and repair techniques for composite members
A must-see for quality assurance department leaders in the aircraft parts manufacturing industry! Delamination detection and repair techniques for composite members
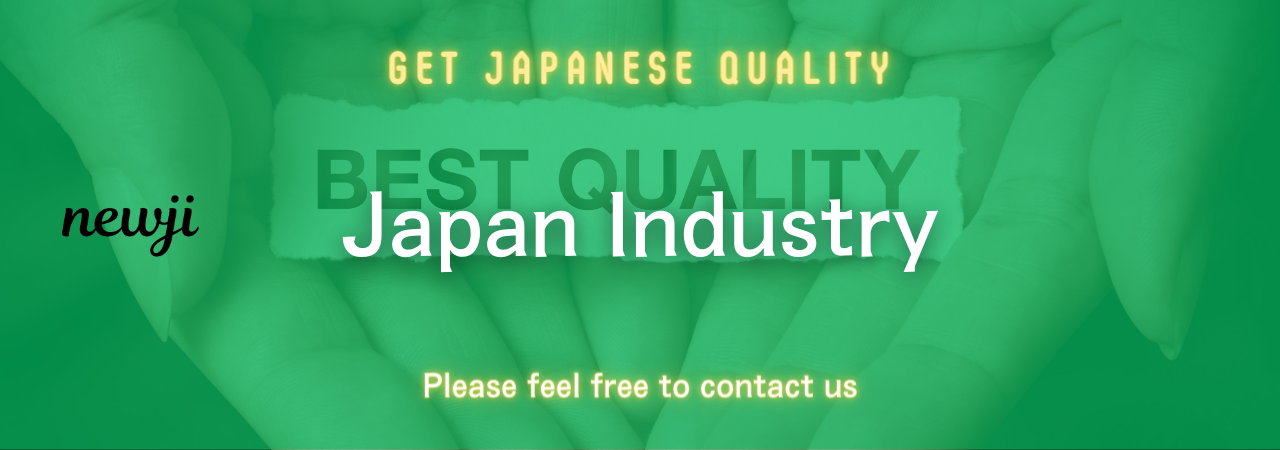
目次
Introduction to Delamination in Composite Materials
In the aircraft parts manufacturing industry, the use of composite materials has become increasingly prevalent due to their incredible strength-to-weight ratio.
However, these materials come with their own set of challenges, one of the most significant being delamination.
Delamination refers to the separation of layers in laminate materials, which can significantly compromise the structural integrity of aircraft components.
As leaders in quality assurance departments, understanding the detection and repair techniques for delamination is critical to ensuring the safety and reliability of composite members.
Understanding Composite Materials
Composite materials are engineered by combining two or more distinct materials to create an advanced material with superior properties.
Aircraft components frequently utilize composites like carbon fiber reinforced polymers and fiberglass.
These composites offer several advantages, including reduced weight, increased strength, and resistance to corrosion.
However, their layered structure makes them susceptible to delamination under certain conditions.
Causes of Delamination
Delamination can arise from several factors during the lifecycle of aircraft components.
Manufacturing defects, such as improper curing or poor adhesive bonding, can initiate delamination.
Moreover, exposure to excessive mechanical stresses, thermal cycling, or environmental conditions like moisture can exacerbate separation between layers.
Even minor delamination can escalate rapidly if left unchecked, potentially leading to catastrophic failures.
Detection Techniques for Delamination
Early detection of delamination is crucial for maintaining the structural integrity of composite members.
Several advanced non-destructive testing (NDT) techniques are available for identifying delamination in composites.
Ultrasonic Testing
Ultrasonic testing is one of the most widely used NDT methods for detecting delamination.
It involves sending high-frequency sound waves through the material, where they reflect off interfaces and defects.
Differences in wave patterns can indicate the presence of delaminations or voids within the composite layers.
Thermography
Thermography utilizes infrared imaging to detect variations in surface temperature, which can indicate subsurface defects.
The technique is effective because delaminated areas often exhibit different thermal conductivities compared to intact regions.
This difference appears as a distinct thermal pattern, making it easier to pinpoint potential delamination areas.
Resonance and Acoustic Emission Testing
Resonance testing involves striking the material and analyzing sound wave patterns to detect irregularities.
Similarly, acoustic emission testing monitors high-frequency sound waves released during material deformation.
Both methods can effectively identify delamination by highlighting changes in resonance or acoustic emissions.
Repair Techniques for Delaminated Composite Members
Once detected, it becomes imperative to address delamination promptly to prevent progression and potential failure.
Several repair techniques are employed in the aircraft industry to restore the integrity of composite materials.
Resin Injection
Resin injection is a common technique for repairing minor delaminations.
The process involves injecting a resin adhesive into the delaminated area to bond the separated layers back together.
After injection, the area is typically subjected to heat and pressure to cure the resin and restore strength.
Vacuum Bagging
Vacuum bagging is often used in conjunction with resin injection to enhance the repair process.
The technique involves wrapping the component in a vacuum bag and applying atmospheric pressure to evenly distribute the resin and remove air bubbles.
This ensures a uniform bond and minimizes voids within the repair area.
Patching
For more extensive delamination, patching may be necessary.
This technique involves removing the damaged section and replacing it with a patch made from the same composite material.
The patch is bonded into place using adhesives and may require curing in an autoclave to achieve optimal strength.
Proactive Measures to Prevent Delamination
While detection and repair are crucial, implementing proactive measures to prevent delamination is equally important.
Quality Control During Manufacturing
Ensuring strict quality control procedures during manufacturing can significantly reduce the risk of delamination.
This includes proper material handling, accurate adhesive application, and precise curing processes to prevent manufacturing defects.
Regular Maintenance and Inspections
Routine maintenance and thorough inspections are vital in identifying early signs of delamination.
Implementing a proactive inspection schedule can help catch issues before they develop into major problems, saving time and resources in repairs.
Environmental Considerations
Protecting composite materials from harsh environmental conditions can mitigate delamination risks.
Using protective coatings or environmental barriers can help shield composites from moisture, temperature extremes, and UV exposure.
Conclusion
Delamination poses a significant challenge to the structural integrity of composite materials in the aircraft parts manufacturing industry.
As a quality assurance department leader, it is crucial to be equipped with knowledge of detection and repair techniques for combating delamination.
By employing advanced non-destructive testing methods and implementing effective repair strategies, one can ensure the continued safety and performance of composite members.
Moreover, proactive measures aimed at preventing delamination can lead to long-term savings and improved reliability of aircraft components.
Understanding and addressing delamination is essential for advancing the safety and efficiency of modern aircraft materials.
資料ダウンロード
QCD調達購買管理クラウド「newji」は、調達購買部門で必要なQCD管理全てを備えた、現場特化型兼クラウド型の今世紀最高の購買管理システムとなります。
ユーザー登録
調達購買業務の効率化だけでなく、システムを導入することで、コスト削減や製品・資材のステータス可視化のほか、属人化していた購買情報の共有化による内部不正防止や統制にも役立ちます。
NEWJI DX
製造業に特化したデジタルトランスフォーメーション(DX)の実現を目指す請負開発型のコンサルティングサービスです。AI、iPaaS、および先端の技術を駆使して、製造プロセスの効率化、業務効率化、チームワーク強化、コスト削減、品質向上を実現します。このサービスは、製造業の課題を深く理解し、それに対する最適なデジタルソリューションを提供することで、企業が持続的な成長とイノベーションを達成できるようサポートします。
オンライン講座
製造業、主に購買・調達部門にお勤めの方々に向けた情報を配信しております。
新任の方やベテランの方、管理職を対象とした幅広いコンテンツをご用意しております。
お問い合わせ
コストダウンが利益に直結する術だと理解していても、なかなか前に進めることができない状況。そんな時は、newjiのコストダウン自動化機能で大きく利益貢献しよう!
(Β版非公開)