- お役立ち記事
- A must-see for quality assurance department leaders in the press clutch plate manufacturing industry! Designed for durability and precision
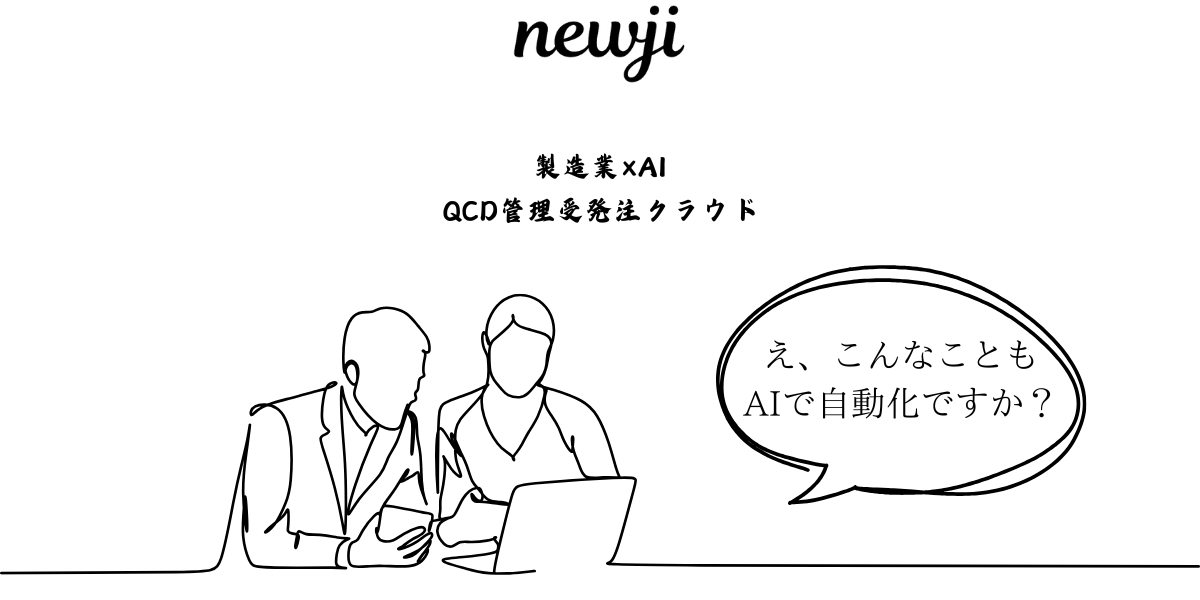
A must-see for quality assurance department leaders in the press clutch plate manufacturing industry! Designed for durability and precision
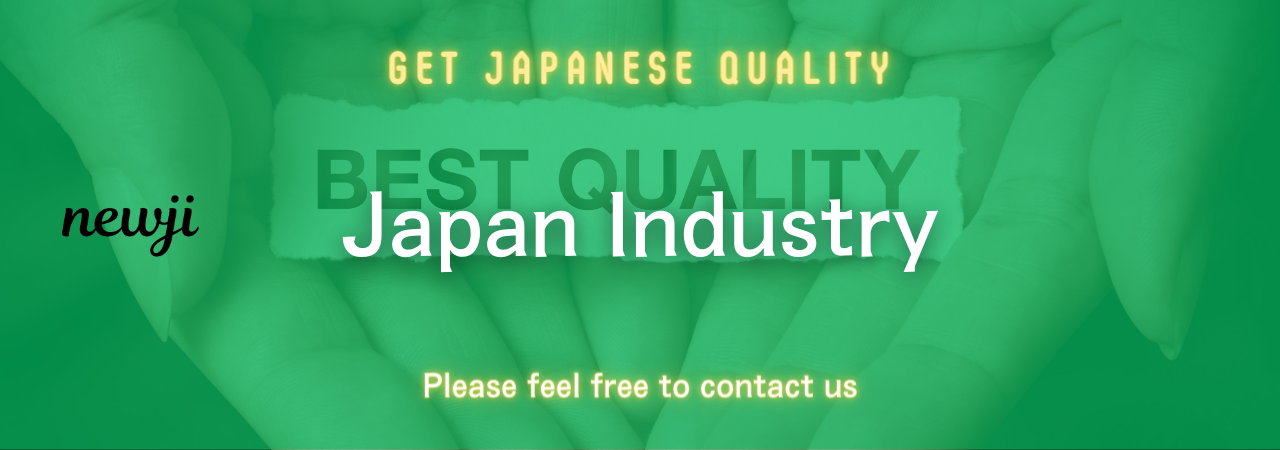
目次
Introduction to Press Clutch Plate Manufacturing
In the world of automotive manufacturing, the clutch system plays a vital role in ensuring smooth vehicle operation.
At the heart of this system are clutch plates, which are essential components for vehicle transmission.
For leaders in the quality assurance departments of press clutch plate manufacturing, understanding the intricacies of production is crucial.
This article explores the processes involved in manufacturing clutch plates, focusing on durability and precision—two key aspects that cannot be overlooked.
Understanding the Importance of Quality Assurance
Quality assurance (QA) is a systematic process that ensures products meet specific requirements and standards.
For clutch plates, QA is especially important because these components endure significant wear and tear during vehicle operation.
A small defect in a clutch plate can lead to severe vehicle performance issues, emphasizing the need for strict quality controls.
QA leaders need comprehensive knowledge of the entire manufacturing process to identify potential issues and improve product quality.
The Manufacturing Process of Press Clutch Plates
Material Selection
The first step in clutch plate manufacturing involves selecting the right materials.
Most clutch plates are made from a combination of metals like steel or aluminum and friction materials like fiberglass or Kevlar.
The choice of materials impacts the plate’s performance, durability, and cost.
It is crucial to select materials that can withstand high friction and heat, ensuring the clutch plate’s longevity.
Design and Engineering
Designing a clutch plate requires precision engineering to meet automotive standards.
Engineers use computer-aided design (CAD) software to create detailed models, considering factors like plate size, shape, and friction material thickness.
The design phase includes simulations to test the plate’s performance under various conditions, ensuring it meets durability and precision requirements.
Pressing and Shaping
Once the design is finalized, the manufacturing process moves to pressing and shaping.
Hydraulic presses are commonly used to shape the metal and friction material into the desired form.
Precision is critical here, as even a minor deviation can affect the plate’s functionality.
Pressing machines must be regularly calibrated and maintained to ensure they operate within the required tolerances.
Heat Treatment
After shaping, the clutch plates undergo heat treatment to improve their strength and wear resistance.
This involves heating the plates to high temperatures and then cooling them rapidly.
Proper heat treatment enhances the material’s properties, ensuring the plates can handle the mechanical stress of vehicle operation.
Finishing and Assembly
The final steps in the manufacturing process involve finishing and assembly.
Finishing processes like grinding and polishing are used to achieve the desired surface finish and thickness.
The plates are then assembled with other clutch components, ensuring all parts fit perfectly.
Any imperfections found during inspection are addressed before the plates are approved for distribution.
Quality Assurance Techniques in Clutch Plate Manufacturing
Non-destructive Testing
Non-destructive testing (NDT) methods are vital in QA for clutch plates.
Techniques like ultrasonic testing and magnetic particle inspection allow QA teams to detect internal defects without damaging the product.
These methods help identify issues early, preventing defective plates from reaching the market.
Friction Material Testing
Given the importance of friction materials, specific tests are performed to evaluate their performance.
Abrasion tests, for example, measure how the material withstands wear over time.
This testing ensures that the friction material used in the clutch plates maintains its integrity and performance under various conditions.
Dimensional Verification
Dimensional accuracy is critical in clutch plate manufacturing, impacting the component’s fit and function.
QA teams use advanced measuring instruments such as coordinate measuring machines (CMM) to verify dimensions against the specifications.
This step ensures that every component meets the precise measurements required for optimal vehicle performance.
The Role of Technology in Enhancing Quality
Technology plays a pivotal role in improving the quality of clutch plates.
Automation and robotics in manufacturing help achieve consistent results, reducing human error.
Advanced software for data analysis allows QA teams to monitor production metrics and spot trends that could indicate potential quality issues.
Embracing these technologies enables manufacturers to produce high-quality, durable clutch plates efficiently.
Conclusion: Ensuring Durability and Precision
For QA leaders in the press clutch plate manufacturing industry, guaranteeing durability and precision is non-negotiable.
Understanding the entire production process, from material selection to final inspection, equips them with the knowledge to implement effective quality assurance practices.
By utilizing advanced testing methods and technology, they can uphold high standards, ensuring that every clutch plate leaving the factory meets the rigorous demands of the automotive industry.
資料ダウンロード
QCD調達購買管理クラウド「newji」は、調達購買部門で必要なQCD管理全てを備えた、現場特化型兼クラウド型の今世紀最高の購買管理システムとなります。
ユーザー登録
調達購買業務の効率化だけでなく、システムを導入することで、コスト削減や製品・資材のステータス可視化のほか、属人化していた購買情報の共有化による内部不正防止や統制にも役立ちます。
NEWJI DX
製造業に特化したデジタルトランスフォーメーション(DX)の実現を目指す請負開発型のコンサルティングサービスです。AI、iPaaS、および先端の技術を駆使して、製造プロセスの効率化、業務効率化、チームワーク強化、コスト削減、品質向上を実現します。このサービスは、製造業の課題を深く理解し、それに対する最適なデジタルソリューションを提供することで、企業が持続的な成長とイノベーションを達成できるようサポートします。
オンライン講座
製造業、主に購買・調達部門にお勤めの方々に向けた情報を配信しております。
新任の方やベテランの方、管理職を対象とした幅広いコンテンツをご用意しております。
お問い合わせ
コストダウンが利益に直結する術だと理解していても、なかなか前に進めることができない状況。そんな時は、newjiのコストダウン自動化機能で大きく利益貢献しよう!
(Β版非公開)