- お役立ち記事
- A must-see for quality assurance department leaders in the stainless steel valve seat manufacturing industry! Technology that combines corrosion resistance and sealing performance
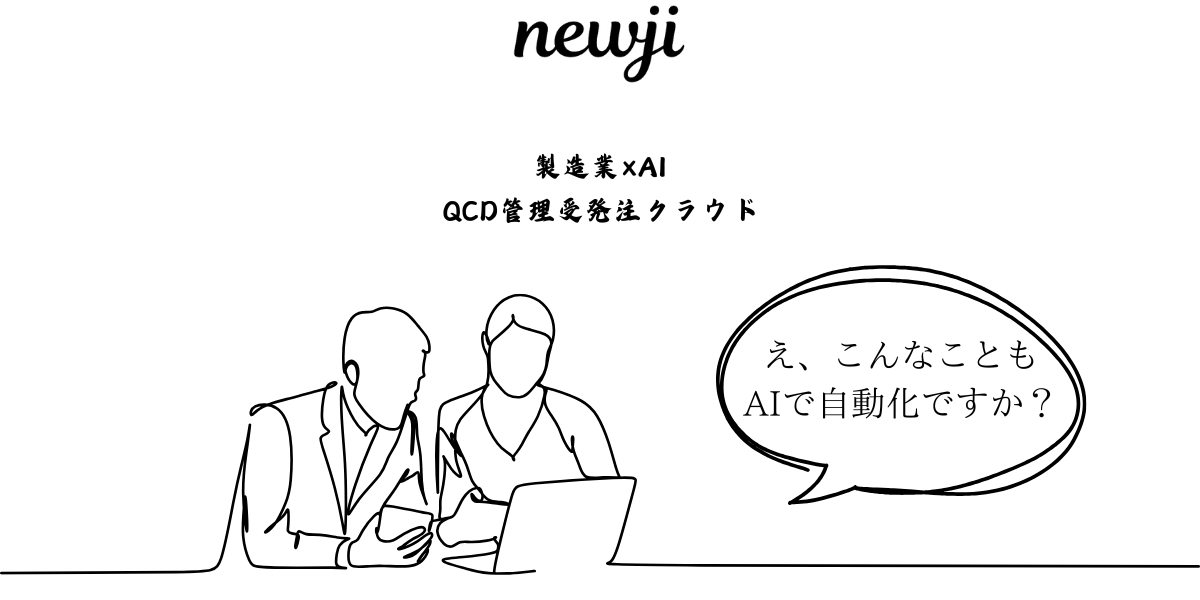
A must-see for quality assurance department leaders in the stainless steel valve seat manufacturing industry! Technology that combines corrosion resistance and sealing performance
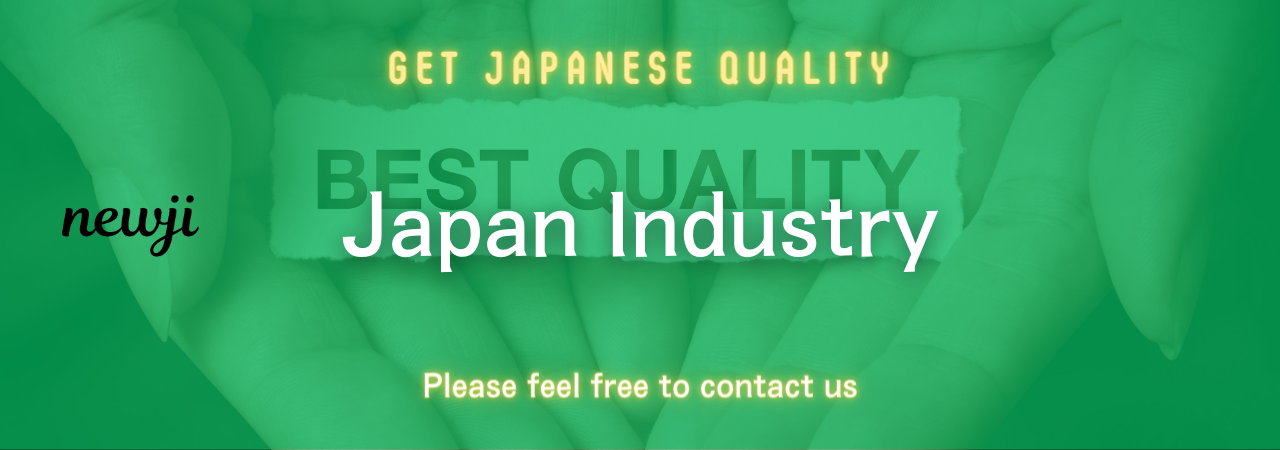
目次
Introduction to Stainless Steel Valve Seats
Stainless steel valve seats play a crucial role in a wide array of industries, primarily due to their exceptional durability and resistance to harsh conditions.
They are essential components in machinery and systems where the management and regulation of fluid flow and pressure are necessary.
When discussing stainless steel, emphasis is often placed on its inherent properties such as corrosion resistance, which is vital in extending the life of valve seats.
Whether it’s for industrial, commercial, or residential purposes, ensuring the quality and longevity of these components is paramount.
The Importance of Corrosion Resistance
Corrosion resistance is a critical factor in the performance of stainless steel valve seats.
In environments where the valve seats are exposed to chemicals, high humidity, or saline settings, the material’s ability to withstand corrosion without degrading is imperative.
Stainless steel naturally possesses this resistance due to its chromium content, which forms a protective oxide layer on the steel surface.
This inoxidizable layer acts as a shield against various environmental factors, preventing rust and deterioration.
As a result, valve seats made from stainless steel show an extended lifespan, reducing the need for frequent replacements and minimizing downtime in operations.
For quality assurance department leaders, understanding and promoting the corrosion resistance of stainless steel is vital in maintaining product reliability and customer satisfaction.
Sealing Performance: A Key Attribute
Another essential characteristic of stainless steel valve seats is their sealing performance.
The ability of a valve seat to effectively prevent leaks, ensure pressure retention, and maintain optimal fluid flow is fundamental to its functionality.
The sealing performance of these seats directly affects an application’s efficiency and safety.
High-quality stainless steel valve seats are designed to provide tight seals, even under extreme pressures and temperatures.
The precision in manufacturing and the choice of material contribute to the superior sealing capabilities of these components, ensuring they perform consistently and reliably over time.
Quality assurance leaders should prioritize maintaining these standards to avoid operational inefficiencies or hazardous situations.
Advanced Manufacturing Techniques
The manufacturing process of stainless steel valve seats has evolved significantly, incorporating advanced techniques to enhance corrosion resistance and sealing performance.
Computer-aided design (CAD) and computer-aided manufacturing (CAM) are commonly employed in the design and production phases.
These technologies ensure precision engineering, enabling manufacturers to create valve seats tailored perfectly to specific needs.
Additionally, adopting innovative practices such as laser cutting, precision machining, and surface treatment processes can drastically improve the performance of valve seats.
These techniques help refine the valves’ edges and surfaces, which contribute to their overall durability and functionality.
By embracing such innovative manufacturing methods, quality assurance leaders can stay ahead of industry standards and enhance the competitiveness of their products.
Quality Assurance Practices
Implementing robust quality assurance practices is essential in the development of stainless steel valve seats.
These practices ensure that every product meets high safety and efficacy standards before reaching the market.
Key quality assurance measures include material testing, which evaluates the corrosion resistance and tensile strength of the stainless steel used.
In addition, conducting dimensional inspections using precise instruments ensures that each valve seat meets exact specifications.
Non-destructive testing methods, such as ultrasonic and X-ray inspections, can also be employed to detect internal flaws without damaging the component.
By maintaining stringent quality assurance procedures, leaders can secure the reliability and performance of stainless steel valve seats, boosting customer trust and industry reputation.
The Role of Technology in Quality Improvement
Technology plays a significant role in improving the manufacturing quality of stainless steel valve seats.
The integration of smart technologies such as IoT (Internet of Things) and AI (Artificial Intelligence) allows for enhanced monitoring and control of production processes.
IoT enables real-time data collection from manufacturing equipment, ensuring that every step is executed within predefined parameters.
AI algorithms analyze this data to detect patterns and predict potential issues, enabling proactive maintenance and quality control.
These technological advancements result in higher yield rates, reduced waste, and improved overall product quality.
By harnessing these tools, quality assurance leaders can further improve the integrity and cost-effectiveness of their valve seats.
Conclusion
Stainless steel valve seats are integral to ensuring the smooth operation and reliability of various systems requiring fluid control.
Their corrosion resistance and sealing performance make them indispensable in challenging environments where durability is a priority.
Advanced manufacturing techniques and stringent quality assurance practices are essential in maintaining and enhancing the performance of these components.
By staying informed about technological advancements and implementing rigorous quality control measures, quality assurance department leaders can ensure their stainless steel valve seats remain at the forefront of industry standards, ensuring safety, efficiency, and customer satisfaction.
資料ダウンロード
QCD調達購買管理クラウド「newji」は、調達購買部門で必要なQCD管理全てを備えた、現場特化型兼クラウド型の今世紀最高の購買管理システムとなります。
ユーザー登録
調達購買業務の効率化だけでなく、システムを導入することで、コスト削減や製品・資材のステータス可視化のほか、属人化していた購買情報の共有化による内部不正防止や統制にも役立ちます。
NEWJI DX
製造業に特化したデジタルトランスフォーメーション(DX)の実現を目指す請負開発型のコンサルティングサービスです。AI、iPaaS、および先端の技術を駆使して、製造プロセスの効率化、業務効率化、チームワーク強化、コスト削減、品質向上を実現します。このサービスは、製造業の課題を深く理解し、それに対する最適なデジタルソリューションを提供することで、企業が持続的な成長とイノベーションを達成できるようサポートします。
オンライン講座
製造業、主に購買・調達部門にお勤めの方々に向けた情報を配信しております。
新任の方やベテランの方、管理職を対象とした幅広いコンテンツをご用意しております。
お問い合わせ
コストダウンが利益に直結する術だと理解していても、なかなか前に進めることができない状況。そんな時は、newjiのコストダウン自動化機能で大きく利益貢献しよう!
(Β版非公開)